Donner Company
Donner Company is a Service oriented Manufacturing Company that makes printed circuit boards as per the specifications of its customers. Its customers are a variety of electronic manufacturers who need these custom-made printed circuit boards as a part of their supply chain. Their specialization was in making circuit boards for experimental devices and for pilot production runs. The business model hence is characterized by a need for handling Low-Volume, High-Customization products.
This necessitates high degree of flexibility within its Design and Manufacturing processes and Technological superiority. The president and the Chief Design engineer were veterans from the industry with patents on the applications, processes and modifications to the commercial industry. 1. 1 Document Scope The scope of this document is restricted is to a study and analysis of the operations of the company. The other aspects of the business model including Marketing, Market Research, Sales, R&D and Customer service have not been considered in the analysis report.
2. Process Flow The High Level pictorial flow diagram of the process flow of the company is depicted in figure (see Page 4 - Process Flow). A Brief Description of the process flow is detailed below. Sales Stage - Process Flow The Sales stage involves bidding for the customer's specification with a concrete proposal. The Sales stage starts from the Proposal Preparation to the Acceptance of the Proposal. The Proposal has the quoted cost and the quoted delivery time - which are estimated based on the inputs from the Operations team.
Order custom essay Donner Company with free plagiarism report
Once the order is accepted, the customer design is studied for feasibility. Factory order showing delivery date, the number of circuits, the material specifications and sequence of operations is written and the order is logged into the order system (log file) and sent for manufacturing. PROCESS FLOW Procurement and Job Scheduling Stage This stage deals with the procurement of the required raw materials. The principal raw material is the copper clad glass epoxy sheets. The procurement team orders the same based on the best quote from its supplier base.
The existing cycle-time for the procurement order placement is 1-2 days. The Job scheduling stage is the first step in the manufacturing process where the incoming order needs to be scheduled. The Operations Manager in Donner typically delays scheduling the job until the raw material arrives. Labour required in each step, work at critical points, difficulties in meeting dates, sales possibilities of these orders being held up, are all estimated, before the job is scheduled. Manufacturing Stage Preparation Phase . Donner's manufacturing process - Soldermask Over Bare Copper (SMOBC)
Three stages - Preparation, Image transfer and Fabrication. The artwork is used to produce a negative image pattern. The standard panel size used is 12" x 18". The glass epoxy laminate is inspected for defects and sheared into 12" x 18" panels. Location holes are punched on this. Image Transfer Phase Image transfer phase consists of Configuring the board according to customer specifications and then to transfer the pattern to the panel. About 500 holes are drilled either manually or automatically using CNC. The programming of the tool to drill the hole is different.
After drilling, Metallization deposits a layer of copper in the drilled holes. After metallization, the panels are washed, scrubbed and coated with DFPR. The customer artwork is laid on top and exposed to UV light. The film is developed. Then the copper conductors are electroplated. The DFPR is then stripped off in the next processing step. Then the copper layer which has not been previously electroplated is chemically etched off the glass epoxy base. The desired circuit pattern has been created on the board. Fabrication Phase
The panels are processed through Solder mask silk screening which leaves a protective epoxy coating on the circuit traces. The panels are then dipped into a molten solder bath and the exposed copper of the plated holes are covered with the solder. Profiling Each individual circuit board is separated from the panel and reduced to its desired finished size either be CNC routing or by stamping on a 20 ton punch press. Testing and Packaging The individual boards are visually inspected, electrically tested. This process was done manually. A senior employee was assigned to do this Quality Control (QC) Activity.
If there were any issues identified during this phase - then based on the nature of the defect - either a full rework is required or a partial rework is carried out. If there are no issues then the package is ready for shipment. Given below is the product process matrix of the current as well as the recommended positions for the product. Currently the company functions more as a job shop. This is amply evident due to three factors, 1. Donner Company extensively supports midway design change from the customer, thus providing greater process flexibility to support the customer.
2. It supports rush order which disrupt a more connected/continuous flow of work, thus reducing smooth flow of work as there would be in case of a more flow-oriented factory. 3. The larger proportion of small orders (not in terms of no: of boards but orders) indicate that the company works on lower standardization and more of a job oriented operation. The current recommendation for the company is to apportion its resources such that it works as a both a partial job shop and a partial process shop. This is indicated in the above product-process matrix.
Cite this Page
Donner Company. (2018, May 09). Retrieved from https://phdessay.com/donner-company/
Run a free check or have your essay done for you
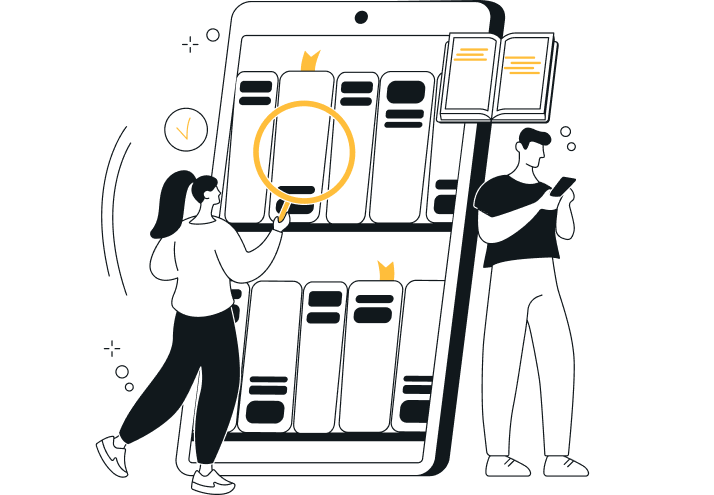