Essay On Job Costing
It is form of specific order costing where an individual job is taken and done as per customer’s special requirements an each order is of comparatively short duration. S the job moves through the various production operations, it is continuously identifiable. The cost of each order produced for a customer or he cost of each lot to be placed in stock is recorded on a job order cost sheet. Each cost sheet is designed to collect the direct and indirect cost charged to a specific job, and each has a job number which is entered on all documents relating to the job e. g. materials issued, labor hours worked, overhead items charged etc.
the indirect factory cost (overheads) charged to a job are usually estimates rather than the actual costs incurred. Estimated overheads charged = OAR ? Activity level for a job. Batch costing This is another form of specific order costing which is very similar to job costing. Within each batch are identical units but each batch will be different and with a separately identifiable cost unit which is given a batch number just as a job number in job costing. Costs are then identified against each batch number to ensure that they are charged to the correct batch. The individual cost of each unit in a batch is determined thus;
Cost per unit in batch = Total production cost of batch (W. N. Funnel, 1996) Number of units in batch This costing method is widely applicable in engineering component industry, footwear and clothing manufacturing industries. The individual selling prices of the batch is arrived at by adding a profit element to the cost of the batch. Process costing This is costing method applicable production is of mass type, and the products involved are many and identical e. g. production of bottled beer. Average cost per unit is calculated for each process; Average cost per unit = costs of production
Order custom essay Essay On Job Costing with free plagiarism report
Expected/normal output In this type of costing, the output of on process forms part of the input of the next process, and the opening Wok in Progress (WIP) is the closing WIP of the previous period. Uniform costing This method of costing is not described as a costing system as such because it’s based on compromise. In this method, an organization adopts an agreed method of costing for all their products. ii. Issues to be considered when setting selling prices Before a firm sets up selling prices for its products, it considers quite a number of issues. Market competition is one of them.
It is usually an important factor to lay basis on given that many firms are normally in competitive industries as opposed to the monopolistic ones. Pricing model which is ruling in the market can also determine some overhead costs to an extent. For example, advertising costs may be high or low depending on prevailing selling prices. When in a oil business for example, advertising costs will be lower when the price fixed by a firm is similar to those of the other players in the market. This is because similar prices will always attract any customers just like those one of the competitor, hence advertising might not be that necessary.
The other factor which ought to be considered too is the return on capital employed. It is highly applicable in specific costing system where the job undertaken might call for additional equipment or raw materials over and above what the firm has invested in for normal productions. Under such circumstances, the firm can peg some targets to do with the required rate of return, or return on capital. It can use either return on investment, or residual income method of appraisal. Such a condition will call for a proper consideration of the selling price to be chosen.
Break Even Point (BEP) is a point where neither profits nor losses are met. This is a very crucial point for a firm in making several decisions including setting of a selling price. The lower the BEP the lesser the units needed for the firm to sell to attain a profit, and vice versa. The price which will be charged by the firm also determines their Margin of Safety. These are the units which need to be produced and sold to attain a profit level. The determination of both the BEP and the Margin of Safety takes into account both fixed and variable costs of a product, i. e. the full cost.
The close link between the BEP and the selling price is that the selling price is that the higher the selling price, the higher will be the BEP, and this necessitates for higher chances of making losses. To be considered too before a price is fixed I the demand and its variations. Demand dictates he maximum number of units of a product that can be produced and sold within a given time frame. Demand greatly affects the determination of the selling price because such a selling price also determines the quantity to be sold in the market especially in a competitive scenario.
There are some products of some firms which can be sold before the complete their production cycle. For example, in paper milling industry, some papers may be sellable as plain papers for printing, or alternatively wait to be ruled and be sold as foolscaps. In such cases, a ‘sell or continue processing’ decision has to be made. Selling price to be fixed will depend on full costs incurred up to the point of making the decision, or those incurred for the entire completion of the process. This clearly indicates that such a point of decision or possible causes of alternatives is a major factor to consider before pricing is made.
Nature of special offers accepted is also other factors to consider before a pricing decision is arrived at. The availability o spare capacities, or marginal costs incurred to make such a capacity available, are important components of ascertaining full costs of the offer, which will directly affect the selling price of the product concerned. iii. ABC and Conventional costing methods analyzed Activity Based Costing (ABC) is a method of charging overheads to cost units on the basis of benefits received from the particular indirect activity e. g. ordering, planning, setting, etc.
it attributes overheads to products costs on a more realistic basis than simply production volume and at the same time attempts to show the relationship between the overhead costs and the activities that cause them. (Hicks, 2002) The conventional costing system is an old method of costing which dealt with product costing in the typical factory scenario which existed then. These systems were characterized by high proportion of direct costs in total costs, relatively small number of support functions, low mechanization levels, and small rate of change of both product and methods.
(Emblemsvag, 2003) The key differences between ABC and traditional systems is the way that the costs of support activities are collected and then charged or traced to cost units. (Yu-Lee, 2001) In traditional product costing, costs are classified as variable and fixed. The fixed costs are then treated as product costs and all the non-production costs (variable costs) written off as they are incurred. ABC classifies costs s short-term variable costs, long term variable costs, and fixed costs.
Short-term variable costs are costs which do vary with the activity levels and are classified as variable costs under the old method of costing. These costs are traced to products under ABC using production volume related cost drivers e. g. direct labor hours to the, machine hours, direct material cost, or weight. The proportion of these costs to the total costs is very negligible in many organizations. (Pizzey, 1989) Long term variable costs are costs which do not vary with production levels but vary with other factors usually after a long period.
Examples are stock holding costs, production scheduling, set-ups cost, etc. They are fixed in the short run but vary in the longer term because of range in and complexity of product manufactured. ABC traces these costs to products based on the transaction-based cost drivers. Most of these costs are classified as fixed costs in the traditional system. Fixed costs are those which do not vary for a given period of time with any activity indicator. Example is the salary of the Managing Director. Under ABC, such costs normally carry a relatively small proportion of the total cost.
Cite this Page
Essay On Job Costing. (2018, May 25). Retrieved from https://phdessay.com/job-costing/
Run a free check or have your essay done for you
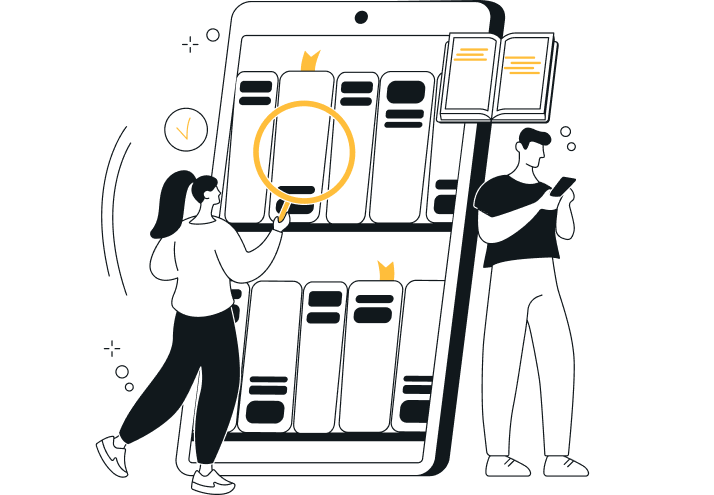