Leadership and Change Management: a Case Study of Pemancar
For personal use only. Leadership and Change Management: A Case Study of Pemmican Mr.. Denial Tarter, the new plant manager was walking through the factory floor during his daily rounds in Pemmican's, a production plant located in Peninsular Malaysia. This is his first week on the job. Pemmican's parent company, Nova Europe International Corporation (Nova), was not happy that Pemmican had not consistently achieved the production targets set by them. The previous plant manager, Mr.. Adam was held to task for the non-achievement of the set targets. He was demoted and asked to head another small subsidiary a few months earlier.
Before Denial was brought in, Pemmican was temporarily managed by managers brought in from Nova. Tindal heard that Adam, the previous plant manager, who had been working at Pemmican for nearly twenty years, might probably be laid off later. He keeps thinking of the situation in Pemmican and the changes he is going to make to ensure that the production targets are met and the cost contained. After walking through the factory floor, Denial took the stairs to the administrative office of Pemmican. Although it was nearly seven in the evening, there were still staff working at their desk.
He needed to talk to the head of finance regarding the Issues and problems faced In the factory. On his way to the office of the head of finance, he saw that one of the employees was filling in application forms to work in other companies. All Beth names have been changed. Name of the company has been changed to ensure confidentiality. DOE 10. 1142,'S0218927512500058 0 2012 by World Scientific Publishing Co. 116 ACRE Denial reflected on the conversation and the information he gathered from the managers and other employees since the first week he was in Pemmican.
Order custom essay Leadership and Change Management: a Case Study of Pemancar with free plagiarism report
In fact, in his various conversations with the employees, some of them did mention that they had created resumes, surfed the websites to look for other Job opportunities, or applied for continuing education to prepare for the eventuality of being out of a Job at Pemmican. He now needed to identify the issues and problems pertaining to the non-achievement of targets and the ways to keep the employees motivated and their morale high. Pemmican Pemmican is an automotive part production company located in Peninsular Malaysia. The company was established in the late sass and was owned by several state and federal government agencies.
In the mid-sass, the company was acquired by KILL Corporation (Color), one of Malaysia's leading multinational conglomerates. Since the acquisition by Color, the company has undergone a technical cooperative agreement with a Japanese company in 1987. This was to ensure that Pemmican is equipped with the latest technology and expertise of their production. The marketing and distribution of the products was then carried out by the marketing and sales department in Pemmican. Figure 1 portrays the kind of organizational structure that used to exist at Pemmican while it was under Color.
Pemmican, under Color was headed by a Plant Manager, who oversaw the whole operation of the plant and the support division. The Manufacturing Division consists of seven main departments, namely, Production, Engineering, Industrial Engineering (E), Planning, Quality Management (KM), Product Industrialization (P'), and Plant Operation. While the Support Division consists of the following six main departments, namely, Human Resources, Finance and Accounting, Controlling, Purchasing, Information Technology (IT) and Environmental, Health & Safety (SHE). Asian Case Rest. J. 012. 16:11 5-132. Downloaded from www. Worcestershire. Com by Plant Manager (PLUM) First PLUM (before acquisition to December 2006) Senior Management Secretary to PLUM Head of Plant Purchasing Head of Finance & Accounting Head of Controlling Head of IT Head of SHE Head of POP Head of Planning Head of IEEE Head of Production Head of Eng Head of KM Head of PI Middle Management Executives Section Heads & Executives Junior Management Supervisors & Personal Assistants Staff (Clerical and non-clerical) Lower Level Employees Shop-floor Employees (Leading Hands & Machine Operators)
LEADERSHIP Oral CHAngE Marriageable: A CASE STUDY OF Pemmican 117 Fig. 1 . Pemmican -? Organizational Structure before acquisition until December 2006. 118 In terms of manpower, Pemmican has approximately 1,700 employees of which 100 are at the middle management and managerial level, 130 are at the supervisory level, 100 are administrative (clerical) staff and 1,370 are at the operative level (direct and non-direct). Under Color, Pemmican is the largest plant in the northern part of Peninsular Malaysia, which produces various types of automotive parts.
Its keg in year 2003/04. Pemmican has grown and flourished over the years and its production volume has secured the company as one of the leading automotive parts suppliers in Malaysia. Its products are also exported to more than fifty countries, I. E. Europe (41 the Middle East (23%), Australia (18%), Sean countries (15%) and other countries (3%). Pemmican has received recognition at both the national and international levels.
They have received several quality and management awards (such as the ISO 9002 recognition and the Malaysian Standard awarded by SCRIM, the European Standard and the gulf Standard, SHOOS, the China Standard ACT) and also recognition awards from their customers (for example: Best Supplier Award, Best Supplier Performance Award, Quality Management Award, Export Excellence Award, and Energy Savings for Industrial Sector Award). OrgANizAtiONAL CuLturE under Color under Color, the mission of Pemmican is to become the most prominent producer of automobile parts in the region and in the world.
It aspires to achieve its mission by satisfying the customers' wants with the quality and competitive products and services that it has to offer. Pemmican believes that excellence begins with each individual, which is the catalyst of what they are ongoing. With the above mission in mind, Pemmican is committed to reach a world-class operation through their corporate philosophies and values. Pemmican's corporate philosophies then were to always think of the Customer, Quality, Excellence, Shareholders, Employees, Services and Safety.
The corporate values that LEADERSHIP Oral CHAngE Marriageable: A CASE STUDY OF Pemmican 119 they want to be inculcated in each and every employee are Sincerity, Trust, Openness, Realization and Interdependence. Under Color and the leadership of Mr.. Adam, the sense of responsibility and ownership (or empowerment) within most of he organizational members was lacking. They need to be instructed and pushed before they started to act on arising issues. This was strengthened by the view of the Assistant Manager (Industrial Engineering), Mr.. Ihram, when he mentioned that people were more reactive then, rather than proactive.
The monthly performance report to Color was very simple. The Factory Controller, Ms. Lima, explained: "under Color, we did not prepare the monthly report in detail. The moment the top management sees the bottom line is good, that's it! Everybody is happy. " The Manager (Accounting), Ms. Anita, shared similar views when she indicated: under Color, if you are not able to complete your report in the time period specified, it is still permissible for you to extend the submission to a few days later, or delay the submission and things like that! In addition, it is normal for the Finance department to be held responsible and Lima: "Last time, if anything goes wrong, they will say "Finance! ". Since Costing is also under Finance, hence, they said, "you have to tell me why? " Anything that goes into [their departmental] costs, [they] will come back and ask me why. " Pemmican, under Color used to prepare not Just the one upcoming-year budget but also the next five years' budget, thus, the figures for the five-year budget were sometimes simply put rather than going through a process of deep thinking and justification. In other words, accuracy was not so much emphasized under Color.
In terms of performance, under Color, the management regarded it as good performance if Pemmican could achieve 90% of what was required by the budget. Achieving a 100% performance was regarded as very good performance. As indicated by the Factory Controller, Ms. Lima: 120 "Previously, our culture [is such that to be able to achieve] 93% is [considered] good! Hit 100%, [is considered] very good! " The plant operates twenty-four hours a day, seven days a week and an average of 345 days in a year. The operatives are trained such that they are multi-skilled so that they can perform various production processes as and when required.
This is made possible by running two unique shift systems called the Brazilian Shift System and the Rota Shift System. The employees worked together and regarded the factory as their second home. Teamwork was never a problem for the people at Pemmican, as indicated by Ms. Lima when she said: "Of course, our people here, the good thing in Pemmican is, teamwork. Although, I'm from a different race, they give me good cooperation and teamwork. " Even though Pemmican was a small business under Color, it was considered as one of the best model plants and had contributed to the high profits of Color.
Hence, even during economic recession, the employees were given lucrative bonuses, as explained by one of Pemmican's managers: "We are only a small business in Color. And yet we were seen as one of the best models at the time. During recession, we heard of electronics plants being closed down here and there. We, however, were enjoying three, four months bonus during that time. " Acquisition by NOVA EurOPE international corporation The acquisition of Pemmican took place following two major events that had a huge impact upon its operation.
With the liberalizing of the Malaysian economy and the opening up of felt that they had to find a business partner to sustain the existence of Pemmican. Moreover, their Japanese counterpart, who had been providing the technical assistance for Pemmican, had been LEADERSHIP Oral CHAngE Marriageable: A CASE STUDY OF Pemmican 121 bought over by Pemmican's competitor. Thus, the Technical Cooperative Agreement was terminated in late 2001. In 2001, Color went into a technical agreement contract with nova, one of the world's leading automotive industry suppliers. Nova was established in Europe in the late 19th century.
It is an international conglomerate with nearly 90,000 employees working at more than 100 locations in 30 countries. Subsequently, 30% of Pemmican was divested to nova. In 2003, nova increased their interest in the Joint venture to 51% and, subsequently, to 70% in 2005 in order to strengthen their position. For nova, the Joint venture will put them in a sections to close the regional gap in its global production activities in Southeast Asia. They have a more solid production and sales base, which will make the Sean and Australian markets accessible to them and, therefore, increase their market share.
With annual sales of more than 30 million units of its products, the region is said to have more than twice the market volume of China. The strategic alliance augurs well for Color since the corporation is expected to benefit from nova's product technology, which will further enhance Malaysia's competitiveness in the Sean region and other markets. At the same time, the Joint venture will also benefit from the production and marketing of one of the world's top brand names in the kind of products manufactured. Nova will have access to Sloop's product dealer network in Malaysia, which is one of the largest in the country.
LifE with NOVA Value creation is a central management philosophy in Nova. All employees are encouraged to understand the added value they have created in their day-to-day actions. In this way, all employees need to think and act as entrepreneurs. This concept is also very much stressed by the Manager (Accounting), Ms. Anita when she said: "nova is very specific. Nova has a management style that requires individual responsibility and they delegate the responsibility downwards. For instance, you can be a clerk 122 but you have got a certain responsibility.
Previously, a clerk would process all the invoices, and, hence, checked by the supervisor and released. Another executive would have a look and then sign off. Now, under nova, once the clerk goes in, it's that everything is in order. K? Hence, the burden is going down! " The management is also attentive of the development of corporate spirit, focusing on he culture of high performance, striving for the best, cooperation, responsibility and learning and knowledge management. Employees at nova are required to take full responsibility for their actions and performance.
Employees are expected to welcome constructive criticism, honor suggestions from other stakeholders, and be innovative to achieve performance improvement. Nova managers are expected to foster a cooperative management style that encourages delegation and accountability. Programmer to facilitate the exchange of knowledge and expertise internally, and with their partners outside the corporation are formulated in pursuance of employees' lifelong learning. A new management team, which comprises some members from the old management team, outsiders and expatriates from nova, has been set up to manage and run the plant operations at Pemmican.
Mr.. Adam, the head of production, was promoted to be the plant manager. However, during the first two years after their partial takeover, nova did not implement many changes to Pemmican. Nova's management sent over their people to visit the plant in order to study and understand how works are done at the plant. Pemmican's productivity level, in terms of output per employee, was below nova standards. A higher radioactivity level was expected. Ms. Anita as the Manager (Accounting) highlighted: "For nova everything must be the same. If it's a plant, the way you calculate, the way you define things must be the same as their other plants. The Senior Manager (Quality Assurance), Ms. Freddie added: LEADERSHIP Oral CHAngE Marriageable: A CASE STUDY OF Pemmican 123 "nova is very tight in terms of manpower. Pemmican's has been cut tremendously to ensure that if this is the level that you are producing, hence, this is the level of manning that you should be having. " Asian Case Rest. J. 2012. 16:115-132. Downloaded from www. Worcestershire. Mom by Consequently, in 2005, with the majority stake of 70% of Pemmican, nova decided to reduce the number of employees and intensively implement various changes to improve productivity and contain costs. Nova philosophy, I. . , high performance culture, value creation, quality without compromise and effective communication were to be adopted and integrated by Pemmican's management. Integration into NOVA global OrgANizAtiON The integration of Pemmican into nova of new procedures and processes in almost all areas in Pemmican. One of the reasons for the restructuring is to align the organization according to the type of Truckee that nova has for all its subsidiaries all over the world. The second reason for the restructuring is to break down the high levels of bureaucracy and hierarchies that Pemmican used to have under Color.
This is also one of the ways to achieve the corporate spirit of having a good cooperation between all the employees. As the Senior Manager (Production), Mr.. Solely responded: "now [under nova], we have a flatter organization! Under Color our organizational structure was more like a pyramid, but now, we are going towards a flatter organization. That is one other thing that we have introduced. Ender nova, it's not advisable to create layers. " Thus, Pemmican has to implement new administrative and reporting procedures, budgeting processes, information system and performance evaluation systems.
In terms of the report, nova expected a very detailed one as Ms. Lima, the Factory Controller indicated: 124 "nova compares every single figure. For example, if you take your conversion costs. You need to extract out and show as a separate item the repair/maintenance costs. They want you to show the movement of your repair/ maintenance costs every month... Per standard product. They want you to show your energy costs every onto. They want you to show your freight costs every single detail. They compare. And by improving all these costs, then only you can see your costs reduced.
This we have never done before [under Color]. " Asian Case Rest. J. 2012. 16:115-132. Downloaded from www. Worcestershire. Com by 60. 50. 234. 3 on 07/30/13. For personal use only. In addition, the report will need to be submitted on time, without fail, as the Manager (Accounting), Ms. Anita mentioned: "They want the information, timely! So they have a certain guideline as to when the reporting is supposed to be done and it's fixed, per ay, per month, per time!!! Thus, if nova requires it by twelve noon European time, then that's the time you've got to submit... By hook or by crook! Eve got to get it done! " Moreover, nova introduced new product specifications, new product recipes, new machinery and technology and imposed higher quality and production standards. Practically, these changes have an impact on all aspects of Pemmican, from the work- culture to the specifications of the products manufactured. All these together have created a lot of changes, which, simultaneously, has created a lot of stress at Pemmican, as noted by Mr.. Adam: "Honestly, people are flexible. But, at the moment, maybe there are too many things and changes all at once.
It seems they are at a loss. The new product to be introduced. And then we have the new system that we have to follow. So, it is a little bit chaotic. " Since 2003, when nova held the majority share, Pemmican has undergone several restructuring exercises. The final organizational structure implemented in Pemmican resulted in people moving to different sections or having new responsibilities. The restructuring was done to comply with nova's requirement, which standardized the organizational LEADERSHIP Oral CHAngE Marriageable: A CASE STUDY OF Pemmican 125 structure of its plants worldwide.
The previous pyramidal, hierarchical and bureaucratic type of structure in Pemmican was replaced with a leaner and flatter structure to promote better and effective communication flows in the organization. Since plants within nova are not allowed to handle direct sales to the end customers or retailers, the marketing and sales functions of Pemmican are now handled by a separate marketing arm, which is another separate company. Thus, the sales and marketing staff of Pemmican have been either absorbed by this marketing arm or eve opted to leave the company.
The focus on Pemmican is now totally on production, as explained by Mr.. Adam "nova will send their team to Pemmican to study the plant capability, prices and whatsoever! Then they will propose a certain amount that we have to produce. However, prior to that, we have to propose to them also what is our intention for next year, based on our capacity. Thus, based on that, there is some negotiation". Several departments were affected by the re-structuring exercise. The Finance Department has been split into two different departments, I. . Accounting Department and Controlling Department. The Technical Department has been segregated into Product Industrialization (P') and Quality Management (KM) departments. The Production Department, which was previously separated into two production areas, has been merged into one production area, headed by the Head of Production Department. Pemmican also placed two expatriates from nova in Quality Management and Plant Operations so that they are able to manage both quality and plant operations according to nova standards. Ova has a very strict standard. If the required quality level is not achieved, then the whole production batch will be rejected. Thus, there is a need for Pemmican's management to ensure that they produce good quality products. Due to the re-structuring, downsizing and re- shuffling exercises, many employees, especially those at the management level need to transfer to different sections or newly created departments. Many meetings were developed according to nova Corporation's meeting structure.
The meetings are held often, as often as daily, weekly or monthly, but are usually short, between half-hour to one hour at the most. Among the meetings are the Quarterly Operations Review Meeting, Monthly Management Meeting, the Daily Factory Operations Meeting (FOAM), he daily business team meeting, the shift coordination meeting (twice per shift per day) and roll call for every shift. Another change that had a huge impact in Pemmican was the reduction in the number of employees through the voluntary separation scheme (VS.), which was offered between 2004 and 2005.
More than 100 employees took the VS., including a number of long-serving skilled supervisors and senior supervisors. Consequently, some sections in the production department were crippled because they did not have enough skilled staff to manage and operate the section. To ensure smooth running of the factory, Adam had to negotiate with some f the skilled employees who took the VS. to stay for a few months to train the remaining employees so that they could do the required tasks.
To fill the vacancies, some senior operators were promoted to the supervisory level. From managing four or five different machines and small production sections, they were now responsible for twenty machines and more people. Adam realized that some of them were not capable of managing a bigger section of probably twenty machines and more people. Furthermore, they did not have the required supervisory skills. Nova closely monitors the operations and performance of Pemmican. Detailed monthly reports need to be submitted to nova. Ova implemented strict cost control whereby they compare and contrast every single figure of the current month with that of the previous month. Previously, the reports submitted to Color were not comprehensive. Color was satisfied as long as Pemmican's bottom-line was higher than expected. However, the bottom-line is not the only important information that the current management monitors. According to the factory controller, "... Nova goes for every single detail. " Adam found that gaining acceptance to all these new changes, even at the management level, is not easy.
Cite this Page
Leadership and Change Management: a Case Study of Pemancar. (2018, Aug 24). Retrieved from https://phdessay.com/leadership-and-change-management-a-case-study-of-pemancar/
Run a free check or have your essay done for you
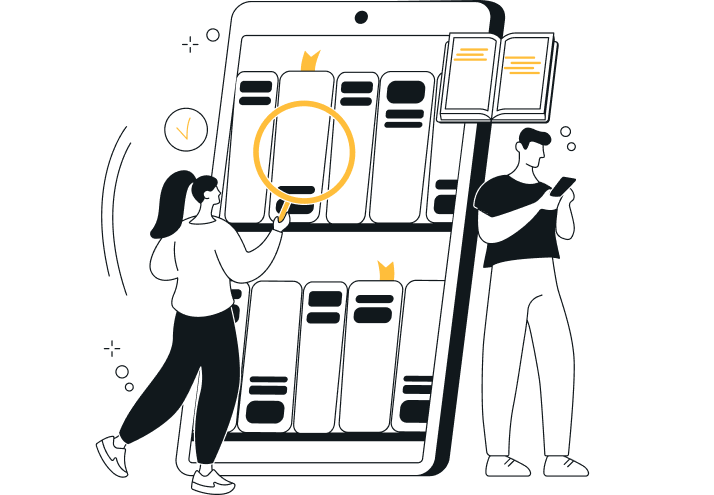