External Failure and Internal Failure Cost
Definition and Explanation of Quality Costs
The concept of Cost Of Quality (COQ) has been around for many years. Dr. Joseph M. Juran in 1951 in his Quality Control Handbook included a section on COQ. The Quality Cost Committee under the Quality Management Division was established by the American Society for Quality (ASQ) in 1961. However it was Philip B. Crosby who popularized the use of COQ because of his book Quality is Fre in 1979. Several current quality system standards, ISO 9000, QS-9000, AS-9000, reference the use of COQ for quality improvement.
The Concept of Cost of Quality is confusing
Order custom essay External Failure and Internal Failure Cost with free plagiarism report
It does not refer to costs such as using a higher grade leather to make a wallet or using 14K gold instead of gold plating in jewelry. Instead the term quality cost refers to all of the costs that are incurred to prevent defects or that result from defects in products. What is being referenced are the costs due to the lack of quality or costs to ensure quality is produced. We understand them as the costs that are associated with preventing, detecting, and correcting defective work. Some authors refer to these costs as “Cost of Poor Quality”. Sometimes poor quality costs refer only to the “failure” costs.
Crosby refers to the COQ costs as “Price of conformance” (the prevention and appraisal costs) and the “Price of non-conformance” (the failure costs). These are divided into conformance and non-conformance costs, also called control costs and failure of control costs. Figure 1 Quality costs can be broken down into four broad groups. These four groups are also termed as four (4) types of quality costs. Two of these groups are known as prevention costs and appraisal costs. These are incurred in an effort to keep defective products from falling into the hands of customers.
The other two groups of costs are known as internal failure and external failure. Internal and external failure costs are incurred because defects are produced despite efforts to prevent them therefore these costs are also known as costs of poor quality. However, we will be focussing on the internal costs failure and the external costs failure for this assignment. The non-conformance costs come into play when the software does not conform to the quality requirements. These costs are divided into internal failure costs and external failure costs.
Failure costs are incurred when a product fails to conform to its design specifications. Failure costs can be either internal or external. Internal failure costs result from identification of defects before they are shipped to customers. These costs include scrap, rejected products, reworking of defective units, and downtime caused by quality problem. The more effective a company's appraisal activities the greater the chance of catching defects internally and the greater the level of internal failure costs. This is the price that is paid to avoid incurring external failure costs, which can be devastating.
On the non-conformance side, we have fault removal costs that can be attributed to the internal failure costs as well as the external failure costs. This is because if we found a fault and want to remove it, it would always result in costs no matter whether costs in an internal or external failure. Actually, there does not have to be a failure at all. Considering code inspections, faults are found and removed that have never caused a failure during testing. It is also a good example that the removal costs can be quite different due to the different techniques.
When a test identifies a failure, there needs to be considerable effort spent to find the corresponding fault. During an inspection, faults are found directly. Fault removal costs also contain the costs for necessary re-testing and re-inspections. External Cost Failure: When a defective product is delivered to customer, external failure cost is the result. External failure costs include warranty, repairs and replacements, product recalls, liability arising from legal actions against a company, and lost sales arising from a reputation for poor quality. Such costs can decimate profits.
In the past, some managers have taken the attitude, "Let's go ahead and ship everything to customers, and we'll take care of any problems under the warranty. " This attitude generally results in high external failure costs, customer ill will, and declining market share and profits. External failure costs usually give rise to another intangible cost. These intangible costs are hidden costs that involve the company's image. They can be three or four times greater than tangible costs. Missing a deadline or other quality problems can be intangible costs of quality.
Internal failure costs, costs and intangible costs that impair the goodwill of the company occur due to a poor quality so these costs are also known as costs of poor quality by some persons. External failure also cause support costs. These are all costs connected to customer care, especially the effort from service workers identifying the problem. Finally, compensation costs could be part of external failure costs, if the failure caused some kind of damage at the customer site. We might also include loss of sales because of bad reputation in the external failure costs but do not look at it in this paper because it is out of scope.
- Quality planning
- QC administration and systems planning
- Quality related training
- Inspection of incoming in process and final product
- Processes planning
- Design review
- Quality data analysis
- Procurement planning
- Market research Vendor surveys Reliability studies
- System development
- Quality measurement and control equipment
- Product Qualification
- Qualification of material|
- Incoming Inspection
- Testing
- Inspection in process
- Quality audits
- Incoming test and laboratory tests
- Checking labor
- Laboratory or other measurement service
- Setup for test and inspection
- Test and inspection material
- Outside endorsements for certification
- Maintenance and calibration work
- Product reengineering review and shipping release
References
- Jones, Capers, Patterns of Software Systems Failure and Success, International Thompsom Computer Press, Boston, Mass. , 1996.
- Crosby, P. , Quality Improvement Through Defect Prevention, Philip Crosby Assosiates, 1985.
- Beecroft, G. Dennis, What is Your Quality Costing You? IIQP Newsletter, Winter 2000.
- Campanella, Jack (Ed. ). Principles of Quality Costs (Third Edition). ASQ Quality Press: Milwaukee, Wisconsin. 1999. 219pp.
- Harrington, H. J. , Poor Quality Costs, Mercel Dekker, Inc. , 1987.
- Morse, Roth, and Poston, Measuring, Planning, and Controlling Quality Costs, National Association of Accountant, 1987.
Related Questions
on External Failure and Internal Failure Cost
Cite this Page
External Failure and Internal Failure Cost. (2017, Apr 09). Retrieved from https://phdessay.com/external-failure-and-internal-failure-cost/
Run a free check or have your essay done for you
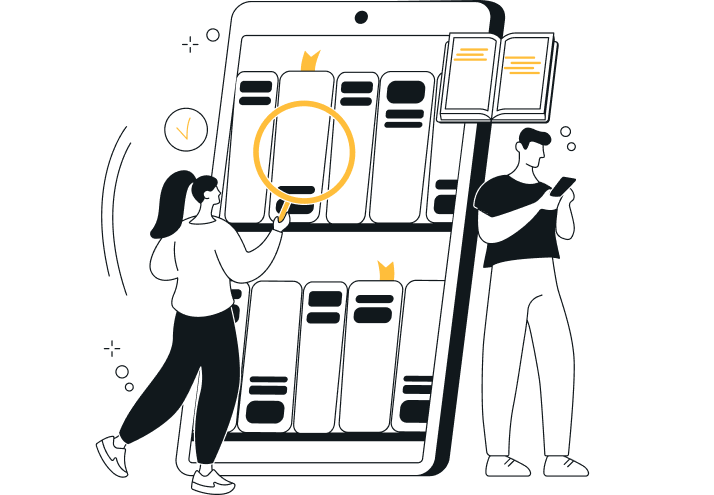