Taylorism and Scientific Management
While this theory has made many positive contributions to management practice, there have also been negative implications. On a positive note, Taylorism has made an impact on the introduction of the 8 hour working day, minimum wage rates and incentive and bonus schemes, and more importantly, highlighted management as an important area of study, allowing for other theorists to improve on, or provide alternative management theories in response to scientific management such as more worker orientated theories, namely behavioural management.
Taylor’s ideals have however been under constant scrutiny as managers highlight the shortfalls of scientific management. While the highly mechanistic way of practice may lead to increased productivity, it essentially works by dehumanising workers and viewing them simply as an ‘appendage of machinery. ’ Caldari argues (2007: 61) that Taylor’s ignorance of social considerations leads to conflict, low worker morale, and low trust between workers and neglect the ability for individual creativity to provide a positive input to the workplace.
While Taylor’s theories have been subject to many criticisms, scientific management has made an instrumental contribution to modern management practice across the world. By placing emphasis on the management of workers, Taylor essentially highlighted the importance of management theory and paved the way for further development on management as an important element of business practices. Taylor created a way of replacing the ‘guesswork’ involved in the manufacturing process by replacing it with a scientific way of thinking, strict rules and procedures (Caldari 2007: 58).
Order custom essay Taylorism and Scientific Management with free plagiarism report
This form of management practice allows managers to more efficiently control and direct their labour force and similarly it provides space for managers to monitor the workforce, and identify inefficiencies and sources of waste in the manufacturing process. As Parker and Ritson discuss (2005: 1340), this allows managers to observe the labour force and ensure that appropriate work procedures are being followed and appropriate results are achieved. Thus, creating space for managers to correct these inefficiencies early in the manufacturing process and minimise waste, subsequently maximising profits.
Therefore, although Taylor's contributions were considered controversial and even radical, his theory and dedication to management practice remains influential on contemporary business management, and he can be held responsible for laying the foundations for current strategic and systematic methods of planning and execution of tasks (Darmody, 2007: 1). Regardless of the benefits that may be gained from scientific work practices, criticism stemmed from the impression that Taylor had little concern with the psychology of workers.
Taylor’s search for a healthy and efficient workforce however, stemmed from research conducted on the relationship between long working hours and fatigue. Taylor was concerned with the effect that working hours was having on productivity and upon results of such experiments, proceeded to introduce shorter working hours believing that with fewer hours comes higher efficiency, intensified laboured hours and improved employee wellbeing. It is upon this philosophy, that Nyl (1995: 2) argues scientific management; primarily Taylor’s thinking was instrumental in creating the 8 hour working day of which is still implemented in many businesses today.
In despite of the above mentioned interest in worker well-being, Caldari (2007: 64) emphasises that Taylor naively assumed that with less, but more intense hours, increased productivity and wages, well being of workers would automatically improve. However, due to the intensely standardised and restrictive rules and procedures that scientific management brings workers are likely to feel unappreciated leaving the door open to the potential of conflict between workers and managers. In this case, a strict line of command is seen to have connection with low worker morale as high productivity is achieved at a price.
Caldari cites Marshall (2007: 66) saying that “trust, esteem and affection for staff are a valuable business asset, of a kind which machinery cannot achieve. ” This emphasis recognises one of the downfalls of scientific management in that it restricts the development of a cohesive ‘team’ like workforce, rather restricting management focus to individuals. The constraints that are placed on individuals prevent any worker initiative and eventually depriving a business of potentially important and vital input from employees.
As Caldari (2007) points out, managers “can miss the opportunity of taking advantage of potential resources but also, and moreover, for society that it is likely to waste its more important kind of capital. ” (p. 67) With this impression in mind, although Freeman’s discussion (1996: 2) focused primarily on the effect of scientific management in a Japanese business environment, he makes some interesting observations about Taylor’s mechanistic approach that can transcend cultural barriers. Freeman highlights that while criticism’s of
Scientific management revolve around it being ‘anti-worker,’ scientific management and ‘democratic’ management (which pays closer attention to the psychology and respect for workers) do not necessarily have to conflict. It is held that while the needs of workers are of foremost importance, Taylor’s ideal of quality management allowed for reduction in waste and increased production in Japanese business practices. In this context, scientific management was instrumental in improving efficiency and creating quality constraints, which ultimately lead to increased profits.
Freeman highlights (1996: 6) that by working with unions with an even handed focus on the interests of workers and productivity, business practice can meet a happy medium between scientific management and human relations in the management of business. This ideal emphasises that although some managers claim that there is no place in modern business practice for scientific management, it is possible for Taylor’s ideals to transcend time as managers adapt scientific theories and collaborate Taylor’s methods with other theorists that have followed in his steps.
Taylor’s scientific management has resulted in both positive and negative implications for business practice over the 20th and 21st century. We can see its contribution to modern business management in that many of its principles are still used today for example, minimum wage, rest periods and incentives for workers who reach a specified target.
While these theories were originally implemented in businesses such as Henry Ford’s car manufacturing, we can see that these processes continue to benefit managers today both in that very same business, and in the same ways in other industries including, and not limited to the hospitality industry where for example, detailed procedures and rules are enforced by a strict line of autocratic managers in a strict line of command at McDonalds or Hungry Jacks.
It has been highlighted that although Taylor’s scientific management incorporates shortfalls with regards to the management of a workforce as far as viewing a workforce as valuable human resources rather than machinery, in today’s management practices, elements of Taylor’s theory are able to work in conjunction with often more palatable behavioural theories in order to control and monitor a successful workforce.
Taylor was instrumental for creating a new ‘paradigm’ of management thinking and the scientific management theory does, and will continue impart to influence the way businesses operate and complete day to day tasks and assignments (Darmody, 2007: 1). Caldari, K. (2007). ‘Alfred Marshall’s critical analysis of scientific management. ’ The European Journal of the History of Economic Thought,14 (1), 55-78. Darmody, P. J. (2007). ‘Henry L.
Gantt and Frederick Taylor: The Pioneers of Scientific Management. ’ AACE International Transactions, 151. Davidson (2008) Management: Core Concepts and Skills in 'Management', John Wiley, Milton. Freeman, M. G. (1996) ‘Don’t throw scientific management out with the bathwater. ’ _Quality Progress,_ 29(4), Parker, L. D. Ritson, P. (2005) ‘Fads, stereotypes and management gurus: Fayol and Follett today. ’ Management Decision, 43(10), 1335.
Cite this Page
Taylorism and Scientific Management. (2018, Feb 02). Retrieved from https://phdessay.com/taylorism-and-scientific-management/
Run a free check or have your essay done for you
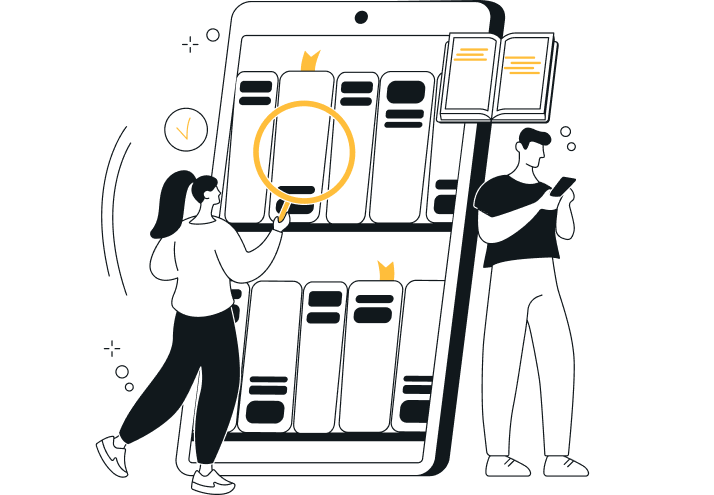