Lean production
Lean production, also known as lean manufacturing is a practice within the production chain that puts into consideration the expenditures of resources towards elimination of wasteful practices during production. It focuses on attaining more value by working less. Lean manufacturing has gained high prominence because of the way it reduced the Toyota seven wastes and hence improving overall consumer value. The Toyota seven problems concerns were transport, inventory, motion, waiting, overproduction, over processing and defects (Vega, 2003, p. 12). Lean manufacturing is an efficiency variation theme that decreases waste by employing empirical methods in decision making, uncritically accepting pre existing ideas. Therefore, it can be argued that lean manufacturing represents stepwise strategy and set of tools for achieving maximum product flexibility, predictable product output flow, minimum system waste and smooth product flow. Concepts used in this method appear to be making holds in various industries by shortening order to delivery lead times.
For many nations and scholars, it is believed that lean is the set of tools assisting in the process of identifying and steadily eliminating wastes. In the process of eliminating wastes, quality improves with costs and production time declining (Cortada, 2004, p. 11). The evolution of lean manufacturing does not come in automatically or cheaply, but it takes time and perseverance. This is because it takes a lot of resources and time. According to experience at Boeing, evolution process is dramatically affected by various technological challenges. Thus, evolution of this system takes three stages.
A case study at the plane manufacturing site of the Boeing of Spokane suggests that moving to lean manufacturing can only be accomplished in large steps but not small ones. If flexibility is not considered in equipment and workforce systems, initial stages can be costly. The flexibility of workforce depends on workforce attitude because they both support and touch labor from comfort zone to new approaches and job descriptions. Equipments should be flexible enough to adapt product mixes, new line layouts and process change failure to which large cost penalties can be charged. Read about lean production vs mass production
Order custom essay Lean production with free plagiarism report
In its evolution, lean production first evolution was from manual to automated cell. In this stage, machines replaced most of the work that was performed by human beings (Bernard, 1999, p. 20). The second evolution marked departure from automation cell to lean manufacturing. This was a change in focus, implying that wastage had captured the attention of many policy makers. The third evolution was marked by movement from manual to partially automated mechanism. In this evolution, it was seen logical and beneficial for a good combination of machine work and optimal decision making.
Automation left decision making to machines, leading to a lot of wastage. Partial automation means that it is important to allow wastage minimization procedurals to function together with machinery efficiency (Swamidass, 2002, . p17). The principles of lead production came from Japanese manufacturing industry. It was first coined by John Krafcik in 1988, when he published ‘‘Triumph of the lean production system’’. Almost at the same time, Toyota took a second approach towards lean production. This second focus is based on improving smoothness or flow of work and hence eliminating unevenness within the production system.
The system promoted by this company of Toyota GM is referred to as mass production. American industrialists realized cheap offshore labor threat in 1910s and then turned to lean manufacturing as a countermeasure. Lean manufacturing has been widely adopted by companies. With exception of operational difficulty in converting from traditional and functional based operation, this manufacturing process significantly involves organizational transformations. It calls for work team’s formation comprising of multi skilled workers.
Work teams improve production and performance processes because they are preferably self directed. Lean and mass production do not differ in goals, but the approaches they apply in achieving them. Smooth flow implementation exposes quality problems already challenging, consequentially waste reduction happening naturally. Mass production naturally takes system wide perspective. Staff members form the Toyota Company have been surprised by the fact that approach is always in use, but the company aims have not been fully achieved.
Both mass and lean production systems are loosely connected by potentially connected principles (Cooke, 2003, p. 16). The principles include continuous improvement, building and maintaining long term relationship with suppliers, flexibility, pull processing, waste minimization, perfect first time quality, automation, visual control, production flow and load leveling. In 1948, Toyota recognized the inefficiency in its system of operation and turned to the lean production strategies. They minimized their non value adding work, unevenness and overburdening.
They developed the sense of exposing problems systematically and employing the tools at times when ideal could not be achieved. These tools are workarounds to various scenarios, explaining apparent incoherence of the above stated principles (Dresner, 1999, p. 22). Mass production is based on to concepts; smart automation and just in time concept. Supporters of mass reduction say that smooth flow delivery achieves as many achievements as the side effects. Automation in this approach is usually achieved through human touch. This implies that systems or machines are designed to assist human focus on what they can do best.
The aim of this type of production is to avail enough intelligence to machines for them to recognize when they work abnormally and hence flag this element from human attention. According to this approach, humans do not focus on normal production but on the abnormal or fault cases within the production channel. The human workload is hence reduced leading to repetitive routine activity that they may not enjoy and ultimately not in their most effective area. The production mode has been viewed a symbol of optimal performance and efficiency since 1980s because of its applicability within the automotive industry especially Toyota.
In 1997, power and shoal companies identified eight areas that are perfected by lean management systems. They included corporate culture, employee improvement, work force flexibility, change management strategies, organizational structure and use of team work, use of kanbans, education and training, human resources issues and lastly the impact on changing roles. There are well spelled differences between mass production and lean production (Cooke, 2003, p. 23). Mass production is a profit maximization based strategy since: price – cost = profit. This is why the practice of systematic cost reduction leads to profit realization.
Lean implementation does not strongly emphasize on profits but just sounds as a fixation with improving the concepts of pull or flow. Another difference regards the tools. The tolls include visual control, value stream mapping and standardized work. Such tools give these two production methods the ability to counter problems or unhealthy challenges. Since every method has got challenges, the tools found in both of them can very applicable in solving problems, meaning that the two can share tools and differ in the objectives or their rationale. Form 1950s, mass production has been operating on management technique as compared to change agents.
This is well observed in push implementation of lean apart from pull by the team itself. This means that mass production does not depend on change agent specialists but on natural operations of the working team. In implementing lean production, developing the specialist is emphasized, but supervisory skills are expected to develop on its own over time (Morrison, 2003, p. 31). Another conspicuous difference between the two methods of production is the concept applied by mass production in batch processing. Mass production handles everything in batches.
Lean production batches are eliminated and reduced along the wait and queue states. Through the organization, work flows continuously from upstream tasks to down stream tasks. Batches are not highly preferred in businesses because they add costs without creating customer value, lengthen work completion time, pose work quality challenges and hide inefficiencies and reduce operational agility (Hitt, 2000,p. 45). Lean implementation focuses on getting right things at the right time, to the right place, in the right quantity. This makes it achieve perfect work flow, enabling change, enabling flexibility and minimizing wastes.
Lean production aims at making the work easy to manage, perform and understand. Organizational cultural impacts have been pointed to affect adoption of these strategies. This is because of the variation in managerial satisfaction of different cultures. Organizational culture may incorporate flexible manufacturing systems, procurement support, production and efficient delivery of finished products. Organizational culture may be developmental, rational, group and hierarchy. Group culture entails team work, empowerment, concern and participation. Hierarchy is the stability, formalization and control.
Rational couture is based on task and accomplishments rather than environment. In developmental culture, flexibility and creativity sustain change and growth. If this cultural environment is harmonized, excellence in adoption of the lead production can babe attained and put the venture in safe operation path. Organizational barriers that impede adoption of this technology are lack of crisis urgency, lack of mutual trust and respect, under organization, complacency, avoidance, overemphasis on core activities and rigid group boundaries (Vega, 2003, p.
34). The future of this manufacturing process is bright, with high probability that it will spread further around the globe. This is because many companies have witnessed the benefits of the process, seeing it as opportunities scratched from the surface. The company that started it fifty tears ago is still struggling to have it fully implemented but still surviving as the most effective automotive industry. Lean manufacturing has further been applied in governments, education, health care, military and service sector.
Its future stability is ascertained by the fact that lure for cheap labor will always exist in the world, which should be accompanied by reasonable distribution of business investment for it to make political and economic sense. The same method has high potentiality to curb recent tides in job loses for it eliminates wastage, driving companies to low cost regions. There are various barriers that are affecting the adoption of the lean production strategy. First and foremost, the strategy requires high collaboration and integration of human behavior in the production process.
Adoption of this strategy can only take place if and only if the concerned management is willing t change the old ideology towards modernism. Again the system requires people to focus on profit motives, which are not very common goal for all businesses (Morrison, 2003, p. 51). Organizational challenge to this technology therefore arises because the objectives of different organizations may not match the objectives of the technology. Organizations also rise up to promote human beings status either by promoting job opportunities or psychologically boosting their understanding.
Lean production aims at wastage minimization and strategies and automation as seen earlier. Automation means excessive exploitation of machinery and equipment in performing most of the functions in an organization. Unemployment and marginalization are major problems in the world, implying that lean production can not be massively adopted by many member states. Organizations may be non profit making, involve human rights activism, profit aimed or to serve government based objectives. Therefore, organizational challenge or barrier is mainly based on the set goals and missions (Cortada, 2004, p.
11). On human barriers, it is worth noting that people are interacting on all bases especially because of globalization aspects. This means controversy must arise in deciding whether or not to adopt any production criteria because of varying interests. In job or organizational environment, it is always advisable to make extensive consultations because all partners are part and parcel of organizational activities and organizational set missions and visions. This means efforts of all participants are essential in pulling the success of the organization closer.
Human barriers are therefore generally experienced in line with conflicting interests in an organizational set up. Operational barriers may compose of the financial ability, availability of machines and equipments and access to new and competitive technology. If a company is financially limited in access to information technology, this is a potential barrier that can limit the possibility of adopting the production process. If however a company that is weak in these terms happens to adapt it, then it may be hard to improve or facilitate full functioning of this process.
Financial and technology based challenges are very well pronounced around the world, meaning that it is illogical and unrealistic ignore such kind of events (Bernard, 1999, p. 19). In my own opinion, implementation of this strategy may be highly complicated or else cheap. This is because different companies, nations and organizations have different levels of development and set out missions. The level of development determines the financial strength, the technological level of the equipments and facilities employed in daily operations, access to information technology and utilization of highly qualified personnel.
As proved and earlier on stated in this paper, it is hard to implement because it consumes a lot of time and resources. This is a clear implication that the method may favor long-term and stable companies (Hitt, 2000, p. 27). This means short term and weak companies are not in position to implement this production program. In terms of output, I highly recommend the process. This is because regardless of the type of company, wastage is a business or organizational vice. Such wastage may take the form of time, finance, labor or equipments.
Whether product or service sector, efficiency is very vital for optimality to be realized. Foreclosures have been witnessed especially for companies that have not accorded efficiency in their operations. Efficiency does not only apply to product or commodity industries bit it is a requirement for all organizations, whether profit making or not. Although companies may differ in goals and internal operation, efficiency maintenance is compulsory for success of any organization to be attained. Every company is always to attain optimality, meaning the lean production is vital.
To end, it is necessary that companies try to curb the challenges towards adoption of lean manufacturing and implement it with full assurance of success (Dresner, 1999, p. 22).
Bibliography Bernard Paul, 1999. Integrated inventory management. New York: John Wiley & Sons; pp. 19, 20 Cooke William, 2003. Multinational companies and global human resource strategies. Westport, CT: Quorum Books; pp. 16, 23 Cortada James, 2004.
The digital hand: How computers changed the work of American manufacturing industries. Oxford: Oxford University Press; pp.11 Dresner Martin, 1999. Benchmarks and best practices for manufacturing profession. New York: John Wiley & Sons; pp. 22 Hitt Michael, 2000. Winning strategies in a deconstructing world.
New York: John Wiley & Sons; pp. 27, 45 Morrison Don, 2003. E-learning strategies: How to get fast implementation and delivery. New York: Wiley; pp. 31, 51 Swamidass Paul, 2002. Innovation in competitive manufacturing. New York: AMACOM; pp. 17 Vega Gina, 2003. Managing teleworkers and telecommuting strategies. Mahwah NJ: Preager; pp. 12, 34
Cite this Page
Lean production. (2018, May 31). Retrieved from https://phdessay.com/lean-production/
Run a free check or have your essay done for you
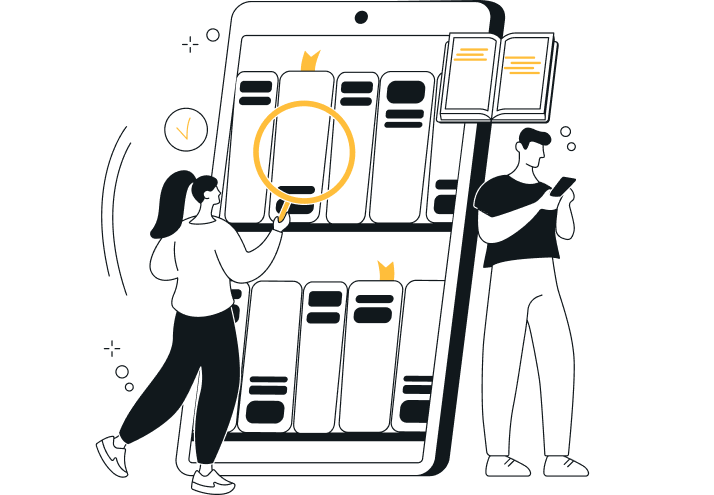