Logistics and Operations Management of IKEA Company
This paper draws on the model that operations and logistic management form the base of any organization with its mission geared towards efficient production and distribution of goods and services in the right quantity and quality as well as in the right place and at the right time. In the business environment, organizations draws on the strategic models of logistics and operations management to make valuable contributions towards design, implementations and system management for the deployment of physical facilities, personnel, in-process inventories, raw materials as well as finished gods and services in the most efficient way.
Business and economics analysts argue that logistics and operations management facilitates a concise approach to supply chain, from the acquisition of raw materials, productions of goods and services to the point where they are consumed. IKEA Group is a National Competitive Advantage of Swedish Company founded in 1943. It operates a multinational chain of stores for home furniture and furnishing; specializing in stylish but inexpensive Scandinavian design furniture, and thus enjoying the reputation of a world’s largest furniture retailer.
Over the years, IKEA Group has employed strategic logistics in its operations, production and marketing (Chary, 2004, pp35-37). Examining the case of IKEA Groups, logistics and operations management has propelled the company to designs its products in a pattern that disassemble the entire unit and transport parts of the furniture in flat packages.
Order custom essay Logistics and Operations Management of IKEA Company with free plagiarism report
The corporate interplay between IKEA’S corporate strategy and the business model of logistics and operations management is evident in the evolution of IKEA’S expansion strategies, business model, supply chain planning and processes as well as the relationship between Ikeas’ management, its suppliers, warehouse operations and store design. The Interplay between IKEA’S Corporate Strategy and Operations Management Research shows that the operations functions of IKEA reflect a relationship with its corporate strategy by exhibiting strategic operations management, supply chain planning, processes and control (Chary, 2004, pp113-114).
Accordingly, the productions of goods and services in IKEA Company involve the organizations commitment and ability to responsibly ensure that business operations in the company are not only efficient but also effective. In light of this, IKEA has drawn from logistics and operations management to paint a business picture of its corporate strategy manifested in the management of resources, production as well as distribution of goods and services to customers in an efficient queue system. Read also Challenges Facing By Ikea
Hoek and Harrison (2008, pp 76-77) postulates that operations and logistics management of IKEA focuses on the concise approach of achieving their goal enshrined in their motto, “ Affordable Solutions for Better Living”. IKEA expresses a relationship between the whole concept of operations management and its corporate business strategy by using the company’s resources in an effective way and thus gain huge profits by equally developing a more economic pedestal of producing their wide range of goods.
This dimension has made IKEA company to work closely with its suppliers in a bid to control elements of business from the production line to supply chain management. Unlike many furniture stores, IKEA builds on operations and logistics management to sell goods that are meant to be assembled by the customer. This operations planning has enabled IKEA to efficiently use the available space in the warehouse.
The company extensively uses operations management to reinforce its corporate strategy by developing business methods that satisfies customers with the wide use of technology as well as their unique selling points such as stock control (Greasley, 1999, pp 217-219). Operations Strategy of IKEA Company IKEA stands out in its supply chain due to its idiosyncratic operations strategy which is inspired by its mission to offer a wide range of furniture of excellent quality, durability as well as lows prices that most customers can afford to buy (Chary, 2004, pp 86-87).
Read also about Threshold Capabilities
The primary operations strategy is enshrined in the innovative approach of IKEA founder to design functional furniture that are inexpensive to build, receive them at the stores when they are already disassembled and display them in the showrooms thus making the need for sale people almost unnecessary (Kent, 2006, p 192). Accordingly, IKEA benefits from this operations strategy by modeling its operations and logistics management to empower customers to typically spend some time in the store.
In this distinguished approach, IKEA achieves a competitive edge in the market place and makes shopping at its store more of an endearing experience. IKEA stores double up the role of a warehouse and they are build for the purpose of browsing such that the furniture are displayed in the stores as it would be in a home setting . Rosenfield et al, (2005, pp 311-312) argue that although this operations strategy seem simple, it enables shoppers to see everything in terms of IKEA’S products, ranging from kitchen wares, furniture to bowl soups under one roof.
Arguably, the genius of this business model is inherently built in the flat packed, assemble at home beds, cabinets, bookcases and other furniture; a concept that reduces the operations cost by making the customers half producers and half consumers. Operating just like a warehouse, IKEA Company produces a high volume of products that are easily self-assembled. With regard to this, Fender et al (1998, pp 62-63) argue that IKEA is able to operate in many companies thereby allowing for the economies of scale and reduce its productions well as operations cost and still maintain a high volume production.
Similarly, there is a variety of dimension in IKEA’S operations strategy such that its furniture becomes the value for money within a wide range of choices. For example, IKEA designs its products to be stored and sold as flat packs that can be easily assembled by the customer. In addition, IKEA promotes its products in a modular perspectives allowing for varied dimensions of the same product to personalize to yield greater variety. Accordingly, these varied dimensions allow IKEA as a company to offer greater variety for its products without the necessity of holding larger amounts of stocks in the stores.
Significantly, IKEA builds on the unique operations management where customers have the flexibility of moving around the stores to pick whatever they want thus eliminating the need for sales personnel. The philosophy behind this approach is not to hassle the customers but instead allow them to make their shopping decisions at their own convenient time. As such, if customers are in need of any advice, the staff only guides them around the store. Process Types and Layout Design It is significant to understand that the older stores for IKEA are usually very large often designed around a layout feature that is one way.
Schonsleben (2007, pp 91-92) underscores that such layout design leads customers on the natural consumption way. In essence, this layout design is made to encourage customer to tour the stores and see the products in entirety as opposed to the customary retail stores that allow customers to go straight to sections with products they need. Newer IKEA stores on the contrary integrate the use of glass for aesthetic as well as functional reasons. In this way, there are advanced self service warehouses, which reduce the costs of energy and improve the morale of the staff, give an improved and better impression of the product.
In addition, IKEA involves a warehouse design in their store integrating a showroom and a market place on one end. This allows for the stock to kept and still allow large stock quantities to be accessed at a single day. According to Hoek and Harrison (2008, pp 145-146), most stores of IKEA company are designed in a layout that reflects a unified business platform such that at the end of the warehouse, there is a cashier and similarly, the returned, damaged or formerly showcased furniture which are not in the good condition are taken out of the IKEA product range and sold at a significant discount.
This means that the operations management and logistic helps IKEA company to communicate the policy of environmental issues. As such, the stores have omitted spaces and the vast stores are located outside the city centers to primarily cushion the element of traffic access and land costs. Facility Design The facility design of IKEA in light with operations and logistics management concerns the wider angle of moving finished products to the customer. In facility design, Greasley (1888, pp 79-81) argues that the element of physical distribution is factored in, where the customer becomes the final destination in the whole channel of marketing.
Accordingly, IKEA Company uses the availability of the product as the important aspect of facility design where each participant in the marketing channel makes a significant contribution in the production and consumption of products. Through the process of facility design and physical distribution, IKEA enhances the customer space and time making it an integral part in the operations management. The logic of this design aims at providing well established warehousing, transport and inventory controls. It also provides IKEA with an opportunity to plan and control supply chains by reaching at strategic decisions.
In addition, the manufacturing flow is enhance through a facility design of this nature where activities related to scheduling, planning and supporting production operations such as work in process storages, transportation and emphasizing of components are done in addition with the geographic as well as assemblies of physical distribution operations (Kent, 2006, pp 221-222). Capacity In this dimension, IKEA continues to use the performance management in the wider perspective of logistics and operations management to increase their ability and produce quality products hence afford to gain a competitive advantage.
Rosenfield et al (2005, p 318) contend that capacity management of IKEA portrays the ability to enhance production process in large measures through planning that helps in decision making about the overall business investment and growth. IKEA, through capacity management, portend a process of embracing global approaches as well a solutions in managing supply planning and replenishment based on store level forecast. Through various operations and logistics managers, IKEA is building on technology and information technology in a bid to network the operations of its 202 stores across the world.
In light of this, Fender et al (1998, pp 67-68) assert that the capacity management of IKEA explain how the company has been able to hold over 3million stock keep units with a variety of products. The reported growth of IKEA over the years describes its efficiency in capacity management. Accordingly, the company has managed to work and solve the problems of transparency in supply chain and integrate earlier supply planning and thus rise above the capacity management challenges associated with high inventory costs, and a fragmented information technology.
The digital age has paved way for the use of ICT in inventory management and so, IKEA Group relies heavily on the use of information technology to track their inventories by scanning in and out of any merchandise on a daily basis (Schonsleben, 2007, p 86). This method, involves the use of a database or other software that are relevant with supply management. Accordingly, the method helps IKEA in the cataloguing of information including the quantity on hand, cost of the item as well as location on the warehouse.
Software inventory management gives a clear picture of how items are sold and allows inventory checks to be processed more efficiently and quickly. Process Design Within the perspectives of logistics and operations management, IKEA Company employs a strategic approach of service characteristics within all operational issues. Scholars have argued that the process design of operations management works within the wider service unique characteristics (Greasley, 1999, 73-74).
In essence, the process design of IKEA include the intangibility, customer influence, heterogeneity, labor intensity as well as the inseparability of both production and consumption aspects of operations management. As service characteristics, the operations management of IKEA uses them within the framework of interdependency. According to Chary (2004, pp 89-91), the process design in these characteristic not only makes them interdependent but also overlap to some degree. As such, IKEA benefits from these processes design by making the operations management easy and efficient.
Essentially, it is plausible to argue that customer interaction, customer contact, customer involvement and participation reflects the impact of IKEA’S process design in operations management. The process design therefore determines the logistic management of inventory management. Primarily, IKEA Group as an organization believes that the ultimate goal of any inventory management system is to facilitate a complete and up to date view of all components in an organization, ranging from assets to capital to turnover.
Greasley (1999, pp 176-177) outlines that the fundamental essence of inventory management is to provide an actual state of affairs for all infrastructural components in the organization. Ideally, IKEA benefits from this rationale hence, as an organization; it forms inventory systems, which facilitates easy and efficient retrieval as well as sharing of information either vertically or horizontally. Various ways used by IKEA organization to manage inventory and the overall operations management, borders the precincts of planning, replenishment and control of activities.
These inventory management have improved an IKEA’S inventory turnover ratio, thus facilitating the transformation of frozen inventory into cash. The organization’s inventory management is one of the biggest in the world with many hubs located across many nations (Kent, 2006, pp 97-98). With this concise process design, IKEA enables the production of goods from the company without the presence of customers then they are stored in the showrooms which facilitates how they are sold.
The simultaneous production and consumption that characterizes how IKEA allows the customer to buy and assemble the furniture at home makes the production process exposed for customer evaluation as well as influence. However, it is plausible to note that the process design of IKEA does not present a clear cut distinction between the stages of production and consumption. IKEA Operations Management The approaches of operations management add value to the delivery of IKEA Company by enhancing the performance and measurement.
There is a strong interplay between the company and customer integration to market share and profitability. Scholars explain that with the operation strategy and capacity as well as process design, IKEA takes advantage of distribution capabilities and extensive emphasis on the perspectives of supply chain in customer relations as well as the company’s performance index (Rosenfield et al, 2005, p 318). In addition, the company realizes logistics competencies by creating and maintains a competitive advantage.
Manufacturing firms that engage in operations management such as IKEA, benefit from the performance measurement that improves the overall productivity of the company. Facility design, process types and layout design are concepts of operations management that enhances the company’s delivery value in light with quality and reduced distribution costs.
Improving Operations and Logistic Management in IKEA Implement leagility in Supply Chains According to Greasley (1999, pp 56-57) leagility, defined within the precincts of supply chain design, is the combination of both agility with lean capabilities within a single supply chain.
It therefore follows that IKEA group should improve its inventory by using leagility because it works best in operational terms as lean capabilities contributing largely to agile performance. In addition, Chary (2004, p221) underscores that leagility is the logistic approach that is required to fit succinctly within a purely agile supply chain strategy as opposed to a rather lean approach. Inventory results using this model will optimize asset utilization in terms of manufacturing because of the variability driven by demand spikes such as customer order, by manufacturing processes themselves in the light of logistical upsets.
Outsource Inventory Another approach to inventory management that IKEA should build on is to apply service-parts technology to the inbound supply side such as vendor managed inventory system. For proof of concept, IKEA Group has virtually no inventory other than the finished product shipped to customers. The entire inbound supply-side inventory is maintained by IKEA vendors and as a result, this approach makes organization’s no-inventory claim somewhat disingenuous. Significantly, the suppliers are carrying the inventory in plants and warehouses camped production plant.
However, somewhere a happy medium exists in IKEA’s managed inventory (Hoek and Harrison, 2008, pp 345-346). Conclusion The fundamentals of any company’s success rest on the elimination of wastes and maximization of profits. Inventory management and transportation approaches in supply chains designs, comes in handy by helping supply managers of IKEA Company, in achieving this coveted business goal. From the foregoing discussions, it is evident that effective logistics and operations management through the various available methods have made it possible for IKEA to benefit from over production and eliminate unnecessary processing.
By including logistics management and workflow, IKEA has set up thresholds and other parameters for a wide variety of variables associated with forecasts, customer demand, production, material movement, and logistics management. In addition, efficient operations management increases the organization’s success in satisfying customers’ demand and at the same time reduces the control of daily logistics operations. Bibliography
Chary, W. 2004. Productions and operations Management: A Case of IKEA Company. New York:
McGraw Hill Fender, M et al. 1998. Global Operations and Logistics. London:
John Willey and Sons Greasley, A. 1999. Operations Management in Business. London:
Nelson Thornes books Hoek, R and Harrison, A. 2008. Logistic Management and Strategy. Competing Through Supply Chain. Oxford:
Prentice Hall Kent, G. 2006. Operation and Logistics Management: A competitive Advantage in the 21st Century. London:
Blackwell Publishers Rosenfield, D et al. 2005. Modern Logistic Management: Integrating Manufacturing, Marketing and Physical Distribution. New York:
Sage Books Schonsleben, P. 2007. Integral Operations and Logistics Management in Comprehensive Value added Networks. New York: Routledge
Cite this Page
Logistics and Operations Management of IKEA Company. (2018, Jan 16). Retrieved from https://phdessay.com/logistics-and-operations-management-of-ikea-company/
Run a free check or have your essay done for you
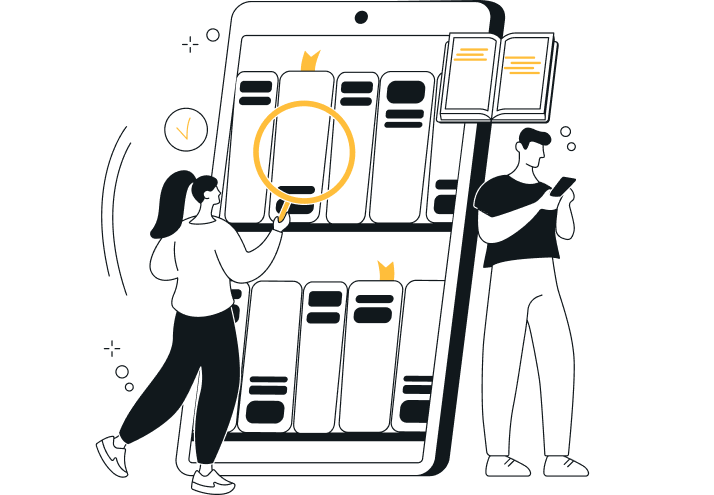