Bayonne Case
Management Operations - BAYONNE PACKAGING, INC.
In a company like Bayonne Packaging, Inc., a printer and paper converter, it is very important that performance measures such as cost, quality and delivery are in agreement with the forecasted values since this firm used to compete based on low cost, good quality and time delivery. Once one of these three performances is damaged, many hidden problems will be aroused. On the contrary, the organization can have a reduction of transaction costs as well as an increase of benefits.
The purpose of this report is to understand the trade-offs among the three performance measures while increasing the complexity of customer ordering requirements and how information flow and production control rules affect operations. Afterwards answer the questions that new VP Operations, John Milliken is asking himself.
Order custom essay Bayonne Case with free plagiarism report
First of all we started to answer the guideline questions. We computed the current capacity utilization in the work centres, and then we found the capacity in pieces of the die-cut work centres, in the different ganging choices (no gangins, ganging pairs of orders or ganging all of the orders). After this we had to focus on the differences between partialed and non-partialed orders of the Royal/Queen work centres so we could analyze the changes in capacity. Concerning the Fold&Glue department, Bayonne Inc. can choose between Royal/Queen and Staude machines, we computed the optimum batch quantity, according to orders’ volume. To conclude about the efficiency of some work centres we computed the yields, including the cumulative one. Finally we examined the exhibit 4 so we could infer about the value of actual shipments in October. With these answers we answered to Milliken’s questions, stated at the case.
Based on the analysis, it is possible to give some useful recommendations that could help the organization to develop and improve its current situation. One of the most problematic work centre is Fold&Glue so we believe the recommendations we made about this department are the most important ones.
Introduction
This study is based in a brief case from Harvard Business Publishing by Shapiro & Morrison where the current situation of Bayonne Packaging, Inc. is presented to us. Over the past ten years, this company never registered any losses, so when it happened, the President of the Company felt the need to hire a new VP Operation. His first act was touring over all departments of the factory in order to identify and solve the main problems that firm is facing.
The report begins with a brief company and industry background and then we perform a process analysis in order to understand better how the production flows through the work centres in Bayonne Inc.
Finally, some recommendations were made based not only in our interpretation of the problems stated on the case but also on the theoretical and practical concepts of Operations Management.
Company Overview
Dave Rand is the President of the company analyzed on the case, Bayonne Packaging, Inc., which was founded in 1964 by his father.
This firm is a 43 million paper converter that produces customized packaging to deliver promotional materials, software, luxury beverages, and gift food and candy, used by industrial customers. This company provides full services from design through final delivery and is specialized in creating innovative packaging solutions.
Even though Bayonne’s sales grew from 10 million in 1982 to 32 million in 2001, in 2011 “they ran a loss for the first time since 2001”.
At the end of the same year, President Rand hired a new VP Operations, Milliken, in order to handle operational problems related with cost area, quality problems and late deliveries. In January 2012 as he investigated the challenges in the current production process, he met most of key departments and work centres by touring the factory.
Industry Overview
Bayonne Packaging, Inc is in the paper packaging industry. In the 1980s and early 1990s companies in the consumer goods industry start to look for a greater impact with their promotional materials and star to implement their promotional budget to the package itself instead of print media and broadcast forms. This led to a rapidly growth on the paper packaging industry. Also, additional customer market segments made a quick impact in a crowded marketplace due to the explosive growth of software packaging. These factors give good reason for the growth in sales from 10 million in 1982 to 32 million in 2001. New challenges were faced with the bursting of the dot-com bubble and when software sales and distribution moved from CDs to the Internet, but Bayonne dealt well this challenges by adopting a strategy of diversification into new markets.
Process Analysis
To make some recommendations concerning the production process of Bayonne Inc., we need to do the process analysis, in order to be able to closer understand how the production flows through the different work centres work and what kind of problems and inefficiencies arise from this process. Assumptions: because it was not requested to use a single unit flow we used different ones (sheets/pieces/orders) according to what it was asked in each question, in order to simplify our work.
Current Capacity Utilization of the Work Centres
To compute the capacity of the work centres we assumed the 347 work hours scheduled for October 2011 as the total working time. We calculated the
ratio between the total number of hours that each machine/work centre worked by the total working time to get the capacity utilization.
COMPOSITION
0,734870317
JAGENBURG SHEETER
0,804034582
HEIDELBERG SHEETER
1,002881844
BOBST DIE-CUT
0,783861671
ROYAL/QUEEN F&G
0,449567723
STAUDE F&G
0,515850144
3A WINDOW/PATCH
0,417867435
We can conclude that the Composition, Sheet, Print and Die-Cut departments have an adequate capacity (the fact that the Heidelberg Sheeter is running at more than 100% capacity can be explained by the fact that we are using schedule working hours and standard hours, which can differ from reality). On the other hand the Fold&Glue department, that contains the machines Royal/Queen, Staude and 3A is not working near full capacity. Actually it is just working around half of its capacity, which can anticipate some of the problems on this department.
Ganging Orders
By reading the case we became aware of the practise of ganging, in which orders with similar set up characteristics are run together after a single setup. In this question we calculated the capacity in pieces per day for the Die-Cut Work Centre regarding three different situations of ganging: none of the orders are ganged, pairs of orders are ganged and all of the orders can be ganged.
First of all, since we know that the Die-Cut centre was running orders of 30000 pieces, we converted this value into sheets. Assuming that each shift works 7.5 hours (because they do an half an hour break in the middle of their 8-hour shift) and that are two shifts, there are 30 daily working hours, 1800 minutes.
Next, we found how much it takes to make one order none-ganged (multiplying the number of sheets of one order by the running time and adding the setup time) and discovered how many orders can the Die-cut department execute (dividing the daily working minutes by the number of minutes one order takes to be executed). After this we just multiplied the aftermath by the number of pieces per order. We had computed the Capacity in pieces if the Company was non-ganging.
If Bayonne decides to do pairs of orders ganged, they include two orders in the same setup so we multiplied the number of sheets by two times the running time and add just one setup time to get the time it takes to do two orders. We divided the previous value by two, in order to find out the time it would take to make only one order. We divided it again, by the total number of working hours to get the number of orders per day. Once again, we multiplied this value by the number of pieces per order to get the capacity in pieces.
Finally, if they decide to gang all the orders, this would mean that they would do only one setup per machine, so the total daily working minutes is now lower (1500min). We subtracted this number to the daily working hours to get the time it takes to do the two setups. One more time we determined how much time it takes to execute one order (the number of sheets multiplied by the running time) and the number of orders per day (daily working minutes/time 1 order), so we could reach the capacities in pieces.
Number of sheets
10000
Number of Machines
2
Daily Working Hours
30
Daily Working Minutes
1800
Running Time
0,0075
SetUp Time
150
Minutes 1 order
225
Number of orders per day
8
Pieces/Order
30000
Capacity in pieces (None ganged)
240000
Minutes 2 orders
300
Minutes 1 order
150
Number of Orders per day
12
Capacity in Pieces(Pairs ganged)
360000
Daily Working Minutes
1500
Time 1 order
75
Number of Orders/Day
20
Capacity in Pieces(All ganged)
600000
By running these calculations we can now conclude that ganging the orders does increase the capacity in pieces. Ganging all the orders more than doubles the capacity in this work center compared with the non-ganging procedure.
The effects of doing partials
Regarding this, we focused on the capacity of the Royal/Queen work centre and we tried to analyze the effects and consequences of partialing. Assuming that during the month of October, 40 of the orders were partialed. Each one of it caused one broken production and consequently the need to do two setups in the work center. We can compare the capacity without these additional setups with the capacity in fact.
We started by dividing the number of orders scheduled for the number of pieces scheduled, in order to obtain the number of pieces per order on this month.
Since we have three machines in this work center, we calculated the total working time multiplying the 347 hours (used before) by the 3 machines and turn it out into minutes. After we calculated the time it takes to do one order (running time multiplied by the number of pieces per order, plus the set up time) we computed the capacity of orders per month (dividing the total time for the time it takes to do one order).
In order to calculate “the capacity in fact”, taking into consideration the additional setups, we calculated the time spend doing partialed orders assuming 80 setups and 40 running times, since we are now assuming half orders for the setups.
Because not all of the orders were partialed we still have to consider the time left for doing the rest of the orders scheduled for October. The available time for these orders is the total working time minus the time spent in the partialed orders. So in order to reach the capacity value we divided the available time by the time it takes to do a non-partialed order.
Setup Time
180
Running Time
0,0023
Orders October Royal/Queen
77
Pieces Schedule R/Q
6209329
Pieces per order
80640,63636
Number of Machines
3
Total Time (Min)
62460
Time 1 order
365,4734636
Capacity Orders per Month
170,9016008
Number of Partialed
40
Half Orders
80
Time of Partialed Orders
14400,092
Available Time
48059,908
Capacity Orders per Month
131,5004037
In the end we can see that the partialing done in the Royal/Queen work center
decreases the capacity in orders per month.
Size of Orders
As said in the case the Royal/Queen machines are high speed machines with a complex setup, so they are more appropriate for high volume jobs. The Staude machines are the opposite, they are slower but easier to set up, being better for low volume jobs. As doing this production process, it is important to know the size of orders to know when we should change from one machine to the other, ie the threshold between low volume/size and high volume/size.
Royal/Queen
Staude
Pieces
(180+0,0023Q*)
(40+0,015Q*)
0
180
40
1500
183,45
62,5
3000
186,9
85
4500
190,35
107,5
6000
193,8
130
7500
197,25
152,5
9000
200,7
175
10500
204,15
197,5
12000
207,6
220
13500
211,05
242,5
15000
214,5
265
By finding the intersection point between the two functions: the times it takes to produce several pieces in the Royal Machine and the time it takes to produce the same pieces with the Staude Machine, we reach the quantity of 11.023,622 pieces, that is the value from which we consider a order as being with high volume.
Losses in the Production Process
In order to interpret and find reasons to the losses during the production process we focused on the yield of each work center. Looking at exhibit 3 (Material Flow Through Operations), we can compute the yields of the Sheet, Print, Die-Cut and Royal/Queen work centers by dividing the number of pieces out by the number of pieces in.
Yield Sheet
0,992999966
Yield Print
0,983000062
Yield Die Cut
0,990000013
Yield Royal Queen
0,899999984
After this we calculated the cumulative yield of these three work centers by multiplying the previous yields and got the value of 0,86972205. This means that as the production goes through these four departments, approximately 13% of production is lost. If we consider that 40000 sheets or 120000 pieces go in to the sheet department, 104366,646 will go out the Royal/Queen Work Centre (they are allocated to this work centre because we assumed that an order with 120000 is a high volume order), only 15633,35399 pieces are lost in the production process. Shipments in October
For the analysis of the data from the Exhibit 4 (Value of Actual Shipments in October) we made a graph comparing the Orders Shippped, Late and Partialed.
Because in October closes the fiscal year we realize that the company is trying to do as many orders as possible, in order to increase its revenues (we know they follow a policy that recognizes the revenues the moment the client is billed, which happens right after the shipment). In fact this is not a good policy because they haven’t received the payments yet and they are not taking into consideration the fact that some of these orders will be defective and they will be returned. The number of late orders by the end of October can show that, once again, Bayonne will have many complains concerning the delivery time because they will start the following month having late orders already. This event will affect the whole process and significantly decrease the quality since we know that the work centre tends to partialize more when there are orders getting close to the delivery date or already late.
Main Problems and recommendations
Instead of high sales and revenues, the company is facing some problems related to costs, quality and delivery. Costumers complained about quality and the late delivery of products, what explains their rejection (exhibit 1).
Regarding Quality Control, the main problems were related to Fold&Glue department. The products have missing glued lines or have excess glue. In this department, die-cut blanks were turned into finished good and the workers do not assume the problems’ responsibility, arguing that they receive the products two days before the due date or even late already. They try to execute the products rapidly but there are already other orders ahead. The rush orders are also a problem because to get these orders done they have to break the first ones, making the fold and glue process by partials. Due to high volumes of orders, the company performs glue process faster than it should, endangering the quality of products. To be precise, they do not wait until the products are completely dried. As a consequence of this situation, for the first time since 2001, in October 2011, 6% of pieces were defective and the costumers rejected 1%. We believe that despite it seems the Fold&Glue department has all of the problems; the Printing department is the one that actually delays the process – the called bottleneck. Its capacity utilization is almost reaching 100% but the products don’t get in time to the die-cut department. In order to solve this problem we recommend the increase Printing department’s capacity, for example, by buying more printers and/or faster printers. This would be a good long-term measure that would increase the quality of the process. At the same time, the managers should provide training to their workers so they could develop their techniques and skills. Concerning Finishing department, some orders are shipped without pieces, so the customers return them back to the company and then workers revise them. Actually, the company has one inspector for Composition, Sheeting, Printing, and Die-cut and another for “Fold & Glue” and Shipping. However, they should increase the number of inspectors on shipping department, as well as, increase the number of pieces they check in every hour (actually two). Although, this decision should be taken taking into consideration the losses from last year, comparing this number to the money they would spend on the wages of the additional inspectors.
Another one of the biggest problems the company is facing is the delivery performance. On October 2011 the late orders were more than 20%. Furthermore, the company sells some pieces to other clients for a higher price. Additionally, they invested in strong marketing campaigns that require delivering on time, otherwise the costumers will complain and Bayonne’s reputation can be damaged. The recommendation is the company should deliver the orders to the respective customers, instead of selling to others at a higher price. This is an important issue because delivering on time is crucial not only to keep the old costumers but also to win new ones, especially in new kind and segments of products. Despite the managers’ daily meetings, where they discuss what went wrong in the previous expeditions and talk about the status of actual orders, there are still some problems concerning the time delivery. The plant scheduler cannot warn Sales department every time an order is late because sometimes they are not sure about it and they hope to get a part of order ready on time.
Moreover, the Composition, Sheeting, Printing, Die-cut and Fold & Glue departments send inaccurate data reports forcing Scheduling Section to spend time spelling out information registered by operators in Work Order Jacket. The data included in the report is not precise because operators inspection the orders, not following the production date but if they have another order they want to ship before, they inspection it even though they did not finish the previous inspection. To avoid this situation, operators should inspection and register pieces in Work order jacket, following all phases of the process and order of parcels, avoiding break orders into runs.
Cite this Page
Bayonne Case. (2018, Feb 10). Retrieved from https://phdessay.com/bayonne-case/
Run a free check or have your essay done for you
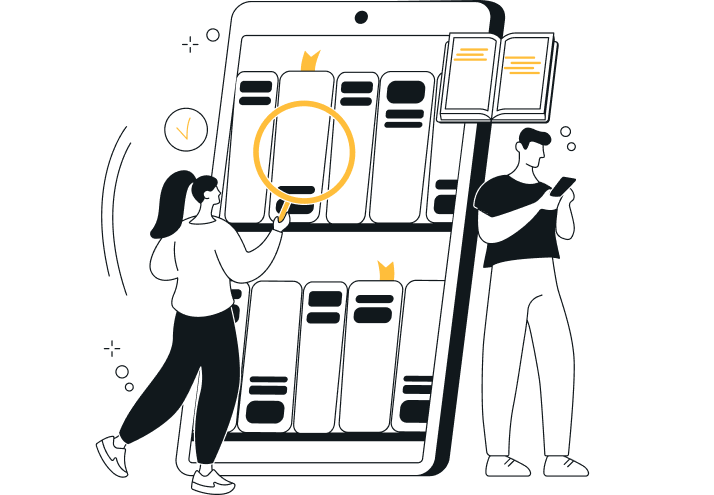