Skema Answer Manufacturing Proces 2
Assignment
- Define the various regimes of cold working, warm working, and hot working in terms of the melting point of the material being formed.
- Indicate some of the advantages of cold working relative to warm and hot working.
- What are some of the negative aspects of hot working? (8 marks)
Order custom essay Skema Answer Manufacturing Proces 2 with free plagiarism report
Answer
The temperatures required for hot working generally exceed 0. 6 times the melting point of the material on an absolute temperature scale.
Cold working generally requires temperatures below 0. 3 times the melting point, and warm working is the transition region, between 0. 3 and 0. 6 times the melting point.
Advantages of cold working are;
- better accuracy,
- better surface finish,
- increased strength due to work hardening,
- possible directional properties due to grain flow, and
- no heating of work required.
Disadvantages associated with hot working involve the reactions which may be promoted by elevated temperature, such as rapid oxidation.
Tolerances are poorer and the metallurgical structure will be nonuniform if the amount of deformation or thermal history varies throughout the product.
- What is the difference between open-die and impression-die forging?
- Explain the reasons why the flash assists in die filling, especially in hot forging.
- Why are heated dies generally employed in hot-press forging operations? (8 marks)
Answer
Open-die forging does not confine the flow of metal in all directions, so the final shape is dependent upon the manipulation and skill of the equipment operator.
Impression-die forging operations confine metal flow in all directions to provide good repeatable control of size and shape.
The flash is excess metal which is squeezed out from the die cavity into the outer space between the two dies. The flash cools faster than the material in the cavity due to the high a/h ratio and the more intimate contact with the relatively cool dies. Consequently, the flash has higher strength than the hotter workpiece in the die cavity and, with higher frictional resistance in the flash gap, provides greater resistance to material flow outward through the flash gap.
Thus, the flash encourages filling of complex die cavities.
Heated dies are usually employed in press forging because the long time of die contact with the hot workpiece would otherwise permit considerable surface cooling and could produce cracking of the surface.
- List some of the products produced on a rolling mill.
- In rolling of steel, what are the differences between a bloom, a slab, and a billet?
- Rolling may be described as a continuous forging operation. Is this description appropriate? Explain. (8 marks)
Answer
Rolled products include flat sheet and plate stock, round bar and rod stock, rails, structural shapes such as Ibeams and channels.
A bloom is a rolled steel workpiece with a square cross section of about 150 mm by 150 mm. The starting work unit for a bloom is an ingot heated in a soaking pit. A slab is rolled from an ingot or a bloom and has a rectangular cross section of about 250 mm by 40 mm. A billet is rolled from a bloom and has a square cross section of about 40 mm by 40 mm.
This is a good analogy. Consider the situation of forging a block to a thinner cross section through ncrements (as in incremental forming). As the number of stages increases, the operation eventually approaches that of the strip profile in rolling.
- Distinguish between direct and indirect extrusion.
- What is centerburst defect? How would you go about preventing centerburst defects in extrusion?
- What are some of the attractive features of the extrusion process? (8 marks)
Answer
In direct extrusion, also known as forward extrusion, a metal billet is loaded into a container, and a ram compresses the material, forcing it to flow through a die opening at the opposite end of the container.
In indirect extrusion, also known as backward extrusion, the die is incorporated into the ram, and as the ram compresses into the metal billet, the metal is forced to flow through the die opening in a direction that is opposite (backwards) of the ram motion.
Centerburst defects are attributed to a state of hydrostatic tensile stress at the centerline of the deformation zone in the die. The two major variables affecting hydrostatic tension are the die angle and extrusion ratio.
These defects can be reduced or eliminated by lowering the die angle, because this increases the contact length for the same reduction and thereby increases the deformation zone. Similarly, a higher extrusion ratio also increases the size and depth of the deformation zone, and thus will reduce oreliminate the formation of these cracks.
The extrusion process offers a number of attractive features. Almost any crosssectional shape can be extruded, including many that could not be achieved by rolling. Size limitations are few. No draft is required, and the amount of reduction in a single step is limited only by the capacity of the quipment. Frequently only one die is required for a product. Because only a single die change is required to change products, small production quantities are economically feasible. Dimensional tolerances are quite good.
What is wire drawing and bar drawing?
Why are multiple passes usually required in wire-drawing operations? l) Name the important process variables in drawing, and explain how they affect the drawing process. (8 marks)
Answer
Wire and bar drawing are bulk deformation processes in which the cross section of a wire or bar is reduced by pulling (drawing) it through a die opening. ) Because the reduced section of material is subjected to tensile loading in the wire drawing process, the possible reduction is limited by the onset of fracture. In order to affect any significant change in size, multiple draws are usually required.
The important variables include:
Yield stress, Y ; it directly affects the draw stress and die life.
Die angle, ?. The die angle in the deformation zone affects the redundant work; in the entry area, the die angle is important for encouraging lubricant entrainment.
Friction coefficient, ?. The friction coefficient affects the frictional component of work and, hence, the draw stress. Reduction in area. As described, there is a limit to the reduction in area that canbe achieved in drawing.
Lubrication condition. Effective lubrication reduces friction, but also may lead to a rough surface due to the orange peel effect. 6. m) Estimate the roll force and power for annealed low-carbon steel strip 200 mm wide and 10 mm thick, rolled to a thickness of 6 mm. The roll radius is 200 mm, and the roll rotates at 200 rpm. Let ? = 0. 1. Plot the force vs. reduction in height curve in open-die forging of a solid cylindrical, annealed copper specimen 2 in. high and 1 in. n diameter, up to a reduction of 70%, for the cases of (a) no friction between the flat dies and the specimen, (b) ? = 0. 25, and (c) ? = 0. 5. Ignore barreling and use average-pressure formulas. (Given : For annealed copper we have K = 315 MPa = 46,000 psi and n = 0. 54)
Answer
The roll force can be estimated as below; L=R? h=2004=28. 3 and have=10+62=8 mm From Table 2. 3 on p. 37, K = 530 MPa and n = 0. 26. The strain is ? =ln106=0. 5108 The average yield stress can be obtained from Eq. (2. 60) on p. 71 as Y=K? n+1n+1=530(0. 5108)1. 261. 26=180 MPa and Y'=(1. 15)Y=180 MPa Therefore, F=L? Y'1+? L2have =0. 02830. 2(207)1+0. 1(28. 3)2(8) =1. 38 MN The power per roll is given by; P = ? FLN60,000=? (1. 38 ? 106)(0. 0283)(200)60,000 or P = 409 kW.
For annealed copper we have K = 315 MPa = 46,000 psi and n = 0. 54. The flow stress is Yf=(315 MPa)? 0. 54 where the absolute value of the strain is ?=lnhoh From volume constancy, we have ?4r2ho=? 4r2h or r=ro2hoh Note that = 0. 5 in and ho = 2 in. The forging force is given as: F=Yf1+2? r3h(? r2) Some of the points on the curves are the following: % Red.
Cite this Page
Skema Answer Manufacturing Proces 2. (2017, Mar 03). Retrieved from https://phdessay.com/skema-answer-manufacturing-proces-2/
Run a free check or have your essay done for you
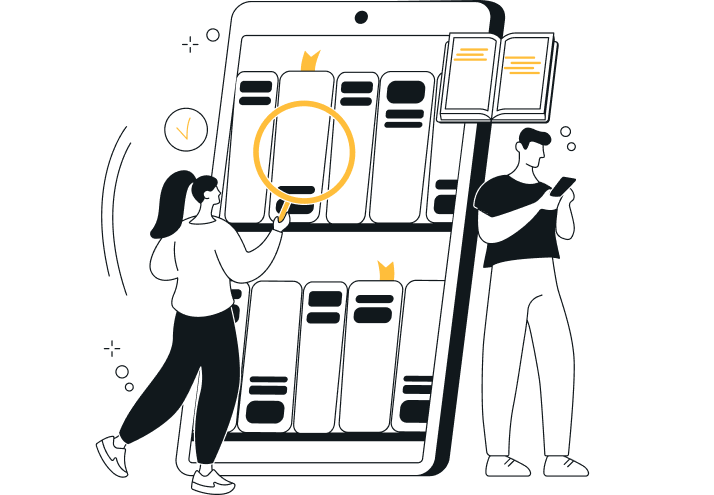