Allocation of indirect production costs
Setting the right price for a product is really crucial: too high, and customers will meet their own needs; too low, and suppliers won't get paid for the value they are delivering and the effort that went into it. How can suppliers figure out the right premium and the pricing model that will suit their customers? Many otherwise rigorously run companies are disconcertingly lax about pricing.
Although a 1 percent improvement in price yields bigger gains in operating profit than a similar improvement in variable costs, fixed costs, or volumes - almost 8 percent on average across the S;P 1000 - companies often base prices on the anecdotal observations of a few vocal sales-people or product managers. However, we see that the demand for effective methods and systems of accounting for activity within an organization is always growing, therefore, it makes sense that companies would want to implement practices which will benefit the structure and performance of their organization.
This was the case in regards to the evolution of the concept known as activity-based costing, or ABC. In order for management to know the basis behind this costing system, which appeared on the scene during the 1980's, they must first become familiarized with the general concept of ABC compared to a traditional costing system. Once a solid base has been established, it allows the opportunity for management to go beyond the surface of the topic and explore into the added value of what it has to offer.
Order custom essay Allocation of indirect production costs with free plagiarism report
Consequently, allocation of indirect production costs is the primary topic of this paper. The topics, which are of interest to this particular costing system may not be available to many firms, let alone university students. For this reason, light will be shed upon ABC. In the past, companies were dependent upon traditional cost accounting methods in order to predict and allocate indirect and direct costs amongst units in production.
However, the reasoning behind this practice tended to be somewhat misleading and provided indications that various products, when produced, would prove to be profitable projects. These misleading projections usually stemmed from the improper inclusion of all manufacturing costs while failing to include vital non-manufacturing costs, which resulted directly from production. (Carrol, 2001) With managers and companies becoming increasingly frustrated with various forms of traditional costing systems, the need for a more reliable, accurate mean of cost accounting increased in demand.
As a result, the concept of activity-based costing (ABC), A system of accounting that focuses on activities as the fundamental cost objects and uses the costs of these activities as building blocks for compiling the costs of other cost objects, was introduced (Foster, 1991). The implementation of activity-based accounting systems proves to be beneficial for manufacturers in regards to making crucial decisions. This concept would serve to provide management with cost information regarding crucial decisions, which could possibly result in manufacturing capacity being altered, which in turn, would lead to changes in fixed costs.
However, how exactly does activity-based costing match up with a traditional costing system and how does it provide managers with crucial information for decision- making? In order to analyze this point, the similarities and differences between the two systems must be illustrated. Throughout both systems, the practice of including manufacturing costs to products is common. As well, each deals with a cost pool and an allocation method of costs in order to maintain records.
The similarities are somewhat trivial and it is the differences between the two systems, which illustrates the added value an activity-based costing system has to offer. With a typical, traditional system, usually one indirect cost pool is created for each department or plant while an ABC system implements a substantially large number of pools. Also, indirect cost application bases, in regards to a traditional system, may be considered as cost drivers, while in an ABC system, cost application bases tend to be cost drivers.
Continuing on, indirect cost application bases in traditional systems tend to be financial, such as direct labour or perhaps direct material costs, while on the other hand, ABC indirect cost application bases tend not to depend on variables that do not have a financial implication. Variables used when determining an indirect cost application base in this instance tend to be number of parts in a product or hours of test time. (Hicks, 1999). Finally, the traditional cost system compared to the ABC system tends to incorporate predetermined rates used based on budget while ABC focuses on capacity (Foster, 1991).
Overall, the similarities between the two systems are to be somewhat expected but as indicated above, the differences between the two systems prove to be quite significant. Consequently, it is these differences that will have the greatest impact upon crucial decisions made by management because the assumptions made by an ABC system will illustrate operations, which prove to be beneficial and detrimental to the performance of a company while these factors may pass through a traditional system unnoticed.
The adoption of technology has affected all areas of accounting and extensive applications have also been developed for organizations using an activity based costing system. These applications help simplify and translate into a better ability to control costs, provide more precise information to a widening group of decision-makers, and link the enterprise with its customers, suppliers and partners. Also, Executives are concerned with financial application integration rather than cross-functional applications such as manufacturing, financial and human resources.
Having managerial and financial information systems integrated gives businesses a greater ability to analyze the data as well as streamlining accounting practices. With increased automation, production information can be collected in a central database and the data can be applied to cost pools in real time. It is this kind of immediate availability of data that management can use to prepare up-to-date cost statements.
Problems arise with these kinds of systems when traditional business practices and recording methods are still used after the adoption of ABC methods. With an activity-based costing system like this journal entries can be automatically generated so that the consumption of costs by specific activities can be measured precisely (Trites, 1999). As a result, managers receive a more granular and accurate view of actual costs, which greatly assists them in improving efficiency and budgeting.
Cite this Page
Allocation of indirect production costs. (2018, Nov 15). Retrieved from https://phdessay.com/allocation-of-indirect-production-costs/
Run a free check or have your essay done for you
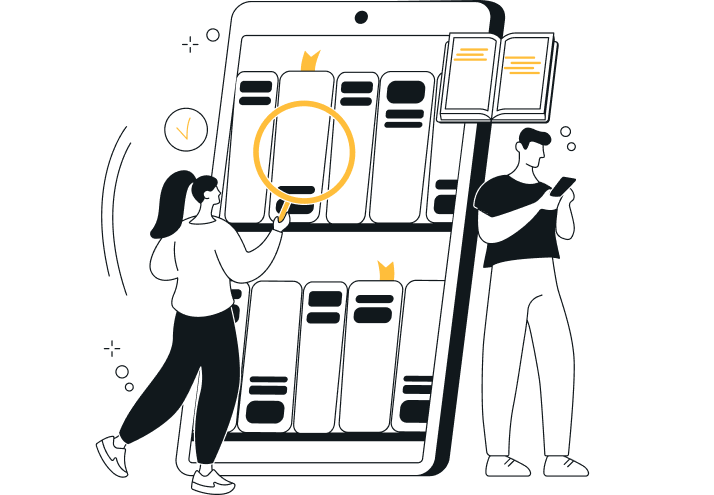