Nucor Steel Case Study Critical Analysis
Nucor From Wikipedia, the free encyclopedia Nucor Corporation TypePublic (NYSE: NUE) S&P 500 Component IndustrySteel & Iron Founded1940 HeadquartersCharlotte, North Carolina, USA Key peopleDaniel R. DiMicco, Chairman, CEO, & President Revenue US$ 11. 2 Billion (FY 2009)[1] Net income US$ 293 million (FY 2009)[1] Employees20,400 (2010) Websitewww. nucor. com
Nucor Corporation (NYSE: NUE), a Fortune 300 company headquartered in Charlotte, North Carolina, is one of the largest steel producers in the United States, and the largest of the "mini-mill" operators (those using electric arc furnaces to melt scrap steel, as opposed to companies operating integrated steel works with blast furnaces). Nucor claims to be North America's largest recycler of any material, recycling one ton of steel every two seconds. The total annual steelmaking capacity of the company is 25 million ton. [2] Contents [hide] 1 History 1. 1 The REO Era 1. 2 The Nuclear Corporation Era 1. The Nucor Era 2 Nucor Today 3 The Nucor Culture 3. 1 Decentralized Management Philosophy 3. 2 Performance Based Compensation 3. 3 Egalitarian Benefits 3. 4 Customer Service and Quality 3. 5 Technological Leadership 4 Environmental record 5 References 6 External links [edit]History Nucor's history consists of three distinct eras: the Reo Motor Car era, the Nuclear Corporation of America era, and the current Nucor era. [3][4] [edit]The REO Era Nucor's origins are with auto manufacturer Ransom E. Olds, who founded Olds Motor Vehicle Company in 1897 (later, as Oldsmobile, to become a part of General Motors).
Having left his company years before it was acquired by GM, in 1905 Olds established a new company, REO Motor Car Company, the predecessor to Nucor, in Lansing, Michigan. Though Olds' cars, including the luxurious REO Flying Cloud, were popular, they were not profitable, and the company's more successful truck business (featuring the famous REO Speed Wagon) was still not sufficiently profitable to avoid a bankruptcy filing in 1938. As part of the bankruptcy reorganization, REO exited the car business to concentrate on trucks, and after World War II, attempted to diversify into lawn mowers.
Order custom essay Nucor Steel Case Study Critical Analysis with free plagiarism report
The reorganized company continued to underperform, and finally in December 1954, REO sold off its entire manufacturing operations to Bohn Aluminum and Brass Company (suffering a $3 million loss on the sale). [edit]The Nuclear Corporation Era After the sale, REO was left with $16 million in cash on hand and no trading businesses. The company initiated liquidation proceedings, with the goal of selling its few remaining assets and distributing the cash to creditors and shareholders. However, a group of dissident shareholders noticed the tax loss and successfully challenged the liquidation in a proxy fight in September 1955.
In what amounted to a "reverse hostile takeover", activist shareholders forced REO to take over a tiny nuclear services company called Nuclear Consultants, Inc. Following the purchase, REO Motor Company emerged as "Nuclear Corporation of America Inc. ", and relocated to offices in the Empire State Building in New York City. Nuclear's attempt to recast itself as a nuclear industry services company was ultimately no more successful than REO had been. Nuclear then followed the example of other companies in the 1950s and 60s and attempted to become a conglomerate, once again moving its headquarters, this time to Phoenix, Arizona.
During this time it would purchase, among others, Vulcraft Corporation, a steel joist manufacturer located in Florence, South Carolina. Vulcraft had been founded by Sanborn Chase (no relation to the coffee company), who died at an early age, leaving the company to his widow. Nuclear purchased Vulcraft from Chase's widow in 1962 and, in a sign of things yet to come, hired F. Kenneth Iverson as general manager. But Nuclear the conglomerate fared no better than Nuclear the nuclear services company or REO the car/truck/lawn mower manufacturer, and in March 1965 filed for bankruptcy for the second time in 27 years.
The Board of Directors fired Nuclear's President (and, in the process, had to return his private jet to him), but for two months could not find a replacement, as nobody wanted to head a corporation that was most likely going to go out of business. Finally, Samuel Siegel, an accountant with Nuclear (and friend of Iverson) who had actively been looking to leave the company, informed the Board of Directors he would remain with the company under two conditions: Iverson would become President and he (Siegel) would become Chief Financial Officer, conditions the Board quickly accepted. [edit]The Nucor Era
Iverson and Siegel quickly reorganized Nuclear around its only profitable business, steel-fabricator Vulcraft. All other businesses were either sold or liquidated. The company moved its headquarters yet again, this time to Charlotte, North Carolina in 1966, to be closer to its main Vulcraft plant. Unable to get favorable prices from American steel manufacturers, and unhappy with the imported steel available at the time, Iverson (a metallurgist by training) decided to integrate Nuclear backwards into steel making by building its first steel bar mill in Darlington, South Carolina in 1968.
The company chose to purchase an electric arc furnace, which was far cheaper than the traditional steel blast furnace, courtesy of a US $6,000,000 bank loan from Wachovia. Although the early days were tough (once the American steel manufacturers learned Nuclear was operating its own mill, they canceled their contracts)[citation needed], Nuclear was finally able to obtain the financial success that had eluded the company from its beginning. In 1972 the company (recognizing that there was nothing "nuclear" about making steel or steel products) adopted its current name.
Since that time, Nucor has expanded into other steel products, gained some control of its raw material supply and greatly expanded its market presence. In the 1990s, Nucor bought Birmingham Steel, including the Mississippi Steel plant and Birmingham, Alabama operations. In September 2000, Dan DiMicco was appointed as the Chief Executive Officer by Nucor's Board of Directors. Under his leadership, Nucor has acquired compatible existing steel manufacturing facilities with similar operating philosophies.
Since 2007, Nucor has made the two biggest acquisitions in its history, one to help control its raw material supply and the other to expand its product line. In January 2007, Nucor agreed to pay $1. 07 billion dollars for Canada’s Harris Steel Co. The deal allowed Nucor to expand its presence in the type of steel used to build bridges, highways and other infrastructure projects. [5] Prior to 2007, Nucor had a single brand, Nucor Building Systems which consists of four facilities in Indiana, South Carolina, Texas, and Utah. 6] In August 2007, Nucor acquired the four brands of Magnatrax (American Buildings Company, Gulf States Manufacturers, Kirby Building Systems and CBC Steel Buildings) for $280 million to bolster its share in the pre-engineered metal building systems market. As a result Nucor Buildings Group was created. [7] In February 2008, Nucor agreed to pay $1. 4 billion for DJJ, one of the largest scrap brokerages. Analysts said the deal would help Nucor pocket more of its sales. In May 2008, Nucor also announced two joint ventures overseas to capitalize on thriving construction markets outside the U.
S. By Mid-2008, Nucor operated 53 facilities throughout the United States and one in Point Lisas, Trinidad. The company also maintained operations through wholly owned subsidiaries, Harris Steel and the David J. Joseph Company (DJJ). Since this time, when the stock reach its peak value (mid-2008), the company has lost one-third to one-half of its market value, and has not recovered as of 2012 [8] [edit]Nucor Today Nucor had sales of $11. 19 billion in 2009 and employed 20,400 workers. The 2009 loss of $293 million posted by Nucor was its first annual loss since 1966. Nucor 2009 Annual Report" Steel products produced include: Bars (carbon and alloy steel) Beams Sheet/Flat Rolled Plate Steel joists Joist girders Steel deck Fabricated concrete reinforcing steel Cold finished steel Steel fasteners Metal building systems Light gauge steel framing Steel grating Expanded metal Wire and wire mesh In addition, through DJJ, Nucor also brokers ferrous and nonferrous metals, pig iron and HRI/DRI; supplies ferro-alloys; and processes ferrous and nonferrous scrap. [edit]The Nucor Culture
The Nucor Culture can be summarized in five areas: decentralized management philosophy, performance based compensation, egalitarian benefits, customer service and quality, and technological leadership. Underlying these elements is the fact that none of Nucor's plants, whether built from scratch or acquired, are unionized. Nucor is opposed to unions, believing them to be a destructive force in the US steel industry. No Nucor plant has ever held a successful union certification election, even though Nucor management has not engaged in the controversial "union busting" tactics adopted by other companies.
The company has never laid off an employee due to a work shortage. [edit]Decentralized Management Philosophy Nucor is highly decentralized in its operations, there are only five managerial levels at Nucor (supervisor/professional, department manager, division general manager, executive vice president, and President/CEO). Most operating decisions are made at the division level or lower. In addition, Nucor claims that its corporate office staff numbers around 75 employees, which may possibly be the smallest number of corporate office employees among major corporations. [edit]Performance Based Compensation
All Nucor employees, from senior officers to hourly employees, are covered under one of four basic compensation plans (in addition to base pay) which reward employees for meeting certain incentive specific goals and targets: Production Incentive Plan: Operating and maintenance employees and supervisors at the facilities are paid weekly bonuses based on the productivity of their work group. The rate is calculated based on the capabilities of the equipment employed, and no bonus is paid if the equipment is not operating. In general, the Production Incentive bonus can average from 80 to 150 percent of an employee's base pay.
Department Manager Incentive Plan: Department Managers earn annual incentive bonuses based primarily on the percentage of net income to dollars of assets employed for their division. These bonuses can be as much as 80 percent of a department manager's base pay. Professional and Clerical Bonus Plan: This bonus is paid to employees that are not on the production or department manager plan and is based on the division's net income return on assets. Senior Officers Incentive Plan: Nucor's senior officers do not have employment contracts. They do not participate in any pension or retirement plans.
Their base salaries are set lower than what executives receive in comparable companies. The remainder of their compensation is based on Nucor's annual overall percentage of net income to stockholder's equity and is paid out in cash and stock. In addition to these established bonus plans, Nucor has periodically issued an extraordinary bonus to all employees, except officers, in years of particularly strong company performance. This bonus has been as high as $2000 for each employee; during 2005 two such extraordinary bonuses were paid and another in 2009 was paid(per the 10-K filing). edit]Egalitarian Benefits Nucor's senior officers are not provided traditional "perks" such as company cars, executive parking spaces, or executive dining rooms. In fact, several programs (such as Nucor's Profit Sharing, Scholarship Program, Employee Stock Purchase Plan, Extraordinary Bonus, and Service Awards Program) are not available to Nucor's officers but only to lower-level employees. As a symbol of Nucor's egalitarian culture, each annual report since 1975 has listed the names of every employee. In 1975, there were 2,300 workers and their names fit on the back cover.
In the 2007 annual report, it took 12 pages to list the names of all 18,000 employees. In August 2006, the company did purchase a corporate jet for use by senior management. In a letter to all employees from the CEO, Dan DiMicco explained that the frequent rentals of charter jets made a corporate jet purchase a cost-effective measure. [edit]Customer Service and Quality Nucor is a member of the U. S. Green Building Council and has participated in other elite environmental programs, such as the Environmental Protection Agency’s National Environmental Performance Track program.
Nucor has also sponsored construction of a regional butterfly aviary, launched a waterfowl protection project and helped preserve wetlands. Several divisions have environmental management systems that conform to ISO 14001 standards. [edit]Technological Leadership Nucor was among the first steel companies in the United States to use electric arc furnaces to melt recycled steel (primarily from junked automobiles). In 2007, Nucor recycled nearly 10 million cars in its production processes, the equivalent of one SUV every four seconds.
The company's website maintains a running count of the tons of recycled steel used during the current calendar year. Currently, Nucor (in conjunction with two foreign-owned steel companies) operates a facility in Crawfordsville, Indiana that continuously casts sheet steel directly from molten steel without the need for heavy, expensive, and energy-consuming rollers. The process (known as Castrip[9]), if successful, would allow an entire mill to be built in 1/6 the space of a 'mini-mill' and at 1/10 the cost of a traditional integrated mill.
They call this concept a 'micro-mill'. Also, Nucor has two pilot projects, one in Western Australia and one in Brazil, which are developing low-cost sources of iron for use in its mills. [edit]Environmental record In 2000, Nucor settled with the U. S. Justice Department and the United States Environmental Protection Agency to resolve allegations that it had not adequately controlled the emission of toxic chemicals into the air, water, and soil of Alabama, Arkansas, Indiana, Nebraska, South Carolina, Texas, and Utah.
The $98 million result was "the largest and most comprehensive environmental settlement ever with a steel manufacturer. "[10] The University of Massachusetts' Political Economy Research Institute in 2002 ranked Nucor as the fourteenth-largest corporate contributor to U. S. air pollution, with a toxic score of 152,421 (pounds released ? toxicity ? population exposure) due to the release of 760,000 pounds of toxins into the air yearly. [11] Since DiMicco took charge of Nucor in September 2000, he has emphasized that he wanted the company to become a leader in environmental performance.
Nucor has added environmental staffing and training and adopted new technology – in some cases, groundbreaking technology that Nucor is working to patent and license to other companies. The number of toxins released, as measured by the University of Massachusetts study, has dropped by more than 35 percent. Nucor is considered to be the largest steel recycler in the U. S. “We have always been green,” explains Shell. “NBS buildings average over 80 percent recycled content. ” Projects fit with the industry trend of implementing green initiatives. [12]
Cite this Page
Nucor Steel Case Study Critical Analysis. (2017, Dec 17). Retrieved from https://phdessay.com/nucor-steel-case-study-146310/
Run a free check or have your essay done for you
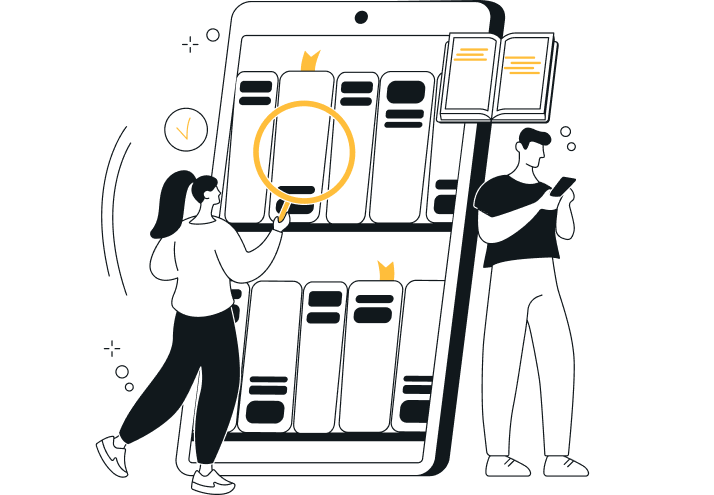