Toyota V.S Ford
Toyota is the number one automobile manufacturer in terms of production and sales. Toyota is a foreign vehicle manufacturer located out of Japan founded in 1937. Ford is the second largest vehicle manufacturer in the United States and fifth largest worldwide.
Ford was the eighth ranked overall vehicle manufacturer on the 2010 Fortune 500 list. Ford is known for producing the “Model T” in 1908 which will forever be known as the first affordable automobile in the United States. Each company will be introduced and described separately. After providing substantial information about each organization, a comparison will follow to highlight the differences between the two. This comparison is imperative for the GBAS model. I will also make an assessment of the four facts or organization life, fit, trade-offs, opposites and if the elements come in packages.
Toyota Motor Corporation Toyota Motor Corporation is a foreign vehicle manufacturer based in Aichi, Japan. Toyota Motor Corporation came to the forefront in 1937; (TMC) is a variation of what originally used to be Toyota industries. Kiichiro Toyoda always envisioned creating a multinational automobile manufacturer and his dreams came to fruition three years earlier, when still with Toyota Industries, they created their first product which was the “Type A” engine and in 1936 came their first vehicle the “Toyota AA”.
Order custom essay Toyota V.S Ford with free plagiarism report
Today Toyota Motor Corporation group companies include Scion, Lexus, Daihatsu and Hino Motors Toyota stepped into the national spotlight in the 1980’s when people started to realize that there was something different about their vehicle. What stood out most was the exceptional quality and efficiency of Toyota vehicles. Japanese cars were lasting longer than American cars and also required less maintenance. At the time, there were several Japanese manufacturers competing in the market, but Toyota stood out the most.
Toyota did not provide the most exciting designs, but what they did was design automobiles that were very consistent and more reliable than most vehicles at an affordable price. Also, Toyota had a canny ability to troubleshoot all of their problems and come back even stronger when one of their weaknesses was exposed. While stock prices of the Big 3 were falling in 2003, Toyota shares increased 24% over 2002. Toyota’s capitalization was higher than the combined capitalization of Ford, General Motors and Chrysler. (The Toyota Way, Pg 4) Toyota has the fastest product development process in the world.
New cars and trucks take 12 months or less to design, while competitors typically take two years. Toyota is benchmarked as the best in its class by all of its peers and competitors throughout the world for high quality, high productivity, manufacturing speed and flexibility. (The Toyota Way, Pg 5) Toyota had a unique way of manufacturing their vehicles which is what helped them create differentiation from themselves and the market. The Toyota Production System and Lean production has dominated the industry for the last 10 years along with Six Sigma.
During and before WWII, Toyota knew that mass production was not their strength. They were too small and disjointed to support high production values. Toyota decided to produce roughly 900 vehicles a month while on the other hand; Ford was about 10 times more productive. Toyota managers knew that if they were to survive, they would have to adapt to the mass production for the Japanese market. The problem was that they didn’t know how. The Toyota production system used many conceptions from those of Henry Ford, but the Japanese were determined to stick to the principles that Ford didn’t abide by.
One very important principle was the concept of the “pull system”, which originated from American supermarkets. This system meant that Toyota would not replenish its parts until the next step in the process used up all of the original parts from the previous step. This directly relates to eliminating waste. At every step of the manufacturing process, Toyota uses “Kanbans” to signal the previous step when more parts need to be made. This creates the “pull” which continues back to the beginning of the cycle. Toyota also implements the philosophy of JIT into their manufacturing process.
JIT is a set of principles that allows a company to produce and deliver products in small batches. This directly cuts down the lead time and allows them to meet specific customer needs. JIT allows Toyota to be responsive to customer demands; it also allows them to deliver the right items at the right time. “Kaizen” is also another principle Toyota stands on. The philosophy reaches for perfection and sustains TPS on a daily basis. Toyota refined their manufacturing process using these principles to make their organization more productive and less wasteful.
What they didn’t know is that they also created a new paradigm in manufacturing that all types of businesses would eventually adopt. A common phrase around Toyota is “Before we build cars, we build people. ” Toyota seeks to develop people so that they are strong contributors to the company culture and organizational development. The focus is to build a learning organization that seeks continuous improvement. That’s how they will ensure a guaranteed long term success hundreds of years from now. TMC management techniques’ goal is to develop their individuals, but at the same time promote effective teamwork.
This technique is necessary for TPS to work. Creating a great culture combined with teamwork is the focal point of solving problems. The concept of bottom-up management is something that Toyota takes very seriously. Team leaders typically have about four to eight workers that they support and group leaders have about three or four groups. Toyota strongly believes in motivation theories when it comes to managing their employees. Their managers implement both internal and external management techniques.
For example internally, Toyota applies Maslow’s Hierarchy of needs to them by providing their employees with job security, good pay, safe working conditions and a culture of continuous improvement. Externally, behavior modification has group leaders constantly on the production floor supervising employees and providing reinforcement. Toyota invests in their employees and in return they get committed individuals are willing to grow the company. Ford Motor Company Ford Motor Company is a multinational automobile manufacturer based out of Detroit, Michigan. It is the second largest automobile manufacture in the United States.
Henry Ford founded and incorporated the organization in 1903. Under the Ford umbrella is the Lincoln brand and internationally Ford has some stake in Mazda and Aston Martin. There used to be several more brands associated with the company but due to harsh economic times in the United States, they were either discontinued or sold. Henry Ford is known for making the most affordable automobile (the “Model T”) and transcending the American auto industry. Most people think that he actually invented the automobile as well as the assembly line. Those are not the facts.
Henry Ford did however use the assembly line to produce his “Model T”. From 1909-1927, he sold 15 million Model T vehicles at a cost of $829 dollars each. During World War One Ford in 1925 also manufactured aircrafts, but after the war ended they returned to only manufacturing autos. Ford’s mission is to be the worldwide leader in the automotive industry and in other industries such as financial services. Ford values its people, products and profits. Some of their principles include commitment to the quality of the business they conduct, customer focus, continuous improvement, employment involvement and teamwork.
Ford strategy is predicated by its vision of being a low-cost, high quality manufacturer in all of their products while simultaneously providing the best customer service possible. In the United States, Fordism was the system of mass production and consumption characteristics of highly developed economies during the 1940’s-1960s. It was a philosophy that aimed to achieve higher productivity by standardizing the output, using conveyor assembly lines and breaking the work into small de-skilled tasks. It is a contrast from Taylorism, which is based off Fordism, which seeks to improve efficiency of machines and workers.
Fordism combines them as one unit and looks achieve minimal cost and maximum profit. (Source: businessdisctionary. com/Fordism) An assembly line is a manufacturing process in which parts are added to a product in a sequential manner in order to create a finished product. The immediate benefit of an assembly line is that it allows you to produce more products faster than if you were to handcraft them. Henry Ford made the assembly line famous in 1908 when he began the mass production of Model T’s. With the implementation of the assembly line, Ford was able to improve other aspects f the company such as reducing the labor hours it takes to produce a single vehicle as well as increased production numbers and parts (Wikipedia. com/assembly_line). The use of assembly lines and mass production processes forced Ford to start using large factories for manufacturing. They were the first automobile manufacturer to use large factories. During the late-2000’s recession when auto sales dropped 37%, Ford requested bailout money. They requested $9 billion dollars from the government and an additional $5 million for the department of energy.
With this money, Ford vowed to make smaller, more gas efficient, vehicles as well as close down dealerships and sell Volvo. Ford didn’t need the money nor did they receive any money, but simply requested for funds because they did not want their competition to have a financial advantage over them. During the auto bailout, Ford was in a better financial position than Chrysler and GM which is the reason they didn’t receive any government funding. Ford’s approach to management organization was the mirror image of their assembly line: specialized, hierarchical and tightly controlled.
Ford has always operated on a pressure system with middle management. The old Ford hierarchy was mechanistic in the sense that it was made to be modified, to be able to be adjusted over time. The structure was designed to be reactive to a slow changing environment. Ford’s management was very authoritarian, regimented and driven by fear. In light of Japanese competition, Ford shifted gears from the mechanistic theme of management to focus on participative management and product development. Narrative Comparison
Today, most companies try to implement some type of lean production or six sigma quality functions into their manufacturing processes. Initially, that was not the focus when it came to manufacturing vehicles. Toyota was the first organization to implement that strategy due to Japan being desecrated by two atomic bombs and not having the money or supplies to mass produce. Post WW II, Ford’s mass production system was designed to make large quantities and a limited number of models; they had no flexibility with their system. This is why all Model T’s were all black.
The Japanese market was very small and fragmented for high production. Toyota needed to manufacture low volumes of several different models using the same assembly line to survive in the market. The demand for vehicles was not high enough to use individual assembly lines for each vehicle type. Ford had ton of cash after the war and they invested it all in large equipment and large factories to house the equipment. This was to support the strategy of mass production. However, there was an issue with all the large volumes being produced, which caused Toyota to take a similar, but opposing manufacturing strategy to Ford.
Ford’s processes were detached from each other due to the large volumes. This cause delays in the process and allowed large amounts of material to sit and become work in progress inventory. Also, workplaces were disorganized and out of control, some Ford factories looked like warehouses. Toyota had the idea of “one-piece flow” where one piece of a product moves from one stage to the next stage, one piece at a time. This was opposite to what was happening over at Ford where several pieces of a product were being made simultaneously at one stage, then moved on to the next stage.
Toyota used Ford’s ideology of a continuous process of materials throughout the manufacturing cycle while at the same time eliminating waste. Toyota didn’t have a lot of money or factories after the war so that had to be very precise in their manufacturing. They didn’t produce large volumes of just one type of vehicle. One-piece flow allowed Toyota the flexibility to change their process according to the demand of the market. Toyota adopted Ford’s manufacturing process, but made it more efficient and flexible. Toyota’s management philosophy was to develop their employees to become leaders within the company.
This was their method of growing the company. Toyota knew that making all of their employees and integral part of the organization was the best way to build commitment within the company and a sure way to achieve all of its objectives. Ford on the other hand implemented a more authoritarian management philosophy where all of the pressure was put on middle management and not as much attention was given to the employees who were the key to their day to day operations. Ford primary focus was on production and the bottom line numbers.
Mass production to make as many vehicles as possible is what drove them to implement such management techniques. The Discussion of goals, boundaries and activity systems. (GBAS Model) After the comparisons and noting the differences between Ford Motor Company and Toyota Motor Company, the GPAS model can be applied to see how effective both companies are at managing fit, trade-offs, packages and opposites.
Boundaries
In terms of customers, the Japanese market was very small, so Toyota knew that they would have produce small numbers of vehicles in various different models.
Mass production wouldn’t work for them in the market because the customer demand was not high enough for that type of production system. Ford had a large U. S. market as well as an international market at the time so they were producing vehicles for everyone. When Henry Ford invented this inexpensive vehicle, there was a high demand for it and he sold millions of vehicles. Mass production worked well for high customer demand and the system made Ford a lot of money in a short amount of time. While Toyota remained in the automotive industry producing vehicles and engines, Ford tried its hand providing other services.
Ford Motor Credit Company is the financial partner of Ford Motor Company. The purpose of the company was to handle automobile loans of Ford and also to offer loans and leases to other consumers. When it came to products, Toyota had an advantage. They designed they’re production system to be flexible due to the low customer demand in the Japanese market; therefore they were able to produce different types of vehicles at a faster pace than Ford. Although Ford produced more vehicles than Toyota they did not have the ability to change the different models or colors of their vehicles within their assembly system.
The mass production system was beneficial because it satisfied high customer demand, but it was limited in the way that it could only make huge quantities of one model. Originally Model T’s were only all black because Ford lacked the flexibility to change colors. Ford used its mass production system to make millions of Model T’s and later Model A’s. Ford also took its hand briefly in the aviation industry during the First World War building engines. Ford’s most successful airplane was the Ford 4AT Trimotor, but after the war was over Ford went back primarily to the utomotive industry. In terms of accessibility, Toyota was limited to the Japanese Market, they did not have the ability to manufacture vehicles elsewhere nor did they have the demand. After the atomic bomb Toyota had very little cash and lacked the infrastructure to compete outside of Japan. On the other hand, Ford had huge amounts of cash from the success of the Model T and they had a huge U. S and international market to sell too. Also, Ford had a huge supply system to support all of their manufacturing efforts.
Activity Systems
Toyota’s activity systems were based around the central theme of their production system which was eliminating waste. When it came to manufacturing the company focused on continuous improvement, lean production and the Toyota Production system. Continuous Improvement also known as Kaizen, is a process that has lead Toyota to be a very lean and productive company. Kaizen strives for perfection and helps sustain the TPS system. The purpose of continuous improvement is to always become better, regardless whether the gains are large or small.
Toyota felt that if they continually improved their processes, they would be able to eliminate as much waste as possible while remaining overly productive. Toyota formed small work groups within the workplace to ensure effective teamwork and to develop the skills of their employees. This also encouraged discussion amongst employees and it helped them make some of the decisions in the manufacturing process opposed to putting all the pressure on middle management. The Toyota Production System is a system that is composed of all of Toyota’s processes and principles in order to achieve a high level of quality production standards.
JIT, Kaizen, One piece flow and continuous improvement theories combine to create a system that changed the way production standards were measured. Using many of the lessons preached by Henry Ford, Toyota evolved a system that helped them overcome challenges in a deplorable economy. At the same time they created a system that has been adapted in many other industries outside the automotive world. Ford, the American powerhouse, also believed in a continuous production flow, but they were not as cautious as the Japanese due to being in a better financial situation post WWII.
They produced millions of model T’s with the help of assembly lines, large factories and a system of mass production to keep up with the high customer demand for the world’s most inexpensive automobile. Ford’s production system was an adaptation of their market and they took full advantage. They had access to complete systems supplies in combination with a lot of cash which tremendously increased their profit margins in 15 years. GOALS: Toyota’s goal was to create a system similar to Ford’s mass productions system, but at the same time adapt it to the Japanese market.
The Japanese were producing automobiles for a market of customers who were not buying vehicles half as much as customers were buying autos in the United States. Even though there was a low demand for automobiles, the Japanese did demand different models, so their system had to be flexible enough to shift with the customers demand. In terms of creating the production system, Toyota aimed for a very lean system. A system that would be very cautious in using raw materials and cash in order to prevent being wasteful. Also, Toyota wanted a very clean and organized workplace in order to utilize all of the warehouse space that they did have.
Toyota aimed to produce small quantities of quality products to meet specific customer needs. Ford was all about big business, money and power. Ford’s goal was to take over the automobile industry with the invention of the Model T. It was clear what their objective was by looking at the way they manufactured automobiles. Ford believed in standardization, but they never manufactured more than one type of motor car in the same facility. They were so focused on making the Model T a commodity that they did not focus on their other brand Lincoln. Ford’s customer base was broad.
The Model T was marketed on a national level as a very inexpensive vehicle. Ford had the luxury of dealing with a high demand in the U. S and International market. Ford however, did not offer a variety of models to choose from. They only produced one vehicle in one color. Several years later they began producing the Model A. Due to the high demands at the time, customers did not pay attention to how inflexible Ford’s production system was. Although Ford may not have been as good as Toyota, they were also advocates of lean production and continuous improvement.
Ford felt that their materials were more important than their employees, an opposing view of Toyota. Ford learned that wasted materials eventually became wasted money and frantically began to search for solutions to be more productive with their raw materials. Eventually Ford had the notion that they owed it to society to be more conservative of their materials. Summary of GPAS: Toyota Ford Boundaries: Narrow, Stable Broad, Stable Activity Systems: Simple, Flexible Complex, Inflexible Goals: Impermeable Permeable
The Four Facts of Organizational Life
Discussion of fit: There is organizational fit between the boundaries, activity systems and goals of both Ford Motor Company and Toyota Motor Company. There are differences between the two companies, but both companies were competing in different markets therefore they had to adjust to the wants and needs of their customers. Ford has very permeable boundaries. Their complex and inflexible system which consisted of mass production, large factories, large machinery and assembly lines was imperative in order to satisfy the demand of their customers in the U. S and international market.
Ford was able to establish a very credible and trustworthy relationship with its customers by satisfying their needs in a timely fashion. The permeable boundaries and complex activity system fit very tightly with customers who were in the market for a vehicle manufactured by Ford. Toyota Motor Company has significantly less permeable boundaries than does Ford, therefore their activity system is simple and more flexible. The fact that Toyota had a significantly smaller market to manufacture vehicles for did not stop them working at a faster pace and creating higher quality vehicles.
Their activity system was designed for customers who wanted different types of automobiles in different colors. They also wanted quality vehicles that would last for a long time to avoid high vehicle turnover. This flexible system was perfect for the struggling Japanese market post World War II. Things come in packages: Ford Motor Company was in a great position post WWII. They had tons of cash, access to a complete supply system, and a high demand for their products in the market and huge factories and equipment to make thousands of automobiles. Those resources helped reinforce their needs to make their automobiles a commodity worldwide.
When comparing the two organizations, it is clear that Ford has more permeable boundaries than Toyota. On the contrary, less permeable boundaries made it more difficult for customers outside of the Japanese market to get a Toyota vehicle. They had not made their vehicles a commodity yet, but that was not their focus. After being desecrated by two atomic bombs, the Japanese manufacturing focused on making small amounts of quality vehicles. Making more quality vehicles using the one-piece flow process increased the skills and intelligence of the employees which directly helped grow the company.
Having a lower customer demand allowed Toyota the time to perfect their craft and create a system that would change the manufacturing world. There are opposites: In terms of activity systems and boundaries, comparing Toyota to Ford is like comparing the tortoise to the hare. Ford was the automobile powerhouse with all its large equipment and mass production processes, producing vehicles at a very affordable price. On the other hand, Toyota was very conservative and waste less with their TPS system when it came to putting automobiles on the market.
This was a classic example of the “Quality vs. Quantity” argument. Ford had created a commodity; they became a pioneer in the automobile industry providing the masses with thousands of vehicles at a time. They had a huge customer base and the infrastructure to provide their products and services worldwide. Toyota had a flexible system that created quality vehicles in a timely manner as well, just not as in much bulk as did Ford. They had an advantage over Ford in the fact that could offer a variety of vehicles with shorter lead times.
Ford had a very inflexible system and very long lead times, credited to their mass production system. Toyota’s system was more productive with their raw materials. They wanted to avoid work in progress inventories in their factories which lead to them incorporating a “pull system” into their manufacturing process. There are trade-offs: In comparing the two companies to each other, the trade-offs between the two become very obvious. Toyota offers a quality of vehicles that Ford can’t produce and Ford offers a price that Toyota can’t compete with.
Ford offered lower prices because supplies were not scarce and they had complete access. Also, after the war Ford had a ton of cash so they could provide their automobiles at a cheap price in hopes of making it a commodity. Their activity system allowed them to only make standardized products without any customization. With the luxury of having a high customer demand, Ford remained efficient. Toyota’s system which used JIT principles which allowed them to manufacture products in smaller quantities, with shorter lead times to meet specific customer’s needs.
This was a very flexible system which helped them offer an option of customization for their automobiles while still providing a high level of quality.
Conclusion
Ford paved the way for the automobile industry when they began the mass production of their Model T’s in 1908. The use of the assembly lines helped them sell thousands of vehicles and make millions of dollars in a short period of time. Toyota came along and used the same principles that Ford used, but refined their process to be more productive by using the ideology of continuous improvement.
Toyota wanted to become less wasteful, produce smaller batches of automobiles and create higher quality products within a flexible system that would allow them to react to customer demands without long lead times. By creating this flexible system, Toyota put their company in a better position than Ford. In order to be a leader in the automobile industry you must be able to react quickly to the market demands and provide the customers with a quality product in a reasonable amount of time. The TPS system allows Toyota to do that, while Ford would be in a world of trouble with inventory concerns because of their mass production system.
Even though both companies had very different beginnings, each has been successful in the automobile industry. They will continue to use each other as benchmarks when trying to create the best automobile possible for their customers.
Cite this Page
Toyota V.S Ford. (2017, May 11). Retrieved from https://phdessay.com/toyota-v-s-ford/
Run a free check or have your essay done for you
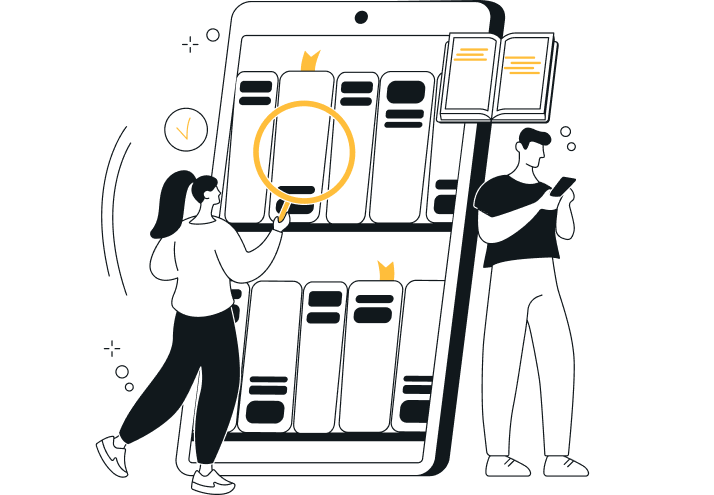