The Heritage of Operations Management
To start, I would like to give a view of ‘what OM is and why it is important today’. Operations management is the area concerned with the efficiency and effectiveness of the operation in support and development of the firm's strategic goals. Other areas of concern to operations management include the design and operations of systems to provide goods and services. To put it succinctly, operations management is the planning, scheduling, and control of the activities that transform inputs (raw materials and labor) into outputs (finished goods and services). A set of recognized and well-developed concepts, tools, and techniques belong within the framework considered operations management. While the term operations management conjures up views of manufacturing environments, many of these concepts have been applied in service settings, with some of them actually developed specifically for service organizations.
OM is also an academic field of study that focuses on the effective planning, scheduling, use, and control of a manufacturing or service firm and their operations. The field is a synthesis of concepts derived from design engineering, industrial engineering, management information systems, quality management, production management, inventory management, accounting, and other functions. The field of OM has been gaining increased recognition over the last two decades.
One major reason for this is public awareness of the success of Japanese manufacturers and the perception that the quality of many Japanese products is superior to that of American manufacturers. As a result, many businesses have come to realize that the operations function is just as important to their firm as finance and marketing. In concert with this, firms now realize that in order to effectively compete in a global market they must have an operations strategy to support the mission of the firm and its overall corporate strategy.
Order custom essay The Heritage of Operations Management with free plagiarism report
When talking about history, there are three aspects OM has focused in:
- Cost Focus (from 1776 til 1980),
- Quality Focus (from 1980 til 1995)
- Customization Focus (from 1995 til 2010).
We include all Eli Whitney, Frederick Taylor, Frank and Lillian Gilbreth, and Henry Ford in the Cost Focus era of the Operations Management History. Eli Whitney belongs to the first years of this era, who was the inventor of the cotton Gin. From a young age, Whitney had an innate understanding of machinery. The Yale graduate would later use this talent to invent the Cotton Gin, a mechanical device that transformed the economy of the pre-civil-war South. When inventor Eli Whitney arrived in the South in 1793, only green seed cotton could be grown inland. Problem was: the process of removing seeds from the cotton was extremely laborious. So Whitney devised a machine that automatically separated the seeds from cotton much faster than people could with their hands (in only one hour, Whitney's invention de-seeded a day's worth of cotton). When word got out about the Cotton Gin, plantation owners began planting as much green seed cotton as the land would allow. Though Whitney received a patent for his cotton gin invention in 1794, by that time the invention was being pirated and used all over the country.
Ultimately, Whitney left the South with very little to show for the invention that had made croppers millions. However, upon his return to the North, he re-invented American manufacturing with the idea of mass production. We also incorporate our second author in this era, Frederick W. Taylor (1856-1915), who is considered the father of the scientific management. Frederick Winslow Taylor devised a system he called scientific management, a form of industrial engineering that established the organization of work as in Ford's assembly line. This discipline, along with the industrial psychology established by others at the Hawthorne Works of Western Electic in the 1920s, moved management theory from early time-and-motion studies to the latest total quality control ideas. Frederick W. Taylor and his colleagues were among the first to systematically seek the best way to produce. Taylor, born in Philadelphia, prepared for college at Philips Academy in Exeter, N.H., and was accepted at Harvard. His eyesight failed and he became an industrial apprentice in the depression of 1873. At Exeter he was influenced by the classification system invented by Melvil Dewey in 1872 (Dewey Decimal System). He became in 1878 a machine shop laborer at Midvale Steel Company.
In his book he describes some of his promotions to gang-boss, foreman, and finally, chief engineer. He introduced time-motion studies in 1881 (with ideas of Frank B. and Lillian M. Gilbreth, strong personalities immortalized in books by their dozen children, such as Cheaper By the Dozen.) In 1883 he earned a degree by night study from Stevens Institute of Technology . He became general manager of Manufacturing Investment Company, 1890, and then a consulting engineer to management. Taylor's ideas, clearly enunciated in his writings, were widely misinterpreted. Employers used time and motion studies simply to extract more work from employees at less pay. Unions condemned speedups and the lack of voice in their work that "Taylorism" gave them. Quality and productivity declined when his principles were simplistically instituted. Modern management theorists, such as Edward Deming, often credit Taylor, however, with generating the principles upon which they act. Others, such as Juran, though, continue to denigrate his work. Read which best describes what people could buy on credit in the 1920s?
Modern theorists generally place more emphasis on worker input and teamwork than was usual in much of Taylor's time. A careful reading of Taylor's work will reveal that he placed the worker's interest as high as the employer's in his studies, and recognized the importance of the suggestion box, for example, in a machine shop. Frank Gilbreth (1868-1924): was an early advocate of scientific management and a pioneer of motion study, but is perhaps best known as the father and central figure of Cheaper by the Dozen. He brought many contributions to scientific management. He was married to Lillian Gilbreth (1878-1972), who was an American psychologist and industrial engineer. She was one of the first working female engineers holding a Ph.D. Lillian and her husband were efficiency experts who contributed to the study of industrial engineering in fields such as motion study and human factors.
Frank Gilbreth was born in Fairfield, Maine to John Hiram and Martha Gilbreth. He had no formal education beyond high school. He began as a bricklayer and became a building contractor, an inventor, and finally a management engineer. He eventually became an occasional lecturer at Purdue University, which houses his papers. He discovered his vocation when, as a young building contractor, he sought ways to make bricklaying (his first trade) faster and easier. This grew into collaboration with his eventual spouse, Lillian Moller Gilbreth, who studied the work habits of manufacturing and clerical employees in all sorts of industries to find ways to increase output and make their jobs easier. He and Lillian founded a management consulting firm, Gilbreth, Inc., focusing on such endeavors.
They both were involved in the development of the design for the Simmons Hardware Company's Sioux City Warehouse. The architects had specified that hundreds of 20-foot (6.1 m) hardened concrete piles were to be driven in to allow the soft ground to take the weight of two million bricks required to construct the building. The "Time and Motion" approach could be applied to the bricklaying and the transportation. The building itself was also required to support efficient input and output of deliveries via its own railroad switching facilities. According to Claude George (1968), Gilbreth reduced all motions of the hand into some combination of 17 basic motions. These included grasp, transport loaded, and hold. Gilbreth named the motions therbligs, "Gilbreth" spelled backwards with the th transposed. He used a motion picture camera that was calibrated in fractions of minutes to time the smallest of motions in workers. George noted that the Gilbreths were, above all, scientists who sought to teach managers that all aspects of the workplace should be constantly questioned, and improvements constantly adopted.
Their emphasis on the "one best way" and the therbligs predates the development of continuous quality improvement (CQI) (George 1968: 98), and the late 20th century understanding that repeated motions can lead to workers experiencing repetitive motion injuries. Gilbreth was the first to propose serve as "caddy" (Gilbreth's term) to a surgeon, by handing surgical instruments to the surgeon as called for. Gilbreth also devised the standard techniques used by armies around the world to teach recruits how to rapidly disassemble and reassemble their weapons even when blindfolded or in total darkness. Lillian Gilbreth combined the perspectives of an engineer, a psychologist, a wife, and a mother; she helped industrial engineers see the importance of the psychological dimensions of work.
She became the first American engineer ever to create a synthesis of psychologyand scientific management. She and her husband were certain that the revolutionary ideas of Frederick Winslow Taylor, as Taylor formulated them, would be neither easy to implement nor sufficient; their implementation would require hard work by both engineers and psychologists to make them successful. Both Lillian and Frank Gilbreth believed that scientific management as formulated by Taylor fell short when it came to managing the human element on the shop floor. The Gilbreths helped formulate a constructive critique of Taylorism; this critique had the support of other successful managers. Her work included the marketing research for Johnson ; Johnson in 1926 and her efforts to improve women’s spending decisions during the first years of the Great Depression.
She also helped companies such as Johnson ; Johnson and Macys with their management departments. In 1926, when Johnson ; Johnson hired Lillian as a consultant to do marketing research on sanitary napkins, the firm benefited in three ways. First, it could use her training as a psychologist in measuring and the analysis of attitudes and opinions. Second, it could give her the experience of an engineer who specializes in the interaction between bodies and material objects. Third, she would be a public image as a mother and a modern career woman to build consumer trust.
Henry Ford (1863-1947) was an American industrialist, the founder of the Ford Motor Company, and sponsor of the development of the assembly line technique of mass production. Ford did not invent the automobile, but he developed and manufactured the first automobile that many middle class Americans could afford to buy. Henry Ford has changed the way of life for many people with his vision to make owning a car both practical and affordable. The moving assembly line and mass production techniques that he developed, set the standard for worldwide industrial practice in the first half of the 20th Century. By the age of 12, he was spending most of his spare time in a small machine shop, which he had equipped himself. It was here that he constructed his first steam engine, in 1878, aged just 15. The next year, Henry left home, bound for the nearby city of Detroit, to work as an apprentice machinist.
His apprenticeship lasted three years, after which he returned home to Dearborn. During the next few years, Henry divided his time between operating and repairing steam engines, finding occasional work in a Detroit factory and overhauling his father's farm implements. The year 1888, saw a major change in his life, when he married Clara Bryant and began supporting his new family by running a sawmill.
It wasn’t long before Henry made another change and by 1891, he had become an engineer with the Edison Illuminating Company in Detroit. A promotion to Chief Engineer two years later, gave him enough time and money to devote more attention to his personal experiments on internal combustion engines. The culmination of his experiments was the building of a self-propelled vehicle the Quadricycle in 1896. The first Ford engine spluttered its way into history, on his wooden kitchen table at 58 Bagley Avenue and this was quickly followed by his next design, an engine mounted on a frame, fitted with four bicycle wheels – the first Ford car.
Lean Production Era (1980-1995): Just-in-time, Computer Aided Design, Electronic Data Interchange, Total Quality Management, Baldrige Award, Empowerment and Kanbans. The main originators of these concepts were: Harvard Business School faculty (USA), Tai-Ichi Ohno of Toyota Motors (Japan), W.E. Deming and J.M. (United States), and engineering disciplines (United States, Germany, and Japan), Eliyahu M. Goldratt (Israel).
Bibliography
- http://www.referenceforbusiness.com/management/Ob-Or/Operations-Management.html
- http://www.american-inventor.com/eli-whitney.aspx
- http://en.wikipedia.org/wiki/Frank_Bunker_Gilbreth,_Sr.
- http://en.wikipedia.org/wiki/Lillian_Moller_Gilbreth
- http://www.ford.co.uk/experience-ford/Heritage
Cite this Page
The Heritage of Operations Management. (2018, Jan 13). Retrieved from https://phdessay.com/the-heritage-of-operations-management/
Run a free check or have your essay done for you
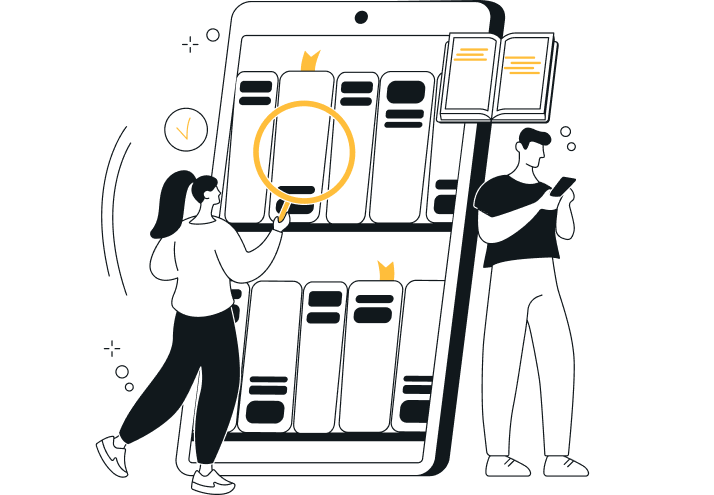