Cost Accounting System of Bpl
This report was originated to make a study about the cost accounting system of Beximco Pharmaceuticals Ltd. for the requirement of completion of 1st semester of Master of Business Administration (MBA) program of the Department of Accounting & Information Systems, University of Dhaka. This term paper was an attempt to acquaint the students with the real world situations so that the knowledge gained from the classroom is further strengthened.
As the classroom discussion alone cannot make a student perfect in handling the real business situation, therefore it is an opportunity for the students to know about the real life situation through this term paper.
Background of the Report
Order custom essay Cost Accounting System of Bpl with free plagiarism report
The importance of cost accounting and cost accounting information is being increased day by day. It is not only help to reduce cost but also in all kind of decision making. Without analysis of cost accounting information no manager can make effective decision. The cost accounting collects the data, analyze those data and help the managers to make better decision.
In accordance with development of new tools and techniques of cost accounting the use of cost accounting information is changing. Managers need to use the cost accounting information in different way from traditional method to evaluate the performance. Developing and accepting the JIT, TQM and other contemporary costing techniques force to manager to change the performance evaluation techniques and requires different cost accounting information unlike traditional labor based information now a day’s which become obsolete.
Primarily this report is concerned with cost accounting information by an organization in decision making as well as corporate reporting, the tools and techniques used by organizations and the implications of these in the organization. We select Beximco Pharma to examine the use of cost accounting information and cost accounting tools and techniques used by the company. We emphasize on the implication of using information and technique and examine whether Beximco Pharma use or not that particular techniques and the reason of following or not following based on our queries to respective authority of the company.
Scope of the Report:
This report is limited to the cost accounting department of the Beximco Pharma including cost accounting systems procedure and techniques. Since Beximco want to achieve top quality along with cost control it uses its cost accounting information very strongly. This report covers only the use of cost accounting information for the purpose of decision making and coporate reporting not overall performance of the Beximco Pharma.
Objective of the Report:
- to have a general idea about cost accounting information and its use in decision making.
- To have clear understanding about the cost accounting system used by Beximco Pharma. . Finding out the disclosure of cost accounting information used by the company.
- To draw a conclusion based on our understanding of Beximco Pharma.
Methodology of the Report: The details of the work plan are furnished below
The data and information for this report have been collected from both the primary and secondary sources. Among the primary sources, face to face conversation with the respective stuffs of the head office. The secondary sources of information are annual reports, websites, and study of relevant reports, documents and different manuals.
Data processing Data collected from primary and secondary sources have been processed manually and qualitative approach in general and quantitative approach in some cases has been used throughout the study. Data analysis and interpretation Qualitative approach has been adopted for data analysis and interpretation taking the processed data as the base.
Organization of the Report
This report is divided in to mainly 5 parts. The 1st part is introductory part that states the origin, background, scope, objectives, methodology of the report. The 2nd part is the literature review of the study.
This part explains the cost accounting information and its use in decision making by the managers. The next part discusses about the cost accounting system of Beximco Pharma. The 4th part finds out the contemporary methods and techniques of cost accounting used in Beximco Pharma. The last part concludes the report with some recommendation.
Limitation of the Report
There were some limitations in the preparation of the report. The source of the cost accounting system of the company was mainly based on their financial reports of different.
Though we conducted the responsible authority, they were reluctant to give us the full disclosure about their management policies. Because of such information is prepared for the management for internal use only, this was not available. Moreover, most of them were confidencial. Other limitations were our time constraint and resources to prepare an effective term paper on this topic.
Cost Accounting Information:
In a broad aspect, cost accounting refers to the measurement, analysis, and reporting financial and nonfinancial information relating to the cost of acquiring or using resources in an organization.
So cost accounting can be defined as the information obtained from cost accounting activities. For example, calculating the cost of product is a cost accounting function that answers manager’s decision making needs (such as choosing products to offer). Modern cost accounting takes the perspective that collecting cost information is a function of the management decision being made. Cost accounting information helps the manager in short-run and long-run planning and control decisions that increase value for the customers and lower the costs of products and services.
For example, managers make decisions regarding the amounts and kinds of material being used, changes in plant processes, and changes in product designs.
Cost Accounting Information in Decision Making:
For making decision by using cost accounting information cost accountant usually follow some specific models. They use different decision model for different courses of action. Management accountants work with manager by analyzing and presenting relevant data to guide decisions. For example, if any organization wants to reduce its existing manufacturing costs it must dentify the alternatives then it will analyze the alternatives by using only relevant data i. e. , which can influence the decisions. For making decision managers usually use five step decision process which is described below: Historical Costs Step-5 Step-4 Step-1 Obtain information Step-2 Step-3 Other Information Make prediction about future costs Specific prediction Choose an alternative Implement the decision Evaluate performance
Factors regarding decision making using cost accounting information: There are several factors that affect the decision making procedure of the managers.
Some important factors are discussed here: a. Relevant costs and relevant revenues: Relevant costs are expected future costs and relevant revenues are expected future revenues that differ among the alternative courses of action being considered. Both relevant costs and relevant revenues must occur in future and they differ among the alternative courses of action. Focusing on the relevant data is especially helpful when all the information needed to prepare detailed income information is unavailable.
Understanding which costs are relevant and which are irrelevant helps the decision maker concentrate on obtaining only the pertinent data and saves time.
Qualitative and quantitative relevant information: Manager defines and weighs qualitative and quantitative information.
Quantitative information are those which can be measured by the numerical number and qualitative information are those which cannot be measured by the number and off course manager will decide which one is measurable by the number and which one is not.
Relevant cost analysis generally emphasis on quantitative factors but qualitative factors also have their own importance.
One time only special orders: When factory has idle production capacity then manager must decide whether accepting or rejection special orders if special order has no long implications. Example: if any company has capacity to produce 18000 units and currently producing 16000 units. The total cost (fixed-5 and variable-5) per unit is tk. 10. If they got an order to deliver 4000 units for tk. 6 per unit they should accept it.
But if they get the order of 5000 units they should not accept it because it crosses its relevant range. To make decision about special onetime order only relevant cost should be considered. A common term in decision making is incremental cost which means additional cost for producing every additional unit is also important in this regard. d. Insourcing Vs. Outsourcing and Make Vs. Buy decision: Outsourcing or Bye decision is purchasing goods and services from outside rather than producing in inside of the organization. Whether bye or make is sometimes influenced by qualitative factors.
For example coca-cola company will never do outsourcing due to secrecy of the formula, know-how, and technology. In order to make decision if bye or make manager usually take into consideration about quality, dependability, material handling and set-up activity. And off course manager does cost benefit analysis based relevant cost information. e. Focusing on grand total: Manager will focus on grand total cost in making decision rather than unit cost. Sometimes unit cost could be misleading. If we want to make decision about make or buy, insourcing vs. utsourcing we need to consider total cost not unit cost. f. Using constrained resources: Under this condition, manager should select the product that yields the highest contribution margin per unit of the constraining or limiting resources. g. In deciding whether add or drop customer or to add or discontinue segment: Manager should focus on whether total overhead cost change in making decision about adding or dropping customer or adding or discontinuing segment. Manager should ignore allocating overhead cost. h. Replacement of equipment:
In the time of equipment replacement existing book value is irrelevant because it is a sunk cost so it should be ignored. i. Concentrate on consistency on performance evaluation: There is always a confliction between the decision model used by a manager and the performance model used to evaluate that manager. Top management must ensure that the performance evaluation model will be consistent with decision model. A common inconsistency is to tell these managers to take a multiple year view in their decision making but then to judge their performance only on the basis of current year’s operating income.
If there is no consistency between performance evaluation and performance model then control will be impossible and making decision model will be valueless.
Cost Accounting Information in Corporate Reporting:
The main purpose of cost accounting information is to help managers in decision making. Such information is provided for the internal purpose only. There are some guided rules and regulations about the information in the reports. According to IAS 1 (Presentation of Financial Statements), aragraph 117, ‘’ An entity shall disclose in the summary of significant accounting policies: (a) the measurement basis (or bases) used in preparing the financial statements, and (b) the other accounting policies used that are relevant to an understanding of the financial statements. ” It is important for an entity to inform users of the measurement basis or bases used in the financial statements (for example, historical cost, current cost, net realizable value, fair value or recoverable amount) because the basis on which an entity prepares the financial statements significantly affects users’ analysis.
When an entity uses more than one measurement basis in the financial statements, for example when particular classes of assets are revalued, it is sufficient to provide an indication of the categories of assets and liabilities to which each measurement basis is applied. According to paragraph 125 of the same IAS, “An entity shall disclose information about the assumptions it makes about the future, and other major sources of estimation uncertainty at the end of the reporting period, that have a significant risk of resulting in a material adjustment to the carrying amounts of assets and liabilities within the next financial year.
In respect of those assets and liabilities, the notes shall include details of: (a) their nature, and (b) their carrying amount as at the end of the reporting period. ” An entity presents the disclosures in paragraph 125 in a manner that helps users of financial statements to understand the judgements that management makes about the future and about other sources of estimation uncertainty. The nature and extent of the information provided vary according to the nature of the assumption and other circumstances.
Examples of the types of disclosures an entity makes are: (a) the nature of the assumption or other estimation uncertainty; (b) the sensitivity of carrying amounts to the methods, assumptions and estimates underlying their calculation, including the reasons for the sensitivity; (c) the expected resolution of an uncertainty and the range of reasonably possible outcomes within the next financial year in respect of the carrying amounts of the assets and liabilities affected; and (d) an explanation of changes made to past assumptions concerning those assets and liabilities, if the uncertainty remains unresolved.
Other IFRSs require the disclosure of some of the assumptions that would otherwise be required in accordance with paragraph 125. For example, IAS 37 requires disclosure, in specified circumstances, of major assumptions concerning future events affecting classes of provisions. IFRS 7 requires disclosure of significant assumptions the entity uses in estimating the fair values of financial assets and financial liabilities that are carried at fair value.
IAS 16 requires disclosure of significant assumptions that the entity uses in estimating the fair values of revalued items of property, plant and equipment. There are also some guidelines for reporting cost accounting information in IAS 2: Inventories. The objective of this Standard is to prescribe the accounting treatment for inventories. A primary issue in accounting for inventories is the amount of cost to be recognised as an asset and carried forward until the related revenues are recognised.
This Standard provides guidance on the determination of cost and its subsequent recognition as an expense, including any write-down to net realizable value. It also provides guidance on the cost formulas that are used to assign costs to inventories. Measurement of inventories Inventories shall be measured at the lower of cost and net realisable value. Cost of inventories The cost of inventories shall comprise all costs of purchase, costs of conversion and other costs incurred in bringing the inventories to their present location and condition.
Costs of purchase The costs of purchase of inventories comprise the purchase price, import duties and other taxes (other than those subsequently recoverable by the entity from the taxing authorities), and transport, handling and other costs directly attributable to the acquisition of finished goods, materials and services. Trade discounts, rebates and other similar items are deducted in determining the costs of purchase. Costs of conversion
The costs of conversion of inventories include costs directly related to the units of production, such as direct labour. They also include a systematic allocation of fixed and variable production overheads that are incurred in converting materials into finished goods. Fixed production overheads are those indirect costs of production that remain relatively constant regardless of the volume of production, such as depreciation and maintenance of factory buildings and equipment, and the cost of factory management and administration.
Variable production overheads are those indirect costs of production that vary directly, or nearly directly, with the volume of production, such as indirect materials and indirect labour. The allocation of fixed production overheads to the costs of conversion is based on the normal capacity of the production facilities. Normal capacity is the production expected to be achieved on average over a number of periods or seasons under normal circumstances, taking into account the loss of capacity resulting from planned maintenance.
The actual level of production may be used if it approximates normal capacity. The amount of fixed overhead allocated to each unit of production is not increased as a consequence of low production or idle plant. Unallocated overheads are recognised as an expense in the period in which they are incurred. In periods of abnormally high production, the amount of fixed overhead allocated to each unit of production is decreased so that inventories are not measured above cost.
Variable production overheads are allocated to each unit of production on the basis of the actual use of the production facilities. A production process may result in more than one product being produced simultaneously. This is the case, for example, when joint products are produced or when there is a main product and a by-product. When the costs of conversion of each product are not separately identifiable, they are allocated between the products on a rational and consistent basis.
The allocation may be based, for example, on the relative sales value of each product either at the stage in the production process when the products become separately identifiable, or at the completion of production. Most by-products, by their nature, are immaterial. When this is the case, they are often measured at net realisable value and this value is deducted from the cost of the main product. As a result, the carrying amount of the main product is not materially different from its cost. Disclosure of Inventory in Financial Statesments The financial statements shall disclose: a) the accounting policies adopted in measuring inventories, including the cost formula used; (b) the total carrying amount of inventories and the carrying amount in classifications appropriate to the entity; (c) the carrying amount of inventories carried at fair value less costs to sell; (d) the amount of inventories recognised as an expense during the period; (e) the amount of any write-down of inventories recognised as an expense in the period in accordance with paragraph 34; (f) the amount of any reversal of any write-down that is recognised as a reduction in the amount of inventories recognised as expense in the period in accordance with paragraph 34; (g) the circumstances or events that led to the reversal of a write-down of inventories in accordance with paragraph 34; and (h) the carrying amount of inventories pledged as security for liabilities. Information about the carrying amounts held in different classifications of inventories and the extent of the changes in these assets is useful to financial statement users. Common classifications of inventories are merchandise, production supplies, materials, work in progress and finished goods. The inventories of a service provider may be described as work in progress.
The amount of inventories recognised as an expense during the period, which is often referred to as cost of sales, consists of those costs previously included in the measurement of inventory that has now been sold and unallocated production overheads and abnormal amounts of production costs of inventories. The circumstances of the entity may also warrant the inclusion of other amounts, such as distribution costs.
An overview of Beximco Pharma Beximco Pharmaceuticals Ltd. is a leading edge pharmaceutical company and is a member of the BEXIMCO Group, the largest private sector industrial conglomerate in Bangladesh. The strategic strengths of Beximco Pharma are its strong brand recognition, highly skilled work force and diversified business mix.
Beximco Pharma brands - Neoceptin R (Ranitidine), Napa (Paracetamol), Amdocal (Amlodipine), Neofloxin (Ciprofloxacin), Bexitrol F (Salmeterol Plus Fluticasone), Bextrum Gold (Multivitamin and Multi Mineral) and Atova (Atorvastatin) are among the most recognized brands in the Bangladesh Pharmaceutical industry. Beximco Pharma started its operation in 1980, manufacturing products under the licenses of Bayer AG of Germany and Upjohn Inc. of USA and now has grown to become nation's one of the leading pharmaceutical companies, supplying 15% of country's total medicine need. Today Beximco Pharma manufactures and markets its own `branded generics' for almost all diseases from AIDS to cancer, from infection to asthma, from hypertension to diabetes, both nationally and internationally.
Beximco Pharma manufactures a range of dosage forms including tablets, capsules, dry syrup, powder, cream, ointment, suppositories, large volume intravenous fluids, metered dose inhalers etc. in several world-class manufacturing plants, ensuring high quality standards complying with the World Health Organization (WHO) approved current Good Manufacturing Practices (cGMP). The recipient of three times `gold' national export trophy, Beximco Pharma is the largest exporter of pharmaceuticals from Bangladesh, spreading its presence in many developing and developed countries across the globe. Beximco Pharma is the only company in Bangladesh to receive this highest national accolade for export, for record three times. Beximco Pharma markets its brands through professional sales and marketing teams in African, Asian and European markets.
It also supplies its products to renowned hospitals and institutions in many countries, including Raffles Hospital and K K Women & Children Hospital in Singapore, MEDS and Kenyatta National Hospital (KNH) in Kenya, Jinnah Hospital, Agha Khan Hospital and Shaukat Khanum Memorial Hospital in Pakistan. Beximco Pharma is also an enlisted supplier of WHO and UNICEF. Another important business activity of Beximco Pharma is the contract manufacturing for major international brands of leading multinational companies. Beximco Pharma is acclaimed domestically and internationally for its outstanding product quality, world class manufacturing facilities, product development capabilities and outstanding service.
Beximco Pharma has a strong market focus and is anticipating continued future growth by leveraging business capabilities and developing superior product brands and markets. In particular the company is very interested in developing a strong export market in USA and Europe. To meet the future demand Beximco Pharma has invested US$ 50 million to build a new state-of-the-art manufacturing plant, confirming to USFDA and UK MHRA standards. This new plant will also offer contract-manufacturing facility to leading pharmaceutical companies, especially from Europe and US. 3. 2 Cost Accounting System of the company: The company primarily uses batch costing method in their costing system.
As a pharmaceuticals manufacturing company they need to produce huge amount of product so here batch costing is appropriate for the company. Here it is cost effective and easy to calculation. Batch costing has the several advantages over other methods in regard of the providing following information: -the analysis and the cost control at each cost generator; -the operative management of each place generator of costs, the specification of the production and of the predicted costs and their control and realization; -the correct assessment of the produced stocks; -determination of the efficiency obtained by the taken decisions. The company uses weighted average method in time of inventory valuation.
They believe that it gives more accurate and clear picture of inventory. In this method it is very hard to manipulate and easy to calculate though it has a limitation that it sometimes can’t represent inflation.
Valuation of Inventories:
Inventories are carried at the lower of cost and net realizable value as prescribed by IAS 2: Inventories. Cost is determined on weighted average cost basis. The cost of inventories comprises of expenditure incurred in the normal course of business in bringing the inventories to their present location and condition. Net realizable value is based on estimated selling price less any further costs expected to be incurred to make the sale.
Cost included for the local raw materials purchased are 1) Procurement Cost. 2) Transportation Cost 3) Bank Charge Cost included for the imported raw materials are 1) Procurement Cost 2) Bank Charge for Opening L/C 3) Insurance 4) Clearing from the Port and 5) Transportation Cost. 3. 4 Disclosure of Inventory in Financial Statements According to IAS 2: Inventories, the Company disclosed the following information regarding inventory: (a) The Company uses weighted average method in measuring the inventories. (b) The total carrying amount of inventories is tk 1,739,818,419.
Contemporary cost accounting methods and techniques used by Beximco Pharma: Beximco Pharmaceuticals Ltd is a leading company in our country. To compete with the other companies in the industry, Beximco Pharma uses several contemporary methods and techniques. Mass production of a mature product with known characteristics and a stable technology was the basis of traditional cost accounting models. Anyway, Beximco Pharma, with automation, lessened the labor content in manufacturing process while the other costs in the company are increased. Flexible manufacturing system: Flexible manufacturing systems use computer controlled production processes, ncluding CAD/CAM programmable machine tools. Because flexible manufacturing reduces setup or changeover times, companies can efficiently manufacture a wide variety of products in small batches. Though Beximco Pharma can adopt flexible manufacturing system, it merely reduces the size of the batch. Total quality management: Total Quality Management refers (TQM) to the process of continuous improvement to achieve the full customer satisfaction. Rather than waiting to inspect items at the end of the production line or striving to stay within acceptable tolerance limit, TQM’s goal is eliminating all waste. In Beximco Pharma, quality is maintained with great care.
As it is a pharmaceutical company, it is mandatory to keep up with the quality level with the other companies. As a result, they have received GMP Clearance from Therapeutic Goods Administration (TGA) of Australia and from Gulf Central Committee for Drug Registration, Executive Board of the Health Ministers' Council for Gulf Cooperation Council (GCC) states (representing Saudi Arabia, Kuwait, Bahrain, United Arab Emirates, Qatar and Oman). The company is also in the process of obtaining approvals from several other regulatory authorities including National Health Surveillance Agency (ANVISA) of Brazil, Medicine and Healthcare Regulatory Agency of United Kingdom (UK MHRA), US FDA etc. Just in Time Concept:
The Just in Time (JIT) minimizes throughput time by emphasizing continuous improvements. JIT reduces inventories by achieving a continuous production process. In JIT system, employees keep on hand only the inventory needed to production until the next order arrives. Having fewer goods in hand not only requires less warehouse spaces and storage equipment but also reduces inventory holding cost, while realizing productivity. For implementing JIT, company must need a strong supply chain system. In Beximco Pharma, they can’t follow JIT because most of the inventory or raw materials are come from abroad so it is impossible to implement JIT in Beximco Pharma.
If they want to implement JIT their cost will be higher rather than being lower because here ordering cost is very high as raw materials are imported. Beximco use EOQ model to determine their ordering size and they have large storage facilities. Pull Rather than push system: Pull system refers to decision will come from downstream of management. The factory production line operates on a demand pull basis. A pull system can only work while manufacturing process can react to a pull system. However Beximco Pharma doesn’t follow the pull system they use push system. The authority of Beximco Pharma believes that push system is more effective than pull in the context of Bangladesh.
Because of JIT is not possible in the firm, pull system is difficult to implement because in pull system it is believed that it is better not to produce unnecessary products and do not keep inventory in hand. Activity-Based Management: The activity-based management system links resources consumption to the activities a company performs and cost the activities to product or customers. Activity-based management uses activity based costing systems to measure and control this relationship. In Beximco Pharma there is no such use activity cost driver to measure the cost of a product. The traditional system is used to determine the cost of the product.
Life Cycle Costing:
Life cycle costing tracks and determines the cost attributed to each product and service from its initial research and development to development to final marketing to customer. In Beximco Pharma, this type activities is done in mainly in the Central Product Management (CPM) Department. The activities of CPM are:
- Market research
- Selection of new product
- Design and testing of product (DTP)
- Sample store (logistics) management
- Making strategy The department deals with the controllable marketing variables, the 4p's.
This department takes decisions in the following areas:
- Product - Size, color, shape, packaging etc.
- Price - Raw materials cost, customer ability, regulatory body's approval etc.
- Promotion - Promotional aids include brochure, pads, folder, and plant visit by physicians, health-related people, students, and people of different student.
Other than this department, in January, 2000, the Business Research ; Development department was established.
The functions that are done by this department are:
- Outsourcing negotiated
- New product study
- New technology study
- Project feasibility study
- Commercial negotiation
- Observing the world pharmaceuticals market
With these departments, Beximco Pharma determines the Life Cycle of the products.
Target Costing: Target costing is an approach which determines what a product or service should cost based on its sales price less a target profit.
Unlike traditional costing for making up cost, it is a market driven way of examining the relationship of price and cost. In Beximco Pharma, the use of Target Costing is very common to make the target for the cost of the product. Change In performance Evaluation: The adoption of JIT, life cycle costing and other innovative techniques requires new performance evaluation techniques rather than traditional productivity measures because it is irrelevant in this context. The use of single short term profit measure may not be sufficient because it is not reliable indicator of managers’ ability. Profit may be increased by doing some activities which are not conform to companies overall organizational goal.
Goal Congruence: this performance measures should encourage manager to achieve overall organizational goal. The Beximco Pharma does not explain the measurement of the performance of the employees. In general, some marketing employees get benefited if the sales volume is high. But the total performance evaluation system depends in the decision of the management. Concluding Remarks: Beximco Pharmaceuticals Ltd. is a leading edge pharmaceutical company and is a member of the BEXIMCO Group, the largest private sector industrial conglomerate in Bangladesh. Beximco Pharma is also the largest exporter of pharmaceuticals from Bangladesh, spreading its presence in many developing and developed countries across the globe.
Recently, BPL has successfully made its footmark in the global market when it made its debut on the London Stock Exchange as the first Bangladeshi company to be listed in the world's most prestigious bourse. This milestone event has widened the responsibility, accountability and transparency of the company beyond geographical border. The listing adds new challenges to the staffs of Accounts & Finance department who are directly responsible for financial reporting to a diverse group of stakeholders both in national and international arena. In this report, we have tried my level best to identify cost accounting techniques and procedures used by Beximco Pharma.
What and how Beximco Pharma use cost accounting information for decision making and external financial reporting along with describing the procedure and systems of using cost accounting information. In this report, we imply our acquired knowledge from cost accounting course and try to comply with the techniques procedure and systems followed by the company. Beximco believes that quality and control should be ensured and these can be ensured by using proper cost accounting information. Relevant and reliable cost information can be ensured by implementing by using effective cost accounting methods. And they do the best one fit in the context of Bangladesh.
References:
- Horngren, Charles T. , Datar Srikant M. , Foster, G. ; “Cost Accounting: A Managerial Approach”, Prentice Hall, Inc. ; 12th Edition, 2007.
- Rayburn, Latricia G. ; “Cost Accounting: Using A Cost Management Approach”; Irwin Book Team; 6th Edition, 1996.
- Hansen, Don R. , Mowen Maryanne M. ; “Cost Management: Accounting and Control”; South-Western College Pub; 5th edition, 2005.
- “International Financial Reporting Standard”; International Accounting Standard Board; as approved at 1 January, 2008.
- http://www. beximco-pharma. com
- http://britannica. com
- http://en. wikipedia. org
- http://www. bizmanualz. com
- http://www. iasplus. com
Cite this Page
Cost Accounting System of Bpl. (2016, Dec 09). Retrieved from https://phdessay.com/cost-accounting-system-of-bpl/
Run a free check or have your essay done for you
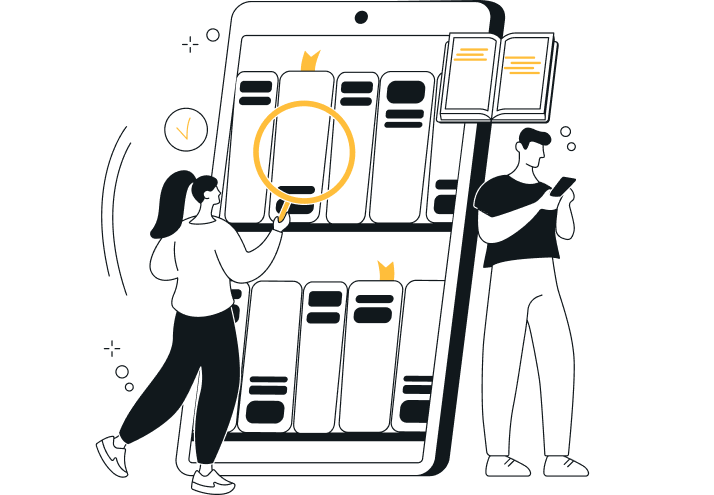