Manual vs. Automated Statistical Process Control in the Food Industries
Israel Ortega-Ramos The Prime Example Our recent visit to a food packaging plant in New Jersey highlighted the inconsistent results of statistical process control routinely faced by Quality Control Managers. Product weight readings were taken from the manufacturing floor, entered into an Excel spreadsheet and analyzed. The results produced no predictable under or over filling trend despite the fact that the same people used the same scales at the same time of day. The problem is simple and fundamental. Human error is an inevitable part of the process of collecting statistical data.
This is consistently overlooked in companies that utilize manual SPC[1] (statistical process control) for their manufactured goods. To ensure the human error factor is eliminated, resulting in lower costs and increased profitability, manufactures must begin utilizing more “high-tech” means of collecting, analyzing, and storing SPC data. The Hidden Problems of the Current Manual SPC Process To better understand the core problem, and find a solution, it is pivotal to understand how this food packaging plant utilizes manual SPC.
Generally, several samples are taken from a product line at different times of day, usually 15 or 20 samples at a time. These samples are then individually weighed; a line worker records the results on a clipboard for analysis. The individual weight readings are entered into a computer and various statistical calculations are derived from the weighing results, including frequency distribution charts and Pareto charts that are used to adjust the actual filling machines to deliver a consistent result.
Order custom essay Manual vs. Automated Statistical Process Control in the Food Industries with free plagiarism report
The Quality Manager must then resolve any conflict between under filling a package, which breaks government laws and overfilling a package which causes lost revenue. Using the diagram to get a better understanding of SPC will make it easier to locate the fundamental problems with the manual SPC system in use. The problems begin with the manual recording of 15 identical products by the line workers. The simple act of weighing an item then transferring the result to a clipboard by pencil or pen is flawed and full of possible errors, i. . the incorrect number can be recorded or a sample can be weighed accidentally more than once. This means the human emotion factor begins to play a large part in the problematic result. In addition, the manager obtains the clipboard results from the same worker who is required to climb inside the hot filling machine to adjust the volume if the weight results are not consistent. A line worker therefore might also assume that weight readings on the clipboard that differ from each other might mean he/she is not doing a good job.
The underlying result of a manual SPC system is the company loses money resulting when each package of food is either overfilled beyond the nominal weight or worse being under-filled which could mean hefty government fines. To summarize, the current manual SPC process allows too many errors and offers no traceability of weighing results throughout the system. The implementation of an automated SPC scale system would eliminate these manual user errors with only a few changes and a small capital investment. The Advantages of an Automated SPC System
Designing an automatic SPC system that eliminates human error begins by removing the manual element from employee responsibility. This will alleviate human recording errors and the fudging of actual weight results. To accomplish this, the old scale, clipboard, and pencil must be removed and replaced with a scale system equipped with automated SPC software. This software is fully configurable to satisfy all SPC tolerances. The scale display will actually prompt the worker when to place a product on the scale.
The fully automated “SPC Scale System” will not allow products placed on the scale to be removed; rather only permit the addition of new products. This will eliminate the possibility of placing the same product on the scale more than once, as well as any confusion and/or fudging. The scale will then calculate the statistical data after the last product is placed on the scale and store this data in a password-protected memory for collection by the Quality Manager. This statistical data can then be sent wirelessly to a spreadsheet, printed on a label to accompany the sampled roduct, or simply viewed on the scale interface. The flow diagram below shows the improved SPC process. Companies can also utilize various connectivity and software options that can integrate filling machines to automated SPC scale systems. This means that fill volumes based on trends calculated by the scale can be adjusted via an automated system. Quality Control Managers and Plant Managers can also connect all the SPC scale systems in a factory via a central control computer that will provide easy access to “real-time” data.
Integrating an automated SPC Scale System into a manufacturing environment will have the following advantages over the older manual SPC systems: Upgrading outdated manual SPC processes is the first step to improve overall quality, efficiency, and trace ability. This can be accomplished with as little as $5,000 in capital investment. Quality Control Managers and Plant managers have to take a hard look at how their product samples are being weighed and how these measurements are turned into results that can improve production line efficiency.
It is now time for companies to step into the 21st century and upgrade to a fully automatic SPC weighing system. [pic] ----------------------- ----------------------- Error Filled SPC System START Statistical data evaluated and translated into adjustments to correct filling machine fill volumes. Data transferred from clipboard to spreadsheet for statistical evaluation. Each product is placed on scale. Random Batch of Product taken from Production Line.
Filling machines manually adjusted according to collected data. Data collected by Quality Control Manager. Weight is recorded on clipboard in order weighed on scale. FINISH Optional Filling Machines adjusted automatically by SPC scale system. FINISH Random Batch of Product taken from Production Line. Each product is placed on scale. Scale automatically calculates statistical data. Statistical Data transferred to computer database directly via wireless or Ethernet connection. START Product Weight Scatter Graph.
Cite this Page
Manual vs. Automated Statistical Process Control in the Food Industries. (2016, Dec 18). Retrieved from https://phdessay.com/manual-vs-automated-statistical-process-control-in-the-food-industries/
Run a free check or have your essay done for you
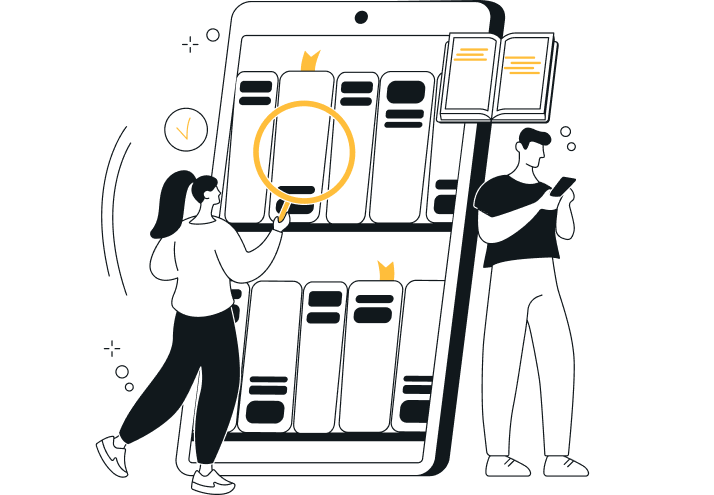