EOQ, Economic Order Quantity
An Economic Order Quantity is the optimal number of order that minimizes total variable costs required to order and hold inventory, that is to say, that EOQ helps us to determine the appropriate amount and frequency when ordering and holding inventory. EOQ is used as part of a continuous review inventory system, in which the level of inventory is monitored at all times, and a fixed quantity is ordered each time the inventory level reaches a specific reorder point, as it shown in the left-hand graphic, where R is the minimum inventory.
Moreover, EOQ is essentially an accounting formula that determines the point at which the combination of order costs and inventory carrying costs are the least. The result is the most cost effective quantity to order. Also, EOQ is generally recommended in operations where demand is relatively steady, items with demand variability such as seasonality can still use the model by going to shorter time periods for the EOQ calculation. This Model have som assumptions that are important to take into account: 1. Demand is known and is deterministic, ie. constant. 2. The lead time, ie. he time between the placement of the order and the receipt of the order is known and constant. 3. The receipt of inventory is instantaneous. In other words the inventory from an order arrives in one batch at one point in time. 4. Quantity discounts are not possible, in other words it does not make any difference how much we order, the price of the product will still be the same. (for the Basic EOQ-Model) 5. That the only costs pertinent to the inventory model are the cost of placing an order and the cost of holding or storing inventory over time.
The basic Economic Order Quantity (EOQ) formula is: WhereA = Demand for the year Cp = Cost to place a single order Ch = Cost to hold one unit inventory for a year Then, the before formula try to Minimize the Total cost per period, that consist in: Total cost per period = inventory holding costs per period + order costs per period Where: Order Cost = The Number of Orders Placed in the period x Order Costs Carrying Cost = Average Inventory Level x the Carrying Costs of 1 unit of Stock for one period Then as a Result of this minimizing we get the Total Relevant Cost (TRC) which is TRC = Yearly Holding Cost + Yearly Ordering Cost = So we can see that the Economic Order Quantity (EOQ) is derived from this formula as the graphic shows. Economic Order Quantities can also have many variations on its basic model. The most useful ones are: * Quantity discount logic can be programmed to work in conjunction with the EOQ formula to determine optimum order quantities.
Order custom essay EOQ, Economic Order Quantity with free plagiarism report
Most systems will require this additional programming. * Additional logic can be programmed to determine max quantities for items subject to spoilage or to prevent obsolescence on items reaching the end of their product life cycle. When used in manufacturing to determine lot sizes where production runs are very long (weeks or months) and finished product is being released to stock and consumed/sold throughout the production run you may need to take into account the ratio of production to consumption to more accurately represent the average inventory level. * Your safety stock calculation may take into account the order cycle time that is driven by the EOQ. If so, you may need to tie the cost of the change in safety stock levels into the formula.
Cite this Page
EOQ, Economic Order Quantity. (2017, May 07). Retrieved from https://phdessay.com/eoq-economic-order-quantity/
Run a free check or have your essay done for you
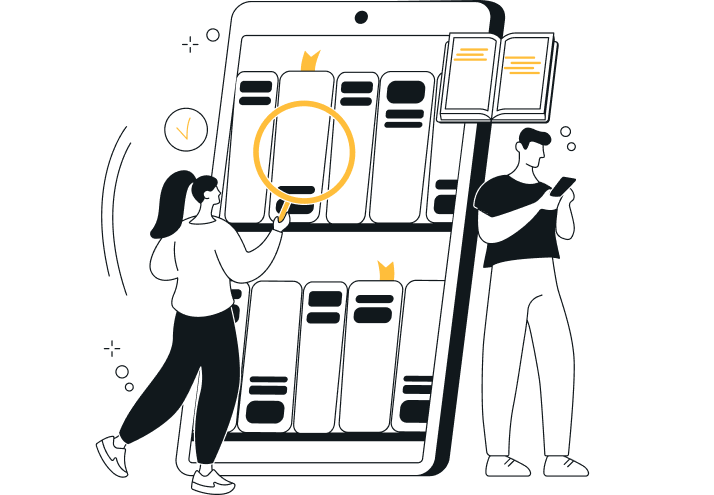