Costs Associated With Quality Management
The costs associated with quality management are divided into two categories. The classifications include cost of control, also known as cost of conformance, and cost of control failure, which is also known as costs of non-conformance. The costs of control can further be divided into two categories. Such subcategories are the prevention costs, which arise due to putting efforts so as to avert occurrence of defects, and the appraisal costs, which occur as a result of detecting defects through inspection, auditing or even tests (Mcdermott, Mikulak & Beauregard, 2008).
The costs of control failure are also subdivided into two categories which include the internal failure costs, which come as a result of defects found internally. Internal failure costs can be dealt with only by discarding or by repairing the items which are defective. The other category is the external failure costs which come by as a result of defects that can actually reach the customers. The categories can be further included in the classification of quality planning costs, systems development and management costs, and workforce development and quality training costs, which are all prevention costs.
Order custom essay Costs Associated With Quality Management with free plagiarism report
Appraisal costs include the costs of inspection, acceptance testing costs, checking labor costs, quality audits costs, and also the field testing costs (Chu, Altwies & Walker, 2005). The internal failure costs include the rework costs and the material procurement costs. External failure costs include the product liability costs, product service costs, and also the product recall costs. Prevention costs are costs related to implementation, designing and upgrading the management to top quality condition.
They should thus be incurred and planned before the actual operations. They include service or product requirement costs which are related to having a specification for the incoming materials, the processes, and finished products. Quality planning relates to creation of plans of quality, production, reliability and inspection (Hendriks & Vogtlander, 2002). Quality assurance relates to the costs of creating and maintaining quality systems. On the other hand, training costs are related to development, maintenance and preparation of quality improvement programs.
Appraisal costs are the costs which can be associated with material evaluation from outside vendors, process evaluation internally and any other services or products to make sure that finished products conform to the specifications. Verification costs relate to the costs incurred in checking the incoming materials and guaranteeing that the process setups are proper. Quality audits costs relate to the costs of external or internal certification to check if the quality system is functioning well.
Vendor ratings costs relate to the costs incurred during formal evaluations of suppliers of the services and products. Internal failure costs arise when processes fail to measure up to the designated standards of quality. They include the cost of scrap which is a defective product which cannot be repaired or used. Moreover, they include the costs of rework as well as the costs of failure analysis. External failure costs relate to the costs that arise when the products do not reach the designed quality standards but are discovered after they have reached the customer.
They include the costs of repairs and servicing of the products returned, warranty claims for the failed products, and the complaint costs for works associated with servicing the customer complaints. The manager’s interest to measure and monitor the costs which are associated with poor quality is to ensure that the products produced have reached the customer at the right quality. The customer is thus not exploited and does not consume products that do not reach the required health specifications since such products may be harmful (Harrop, 2002). Bibliography
Chu, Margaret Y. ; Altwies, Diane; & Walker, Edward. 2005. Achieve PMP exam success: A concise study guide for the busy project manager. Fort Lauderdale, FL: J. Ross Publishing. Harrop, Owen. 2002. Air quality assessment and management: A practical guide. Mortimer Street, London : Taylor & Francis. Hendriks, F. & J. G. Vogtlander. 2002. The eco-costs/Value Ratio (EVR): Materials and ecological engineering. Utrecht Area, Netherlands: Utrecht Area, Netherlands. Mcdermott, Robin E. ; Mikulak, Raymond J. ; & Beauregard, Michael, 2008. The basics of
Cite this Page
Costs Associated With Quality Management. (2018, Feb 14). Retrieved from https://phdessay.com/costs-associated-with-quality-management/
Run a free check or have your essay done for you
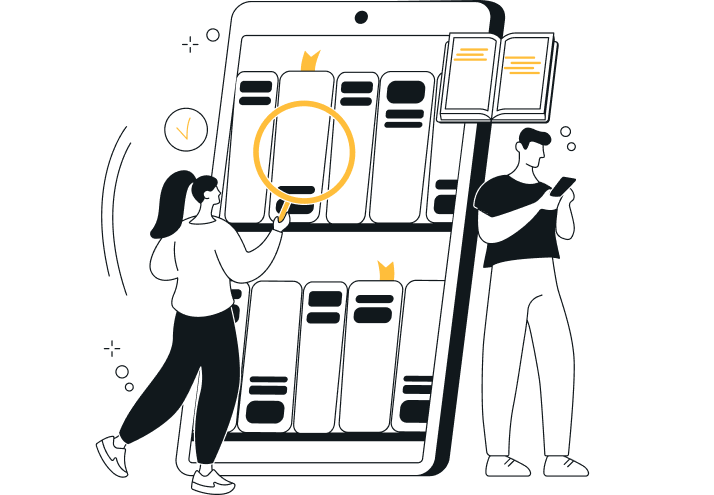