Lean production in companies
Lean production has been broadly used in many manufacturing companies. It has been a source of efficient performance since its inception in 1980’s as a result of its close ties with the automobile industry. Its performance has been shown to outdo other traditional production strategies which produce large consignment of products on several instances (Boyer et al. , 1997). Several research studies refer to lean production philosophy as just-in-time (JIT). These terminologies are interchangeably adopted though they describe the same strategy which includes waste elimination, efficiency maximization, and uninterrupted improvements.
However, migrating to lean production strategies involves a number of changes in organization, operation and human aspects. These changes present enormous challenges to the implementation of lean production and therefore its successful implementation depends on how these challenges are overcome. This paper therefore introduces the concept of lean manufacturing and examines the relationship with other production strategies such as mass production. The paper then examines the challenges to the implementation of this strategy and how best they can be overcome.
The paper concludes by assessing the practicability of implementation of lean production and suggestions for further development. Evolution of lean production strategy Customer expectation is one of the factors that are increasingly impacting on the success of organizations. For these organizations to be successful, organizations should therefore understand comprehensively the constraints and requirements of the market environment in order to develop mechanisms that meet the expectation of customers as well as fulfilling logistical requirements of the system (Landis, 1999).
Order custom essay Lean production in companies with free plagiarism report
Meeting the expectation of customers as well as lowering costs forms are the fundamental aims of logistics management. Lean production strategy has been proposed as enablers of these objectives (Steele, 2001). To clearly understand this strategy and its evolution, a succinct history of the industrial manufacturing processes is described. Three major shifts in paradigm in industrial production exist in the present world. These paradigms are craft production, mass production and lean production. Read about lean production vs mass production
In craft production, the different projects are completed on an individual basis by craftsmen. The consumer’s participation is only necessary when requesting unique products which are relatively different from the previously produced products. In a mass production paradigm, which is associated with the assembly line production age of Henry Ford, the product outputs were delivered at breakneck intervals. The variety of the products is minimal during the initial stages of the production process but increases with elapsed time.
In a lean production strategy also known as just-in-time (JIT) manufacturing, the production utilizes the benefits of mass production in line with the philosophies of just-in-time manufacturing as well as waste elimination in order to lower the cost of product production (Gonzalez-Benito, 2002). The traditional product manufacturing strategies continually face challenges of international competition, economic pressure and the demand for reliability in system logistics. Lean production therefore calls for fewer inventories resulting in minimal faults and consequently producing unprecedented varieties of products (Womack et al.
, 1990). Lean production strategy has been extensively explored by several research studies. According to Womach and Jones (2003) in their description of lean philosophy contained in their book titled Lean Thinking suggested five principles under which lean production is defined. These principles as presented by the authors of Lean Thinking are value, flow, pull, value stream and perfection. Value according to the book derives its definition from the end consumer since it is them who determine what constitutes a value.
For instance, a person traveling would define value as reaching the desired destination promptly. The value stream refers to the route followed by the products during the production process from the raw materials into final products. During this phase of production, value is added to the product. For instance, a basic value stream for a company manufacturing wine would be cultivation of grapes, harvesting the raw materials from the fields, smashing them into liquid form and bottling the resulting liquid for shipment.
Every stage in the value stream process is aimed at adding value to the original produce, where value refers to what the consumer considers important. Ensuring continuous flow of the value stream follows the immediately. Instead of stocking the grapes in warehouses waiting processing into wine, the lean production paradigm ensures that the grapes are immediately utilized upon arrival to produce wine. The pull principle is concerned with the initiative of the various processes.
The phenomenon of pull creates a greater responsibility on the part of the consumer to initiate the process and the sequences of production to ensure that only what is require by the consumer is produced. For instance, in the automotive industry, the manufacture of spare parts would only be initiated upon receiving order from the customer through a chain of retain shops. Actualizing the principle of pull therefore requires that a minimum limit of inventory is set and purchasing only when the available products have been sold.
Finally, perfection is the last principle in the lean production process. This principle is continuously concerned with determining the possible triggers of waste and consequently their elimination. The lean production strategy acknowledges seven forms of wastes namely overproduction wastages, wastages resulting from waiting, transport wastages, wastages as a result of over processing, wastages involving inventories and their movements and finally wastages due to defects (Womach & Jones, 2003).
The above kinds of wastes are related in process and are influenced by the layout and design of the production process. However, the generation of waste is also influenced by operational, human and organizational factors. According to Womach and Jones (2003), several action plans are necessary to reduce the creation of wastes. These action plans basically involves operational and organizational measures.
The operational measures involve acquiring the necessary knowledge and skills associated with the lean production process, matching the phases of value stream and categorizing the products into different families. On the other hand, organizational measures involves steps such as creation of a crisis, embark on visible activities first, enlarge the scope of the production process upon gaining the desired momentum and insisting on the delivering of immediate results. The successful implementation of this strategy involves both human, operational and organization changes (Womach & Jones, 2003).
Cite this Page
Lean production in companies. (2018, Aug 25). Retrieved from https://phdessay.com/lean-production-in-companies/
Run a free check or have your essay done for you
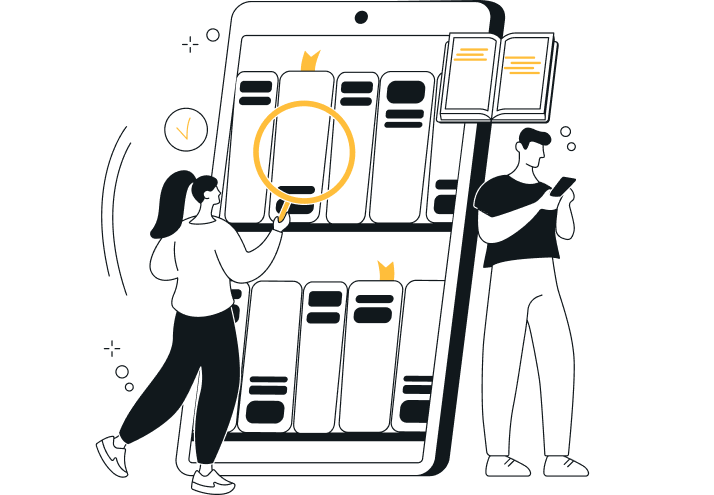