Hyundai Case Study
Asia Paci? c Business Review Vol. 12, No. 2, 131–147, April 2006 Globalization and Employment Relations in the Korean Auto Industry: The Case of the Hyundai Motor Company in Korea, Canada and India RUSSELL D. LANSBURY*, SEUNG-HO KWON** & CHUNGSOK SUH† *University of Sydney, **School of International Business, University of New South Wales, † University of New South Wales ABSTRACT Examination is made of the complex interactions between globalization and employment relations as re? ected in the operations of the Hyundai Motor Company (HMC) in Korea, Canada and India.
After the closure of its short-lived attempt to manufacture cars for the North American market from Canada, the HMC ‘relaunched’ its globalization strategy in India in 1998. An examination of Hyundai’s experience in both countries suggests that employment relations is likely to continue to be an evolving blend of company-speci? c policies and locally-based practices. KEY WORDS : Globalization, management, unions, employment relations, production systems, Korea, Canada, India Introduction The effects of globalization on employee relations are widely debated.
One view is that globalization has created pressures for convergence between different national settings, particularly as multinational enterprises extend their manufacturing and other operations across a variety of countries. Alternatively, it is argued that at national-level institutional arrangements play an important role in creating divergence between employment relations in different countries. As a consequence, globalization is not likely to lead to universal convergence of national patterns of employee relations.
Order custom essay Hyundai Case Study with free plagiarism report
A third view rejects the simple convergence/divergence dichotomy and argues that there are complex interactions between global and national (or local) forces which shape the outcome of employee relations (Lansbury, 2002). The Korean automobile industry offers an opportunity to analyse this debate as it pursues a strategy of globalization and begins the process of expanding production beyond Korea and building plants in other parts of the world. Correspondence Address: Professor Russell Lansbury, Faculty of Economics and Business, University of Sydney, NSW 2006, Australia.
Email: r. lansbury@econ. usyd. edu. au 1360-2381 Print/1743-792X Online/06/020131-17 q 2006 Taylor & Francis DOI: 10. 1080/13602380500532180 132 R. D. Lansbury et al. Globalization of the Korean auto industry has occurred in a very short period of time. It began as a repair industry for vehicles released during and after the Korean War in the early 1950s. The ? rst assembly plant in 1955 had an annual capacity of 1,500 units. When the Korean government launched the ? st Five Year Economic Development Plan in 1962, it introduced the ‘Automobile Industry Protection Law’ and began to promote the auto sector as a key element in emerging Korean manufacturing industry. However, the ? edging Korean auto sector experienced uncertainty and ? uctuations during the 1960s. The Saenara Motor Company was established in 1962 under a technical alliance with Nissan, but due to shortage of foreign exchange went bankrupt and was taken over by the Shinjin Motor Company which was allied to Toyota.
Shinjin assembled the Corona in a complete knock-down (CKD) form of production, whilst the Hyundai Motor Company began production of the Cortina in a technical alliance with Ford. The Korean government announced a ‘localization plan’ in 1970 under which the proportion of local content in passenger cars was supposed to increase from 38 per cent in 1970 to 100 per cent by 1972. However, the localization rate barely reached 50 per cent by 1972. A rapid period of growth occurred in the Korean auto industry during the period 1972– 82.
The government announced ‘A Long Term Plan to Promote the Automobile Industry’ in 1974 which had three major targets: to achieve a localization rate of 85 per cent by 1975; a target of 80 per cent of domestic sales to be in the small car segments below engine capacity of 1500 cc; and an export target of 75,000 units by 1981. By the end of the 1970s, the Korean industry had three local producers: Hyundai, Kia (which had taken over Asia Motors) and Daewoo (which had absorbed Shinjin Motors).
However, a global economic recession in late 1979 resulted in a severe excess capacity for manufactured vehicles and the Korean government announced a ‘Decree to consolidate the Automobile Industry’ in 1980. The plan required that small passenger cars would be produced solely by Hyundai and Daewoo; that Kia would concentrate on small to medium commercial vehicles; and that only buses and large trucks would be open to competition. This resulted in a substantial contraction of the industry and, by 1983, vehicle production had declined to the levels of 1979.
However, production grew steadily again during the mid to late 1980s and expanded substantially in the 1990s (see Table 1). The 1980s and 1990s were a period of mass production as all three major companies built up their annual capacities and began aggressively to export Table 1. Korean automobile production and exports for selected years Production (000s) 1976 1981 1986 1991 1996 2001 Domestic Sales, % Exports, % 49 133 601 1,497 2,812 2,946 97. 5 81. 3 49. 1 73. 9 57. 0 49. 1 2. 5 18. 7 50. 9 26. 1 43. 0 50. 9
Source: Korean Auto Manufacturers Association, Statistical Reports (various years). Globalization & Employment in Korea 133 Table 2. Comparison of production and sales by Korean and Japanese automotive companies for selected years (%) 1992 Korea Japan Overseas Production Domestic Production Domestic Sales Overseas Sales 3 97 Overseas Production Domestic Production Domestic Sales Overseas Sales 1995 4 96 25 75 73 27 61 39 35 65 55 45 64 36 Source: Li Song (1998) The Process of Globalization of the Korean Automobile Industry, Economics and Management Analysis, 18:1 utomobiles, particularly to North American and Europe. By the mid 1980s, more than 50 per cent of total production was exported. A comparison of production and sales by Korean and Japanese auto companies in the early to mid 1990s is shown in Table 2. In 1992, the size of the Japanese domestic market was ? ve times larger than that in Korea. During the early 1990s, however, the Japanese auto industry began to restructure in response to economic circumstances. By 1995, Japanese companies produced about 35 per cent of its global production through subsidiaries outside Japan.
Their globalization strategy concentrated on expanding overseas production and coordinating components suppliers among various global production centres. In 1995, the proportion of exports to total domestic production in Korea was similar to that in Japan. Yet the globalization of the Korean auto industry focused mainly on exporting domestically produced vehicles until the mid 1990s. Although overseas production began to increase in the late 1990s, the proportion was still rather small and most production continued to take place in Korea.
The duration of the globalization process among Korean auto companies has been shorter than their Japanese counterparts. The Korean auto sector adopted a similar strategy to the Japanese of entering foreign markets at the lower cost end and then moving upwards. However, in contrast to the Japanese who began by exporting to less developed countries, Korean auto companies exported ? rst to the developed economies of the European Union and North America and then to less developed countries in Asia. The Korean companies have encountered dif? ulties in developing extensive supply chains and global materials management required for a mature global production system, which have been hallmarks of the successful Japanese auto companies. Most of the important management decisions are still made in the head of? ce in Korea and relocation of complete production systems overseas is still in the early stages. Furthermore, since the economic crisis of the late 1990s, Hyundai is the sole survivor of the three former major auto companies in Korea. Hence, the focus is on the experience of Hyundai as it seeks to ecome a global manufacturer with assembly plants in other countries. 134 R. D. Lansbury et al. Although there is an emerging literature about global automobile manufacturing by the USA, Japan and European companies, and their employee relations (see Boyer, 1998; Lewchuck et al. , 2001), little attention has been paid to Korean auto manufacturers which have also been seeking to establish an international presence (Hill and Lee, 1998; Kochan et al. , 1997; Kwon and O’Donnell, 2000). Examination is made of the experience of the Hyundai Motor Company (HMC) in establishing overseas plants, as part of its globalization strategy.
It seeks to answer the question: ‘to what extent has the Hyundai Motor Company (HMC) applied Korean approaches to employee relations, or adapted to local custom and practices in their overseas plants? ’ HMC provides an interesting case as it has embarked on a long-term strategy of becoming one of the world’s largest auto companies by expanding into new markets and establishing plants outside Korea. In order to achieve this goal, HMC has sought to develop effective and appropriate employee relations strategies for managing its employees in its overseas plants.
HMC’s ? rst venture abroad was in the mid 1980s, when it established an assembly plant in Quebec, Canada. However, this was an unsuccessful operation and HMC closed the plant in 1993. HMC began operations in India in 1998 in an attempt to re-establish its credentials as a global automobile manufacturer. A major issue, which it has confronted, is the management of labour in India, where unions have been very active in seeking membership and bargaining rights in the auto industry, particularly with foreign-owned companies. Methodology
The primary research approach used in this study was ethnographic, and utilized comparative case studies of employment relations policies and practices of the Hyundai Motor Company in Korea and India. Similar methodologies have been used by Frenkel (1983), Kalleberg (1990) and Oliver and Wilkinson (1989). The researchers undertook several ? eld trips to visit Hyundai’s assembly plants in Chennai (India) as well as in Seoul (Korea), over a three year period from 1999 to 2001. Interviews were conducted with managers and workers in these plants using a semi-structured interview schedule.
Documentary material was also collected and analysed from the Hyundai Company in both countries in order to compare the of? cial company policies on employment relations with the prevailing practices at the plant level. Given the fact that Hyundai had closed its assembly plant in Quebec in 1993, the researchers had to rely on interviews with former employees and managers, now located elsewhere in the Hyundai Motor Company, as well as previously published accounts. Fortunately, an extensive study of the Quebec plant had been undertaken and published by Gregory Teal (1995).
In his study, Teal noted that ‘while there was a managerial discourse of participation and diffusion of power [in the Quebec plant] the gap between this discourse and the real diffusion of power was such that a sizable minority of employees did not comply with managerial objectives’ (1995: p. 85). Teal’s ethnographic study of the Hyundai assembly plant in Quebec provided a rich source of comparative data for the study of the Hyundai plant in Chennai. Globalization & Employment in Korea 135 Background to the Hyundai Motor Company (HMC)
The Hyundai business group is one of Korea’s oldest and most successful familyowned conglomerates known as ‘chaebol’ (Steers et al. , 1989). In 1997, the Hyundai business group had over 60 subsidiary companies, more than 200,000 employees and accounted for approximately 18 per cent of Korea’s Gross Domestic Product. In 2000, the Hyundai Motor Company (HMC) and its subsidiaries were forced to separate from the Hyundai group as a result of government policies designed to reduce the size and in? uence of the chaebols.
The Hyundai conglomerate was established by its founder, Chung Ju-Yung, in 1946 as an auto repair shop. This small business expanded into a construction company in 1947 with the establishment of the Hyundai Engineering and Construction Company (HECC). During the Korean War (1950–53) with government support, the Hyundai business group expanded into a number of other areas of activity such as ship-building and heavy machinery. These are key industries which enabled Hyundai to diversify into related businesses, expand in size and maximize economies of scale and scope.
The Hyundai Motor Company (HMC) began in 1968 as a complete knock down (CKD) assembler under an agreement with the Ford Motor Company. In 1976, HMC produced its ? rst originally-designed model, the Pony, using a low cost strategy with more than 90 per cent of its parts being sourced locally. Other new models followed and HMC entered the US market in 1986 with the competitively low-priced Excel. During the late 1980s, however, the international auto industry experienced considerable restructuring due to oversupply, excessive production capacity and intense global competition (see Womack et al. 1990). This gave rise to a number of strategic alliances between various auto companies via mergers and business partnerships. These were initiated to achieve economies of scale and to enhance the enlarged companies’ competitive positions in the international auto market. This was one reason whey HMC formed a strategic alliance with Mitsubishi in Canada. Studies of the Korean chaebol have tended to describe them as having similar characteristics to the zaibatsu in pre Second World War Japan: large, diversi? ed, usually family-owned and managed conglomerates (Amsden, 1989).
The Japanese colonization of Korea, which lasted from the early 1900s to the end of the Second World War, resulted in the establishment of a number of institutions and practices derived from Japan and which in? uenced the way in which companies were developed and managed. The chaebol, like the zaibatsu, have used a variety of means to foster worker identi? cation with and dependence on the company (Janelli & Yim, 1993). Hyundai, for example, used the dormitory system (originally established by Japanese enterprises in the textile industry) to allow close supervision and control over predominantly young workers (Cho, 1999).
This was accompanied by hiring and training schemes as well as paternalistic welfare systems to foster dependency among the workers. Most chaebol also used the ‘moral persuasion’ of the founder to elicit worker compliance by promoting the concept that the good of the nation was based on the company’s performance. The founder of Hyundai, Chung Ju-Yung, regularly exhorted his employees to embrace the ‘Hyundai spirit’. Independent unions were not tolerated and were banned by the government until the late 1980s (Kearney, 1991).
Yet worker dissatisfaction with both the paternalism of the chaebol and authoritarianism of the state gradually built up to breaking point and contributed 136 R. D. Lansbury et al. to major industrial disputes and civil unrest resulting in the ‘democratization’ of Korea in 1987 (Choi, 1989; Ogle, 1990). Development of employment relations policies and practices at HMC were strongly in? uenced by the business partnership with the Mitsubishi Motor Company (MMC) which involved not only technical cooperation but also management development. MMC was actively involved in the design of the ? st full automobile manufacturing systems at HMC. MMC made a strategic investment in HMC equal to 10 per cent of HMC’s total capitalization. MMC also entered into an enhanced technological cooperation agreement to supply various parts such as engines, axles and chassis components. The ? rst model which HMC developed was based on the Mitsubishi Lancer. Elements of MMC’s system of labour management approach were utilized by HMC in order to enhance productivity and reduce production costs. These included quality control techniques and job design which sought to more effectively utilize workers.
Professional engineers became central to the control of production operations and supervisors were given strict control over workers on the assembly-line. The human resource policies practised by HMC during its formative stage comprised two basic characteristics. First, a strict dual labour market created a division between managerial and production workers. HMC applied different selection criteria for each of these groups of employees. Second, a seniority system of promotion was developed in order to strengthen the hierarchical structure of the internal labour market and to educe short-term labour turnover. Years of service was an important criteria for wage increases and promotion. As HMC expanded its production and hired more employees, however, it adopted what was termed an ‘Open Recruitment System’ (ORS) in an attempt to attract more university graduates and develop a professional management hierarchy. The ORS was also used to introduce more formal systems of recruitment for production workers which would enhance the quality of recruits to the production area. However, the dual labour market system remained and was even strengthened within HMC.
Table 3 summarizes the criteria by which management and production employees were recruited. However, HMC argued that their approach to recruitment was transformed from one which relied on personal contracts or connections to one which was based on objective selection criteria. As Kwon and O’Donnell (1999; 2000) have shown, workers in HMC appeared to be more compliant than those in other parts of the Hyundai group until the mid 1980s. Part of the explanation may be the relatively secure employment conditions Table 3. Recruitment practices at the Hyundai Motor Company during the 1990s Management employees
Responsibility Target Groups Assessment Process Production employees Group planning of? ce University graduates Written exam (e. g. language skills) University degree Interviews by senior management and personnel management Personnel department at plant level High School leavers Test for relevant skills High School results Interviews by department head and personnel staff Globalization & Employment in Korea 137 at HMC, although some have argued that HMC workers witnessed the failure of strikes elsewhere and were more acquiescent about their conditions of employment (Bae, 1987).
Furthermore, management in HMC and the Hyundai Heavy Industry group also used various means to oppose the rise of an independent union movement, including physical violence, intimidation and the establishment of complaint in company unions. However, following reforms to labour legislation in the 1990s, HMC was forced to negotiate with unions over wages and conditions. The HMC trade union also became a central force in the formation of the KCTU as the national peak council for the independent trade union movement.
One of the main policy responses by HMC to the emergence of a more militant workforce and trade union movement during the 1980s was the implementation of an extensive welfare system. Welfare expenditure by HMC increased from 286 billion won in 1986 to 857 billion won in 1990. Welfare bene? ts which had been limited to management were extended to production workers in the late 1980s. Various cultural programmes were organized in conjunction with training programmes and other activities in an attempt to build a ‘unitarist’ philosophy of loyalty to the ? m and reduce the anti-management sentiments of many workers. Unions made the improvement of welfare systems a major bargaining issue, particularly in the context of an inadequate state welfare system in Korea. The unions achieved the establishment of joint project teams with management to oversee a range of welfare programmes, such as the Employee Housing Construction Implementation Committee to build houses for workers. Scholarships were also obtained for children of workers by the unions in negotiation with management. Wages were the subject of vigorous negotiation between unions and management rom the late 1980s onwards. Wages at HMC increased by 20 per cent in 1987, 30 per cent in 1988 and 28 per cent in 1989 compared with only 6 per cent between 1982 and 1986. It was not only the amount of wages which were the subject of bargaining with the unions but also the wage structure at HMC. As shown in Table 4, the unions achieved increased allowances, bonuses and superannuation paid by HMC to its members. Hence unions were able to broaden the range of issues for negotiation with HMC from the late1980s and made considerable gains during the 1990s.
In terms of the broad range of human resource policies and practices, however, HMC has continued to use various means in an effort to promote a convergence Table 4. The structure of remuneration at the Hyundai Motor Company during the 1990s Types of Remuneration Components Monthly wages Normal ? xed wage Other ? xed and variable allowances Performance-based pay Productivity-related pay Bonuses Superannuation Value-added remuneration Other forms of remuneration 138 R. D. Lansbury et al. Table 5. Comparison between employment relations practices adopted by the Hyundai Motor Company in the three plants in Korea, Canada and India
Human resource policies and practices Korea Canada India Selection of employees based on performance-related criteria Training programmes which reinforce company norms such as loyalty and team spirit Employee involvement in some aspects of decision-making at plant level Industrial relations Successful avoidance of collective agreements with unions Flexible wages system linked to productivity and/or performance criteria Internal Labour Market Arrangements High status differentiation between workers and managers at plant level Opportunities for promotion from the shop ? or to higher level positions within the plant Yes Yes Yes Yes No Yes No Yes No No No Yes No Yes Yes Yes No Yes No Yes No of interests between employees and management, while seeking to maintain control and authority over the workforce. The HMC union has been able to resist some of the management’s initiatives to change wages and working conditions, but HMC continues to control the basis on which selection and training of employees is conducted and there is still a strong degree of status differentiation between management and workforce. This is re? cted in large differences between wages, bene? ts and conditions of work between HMC employees at the shop ? oor level compared with those in the ranks of management. Some key employment relations practices are set out in Table 5 and a comparison is made between those that prevail in Korea compared with plants in Canada and India. Hyundai’s Experience in Canada In cooperation with Mitsubishi, HMC opened its ? rst overseas plant in Quebec, Canada, in 1985, in order to assemble the medium-sized front wheel drive Sonata model. The objective was to pro? from HMC’s initial success in Canada in 1984, with the Pony, when HMC became the largest auto importer in the country. Sales to Canada accounted for 30 per cent of HMC’s total production that year. By establishing a presence in North America, HMC sought to boost its sales and avoid the imposition of import quotas. HMC acquired a 400 acre green? eld site near the Canadian town of Bromont in Quebec for the token payment of one Canadian dollar and received $Canadian 110 million in grants from the Canadian federal and provincial governments as part of HMC’s total investment of $Canadian 325 million.
In addition, the Quebec Department of Labour gave a $Canadian 7. 3 million grant to HMC to assist with training the workforce over a three year period. HMC built both a paint and a press shop to increase North American content (an important criterion for exporting to the USA) as well as because of problems in gaining components from Korea due to labour problems Globalization & Employment in Korea 139 and strikes at HMC’s Ulsan plant. Yet, when the plant was ? ally closed in 1993, one of the major contributing factors was ascribed to HMC’s failure to manage successfully relations with its Canadian managers and employees (Teal, 1995). An analysis of HMC’s experience in Canada offers some useful insights into the way in which the company sought to manage its workforce in North America. This is examined in regard to two key areas: human resource and industrial relations policies and practices. The data on which the account Hyundai’s experience in Canada is based is from a study of the Quebec plant by Teal (1995).
More information was collected from HMC employees who had worked in the Canadian plant. Human Resource Policies and Practices The hiring policy of HMC in Canada was based on selecting employees who would identify with the company and its objectives. The selection process was lengthy and complex, with candidates spending four days being interviewed, tested for hand– eye coordination and subjected to personality tests. The key selection criteria for prospective employees were that they would be willing and able to do repetitive, monotonous work on an assembly line, as well as work in a team.
The company explicitly sought younger workers, around 22 years of age, with little or no experience in the auto industry. Hyundai sought to socialize new employees in a way that promoted identi? cation with the company. All production workers were called ‘technicians’ and each employee was referred to as a ‘member’. All company employees wore the same uniform, irrespective of whether they were managers or shop-? oor workers. There was one cafeteria and one parking lot for all Hyundai employees.
There was a wide range of sports and leisure activities designed to build team spirit and company ethic among all employees. The training programmes for new employees emphasized loyalty, motivation and team spirit. Some employees were sent to Hyundai’s production centre in Ulsan, South Korea. However, the organization of team work in the Quebec plant was different from Ulsan. The work teams in Canada were less hierarchical and authoritarian than in Korea, team members were encouraged to discuss any problems and there appeared to be greater job rotation within the teams.
There was also a ‘Direct Communication System’ in the Quebec plant which was not present in Ulsan. Each team elected its own representative to a departmental committee. Team representatives from each department met regularly, with management playing an observer role at most meetings. There was also a health and safety committee to which workers elected their own representatives. During 1991 there were more than 50 meetings of Direct Communication committees at which more than 400 topics were discussed. Yet management found it dif? ult to satisfy the demands and expectations among employees. In 1991 there were nearly 160 complaints by workers concerning health and safety issues, of which only 100 were resolved. Industrial Relations A major concern of HMC was to avoid unionization of the plant in Quebec. The Canadian Auto Workers Union (CAWU) devoted considerable organizational 140 R. D. Lansbury et al. and ? nancial resources to attempting to organize the plant, without success, although by the time the plant closed in 1993, the union claimed to have achieved a growing level of support among the workforce.
While much of the emphasis by Hyundai management was on more subtle means of union avoidance, by developing strong identi? cation of workers with the company, a number of employees who were thought to be sympathetic to or organizing on behalf of the union were suspended, transferred or dismissed. The union brought cases of alleged unfair dismissal before the Quebec Government Labour Commission and was successful in achieving an out-of-court settlement for a worker who had been dismissed in 1990.
However, the union did not succeed in gaining a collective bargaining agreement to cover workers at the site. One of the devices used to prevent unionization of the plant was the formation of a pro-company, anti-union committee among the employees called ‘the Silent Majority’. It was formed in 1991 to dissuade employees from joining the union. The committee distributed pamphlets which alleged that if the plant became unionized, workers would lose money in union dues and their jobs would be insecure.
The committee claimed that while workers were being laid off in other Canadian plants, which were unionized, Hyundai had hired new employees, opened a press shop and provided a high degree of job security. It also charged that the union was more concerned with protecting the jobs of workers in the ‘big three’ auto plants in Ontario where it had a large membership, rather than at the Hyundai plant. But faced with the depressed economic climate in Quebec and the disappointing sales of the Hyundai Sonata in Canada and the USA, Hyundai introduced a reduced work week for all employees and ? ally shut the plant in September 1993. Internal Labour Market Arrangements Distinctions between managerial and production workers were minimized in terms of status differentials within the plant (such as dining facilities), and workers were encouraged to participate in decision-making at the level of team or work group. Yet the work itself remained organized along Taylorist principles, with a strong division of tasks and demarcations between various job functions. Workers complained that even though they were supposed to be involved in a team-based approach to management, they were subject to ‘speed-up’ and work intensi? ation without consultation. They also claimed that Hyundai actively discouraged union membership by workers and refused to engage in collective bargaining. Hence, employee involvement in decision-making was highly restricted and had little impact on the internal labour market arrangements. Yet there existed greater opportunities for promotion of workers in production and other functions to higher level positions in the Canadian plant compared with similar plants in Korea and India. Experience of Hyundai Motor Company in India
In 1996, ? ve years after the closure of the Quebec plant, HMC established a 100 per cent owned subsidiary, the Hyundai Motor Company of India (HMI), Globalization & Employment in Korea 141 to manufacture cars in India. It represented an investment of more than US$ 450 million. Construction of a plant with the capacity to produce 120,000 passenger cars per year was completed in Chennai, Southern India, in 1999. By May 2000, the Chennai plant was producing 100,000 vehicles a year and had captured 14 per cent of the Indian market.
HMI produced two models in Chennai: Santro (999 cc) and Accent (1,499 cc), both of which achieved approximately one quarter of their respective market segments during the ? rst four months of 2000. HMI began its operation in Chennai with a workforce of 1,400 operating in a one shift production system in October 1998. By January 2001, the workforce had increased to 3,000 workers and a three-shift operation. It had become one of the fastest growing auto manufacturers in India and shared the lead with Ford of India in its respective market segments. It is dif? ult to make a direct comparison between Chennai and the Quebec plant as Chennai was larger and produced two models instead of one. Nevertheless, HMI followed some policies similar to both the Korean and Canadian plants and also implemented HR policies and practices which emphasized selection procedures and training programmes designed to ensure that new employees are strongly integrated with the organization. However, due to lower labour costs in India, there was more reliance on labour-intensive methods and less use of automation than in Canada or Korean plants.
Given the lower levels of education and skill among the Indian workforce, compared with Korea or Canada, there was a much greater presence of Korean managers and technical advisers in Chennai, particularly during the ? rst year of operation. The lines of demarcation between different segments of the workforce were also greater in the Indian plant and there was a more hierarchical structure in the Indian company. Some of these practices re? ected local norms in Indian work culture and industry.
The experience of the Hyundai Motor Company in India is analysed with regard to three areas: human resource policies and practices, industrial relations and the internal labour market arrangements. Human Resource Policies and Practices HMI used a variety of HR policies and procedures to align the attitudes of its employees with the corporate culture. Training programmes within HMI re? ected the paternalistic nature within the company and emphasized the development of a strong work ethic among the employees. New recruits were given two-day basic orientation training before being allocated to a speci? c department.
Most of the initial work skills are taught on the production line. There followed a job rotation programme which exposed workers to other parts of the plant operations. As Chennai is a mass production plant, most of the jobs were fragmented into relatively simple, repetitive tasks and there was a highly detailed division of labour. Much of the training beyond basic skills development was used to promote employee loyalty and develop harmony at the workplace in order to avoid internal con? ict. Workers were also encouraged to participate in productivity campaigns, employee suggestion schemes and quality control systems.
There was a Supervisor Development Programme to enhance the skills of ? rst line managers. At executive level, there was a Management Development Programme to improve 142 R. D. Lansbury et al. the capacity of managers to think strategically, manage their time effectively and improve work methods and quality. The majority of workers at the Chennai plant were employed at trainee level for the ? rst three years and it was anticipated that some of these would leave the company after three years (when the traineeship ended) in search of better wages and conditions.
By maintaining high turnover at this level, HMI could keep wages down and retain a group of low-paid trainees who were not permitted to join unions and could provide a ‘buffer’ should demand fall and the workforce need to be quickly reduced. In effect, the trainee position was a de facto short-term contract job, although some workers did receive promotion at the end of the trainee period. Nevertheless, promotion procedures were slow and were aimed at cost minimization, although employees with exceptional performance could receive rapid promotion.
In general, it could take up to 20 years or more for production workers to rise to the highest level in their employment structure. There was a system of performance appraisal which varied according to the level of the position. When applied to the non-executive groups the emphasis of the appraisal system was on behavioural criteria such as discipline, attitudes to work, cooperation, punctuality and attendance. The system led to some con? icts between production workers and management, although it was supposed to enhance competition between workers to achieve the highest performance ratings.
Wages policy was the most critical factor in enabling HMI to achieve a ‘cost effective’ approach to labour management. HMI’s goal was to minimize labour costs while providing management with considerable ? exibility to link allowances to productivity improvements. The total wage package comprised four key elements: a base level amount, a cost of living component, house rental allowance, a ? exibility allowance and a mixture of sundry other minor components (including travel, children’s education, provident fund etc. ).
There was considerable variation in the ratio of different components depending on an individual’s position in the hierarchy. Hence, the base component of total salary varied from 60 per cent for managers to 30 per cent for production workers. According to HMI, this system helped to promote employee loyalty to the company. The wages of HMI employees were adjusted annually through increments paid in April and the wage structure was reviewed every three years. During 2000, HMI came under pressure from its workforce to increase wages, and a 20 per cent increase was granted to trainees and junior technicians.
The wage levels for trainees and junior technical employees at HMI compared favourably with other multinational auto companies in the same area, but were superior to Indian companies in the auto components sector. However, by having the vast majority of their employees at trainee level, HMI was able to contain its wage costs. The wages and salaries differentials between executive and non-executive employees remained fairly constant over the ? rst few years of HMI’s operation in Chennai, with executives receiving approximately six times that of production workers. However, it was dif? ult to gain accurate information about senior executive salaries paid by HMI. Anecdotal evidence from HMI and other automobile producers in India suggested that the foreign-owned companies shared information about wage Globalization & Employment in Korea 143 levels and generally maintained comparability so that they were not competing against each other in this regard. Hence, the variations between multinational auto companies operating within the Chennai area were minimal. However, there were signi? cant wage differences between the component suppliers (mainly local Indian ? ms) and the foreign-owned assembly companies. Furthermore, wage levels in the Chennai area were generally lower than those in the northern industrial zones of India as they had been industrialized for less time and were still ‘catching up’ to their northern counterparts. Industrial Relations HMI has been strongly in? uenced by the experience of HMC in Korea. From the mid 1980s, with the emergence of militant unionism, HMC experienced considerable industrial con? ict at its plants in Korea. There was a great deal of external intervention in an attempt to resolve con? cts at HMC, with varying degrees of success. Experience in Korea conditioned attitudes among the senior managers at HMI. One of the principal reasons why HMC chose to locate its plants near Chennai in the south of India, was that unions were not as well organized as in some other parts of India. The trade union movement is well established in India and is closely linked with socialist politics. The Indian Industrial Relations Act provides a range of rights for workers and unions. The Act guarantees freedom of association and allows for multiple unions in workplaces.
It also seeks to facilitate third party intervention in the workplace to resolve industrial disputes. In 2000, trade unions were organized in 24 of the 28 major car manufacturers in India, although not in foreign-owned or joint ventures, including Ford, Volvo, Toyota and HMI. There were two major strikes in the auto sector during the late 1990s. One was a strike over wages and compensation issues at the Ascot-Faridabad plant and lasted 70 days. The other was at Hindustan Motors over factory conditions and wages and was 30 days in duration (Bhaktavatsala, 1992). During the ? st two years of HMI’s operations in India, there were no successful organizing efforts by unions or industrial disputes at the Chennai plant. Yet, as the plant became more established and HMI’s market share and pro? tability increased, production workers increasingly raised complaints about labour intensi? cation, low wages and limited opportunities for promotion. However, as the trainee workers comprise half of the workforce at HMI, and were not permitted to join a union or participate in industrial disputes, HMI management was able to resist union pressures.
Another source of tension within the Chennai plant occurred between Korean managers dispatched to India from HMC in Korea, and local Indian management. An important contributing factor related to the management style displayed by some of the Koreans which the Indians felt was unsympathetic to prevailing customs and practices in India. They complained that their Korean counterparts frequently communicated with each other in the Korean language which excluded Indians from the decision-making process.
For their part, a number of Korean managers claimed that the Indians lacked a strong work ethic and therefore had to be more strictly supervised in order to achieve the required levels of productivity. 144 R. D. Lansbury et al. The Koreans also argued that the caste system interfered with the ef? cient operation of the plant because some Indian workers were appointed by Indian managers to positions in accordance with their caste position rather than on the basis of merit. The Indian management system was regarded as unduly paternalistic by some of the Korean managers.
HMI established a Works Committee, with the objective of resolving con? icts and differences at the workplace without involving unions. The works committee comprised equal representation from both management and production workers. The Committee met monthly and provided a forum in which disagreements over wages and conditions could be discussed and resolved. However, in the absence of a trade union, employees had little bargaining power in regard to management and the Committee had no means of enforcing its decisions. HMI management tended to use the Committee as a means for disseminating its policies among the workforce.
The Committee did not have any jurisdiction to set wages or working conditions. While HMI has remained union-free and had not experienced any major industrial dispute, strikes occurred among component suppliers which were Korean joint ventures with HMI, including Donghee, Pyungbuang, Hwasung and Samrib. The disputes concerned wages, job security and welfare issues. The strikes had adverse effects on HMI’s production ef? ciency as many of the companies had a monopoly supplier relationship with HMI. The resolution of these disputes often required direct intervention by HMI. Internal Labour Market Arrangements
From the initial establishment of the Chennai plant, HMI adopted a dual internal labour market, which differentiated between managerial and production employees in relation to wages, promotion and welfare facilities. Initially, there were two classes of employees: executive and non-executive. In the executive group there were 11 categories while in the non-executive group there were 14 positions. Within the ? rst year of production, however, the total number of employees increased from 1,503 to 2,320 and there was pressure from the workforce to provide greater wage differentials based on quali? ations. Accordingly, the number of categories in the non-executive ranks was increased from 14 to 18 and two new classi? cations of junior engineer were introduced. The expansion in the number of layers within the non-executive group reduced some of the discontent about the limited status differentials in the organizational hierarchy. However, HMI placed restrictions on the number of promotions of workers to higher level categories. This is an important factor in the management of labour within the plant because, as mentioned previously, trainees have only temporary employment status for the ? st three years and are not permitted to join unions. Hence, their opportunities to gain advancement are limited. During the ? rst year of operation, almost all senior decision-making positions at HMI were held by Koreans dispatched from HMC. The Korean managers not only were heads of division, with responsibility for all key activities in HMI, but also some were placed at operational level to provide support and advice to middle level Indian managers and to coordinate management activities.
As the number Globalization & Employment in Korea 145 of total employees increased during the ? rst two years of operation, the ratio of Koreans to Indians in the plant changed from 1:19 to 1:46. However, most key roles remained under the control of Koreans. In the production division, the ratio of Koreans to Indians underwent more signi? cant change, from a ratio of 1:26 in 1998 to 1:172 in 2000. This was in keeping with HMI’s policy of becoming less reliant on Korean managers at plant level. Discussion
The comparison of HMC’s operations in three countries demonstrates that there are complex interactions between globalization pressures towards a uniform approach to employment relations across various countries and divergent tendencies at the local level in each country. Although HMC sought to carefully select employers at its plant in Canada who would identify with the company’s objectives and follow its procedures, the Canadian workers were willing to challenge management decisions and to exercise their rights on issues such as health and safety.
This was despite the fact that the Canadian Auto Workers Union was unsuccessful in gaining collective bargaining coverage of the Bromont plant. Although HMC were able to remain non-union, they had a divided workforce and were not able to implement the full range of Hyundai-style human resource policies and practices as planned. Although the closure of the Canadian operation was primarily due to disappointing sales of the Sonata model, poor employee relations were also a contributing factor to Hyundai’s failure in Canada.
The Indian operations marked an important attempt by Hyundai to relaunch its globalization strategy and demonstrate that it could successfully manufacture and sell overseas-made Hyundai vehicles outside Korea. The employee relations practices which Hyundai implemented in India were more like ‘traditional’ Korean approaches and appeared to represent a ‘retreat’ from some of the more ‘progressive’ ideas which were attempted in Canada – such as a ? atter hierarchical structure and greater employee participation in decision-making (albeit limited in scope).
But the Indian plant was more labour intensive and had lower labour costs, which is similar to the earlier stages of auto production in Korea. Unlike the current situation in Korea, where HMC is required to negotiate with the union movement (due to both its organizational strength and changes in legislation), Hyundai has so far been able to avoid unionization in India. It remains to be seen whether the widespread nature of unionization in the Indian auto industry and political pressures in India may force Hyundai to abandon its policy of union avoidance.
An alternative strategy, pursued by some other foreign auto companies in India has been to recognize or foster enterprise unions, which may be more cooperative than industry-wide unions. Implications As has been noted in other studies of auto companies, which established transplants outside their home country, there is a strong tendency towards ‘hybridization’ both in terms of production methods as well as employment relations. This has been observed in the case of Japanese companies which have 146 R. D. Lansbury et al. established plants in the United States (see Cutcher-Gershenfeld et al. 1998), but it has also occurred with US auto companies in Canada (Lewchuck et al. , 2001) and European auto companies which have opened plants in other parts of the world (see Boyer et al. , 1998). It would appear, from the current study, that a similar tendency is occurring within the Hyundai Motor Company as they seek to re-start their overseas production activities in India. A more diversi? ed employee relations strategy, which takes into account the demands of local employees and their unions, may be required if Hyundai is to continue to develop an effective global production system.
For its global ambitions to be realized, Hyundai will require a much greater proportion of its manufacturing to be undertaken outside Korea, the development of global supply chains and global coordination of production, marketing and technology development. The experience of Hyundai in Canada and India suggests that employee relations are likely to be an evolving blend of company-speci? c policies and locally-based practices, depending on the context in which Hyundai is operating. Conclusions
The experience of the Hyundai Motor Company in India illustrates the complexity of the impact of globalization strategies on employment relations. It supports the hypothesis that there are dynamic interactions between global and local forces, which shape employment relations when a multinational enterprise establishes a production facility in a country outside its home base. Hyundai has applied some of its human resources policies from Korea to India, such as training programmes to reinforce employee loyalty to the company, but it has provided fewer opportunities for employees to be promoted from the shop ? or to higher-level positions within the plant. This has caused resentment among some of the Indian employees who feel that they have limited career prospects in the company. Hyundai has also successfully avoided unionization despite the fact that unions have collective agreements with most local automobile producers in India. It remains to be seen whether the Indian unions will be able to apply pressure successfully to the company to bargain collectively or persuade the government to require Hyundai to negotiate with the union over the wages and conditions of its employees.
Acknowledgements The authors wish to acknowledge the Australian Research Council (ARC) for their award of an ARC Discovery Grant for this research project and the helpful comments of the reviewers and editors. References Amsden, A. (1989) Asia’s Next Giant: South Korea and Late Industrialization (New York: Oxford University Press). Bae, K. H. (1987) Automobile Workers in Korea (Seoul: Seoul National University Press). Bhaktavatsala, R. C. (1992) The Indian automobile industry: patterns of expansion, entry and performance, Management, Journal, 5(2), pp. 7– 111. Globalization & Employment in Korea 147 Boyer, R. (1998) Hybridization and models of production: Geography, history and theory, in: R. Boyer, E. Cherron, U. Jurgens & S. Tolliday (Eds) Between Imitation and Innovation: The Transfer and Hybridization of Production Models in the International Automobile Industry (Oxford: Oxford University Press). Cho, H. J. (1999) The employment adjustment of Hyundai Motor Company: a research focus on corporate-level labour relations, Korean Journal of Labour Studies, 5(1), pp. 63–96 (in Korean). Choi, J. 1989) Labour and the Authoritarian State: Labour Unions in South Korean Manufacturing Industries (Seoul: Korea University Press). Cutcher-Gershenfeld, J. et al. (1998) Knowledge-Driven Work: Unexpected Lessons from Japanese and United States Work Practices (New York: Oxford University Press). Frenkel, S. (1993) Workplace relations in the global corporation, in: S. Frenkel & J. Harrod (Eds) Industrialization and Labour Relations, pp. 37–63 (Ithaca, NY: Cornell ILR Press). Hill, R. C. & Lee, Y. C. (1998) Japanese multinationals in East Asian development: the case of the auto industry, in: L.
Sklair (Ed. ) Capitalism and Development (London: Routledge). Janelli, R. & Yim, D. (1993) Making Capitalism: the Social and Cultural Construction of a Korean Conglomerate (Palo Alto: Stanford University Press). Kalleberg, A. (1990) The comparative study of business organizations and their employees, in: C. Calhoun (Ed. ) Comparative Social Research: A Research Annual, pp. 153– 175 (Greenwich, CT: JAI Press). Kearney, R. P. (1991) Warrior Worker: History and Challenge of South Korea’s Economic Miracle (New York: Henry Holt & Coy). Kochan, T. A. , Lansbury, R. D. & MacDuf? e, J. P. 1997) After Lean Production: Evolving Employment Relations in the World Auto Industry (Ithaca, NY: Cornell University Press). Kwon, S. H. & O’Donnell, M. (1999) Repression and Struggle: the State, the Chaebol and the Independent Trade Unions in South Korea, Journal of Industrial Relations, 41(2), pp. 272– 293. Kwon, S. H. & O’Donnell, M. (2000) The Chaebol and Labour in Korea (London: Routledge). Lansbury, R. D. (2002) The impact of globalization on employment relations: the automobile and banking industries in Australia and Korea, The Bulletin of Comparative Labour Relations, 45, pp. –16. Lewchuck, W. , Stewart, P. & Yates, C. (2001) Quality of worklife in the automobile industry: A Canada–UK comparative study, New Technology, Work and Employment, 16(2), pp. 72– 87. Ogle, G. E. (1990) South Korea: Dissent within the Economic Miracle (London: Zed Books). Oliver, N. & Wilkinson, B. (1989) Japanese manufacturing techniques and personnel and industrial relations practices in Britain: Evidence and implications, British Journal of Industrial Relations, 27(1), pp. 73– 91. Song, L. 1998) The process of globalization of the Korean automobile industry, Economic and Management Analysis, 18(1), pp. 20–35. Steers, R. M. , Shin, Y. K. & Ungson, R. (1989) The Chaebol: Korea’s New Industrial Relations Might (New York: Harper & Row). Teal, G. (1995) Korean management, corporate culture and systems of labour control between South Korea and North America, Culture, 15(2), pp. 85–103. Womack, J. P. , Jones, D. T. & Roos, D. (1990) The Machine that Changed the World (New York: Macmillan).
Cite this Page
Hyundai Case Study. (2017, Apr 09). Retrieved from https://phdessay.com/hyundai-case-study/
Run a free check or have your essay done for you
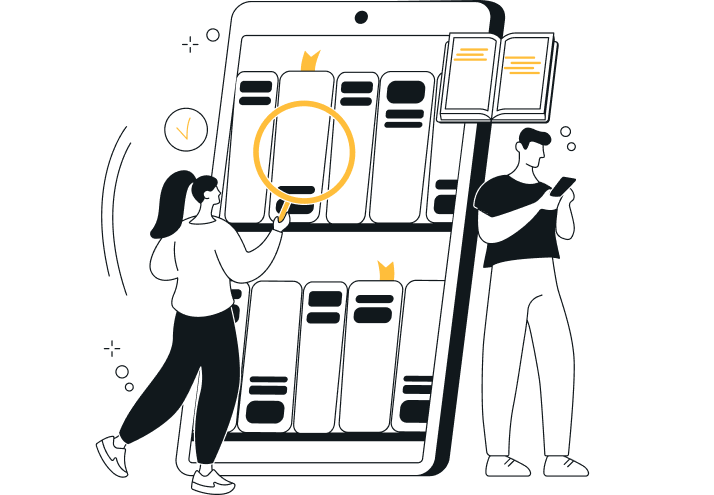