Health and safety issue for contractor company in oil and gas industry
Abstract:
Exploration and production of petroleum is highly profitable sector, but on the other hand, it is very risky business. Catastrophe in refineries and oil rigs like Mexico II (1983) in the Gulf of Mexico, Pipe Alpha, has totally changed the script of safety procedure and risk assessment. It is evident from the past history, 65 % of disasters resulted due to Human Organizational error. That’s why it is highly recommended to the oil operating and contractor companies to identify the risk, potential hazard and consequence of hazardous incident.
Health and safety measure are always seems to be an overburden for project, but in reality they are preventing the tragic accident which would be result in damage of assets, loss of valuable human lives, demoralization of team and hazardous environmental impact. In last 35 years of North Sea, average yearly accidental cost is 200M (except in 1988-1989 cost ?1200 M due to Piper Alpha) and loss of 485 precious human lives . In this report, we will try to discuss the critical issues of health and safety faced by a contractor company in oil industries. Furthermore, we will try to show what was done wrong in past and will try to suggest how similar incident might be prevented in the future.
Order custom essay Health and safety issue for contractor company in oil and gas industry with free plagiarism report
Discussion:
“Nation have passed away and left no traces, Any history gives the naked cause of it – one single simple reason in all cases; they fell because their people were not fit.”Rudyard Kipling.
Unfortunately, the history of the oil and process industry indicates that a lot of incidents are repeated after a lapse of a few years .Because people move and lesson are forgotten. Accidents caused during the following activities are very common, many of them are not resulted in death, serious injury or serious damage – they were near-miss. But they could have had much more serious consequence. We will discuss few of them in detail.
- Isolation of Equipment.
- Accident caused by Human Error
- Entry to Vessel
- Liquefied Flammable gases
- Modification
- Storage Tanks
- Stacks
- Leaks
- Pipe and Vessel Failure
- Hazard of Common Material
- I don’t know that (Like Ammonia can explode, Hydraulic pressure can be hazardous, Diesel engines can ignite leaks.
1. Isolation of Equipment:
Case I:
Three people were killed and the plant was destroyed during a pump repair. Dismantling was done to repair the pump. When the cover was removed, hot oil, which is above its ignition temperature, came out and caught fire.
From several days, a pump was waiting for repair work and work permit was issued. On the day of accident, the foreman who issued the permit should check the drain valve should be opened and suction & delivery valves were shut. But suction valve was opened and drain valve was closed by someone. Maintenance team only intend to change the pump bearing and they decide to open the pump and inform the process team but no further checks and isolation was done.
It is not habitual in company concerned to isolate the equipment under repair by slip plate, only by close valves. Similarly, failure in permit to work procedure was the major reason for the disasters of Piper Alpha.
Recommendations:
Permit to work will be withdrawal and new one is issued, if there is any change in the nature of work.
Isolation of equipment must be done when it is under repair.
Bleed valve and double blocks must be installed, where fluid at having gauge pressure above 600 psi or temperature above or near auto-ignition point.
2. Accident caused by Human Error:
Case I: (Warning Ignored)
During the working shift, it had been noticed by the operator that the level of fluid in tank is falling rapidly. He informed the instrument department that the level gauge is not working properly. After few hours, when they were changing the gauge, they found that the previous gauge was correct and there was a leaking in the drain valve. But it is quite late and they has been lost 10 ton of material.
Case II: (High Temperature Alarm)
After a modification pump was installed, it was used to transfer some liquid. When the transfer of liquid completed, operator pressed the switch off button, he saw the pump is “running off” light went out.
After a several hours, high temperature alarm of pump sounded. Operator supposed that there was a fault in alarm and he ignored it. Soon afterward, there was a huge explosion in the pump. During the modification of pump, an error in the circuit was introduced and stop button was not working properly.
Recommendations:
Proper training should be given to the operators; they must take a necessary action upon unusual reading.
Always respond to alarm. They might be correct. Training should be emphasis the importance of alarm.
In record sheet, control limit must be defined.
3. Entry to Vessel
Many incident have been happened which killed no of peoples because they entered inside the vessel or any other confined space which had not been thoroughly cleaned or tested.
Case I: (Unauthorized Entry)
Contractors mostly unfamiliar with the operating companies rule, have frequently got into the vessel without authority. A contractor foreman entered in a vessel which was opened and disconnected, setup for entry, but it was not yet tested. The foreman was estimating the cost of cleaning, he supposed that there was no need of permit for entering the tank just for inspection and got affected by the gas.
Similarly an incident happened during the lunch time, a process foreman was taking a last look of vessel before boxed up. There was an old gas mask lying on the floor, he decided to go and remove it. While going inside he slipped from the ladder and fell and was knocked. His tongue blocked his throat and he suffocated.
Case II: (Entry into vessel with Irrespirable Atmosphere)
A contractor entered in the combustion chamber of a gas plant watched by two standby men but without waiting for the breathing apparatus to arrive. He lost consciousness halfway up when he was climbing out of the chamber. He was hanging between the chamber wall and the ladder. Rest of the men could not pull him out with lifeline. One of the men reached to the person without breathing apparatus and he also lost consciousness. Both of them were rescued, but standby man was died by this time.
Case III:
Vessel was generally split up into two halves by a baffle which had to be removed. The vessel was cleaned out, inspected, and a permit issued for a worker to enter the left hand side of the vessel to burn out the baffle. It not possible to see on the right hand side of the vessel but as the left hand side of the vessel was clean and because no combustible gas was detected it was assumed that the other half was also clean. While the welder was in the vessel, some deposited in the right hand half caught fire. The Welder came out side without a sever injury but wounded himself in his rush.
Recommendations:
Vessel should assume to contain hazardous material, if a portion of the vessel can not be tested and it seems to be safe.
Only gas test are not enough. When the vessel will be heated or disturbed it may produce gas which was present in the sludge.
For any addition work inside the vessel, new work permit for confined space should be issued.
People should now put their head inside the vessel unless entry has been authorized.
Manhole should be covered with barrier if the vessel is opened but entry is not yet authorized.
Rescue person should be available at the spot with necessary equipment.
Always use breathing apparatuses before entering the vessel.
Do not relay on contractor reading rule, just follow the safety procedure of operating company.
4. Liquefied Flammable Gases:
Case I: (Fire and exploration at processing plant at Mexico City)
November 1984, there was a worse incident at processing plant (LPG-actually Propane 20 % and Butane 80%) in San Juanico, Mexico. About 542 people were died, 4,248 were injured and 10,000 become homeless.
The main cause was the rupturing of 8 inch line. During investigation it was revelled that the tank was overfilled and the inlet pipeline was overpressure. It is not known why the pressure relief valve was not lifted. The gas was spread in the area of 200m by 150 m before it caught fire. Most of the people got killed and injured are pubic, who were living near the plant.
Recommendations:
There was not gas detector in this area. This should be present.
Plant was at congested place about 160 m away from town. It is recommended that for LPG plant it should be 600 m away from the town.
There was no fire insulation on equipments. Vessels and tank should be fire insulated.
The water deluge system was inadequate.
5. Modification:
Many accidents have happened just because modifications were carried out in plant and these modifications were not fulfilling the safety criteria.
Case I:
A reactor was cooled by a providing of brine to the jacket. There was a repair work in brine system and it was to be shutdown so water from town was used instead. This town water pressure (130 psi gauge pressure) was more than that of brine, so the reactor collapsed.
Before the modification, a modification approval form was approved which had twenty important questions. But this form was filled as a formality.
Recommendations:
Before modification, however inexpensive, temporary or permanent, is made to a plant or process or to a safety procedure, it should be authorized in writing by a manager and an engineer.
They manager and engineering who authorized modification can not be expected to stare the drawing and hope that the consequence will be show up. They must provided with an aid such as a lost of questions to be answered.
The foreman should not be authorized to make any modifications at field work.
We have discussed few of the above critical issues which are very important for a contractor company to work in oil and gas industry. Furthermore, critical issues of a plant are also indicated in logical tree analysis in figure 1.
Conclusion:
The purpose of this report is to indicate the safety issues for a contractor company in oil and gas industries. The purpose of giving the cases and recommendation is to understand what they had done wrong in the past and to advise how similar disaster might be prevented in the future. After reading this report just analysis your plant, are you doing the same wrong thing which people did and resulted in disasters. Development of a safety culture is necessary, culture which would be committed with safety; safe work practise would be encourage and people do insist for safe work for every one, their attitude must be toward safe work practise. Leadership and top management should have to set a meaningful safety program by providing sufficient training and experience. Moreover, communication played a significant role; proper training and safety induction should be given to supervisor level, so that the correct information should be transmitted to them.
Reference:
- The integration of Quantitative Risk Assessment and Reliability centered Maintenance to optimize platform Design and Operations by R.M Marshell, S.T.Maher, P.R. Stevenson & B.C.Morris
Cite this Page
Health and safety issue for contractor company in oil and gas industry. (2019, Apr 06). Retrieved from https://phdessay.com/health-and-safety-issue-for-contractor-company-in-oil-and-gas-industry/
Run a free check or have your essay done for you
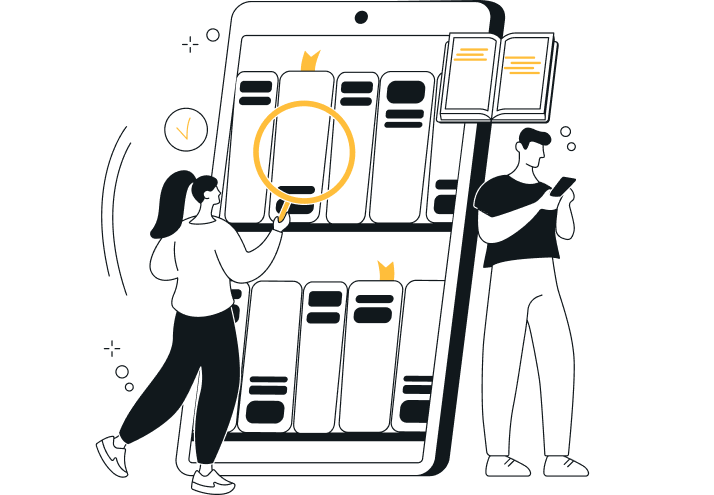