Investigation Into Waste Management on Construction Sites
Abstract
This study aims to report investigation into the problem of waste management on construction sites in South Western Nigeria and to unveil inherent dangers material wastage poses to the construction Industry. In the construction industries, materials are very vital in building sites, but not all the materials delivered are used for the purposes for which they have been ordered and the subsequent disappearance of these materials constitutes part of the waste.
The primary research instruments used was the questionnaire which contained varied questions on material wastage and management. The investigation revealed that material wastage brings about additional cost to the construction project as well as a reduction in the profit of the contractor, considering the cost of storing and transporting construction waste along with the loss of revenue from not reclaiming waste. Also, most waste that occurs at construction sites is due to poor management and lack of awareness of effective waste management.
Order custom essay Investigation Into Waste Management on Construction Sites with free plagiarism report
The study finally recommends that recycling and reusing of construction waste is a viable option in construction waste management and that material wastage can be reduced by giving incentives to the workers for better handling of materials and by having trained personals to supervise the works.
Key words: Construction Waste, Waste Recycling, Waste Reusing
Introduction
Inadequacies of the materials such that at the end not all the materials procured and delivered to sites are used for the purposes for which they are ordered. This excessive loss in materials is what is called Waste[4].
Material wastage is any extra cost over and above the materials used, plus their handling as contained in the estimated price for the job[5,6]. Building Research Establishment[7] divides material wastage into four distinct categories namely design waste, taking off and ordering waste, supply waste and finally, contract waste. This study will help to determine. Effective waste management is of growing significance for the construction industry. Adding the cost of storing and transporting construction waste, along with the loss of revenue from not reclaiming waste materials, it makes financial sense for onstruction companies take action to minimize waste. The use of recycled aggregate derived from concrete rubble in the production of ready mixed concrete was demonstrated in the example of an office building, erected in Darmstadt, Germany[1]. Generally, the economic interest in re-using or recycling building materials is governed by three factors listed below[2, 3]:
The availability and thus the cost of natural or new building materials. The availability of disposal space, the tipping charges and the taxes for dumping. The transportation cost. The inherent dangers material waste poses to the onstruction industry. Ways of minimizing waste on construction sites. Ways of keeping proper site records for accountability purposes. Finally, recommendations were made on effective waste management on construction sites. The significance of the Research: In the past, most especially in some parts of Nigeria, practices to reduce, reuse or recycle waste did not achieve widespread implementation for a number of reasons. Firstly, people were not aware of benefits of minimizing waste, nor had any experience of reusing recycled or reclaimed materials. In addition some even believed that the cost f reusing or recycling these wastes was prohibitive. Materials, as one of the resources employed by the construction industry, pass through a number of processes before they are finally incorporated in the construction. These processes bring about the 980 American J. Applied Sci. , 2 (5): 980-984, 2005 This research is meant to reveal various losses arising from material wastage and to propose measures that will enhance the judicious use of clients' money coupled with an overall effect on cost savings on a construction project, as well as lead to increase profit and time saving on the construction period.
It will also serve as a form of enlightenment to the general populace particularly those in the construction industry.
Materials and Methods
This research relies on primary data, which was btained using questionnaires having both closed and open-ended (un coded) questions; containing varied questions on material wastage and management. It was directed at the respondents relevant to the study including engineers, architects, quantity surveyors, builders and contractors to identify the various sources of waste encountered on construction sites and how these wastes can be minimized and managed. The data obtained were analyzed using tables and statistical indices. The scope of this research is limited to firms in Lagos, Oyo, Ogun, Ekiti and Ondo States. Lagos is considered to be the nerve of commercial activities in
Nigeria and so the relative volume of construction work there is very high. Other states were chosen to complement that of Lagos. Furthermore, a sizeable number of all firms chosen to constitute the sample for this research were undertaken one form of construction or the other in different states of the country, therefore information gathered can be broadly applied to the entire nation.
Results
Inventory Tools: This aspect shows the importance of materials in building projects and also highlights the need for their effective management and control. Table 1 shows the percentage cost of materials to the total cost of the project. The table shows that 66% of the respondents quoted that the percentage cost of materials to the cost of the project is above 50%, closely followed by 22% who believed that the percentage cost of materials to the cost of the project is between 41and 50%.
Also, it can be observed from Table 2 that a sizeable number of firms did not respond to the method used for keeping store records, while 21% indicated that use of a stock card system is the best, 10% believed that the bin card system is the best. Furthermore 10% believed in the use of daily stocktaking, 13% expressed confidence in the use of the log book. On responses on the sources of waste, 40% of the firms agreed that the major source of waste was due to the adoption of a storage system; this was closely followed by 38% of the firms who agreed that the major source of waste was due to transport and delivery to site.
Other sources were also given and the results are presented in Table 3. Other sources of waste pointed out by the respondent but not shown in Table 3 include residual wastes, overestimation of quantities required and the use of unskilled laborers. As for the incentives for good handling and minimum waste, 41% of the firms agreed that there were incentives for good handling and minimum waste while 59% suggested that there were no incentives. The incentives identified by the firms are listed in Table 4. Also, Table 5 presented methods of minimizing waste on sites. Other methods of minimizing wastes on sites roposed by some firms are given in Table 6. Material Utilization: The section presents the methods used by firms to minimize waste on sites, sources of wastes and incentives for good handling and minimum waste. It also considered various means of reusing and recycling wastes on construction sites. Materials Stock Control and Storage: This section gives an analysis of the data collected on material stock control and storage before its movement to the site for utilization. 981 American J. Applied Sci. , 2 (5): 980-984, 2005
Incentives for good handling and minimum waste
- Commendation of hardworking and careful workers in kind and in cash
- Supervision and effective monitoring are experts.
- Giving bonus to workers.
- Regular payment of worker's salary as time due and provision of medical care for workers in case of accident
- Increasing salary when deemed fit.
- Promoting good handlers.
- Using the right specifications.
- Approving more overtime hours.
- Good design, detailing and erection practice all lead to waste minimization, these should be rewarded periodically in cash or kind.
- Avoid overloading trucks.
Material Purchase and Delivery: On the origin of materials supplied to site, 70% of the respondents obtained their materials direct from the suppliers, while 39% usually contracted the supply out. Others (24%) purchase before use and store it central store. The results are presented in Table 8. Concerning the time of placing an order of materials prior to use, responses showed that 32% of the firms placed their orders less than two weeks before they were required, 27% placed theirs between three and four weeks while the remaining 41% usually placed immediately stock becomes less.
Meanwhile, on responsibility for damaged materials in transit, the majority of the firms claimed that the suppliers were liable; they held the opinion that the materials were still in possession of the suppliers as long as they had not arrived on site. However, a minority of firms, about 11% had a different opinion.
- Monitoring the supply of materials and goods to prevent damages.
- Close supervision and monitoring by experts.
- Provision of both day and night security. Effective planning before the commencement of any project.
- Materials should be supplied to specifications and detailed drawings should be followed to the letter.
- Conversion of wasted materials to other use.
- Introducing incentives to make workers happy
- Ensuring adequate storage facility for construction materials on site.
Other equipment indicated by the respondents included concrete mixers, loaders, excavators, head pains, shovels, diggers, vibrators and tipper lorries. Meanwhile, the question on whether fragile materials should be given special attention and handling or not, 59% of the respondents opined that special attention and handling was paid to these materials, while 18% of the firms surveyed indicated that no such care was essential. The remaining 23% of the firm surveyed did not give any response, some of the methods (suggested by the respondents) of storing and handling fragile materials.
On material storage system, 51% of the firms used a centralized system of storage, while 25% used a mixed procedure, that is, the combination of the centralized and decentralized systems. On methods used in material stocktaking, most firms used a periodic stock checking procedure, about 85%, while the remaining 15% used perpetual inventory that is, continuous stock checking.
- Fragile materials should be stored separately
- Supervision and handling of materials should be done by experts Materials should be stacked on pallets, with little or no access
- Fragile materials should be packed amongst saw dust
- Stack such materials between shock absorbing materials
- Careful offloading during delivery
- Materials should be stored in special packs during transporting to prevent damage.
- Materials should be stored away from point of heavy traffic, passer-by’s and workers.
- Adhere to the manufacturer’s instructions.
- Allow only single handling.
- Store in central store and carry directly to the site when needed.
Cost of materials when compared to the total cost of the project may well be over 50%, hence aterials should be judiciously utilized and handled. Manual labor is more extensively employed in most of the construction firms surveyed than the use of mechanized labor. The major sources of waste that was revealed was due to improper site storage, although a high proportion of firm surveyed also believed that the transportation and delivery of materials to the site were important considerations as well. Giving incentives to workers for good handling of materials greatly minimizes waste on construction sites as well as trying to make the workers have a sense of belonging in the firm.
Discussion
If materials handling and control are to mean anything, high control needs to be exercised between the parties involved. Mechanization of the movement of materials on the construction sites offer advantages in both cost and time saving, but from the present study, manual labor is far more extensively used in comparison to plants. Usage of manual labor for materials handling increases the level of waste that occur on sites and this can be readily observed at construction sites from the way materials litter such areas.
If was observed from the study that some construction companies do not give special attention to the handling of their fragile materials, whereas in developed countries such items are treated with care because they are liable to damage quite easily[6]. The supervision of fragile materials is to be done by experts and only single handling should be allowed. More so, some of the firms studied are not in the habit of giving incentives for good handling and minimum waste of materials, this ought not be in if incentives are given to the workers, they will feel more responsible for the materials and they will take extra are in handling such items. Finally, from the research, it is obvious that nearly all construction firms in Nigeria are yet to start recycling or reusing waste materials on site. Giving contractors the option of reusing or recycling waste will determine the economic feasibility of such operations.
Construction waste recycling and reusing is a viable option in construction waste management and from further studies or research, laboratory experiments can be performed on some construction wastes like broken aggregates or demolished concrete to establish the feasibility of this option[8]. It would be worthwhile extending the nvestigation to other building materials like timber, iron-mangery, broken glass, sanitary wares and similar items. The use of computers should be adapted for storing records on construction sites and for construction planning. There should be awareness programs for all construction companies on construction waste management through reuse and recycling. Also formal education should be given to storekeepers and the foremen on effective materials handling and systems. The federal government should come up with a policy on construction waste management which may include introduction of heavy tipping charges n construction wastes (particularly those that can be reused or recycled) and taxes for dumping or disposing wastes carelessly. This research is focused on the construction industry in terms of waste utilization and management. However, the methodology adopted here could similarly be extended to other fields in the context of engineering.
References
- Grubl, P. and A. A. Nealen, 1998. Construction of an office building made from recycled demolition material. Contribution to International Symposium Sustainable Construction: Use of RecycledConcrete Aggregate. University of Dundee, Concrete Technology Unit, London. American J. Applied Sci. , 2 (5): 980-984, 2005 2. 3. 4. 5.
- Illingworth, J. R. and K. Thain, 1988. Handling of materials on site. CIRIA Special Publication No. 57 Service Paper No. 92, London.
- Watts, J. W. , 1980. The supervision of construction. 1st Edn. , Batsford Academic and Education Limited, Fitzhardinge street, London, pp: 37.
- Tiffin, P. J. R. , 1997. The organization of building sites. Seminar Paper Presented at Birmingham Centre Hotel, New Street, Birmingham, England, pp: 2.
- Hansen, T. C. , 1992. Recycling of demolished oncrete and masonry. First edition E and FN Spon Publishers, 316 Pages, London.
- Illingworth, J. R. and K. Thain, 1988. Materials management- is it worth it? CIRIA Special Publication No. 58, London. Sheeduzzafar and A. Khan, 1984. Recycled concrete- a source of new aggregate. Cement, Concrete and Aggregates (ASTM), USA, 6: 17-27.
- Grubl, P. , 1997. Die Erstellung von Bauwerken unter Verwendung von industriell gefertigtem Beton mit rezykliertem Zuschlag (Creation of Buildings with Industrially made Concrete Containing Recycled Aggregate). 18. Darmstadter Massivbau. Seminar, Vol: 18.
Cite this Page
Investigation Into Waste Management on Construction Sites. (2017, Feb 01). Retrieved from https://phdessay.com/investigation-into-waste-management-on-construction-sites-in-south-western-nigeria/
Run a free check or have your essay done for you
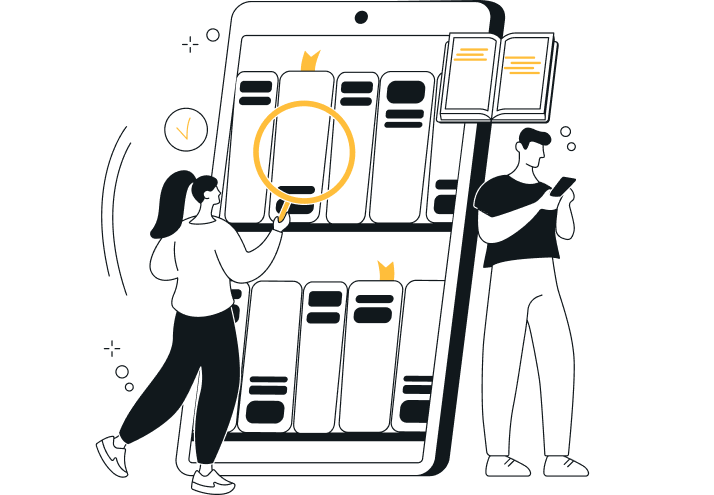