Job order costing
Job order costing is a method employed mainly by custom manufacturers to keep a record of costs associated with particular units of production (H. James Williams (1985). It is tailored to calculate the expenses that are incurred in a particular job. These jobs are ordered to be produced and delivered to customer as per his/her unique preferences and specifications. Job costing assists in proper invoicing of jobs as well as to analyze between different jobs that are given.
Job order costing is used by the management as a control tool in analyzing any differences between the quoted price and actual cost incurred in producing that particular unit. It pinpoints areas of variances thus assist in quotation of future jobs of similar nature and magnitude. In recording, the costs are accumulated in job cost sheet.
- Each department fills the cost it incures. Overheads are determined and allocated on pre-determined overhead absorption rate. Job costing has got the following distinct characteristics;
- Each production unit is often unique in that each customer has got specifications that are as per his preferences. This means that the costs of production vary with each client
- There is always a time frame in which a particular job given should be completed.
- The materials used in a unit are distinct from other materials in different unit.
- The jobs costing is usually used to project revenue to be received that is, it is used as a budgetary tool. It’s important to note that job costing may be done for a job that is one off i. e. done once in a long time frame. Process costing.
Order custom essay Job order costing with free plagiarism report
This method of costing is used mostly in manufacturing companies that produce in bulk and identical or similar products continuously (Jan R. Williams, et al 2007). The output is a product that has passed several processes. The main aim is to deduce the unit cost of item produced in a particular p of period by accumulating the manufacturing cost for a particular period. To calculate the cost of items produced in a particular period the following steps are followed; i. The number of units produced in a particular period is identified and determined. ii. The cost incurred in relation to those items is computed
iii. The cost attributable to items produced is divided by items number to arrive at unit cost of production The cost accumulation is reported in each apartment and this acts as a control tool of production. Indirect costs are appropriated in a predetermined overhead absorption rate in the final manufacturing trading profit and loss account.
Point of stress That in both job order costing and process costing at the end of period there are unfinished jobs or work in progress, to determine the cost attributable to each unit, the unfinished jobs are converted to equivalent units i. e. according to percentage of completion, such that period costs are attributed to that period only and not forwarded to next period remain matching to the period incurred i. e. according to the matching concept of accounting. Secondly, direct costs are of attached to the specific job or process and indirect costs are apportioned as per predetermined overhead absorption rate. Standard costing This is a management budgetary tool as well as control tool that is used to estimate overall production cost assuming normal working conditions (Charles T.
Horngren, et al (2005). In control, it is used to measure deviations from the expected. In their book, Michael W. Maher, William N. Lanen, Madhav V. Rajan. (2004). , explain that standard costing is used in the following fields during production; • During planning of the resources needed i. e. these is meant to ensure that the required funds are available for the task to be completed.
- They define the cost elements of each cost center thus areas where savings can be realized is capitalized on.
- The work in progress and inventory can be valued appropriately using standard costing methodology to determine if there are any deviations to estimated costs.
- Any variances can be detected in advance investigated and a corrective measure made before the situation runs out of control.
- The prepared standard costing figures are important in forecasting the profit and • The figures used in standard costing can be simulated to effects of variables of cost on the final production process cost.
According to Don R. R. Hansen, Maryanne M. Mowen. (2006)., standard costing is linked very much to budget where it is used as a budgetary tool of control, as it is one of items used by management accountant in making budget forecasts.
Reference:
- Charles T. Horngren, Gary L. Sundem, John A. Elliott, Gary Sundem, John Elliott. (2005). Introduction to Financial Accounting 9th Ed. London.
- Prentice Hall Don R. R. Hansen, Maryanne M. Mowen. (2006). Management Accounting. South-Western H. James Williams (1985).
- Job Order Cost Accounting Information Systems. Journal of Small Business Management, Vol. 23,. Jan R. Williams, Susan F. Haka, Mark S. Bettner, Robert F. Meigs. (2007). Financial and Managerial
Cite this Page
Job order costing. (2018, Aug 23). Retrieved from https://phdessay.com/job-order-costing/
Run a free check or have your essay done for you
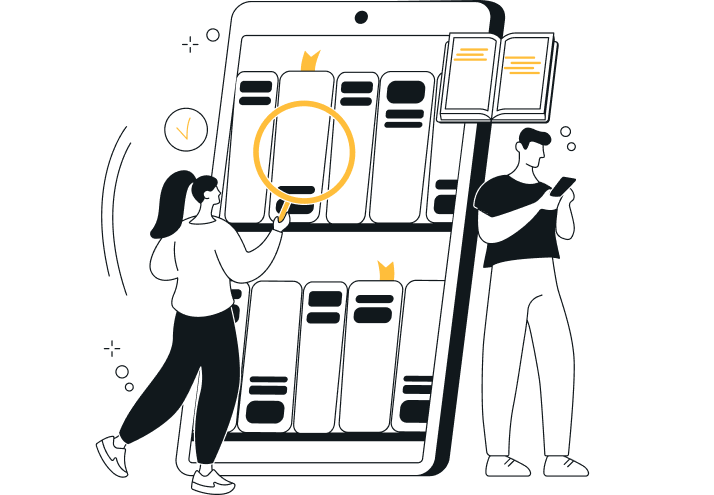