HP Case Study – Deskjet Printer Supply Chain
DeskJet Printer was becoming one of Hewlett-Packard (HP) Company's most successful products. Sales had grown steadily reaching around 600,000 units in 1990. Uneven distribution of inventory was one of the key issues which needed to be addressed since in spite of having distribution centres (DC) filled with printers, organisations in Europe claimed that inventory levels needed to be raised to maintain satisfactory product availability.
Also there seemed to be an issue of requiring the buy-in of the various parties on what was the right level of inventory to be maintained. Worldwide sales were about 17 million units which amounted to $10 billion. The US-Western Europe markets were mature while that in Eastern Europe and Asia-Pacific were developing markets. The ink-jet printer (DeskJet was one of the products in this category) had around 20% of the retail printer market. HP was the market leader in US while Cannon was in Japan and Europe had competitors like Epson, Manisman-tally, Siemens and Olivetti.
The Vancouver Division of HP (the personal printer activities were consolidated) introduced the Kanban process and converted it to stockless production which also reduced cycle time and reduced inventory time from 3. 5 months to 0. 9 months. The Supply Chain The network of suppliers, manufacturing sites, distribution centers (DCs) dealers and customers for the DeskJet product comprised the supply chain. Manufacturing which involved two stages- Printed Circuit Assembly (PCAT) and Final Assembly and test (FAT) was done at HP in Vancouver.
Order custom essay HP Case Study – Deskjet Printer Supply Chain with free plagiarism report
The components needed for the manufacturing process were sourced from other HP divisions as well as from external suppliers. Currently, localisation of the printer which meant customizing to the specific region was done at the factory. Outgoing products were shipped to the three DCs by the ocean. No significant buffers were maintained between the PCAT and FAT stages. Here d, the demand forecasted is given in Table 1 as the mean of the demand. Lead time for DC within US is one-day transporting time from Vancouver to California and one week factory cycle time.
That is a total of 8 days. For Europe and Asia, the lead time was 42 days (5 weeks to ship and one week factory cycle time) by sea and 14 days (1 week to ship by air and I week factory cycle time). The Reordering interval is assumed to be 7 days as per the question. The safety stock is obtained from the standard deviation of monthly demand ?. The company target for the line item fill rate which has been estimated by the marketing division is 98%. The z value for the 98% fill rate in the equation is 2. 05.
Thus the safety stock for the given lead time and review period can be found. The average demand is found from the mean of monthly demand and the lead and review times. The quantity of inventory is computed by the addition of the average demand and safety stock. There are two possible means to calculate the inventory carrying costs. Using HP's cost of debt and warehousing expenses an inventory cost of 12% is obtained and if the ROI expected on new product development projects is used the inventory carrying cost is 60%. The cost of a single unit is taken to be 400$.
Therefore the inventory carrying cost per unit is either 48$ or 240$. The total inventory carrying cost is calculated using both rates by multiplying them with the number of units that form the inventory of the three DCs. The total sales are 600,000 units which are close to the total of the forecasted demands. Therefore it is assumed that the sales in the different regions are equal to the forecasted demands. This is then used to calculate the weeks of supply. The steps to be taken to compute the inventory is given above.
The data collected by the team to improve the forecast is used here. Only the inventory levels in Europe are considered for comparing the various alternatives. The expenditure required to set up a manufacturing facility in Europe is not known. This will be a long-term investment and depends on the scale of demand in Europe. It should be sustainable and have sufficient volume to justify its inception. Assembly can be done in Europe: The manufacturing process should be modified so that final assembly can be done at the DC in Europe.
These processes that can be done in Europe include the power supply and the manuals. This will help reduce the lead time by reducing the factory cycle time. These should also enable the DC to be more flexible. The shipping costs will also come down. The actual savings cannot be calculated from the given data and more information is required. The top management prefers to maintain the DCs in a warehouse mode as it will difficult to manage the work in the DCs. Additional expenditure will be incurred in setting up support processes. Conclusion
If 12% is considered to be the carrying cost of inventory then it is more cost-effective to just use the new data to forecast the demand and thus maintain a 98% line item fill rate. But if it is 60% transportation by means of air should be used. In the long term as the demand in Europe builds up the setting up a facility in Europe can be considered. As an initial step in this process assembling in Europe can be considered. Another alternative that can be considered is inventory pooling by building up finished good inventory in the factory.
Cite this Page
HP Case Study – Deskjet Printer Supply Chain. (2018, Feb 12). Retrieved from https://phdessay.com/hp-case-study-deskjet-printer-supply-chain/
Run a free check or have your essay done for you
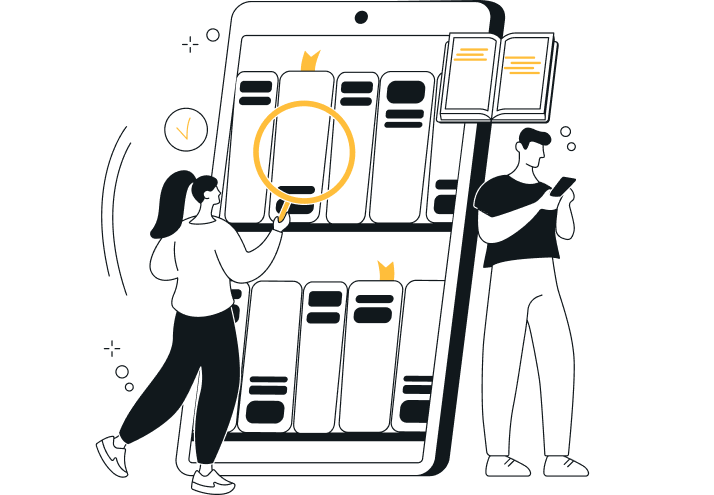