Garments Industry Pakistan Cometitiveness
First of all we would like to thank Almighty Allah.We would also like to thank Ms. Khadija Bari, Zahid Aslam - Managing Director BABRI, Mr. Amir Iqbal- Production manager of UNIBRO Textiles, Mr. Ikhtiar Baig- Federal Advisor to PM of Textile, Mr.
Mushtaq Vora – ex-Chairman APTMA, Mr. Jawed Bilwani – Chairman PHMA, Mr. Zaheeer A. Hussain – CEO Textile City and Mr. Dawood Zakhura – member of central committee PRGMEA for their valuable help in making this report possible. We greatly appreciate the help. Garments Industry: A Global Perspective Textile and Garment can be taken as relatives performing in the same fraternity.
Both industries depend on each other however one main difference between these two sibling industries arises at the very grass root level. Textile is more capital-intensive that is it require huge injections of finance and technology while the garments side is more labor-intensive and depends on human resource making it cheaper of the two options (strictly in the case of developing countries where labor is cheaper than machinery). The market for these two industries is colossal, thanks to the basic human necessity of hiding bare bodies.Global garment exports are valued at $ 310 billion and top 15 clothing exporters account for 80% of the exports. EU is the biggest exporter while China is second biggest exporter. Global Trends in Garments Geographical shift: Till 2004, there was an international treaty called Multi-Fiber Arrangement (MFA) which had placed quota restrictions and textiles and garments manufacturers among WTO members. On January 1 2005, MFA expired and ended restrictions which had been placed for almost four decades.
Order custom essay Garments Industry Pakistan Cometitiveness with free plagiarism report
The main impact of MFA was on the exports from low-cost countries such as India, Pakistan and Bangladesh to regions like EU and US. After the abolition, new doors of business were opened to these low-cost countries and China led the way in grabbing market share internationally. Lean Retailing: In this day and age, those retailers are considered smart retailers who focus on selling the garments only while depending on the suppliers for rest of the supply chain activities and such a retailer is called ‘Lean Retailer’.This has forced to suppliers to offer a complete package to the retailers which include both the upstream and downstream services. Retailers have adopted methods which have eliminating the need for agents and hence, they deal directly with manufacturers who are required by the company to provide a range of other activities than was traditionally expected of them. In some cases, garment manufacturers may even be asked to track the stock of retailers and arrange for replenishment when need be. This might require them to use advanced technologies such as RFID.
This poses a major challenge for Pakistani manufacturers as their know-how is not this advanced that they employ modern technologies to coordinate their activities with huge retailers. Speed-to-market: Like all industries, garments industry too has become very fast. There was a time when retailers placed orders way before the season started. But now with the help of technologies such as RFID and Barcode, they have adopted practices like Just-In-Time inventory. This trend has put a lot of pressure on the suppliers who have to supply goods fast and irregularly.The supply chain must be highly integrated in terms of information and efficiency, while often being geographically highly disintegrated Garments Industry: A Pakistani Perspective Pakistan primarily depends on its Textile Industry to churn majority of revenues earned. Garments industry provides highest value addition in textile sector- increasing revenue internationally.
Pakistan in addition also gets income tax exemption and duty-free imports to further buttress the thriving temperament of local industries. Textile Industry is a darling for Pakistan manufacturers since it demands small units of input in terms of machines, workers and output.Exports in Pakistan comprise of various kinds of garments for men, women, boys such as plain/embroidered/printed dresses, blouses, shirts, skirts, night dresses, track suits, trousers, sub-dresses etc (cotton fabric and synthetic fiber). The garment industry generally operates on a small and unorganized scale. One of the main reasons behind this is the fact that small-scale garment industries become a source of income for myriad number of men and women; facing creative damper due to mobility issues in the northern part of Pakistan.The small units do not usually have modern equipment nor do they require strenuous creative effort. However, like every accounting transactions Garments Industry comes with its share of cons.
Our garments are inferior in quality in comparison with garments from India, Korea, Hong Kong, Taiwan, Philippines and Sri-Lanka and suffer rejection when it comes to competing with high-quality goods. These countries although most definitely of developing fashion have an edge over Pakistan because of their readily available and cheaper human and technological resources.Quite evident is the fact that garment industries require a large labor pool functioning at all times. So even if Pakistan’s labor cost 23 cents/hour higher than all these countries multiply this amount by say 200 hours and you can see that a displeasing amount is being over spent on labor. Pakistan is crippled when it comes to cutting costs as further cost reduction would mean probable low quality products which obviously would strike Pakistan back on its face. Already Pakistan is not a strong player in the international market and further quality regression might jeopardize Pakistan’s entry in the international cloth market.Current Scenario 1) Current scenario of the Garment industry in general 2) Garment Production Vs Yarn production 3) Increased demand for Eco-friendly products 4) Textile Engineering Industry According to the latest global competitiveness report, Pakistan failed to improve significantly on any of the basic determinants of its competitiveness.
It was ranked 104 in institution, 89 in infrastructure, 114 in macroeconomic stability and 118 in basic and higher education. - Rising cost of production - Energy shortage - Weak Global demand - Lack of competitivenessRemained the reasons for the poor performance of the country's biggest export revenue generating sector. Production of cloth Pakistan textile sector is by far the most important sector of the economy contributing 67% to export earnings and engaging 35% of labor force. Due to its unprecedented contribution to Pakistan’s economic institutions, the Textile Industry receives a considerable amount of revenues earned in the form of capital investment. There are hundreds of factories, having high-speed rotary textile printing and processing machines.However, most of the leading units working on high tech machines are owned by big industrial and commercial cartels. These big groups or more infamously known as sharks have taken up ownership and have formed a perverse monopoly.
Their joint threshold becomes the basic hindrance in the way of small companies entering and thriving into this segment of the market. According to the estimates, textile finishing industry is embrace almost 731 units. The weaving and made-up sectors have three different sub-sectors integrated, independent weaving units and power loom sector.Cloth is being produced in both mill and non-mill sectors. Pakistan’s fabric range from coarse to super varieties, with coarse and medium varieties consumed locally by those who not wish to or afford to buy high-quality and expensive varieties. The use of colored cotton being unique and attractive has the potential to become a part of cotton fabric and apparel market, but there are some limitations to it. The natural colored cotton is low in yield usually short staple and weaker in strength.
For its impotency colored cotton falls just a mile short from being the hero in Pakistani market.There are a large number of vertically integrated units, where production is controlled from fibre to the end product, and marketed abroad directly. Production of cloth increased at an average of 5% per year from 2004-05 to 2008-09. Out of total production of 1,017 million sq. meters cloth during 2008-09 in mill sector, 57% produced in grey form, 30% dyed and printed, and 13% blended and bleached. |Table 1 : Production of Cloth | |Year |Production (Million. q mtrs.
) | |1999-00 |437. 2 | |2000-01 |490. 2 | |2001-02 |568. 4 | |2002-03 |576. 6 | |2003-04 |683. 4 | |2004-05 |920. 7 | |2005-06 |915.
| |2006-07 |1,012. 9 | |2007-08 |1,016. 4 | |2008-09 |1,071. 0 | | Source: Textile Commissioner’s Organization Government | | of Pakistan. | Import of machinery The production capacity is being utilized to its optimum levels in Pakistan. The country has spent $ 7 billion for the sake of higher value addition and innovation in the textile sector.Import of textile printing and finishing machines saw a decline of around eighty per-cent from 2005- 2010.
Import of textile printing and finishing machinery into Pakistan is given in Table 2 : |Table 2: Import of Textile Finishing Machines | | (Rs. in Million) | |Machines | Export of fabrics per-cent of the total world’s exports is covered by the Textile industries. Such is the importance of this industry as many countries heavily depend on it for foreign exchange and creating employment. It is even more important for many underdeveloped as well as the developing countries which are highly dependent on this sector which holds up to 90 per-cent of their exports and provides employment to up to 50 per-cent of the population By those statistics one can easily understand what major role is the Textile industry playing in helping people prevent poverty and joblessness.Currently Pakistan is in dire need of as many industries as possible to accommodate workers and jobs- This would help in bridging the gap between the various income levels and classes existing at present. Cotton and blended fabrics and synthetic and artificial fabrics, can be safely said to be the two broad categories globally in woven fabrics. Asia is fast emerging as major source of exports, especially of textiles, to the USA, EU and other countries of the world.
Pakistan has emerged as one of the major cotton textile product suppliers in the world market.However, India, Bangladesh and China are giving such a tough competition to Pakistan that our textile products are fast losing their value in the global market. The advantage that these countries have over Pakistan is their low labor cost and better technology. The situation is somewhat tricky for Pakistan which is not in the position of bringing down its labor/energy cost as that would mean compromising on the product quality- the country for sure is not in the position to afford anymore bad name in the global market. Export of cotton fabrics from Pakistan is given in Table-4. Table 4: Export of Cotton Fabrics | |Year |Quantity |Value |Average | | |(Million sq. meters) |(US$ Million) |($ sq.
Meter) | |1999-00 |1,575 |1,096 |0. 71 | |2000-01 |1,736 |1,035 |0. 0 | |2001-02 |1,957 |1,133 |0. 58 | |2002-03 |2,036 |1,346 |0. 66 | |2003-04 |2,409 |1,711 |0. 71 | |2004-05 |2,399 |1,863 |0. 78 | |2005-06 |2,634 |2,108 |0.
0 | |2006-07 |2,211 |2,026 |0. 90 | |2007-08 |2,035 |2,010 |0. 99 | |2008-09 |1,882 |1,929 |1. 02 | | Source: Export Promotion Bureau, Government of Pakistan. | Major buyers of Pakistani fabric are USA, Belgium, Sri lanka, Spain, Turkey and Bangladesh. Major chunk of Pakistani fabrics’ export comprises of the nprocessed form (which makes up to 40% of the exports)- and this results in low unit value realization. 2.
The yarn makers of Pakistan are at dispute with the downward processors of the country. The government out a quota on the yarn exports from the country; however this restriction has brought no good to the cotton prices which remain being high as ever and the local yarn users are still perplexed about the situation. To add fuel t the fire the petroleum prices have risen up to touch the sky and this situation is doing no good to the already adverse textile industry of Pakistan..As it is the recent inflation and the energy prices have brought down the value of Pakistani products in the eyes of the International buyers. Pakistan’s textile exports in 2007-08 were $10. 59 billion and they dropped down to $9.
95 billion in 2008-09. The obvious reasons for this dip are the political turmoil, more than frequent power outages and the much better performance by the world market. FLIGHT TO BANGLADESH While a number of textile businesses are shifting to Bangladesh, many have already made their move because of the severe cotton crisis here.And by no means it is an unethical or a wrong decision because businesses need to survive and therefore they will make decisions that are beneficial for them. A UNDP report suggests that Bangladesh despite being a non-cotton producer is doing fairly well as compared to Pakistan which is a cotton producer. It lists down a number of reasons for the situation. Labor cost in Bangladesh is way too low than that in Pakistan- being 23 cents/hour in the former country and 41 cents/hour in the latter.
Similarly, energy cost in Pakistan too touches the sky when compared to Bangladesh (6. 2 cents/kwh versus 2 cents/kwh- figures from year 2007). And the disparity between the costs is likely to increase with time- owing to sheer lack of competitiveness. Until Pakistan finds a solution for its high labor and energy costs along with poor exports and low sales, things are likely to remain the same. 3. As people are getting more and more aware of their surrounding environment; they are beginning to prefer products and services that cause least or no harm to the mother earth. This trend of eco-friendly products as moved on to the apparel industry as well.
Import of organic chemicals With time as people realized the negative effects of the synthetic chemicals and dyes, a new trend emerged as everyone shifted to used natural colors and dyes. The shift is due to many advantages of the latter- natural dyes as the name suggests are chemical free thus non-toxic; this makes them highly environmental friendly which makes them comparatively harmless. In addition, the textile industry has also welcomed the usage of renewable resources because of their obvious advantages.The Table below showcases the increasing import of the organic chemicals in Pakistan (over the years): |Table 3: Import of Organic Chemicals | |Year |Value Million US $ | |2006-07 |1,330 | |2007-08 |1,687 | |2008-09 |1,557 | | Source: State Bank of Pakistan. 4. Perhaps one of the most undersized sectors of the country is the Pakistan Textile Engineering Sector. Largely, it serves the cottage industries of the country- that comprise of most of the businesses in the Textile industry of Pakistan.
If the entire Textile industry is broken down we will find that only five per-cent share goes to the large Engineering units, compared to which a huge eight per-cent is comprised of the small industry units and medium units take around fifteen per-cent. And the mentioned five per-cent fall in the public sector.An analysis of all these industrial units show that a small minority of all these businesses have facilities catering to Quality Control of their products and services and very few work according to the Engineering drawings. As per one of the surveys the Textile industry of Pakistan consumes around fifty thousand skilled force in its five hundred units. Despite the current conditions, the industry gets a decent monetary support from the government of Pakistan. And the sector plays some role in xporting products to the neighboring countries (for example Bangladesh and Iran) as well as some other countries like Sri Lanka. One of the major burdens on the Textile Engineering sector is the imposition of heavy taxes in various spheres- be it importing machinery and/or machinery components or buying raw material.
Competition The present Textile Engineering Industry is up against competition from smuggled, undersized components, parts and accessories. Let’s take an example of the second hand machinery- there’s an absolute absence of any sort of check and balance.To add, people are generally competing to get as low prices as possible. Hence the justification of using the machinery and equipments, from China or Taiwan- low quality being accepted and appreciated by people just because they come in low prices. Such an attitude of resorting to cheap prices is giving an abhorrent effect on the global competition. Therefore a revolutionary change in the environment is a much needed step currently to help kick start a much better standard of competition (in terms of serving quality). Application of Porter’s Diamond Model: Factor Conditions:As discussed earlier, Michael Porter, in his diamond model, divided the factor conditions into two subgroups which are the basic and advanced factors.
He suggested that basing competitive advantage solely on basic factors is not sustainable in long term which is exactly the case with the garment industry. We had sufficient basic factors to start this industry at the time of independence but we did not build up those factors to an advanced level and hence face threats in garments sector from other nations. LABOR Garment industry is more of a labor intensive industry in nature and Pakistan as One of the cheapest labors cost per hour as compared to our other competitors like China and Indonesia in this sector. This fact would have provided us with a great competitive edge had the productivity of our worker been not very low. The major issue with labor force in this industry is that it is not skilled. It nullifies the advantage we had in terms of cheap labor since we have to hire more labor or take more hours of work from them due to their low productivity. A little effort has been made on part of government to educate and train these employees to improve the level of skill and productivity of these workers.
Recently, the Knitwear and Sweaters Export Association began a training program for men and women working within the industry to teach basic techniques as well as advanced machine operation. However, such training courses are not generally available, and even this course can train only 30 individuals at a time in an industry that employs more than 100,000. Another problem which confronts manufacturers is the attitude of the labor force. Most manufacturers find that their workers have a "careless" attitude toward the quality of the final product. A little training which is provided is by the company itself.Countries which joined this industry after us are now posing threats to us and one of the reasons for that is their skilled labor. RAW MATERIAL The basic raw material for garments is cotton, silk and wool which are easily available in our country.
Pakistan produces around 8 to 10 per cent of the world's cotton but its share in total world trade for textile and clothing is around 2 per cent in value terms. The nature of our cotton is short and medium staple which is not suitable for the production of better cloth. The cotton, when picked, is put in jute bags which add impurity.This, in extension, affects dying process. The quality of yarn allows us to only produce grey cloth which limits our international market since we cannot perform piece dying on grey cloth. Hence we also import raw material from USA and Egyptian cotton from Egypt. Proper education and government intervention can help improve the quality of raw material which is produced which will expand our international and domestic market and help in the process of competitiveness.
ENVIRONMENTAL FACTORS Environmental factors have also affected the production and competitiveness in the market and export performance as a whole.The National and Provincial Assembly elections, load-shedding, floods and law and order situation are factors which have also contributed significantly to adverse performance of the industry and of exports. MACHINERY Up to date and latest machinery plays key role in efficient productivity in an industry and in extension helping it become competitive in the international market. Although garment industry has been developing since its inception, the indigenous manufacturing of its machinery could not develop along with its growth.Resultantly, the demand for machinery is still entirely met through global imports. We import machinery from Japan, Germany, Switzerland, Belgium and China. It increases our freight cost and fixed cost of production which results in loss of global competitiveness.
Some companies also import machinery and equipment from Faisalabad which is also very old. The machinery which we have in our garment sector is very obsolete. It consumes a lot of fuel and gives a low productivity. This area is rather neglected by the government as compared to the spinning sector which has good machinery.Import of textile machinery in Pakistan registered an impressive growth of 66. 29% in the fiscal year 2004-2005. Taiwan's exports of textile machinery to Pakistan have also seen a substantial increase in recent years.
Moreover, as per the estimates of TAMI (Taiwan Association of Machinery Industry), the export figures on textile machinery from Taiwan to Pakistan in the year 2002-04 placed Pakistan on the 9th position in terms of total value but a very little part of these imports was for garments sector.Value addition is very important in garments to become and remain competitive and latest machinery and equipment plays an important role in this regard. R;D Pakistan spends less than one percent of its total budget on R;D and a very few percentage of this amount is allocated for garments. All the R;D which is done by the government is focused on cost competitiveness rather than improving quality and innovation. A few plans for R;D have been made from the side of government which is there on paper, but due to corruption and lack of interest, these plans could not be implemented.One other reason which keeps companies to research and work on new products is the absence of local demand for such new products. The companies do not come up with new and different products because there is no local demand for it.
As a result of this, we lack innovation which is needed for competitiveness. Land, location, natural resources and labor are some basic factors which are God gifted to us in this sector. But industrial growth and base for competitiveness has hardly been built on these inherited factors.In order to remain competitive, a country has to convert these basic factors into advanced; the ones which are difficult to imitate by other nations. Stock of factors at a point in time is important than the rate at which they are upgraded and deployed and hence development of basic factors into advanced is important. We have however failed to do so throughout 60 years. We had basic resources but we did not convert them into advanced factors.
We did not spend on educating and training our labor which affected the productivity of workforce. Lack of knowledge also harmed the cotton in the picking process.The government also neglected the sector in machinery as well forcing it to operate on obsolete machinery which hinders the efficient production process. R;D is also very minimal due to which we lack innovation. Demand Conditions Local demand holds significance in the process of competitiveness. A sophisticated local demand forces the firms to develop better solutions to consumer problems. On the other hand, global demand does not have a significant impact on fostering innovation and making a firm competitive in the international market.
In the garment industry, the major chunk of demand omes from public sector institutions. In that, household generates the greatest share of demand. But unfortunately, this local garment generated demand is very small and insignificant as compared to the international demand. The country's ready-made garment industry came into its own during the 1970s, and has taken an export stance since that time. Garments export has increased by about 92%, and made-ups, including bedding, increased by about 125% from 2000/01 to 2007/08. These figures once again confirm that Pakistan is increasing its textile exports, particularly in value added products.According to one estimate 70 percent of these units are in the unorganized sector, producing cotton-made articles.
These units do not have modern machinery and use the non-mill made cotton cloth. This may be one of the reasons that the price we fetch for our apparel exports is low compared to other countries. The garment industries start their work upon getting orders from abroad. The final product, after completion is transported to the desired destination. The rejected pieces from these orders are sold locally in places like Zainab Market.People who belong to upper class and upper middle class are reluctant to buy these shirts as they are the rejected products from abroad or they are afraid that buying clothes from such places might make them social outcast as these are the places from where lower middle class and lower class shop for their clothes. Sportswear for the fifa world cup 2010 is exported from Pakistan but people couldn’t buy them locally.
Due to the low quality of cotton that we produce, Pakistan has an image of low priced commodity seller in the international market.Neither the local demand is sophisticated nor does the international market demand us of high quality product causing no pressure to innovate. Avais Mazhar Hussain, the CEO of Angora Textiles, gave a presentation at NIPA to government policy makers on the state of garment industry. Discussing Pakistan’s industry weaknesses, he said, “We cater to the low end of the global market because of skill deficiencies in manufacturing and design, furthermore, we have to contend with poor country image. It’s a desperate situation. The weakest link in our value chain is dyeing and fabric processing.You can’t find a single dyeing technician/Chemist in Pakistan who can dye polyester and pdex (Lycra) satisfactorily.
We have better equipment than China and India. Garment technology is a proper science. India produces industrial scientists in fifteen months flat since they have schools that offer industrial training. In Pakistan, totally clueless people are leading the factories fabric processing facilities. Some of our technicians do not even know how to use hydrogen peroxide. One of the expats, a Spanish gentleman, conducted a study in our factory for me, only 48% of the garments being produced were first time right. 2% is a high rejection rate.
” Strategy, structure & rivalry Structure and nature of the industry is of the monopolistic competition model that we study in micro economics, which implies that there is competition but mainly on the cost cutting side and no one competitor can manipulate the prices of the export. Spinning has always been the major focus of the stakeholders in the textile industry. A major portion of good quality yarn is exported rather than being used in the local industry for value addition and transformation into garments of fabric.This is a structural weakness of our textile industry. Countries like Japan and China import this yarn from us, and are well-flourished & have converted their textile industry into high value-added products and it fetches much higher prices in the international market. These countries do not grow cotton, but they have well-established textile industry because they have invested in modern manufacturing technology as well as in qualified and well-trained work force. Their efficient methods of production have enabled them to overcome the handicap of imported yarn.
Whereas in Pakistan, textile industry continues to suffer due to lack of investment, and well qualified work force, despite having the advantage of cotton and labor. Countries like Japan & China import almost 60 percent of Pakistani yarn. This implies that the organized mill sector has made a shift towards spinning and there was neglection seen in the efforts to develop or modernize the weaving sector. More than 80 percent of our cloth is produced in the non-mill sector and this decline of fabric production in mill is compensated by the production in the non-mill sector.But the problem with this non-mill sector is they have low technology power looms in their units, which mostly produce narrow width poor quality greigh fabrics, which is sold at a lower price. As far as the garment production in Pakistan is concerned, the highest value-added product among the textile group, but the price we are getting for our products is less compared to other countries. According to one estimate 70 percent of these units are in the unorganized sector, producing cotton-made articles.
These units do not have modern machinery and use the non-mill made cotton cloth.This may be one of the reasons that the price we fetch for our apparel exports is low compared to other countries. There has been a change in the world trade, i. e. the shift in favor of clothing. In fact clothing exports have now become the highest growth sector in world trade, exceeding the value of textile exports. So Pakistan also needs to focus more on the garment exports to increase its world share and foreign reserves.
The content of man-made/ or synthetic fibres in the textile products of Pakistan is marginal only 11 percent, which compared to the North East Asian competitors is very low.Their textile products contain synthetic fibres in a very large quantity e. g. in Korean products, it is more than 70 percent. As mentioned earlier, the comparative advantage in textiles and clothing has been declining for the industrial countries and rising for the developing countries as a group. But at the same time, countries which are industrial do have a much stronger comparative advantage in capital-intensive synthetic fibres than the developing countries. World demand for these fibres is increasing at a very fast pace as they impact upon the durability of the product.
China has a strong cotton-base, but at the same time use of synthetic fibers is also increasing. Domestic garments & apparel industry especially the knitwear segment is characterized by heavy presence of Vertically Integrated Units (VIUs). Since each process stage in the value chain of the final product effects the achieved cost, quality and hence price of the garment; therefore while discussing the structure of the garment industry it is important that we take into account available infrastructure at all of these processes.Pakistan's apparel industry comprises of approximately 700 vertically integrated units in the knitwear sector, whereas very few integrated woven garment-manufacturing units are present. There are additionally 670 finishing units both for the woven and knit fabrics. Approximately, there are 4,000 garment units, knit and woven garments and made-ups with 160,000 industrial and 450,000 domestic sewing machines. Most of these are small units which have less than 30 stitching machines.
The industry is characterized by majority of the manufacturing units located in few marked cities.Major concentration of industry is in Karachi and Lahore. Other hubs are Faisalabad, Gujranwala, Quetta, Rawalpindi and Sialkot. Market trend ; related industries The major relation comes directly from the spinning segment, and the main component of the spinning segment, i. e. cotton has the main connection with the agricultural industry of Pakistan. Other than that the wastage of the garments industry are usually recycled and other products, e.
g. blankets can be made out of that wastage. Our readymade garments market focus is on the limited quota market of EU ; USA.Even with quota protection, Pakistan’s exporters have restricted themselves to only a few product categories with poor quota utilization performance in the majority of the categories. Pakistan has been given quota allocations in various product categories to USA. However if we look at overall performance we find out that our industry has been locked mainly into Men's Clothing-Knit and Woven. The rest of the guaranteed market continues to under-perform.
Marketing and Technology are two key areas of concern, which need to be concentrated upon to upgrade the competitiveness the overall industry.Marketing is one of the weakest areas where great emphasis needs to be made. Demand in the ready-made garments sector is cyclic. Manufacturers and exporters have concentrated their efforts in selling to a few buyers in European and the US markets, resulting in stiff in-house competition. Apart from a few well established manufacturers, smaller units face serious difficulty in exporting directly to the foreign buyers. In mid 1980s Pakistan used to be a preferred supplier for buyers in the American, Japanese and European Markets. Pakistani products were superior in quality and were competitively priced.
However the edge was lost as the industry refused to evolve with changing market realities. The initial good quality reputation with foreign buyers was also lost by the unscrupulous activities of the industry itself, it should not be difficult to regain buyers' trust by offering consistency and reliability. As the clothing industry becomes more attuned to operating quick response systems and as consumers' interest in new fabrics and finishes grows, it is likely that the textile industry will become more of a limiting factor within the overall supply chain and therefore will require a prime focus for technology and service development.As more new development in technology comes in more products with better quality and variety could be made. The growing number of new styles and collections required each year demands shorter lead times from design to sample, through manufacturing and delivery requires technology. The Pakistani ready-made garment sector however is marred by very high process losses at every stage of garment manufacturing. One of the major reasons why the local manufacturers have not yet been able to reduce losses is the lack of preference for specialized units.
The industry has long been on the bandwagon of Vertically Integrated Units. The need is to make the manufacturers understand the relationship between process efficiencies, labor productivity and the cost of product. Perspective of a local Garments Importer, Exporter and Distributor For the purpose of empirical research and to get firsthand knowledge of the industry we visited BABRI IMPEX; here is an abstract of the discussion we had with its Managing Director, Mr. Zahid Aslam Khan The Garment Lifecycle:As we moved through the production process we could see the raw materials being used, labor intake, the recycling of the wastage and the safety precautions being implemented. The production process itself is quite a dense phase therefore it is categorized into three major parts out of which the first and the foremost is the cutting of clothes into pieces as per the design of the end product or they may also fabricate it but the firm we visited provides yarn to another company that in turn supplies them with the cloth. Second is the printing done on the cloth and in the third stage these pieces are stitched together to give the final shape.Every process is very critical and is conducted with great care and precaution as various chemicals and machinery are being used to achieve the desired goal.
Q/A: When we inquired about the chemicals being used he told us that they import them as prescribed by the customer. Their comments on Organic chemicals was that, “yes people are shifting towards organic chemicals to some extent but to talk in general it’s still a spoken fad because there is absolutely no way to judge whether organic chemicals are used or not after the dying and washing has been done. In addition to chemicals we inquired about the machines they were using and this was where we came to know about their R&D efforts. The machines they import are not just for their personal use but they also supply them to domestic users. Previously they used to import machines from Germany and US but now due to low prices, China is preferred. Moreover they were the first to adapt to modern semi automatic machines for screen printing but to use them they had to train their employees and as they said most of the people using these machines have got the machines and the appropriate training from them.He also mentioned that due to their experience and knowledge of the machines they could print 21000 shirts at a time from the same machine that others in Pakistan can only use to print 3000 shirts at a time which indeed makes them unique from others.
We also inquired as to why machines were not used to cut the cloth during the initial process to which they said that it is difficult to cut the cloth for knitting with machines because of the stretchable nature of the material however when we talk about the weaving process its highly recommendable to use machinery.He also added that cutting was a very crucial part in the garments process and it distinguishes good from the best, this is where Bangladesh and India have a strong advantage. The little amount of waste that does arise from the cutting process is recycled to form blankets, etc and to give an example he mentioned that those blankets are used by the NATO forces are in fact made from this waste. He also said that Pakistan is the quickest when it comes to turn around time which is the overall time of the production process.As mentioned earlier that the entire working of production is done under great protection. So let’s now talk about the precautions they take in the production process. Due to the changing weather conditions it is important that the same yarn be used for a specific consignment otherwise the end products may have differences.
He also talked about the safety precautions most of which are difficult to implement as the labor is sometimes not trained to use them or they just don’t feel the need of using them. When we queried them about the labor, they said that the whole production process is labor intensive.Talking about the salary, average wage is 10,000 Rs. Therefore the labor is sometimes referred to as cheap and unskilled but they find it cost effective because the people come to them without much education or training and what they take from here is experience and a fair amount of income. BENCHMARKING ANALYSIS OF THE GARMENTS SECTOR Benchmarking is the process of identifying and adapting outstanding practices from Organizations and companies around the world to assist an organization or company in measuring and improving its performance.A thorough understanding and knowledge of best practices in the relevant areas is the basis of a successful benchmarking exercise. It took years and years of unending research to come up with a system of metrics and quartile- not to forget a detailed understanding of best practices in the Garment industry that too aided in coming up with a system as comprehensive as this one.
Top ranking factories in the world, are those that get an overall benchmarking score in the top quartile while those in the fourth quartile are considered poor organizations, giving low class performances.Likewise factories whose scores put them in the second and third quartiles are medium-high performers and medium-low performers. Research and studies were conducted over a time period of two to three years and the following results were reached: BENCHMARKING PARAMETERS Following are the agreed benchmarking parameters from the respective technical Fields: Dyeing/Finishing, Knitting & Laundering 1. Productivity 2. Work Method 3. Technological Strength 4. Time Line 5.
Maintenance 6. Quality 7. House Keeping 8. Workers Conditions 9. Presence of Analytical Culture 10. Training 11.Product Development Sewing, Industrial Engineering & Maintenance 1.
Production per machine per shift 2. Marker efficiency 3. Defects percentage 4. B-Quality 5. Production moving system 6. Standard minute value 7. through put time 8.
on time delivery 9. Turnover 10. Absenteeism 11. Direct to indirect ratio 12. Safety & House keeping 13. Preventive maintenance 14. Machine per technician 15.
Spare part control 16. Numbering system to Machine 17. Machine attachment control Poor Practices [pic] [pic] Compliance Issues Finishing hall and HousekeepingHousekeeping Issue Line Balancing Maintenance Overstocking Compliance Improper utilization of electricity Overcrowding Good Practices Effective use of lighting Passage way mark Storage bins for spare part Tool handling (maintenance) Drainage line Covered and Clean Floor Written Instructions GOOD PRACTICES/RECOMMENDATIONS FOR IMPROVEMENT The Textile sector of Pakistan has seen some foremost changes from the year 2005 (onwards).Like any other business in the world, this industry too requires the servers to be better and faster than their competitors in order to serve their consumers and make a better name in the market by staying ahead of others. Some countries experience a boom while others go through a fall in this race. In case of Pakistan, we consider India, Bangladesh and China to be our direct competitors, so any result of Pakistan will always be directly compared with the three- which is not very good for the country’s image as we are lacking far behind our competitors.Just to quote a report : During the period 1990-2001 the growth in garment exports achieved by Pakistan was only 110% as compared to 160%, 278% and 750% achieved by India, China and Bangladesh respectively.
Pakistan’s clothing exports make up to 1 per-cent in the international market, compare this to India which is twice as much and China which is sixteen times ahead of us. Pakistan’s readymade garments sector is a mixture of good and bad results : A certain amount of growth has been witnessed in the denim sector, on the contrary the knitwear sector has done a poor job.It is said there are a number of reasons behind this bad performance in the market- some among them are higher utility costs and neighboring countries giving subsidies to their products. But if we notice all these causes are beyond a manufacturer’s control. This study focuses on the internal factors that we can work on to improve Pakistan’s Textile industry’s standing in the International market. All the aspects have been brought down under the following three categories: 1. Factor Driven aspects 2.
Efficiency Driven aspects 3. Innovation Driven aspects FACTOR DRIVEN ASPECTS 1. Plant LayoutA plant layout of any factory/organization reflects on its performance and level of efficiency. It was observed that majority of factories in Pakistan are void of substantial plant layouts. There are many adverse effects of such an inefficiency- to begin with you get undesirable working conditions which lead to constant augmenting of the costs. The plant layout is one of the key phase of the manufacturing cycle thus ample importance should be given to it. It is a must for all the companies to analyze the process flows, time frames, motion, bottlenecks, speedy/slow workers, passage ways, etc.
2. Lighting ConditionsOne of the smart ways of reducing manufacturing costs is to utilize the natural day light effectively. Therefore recipients should formulate a lighting plan whereby they make sure they reduce the utility costs by utilizing the natural free light available all day. Moreover, it was also observed that the in-house lighting systems of many factories was below satisfactory level- such irresponsible lighting conditions will obviously result in disappointing products especially in the cases of sewing operators and quality controller who then provide highly defected material in the market.. The tube lights should be according to the tandards. Offices should be well quipped with energy savers to save as much light as possible.
3. Working Environment It is only natural and a part of human nature to produce better results if an environments is clean and suitable to the functions that are needed to be carried out. If the basic environmental needs are not taken care of, the workers will be agitated and will not be in a position to deliver best of their performances. This happens because the concentration of the workers is then diverted and their comfort is not taken care of- thus low productivity and quality of products produced.All the big corporations of the world (regardless of what industry are they associated with) take good care of their working conditions and the basic needs of their workers. However, our study showed poor results in this regard, only a handful of industries have an inclination towards such aspects and majority of them are neglectful towards the working conditions being provided to the workers. If Pakistan wants to improve its stand in the global market, it will have to give substantial importance to the working conditions being provided to the orkers so that they may work in environments that fosters productivity and better quality.
4. Workstation Layout A better work is produced if the operator feels better. Our study reflects that only two of the corporations have a satisfactory workstation layout whereby the operator was fine with the workstations. The uncomfortable workstations cause pain, numbness, or tingling in the shoulders, neck, back and hands, eventually affecting the productivity of sewing machine operators. These symptoms are related to the job/workstation for instance.An uncomfortable work position: Sewing work forces you to hold your body in one position for long periods. If it is an uncomfortable position, pain and injury can result.
Your position is determined by the fit of your chair and foot control, your need to see the work, and your need to grasp or hold materials in place. Repeated or forceful motions Reaching, stitching, pinching, pulling... hundreds of times a day. Each motion can cause small injuries to muscles and joints. Long work hours and few breaks mean less time for muscles and joint injuries to heal.
Hard edges: If the edge of your chair, worktable or table legs press into your body for long periods, it can damage nerves or other soft body parts. We can achieve better efficiency and high productivity & quality by conducting Ergonomic studies and consequently providing the good & efficient workstation to Operators: Use adjustable chairs: Employers should get durable industrial chair that have Adjustable seat height, padded seats, swivel bases with five legs (not four) and Padded adjustable backrest. Use foot supports: Foot supports are an important part of the seated workstation.Employers may need a mechanic to adjust, install, or build up foot support in the Right position for each worker (height, forward/back and left/right). Adjust your equipment to fit your body: Every operator should adjust their Equipment according to its body ergonomics for better productivity and also to EFFICIENCY DRIVEN ASPECTS 5. Capacity Building Only installing automation and the latest machinery hardware does not guarantee Productivity improvement, but training has its own importance for improvement Even with existing infrastructure.Therefore, the basic recommendation for Improving the overall performance of the garment industry is to implement training /capacity building programs (especially focusing the soft skills) for: Management: Top managerial personnel should be trained both at company Premises and at the international business schools in administration, finance, Marketing and production.
Technical Management: Technical managers receive training almost exclusively from textile institutes/colleges. In plant arrangements for training of technical personnel are required in the modern scientific management control methods.Supervision: In the vast majority of textile mills, supervisors receive no formal training whatsoever. Arrangements for training of supervisors should be provided. Workers: Formal training programmers for the training of workers inside the mills are generally non-existent. Workers are accustomed to low quality and low productivity in general. These habits can be changed only by training so that workers develop the habit of obtaining guidance and assistance of qualified professionals.
Management usually invests on machinery, but the people who run that machinery are the most important to be trained to make them understand about the machinery: operation and routine maintenance. This would improve the reliability and efficiency of the machine and operator as well. The highest priority is to train middle management such as line supervisors and industrial engineering personnel. As garment industry is a labor intensive industry and labor wage directly impact the total cost of the business, therefore the middle management have the greatest effect on the efficiency of the plant. 6. Performance MeasurementPerformance measurement is evaluating how well organizations are managed and the value they deliver for customers and other stakeholders. It is the process of assessing progress toward achieving predetermined goals, including information on the efficiency with which resources are transformed into goods and services (outputs), the quality of those outputs (how well they are delivered to clients and the extent to which clients are satisfied) and outcomes (the results of a program activity compared to its intended purpose), and the effectiveness of operations in terms of their specific contributions to program objectives.
The garment industry should adopt performance management system in their organizations in order to measure and evaluate their performance and take corrective measures accordingly. An effective approach to performance management enables employees and teams to understand the goals of the organization and to see how individual and team outputs contribute to the achievement of organizational objectives and values. Integrating people, planning and performance with organizational objectives develops individual and organizational capability and leads to higher performance.The performance appraisal process articulates the standards of work expected of employees and the values and behaviors employees are expected to uphold in meeting their job requirements, communicating and working with others. Performance management leads to higher performance that is more closely directed to the objectives and needs of the organization. Performance appraisal and feedback assist employees to understand what work they do well and how they can improve their performance. Suggested techniques to utilize are climate survey, 360° evaluation, and productivity Diagnosis, etc.
7. Industrial Engineering DepartmentIndustrial Engineering techniques are very helpful in any organization for increasing its productivity and quality. The garment sector in Sri Lanka, India, China, and other competitive countries employ IE techniques to make their processes and workers more productive. IE techniques are helpful in addressing estimating lead times, no. of workers, working / operating time, costing, process designs, process flows, line balancing, best methods to produce, etc. In Pakistan, the industrialists are realizing the importance of IE and making their efforts to establish IE departments within their ompanies. Only few companies are successful in this regard, but still unable to tap the full potential of IE.
Therefore, it is proposed to establish and/or strengthen industrial engineering departments in the companies and in plant arrangements for the training of technical personnel are required in order to implement the IE techniques more effectively. Moreover, master trainers on IE should be developed from foreign institutions. Suggested techniques to implement are work study, method study and value stream mapping. 8. Supply Chain ManagementSupply Chain Management (SCM) is the process of planning, implementing, and Controlling the operations of the supply chain as efficiently as possible. Supply Chain Management ps all movement and storage of raw materials, work-in-process inventory, and finished goods from point-of-origin to point-of-consumption. In essence, Supply Chain Management integrates supply and demand management within and across companies.
It is all about having the right product in the right place, at the right price, at the right time and in the right condition.We can also use the concept of Quick Response in order to understand the supply chain management. The quick response strategy is to linking manufacturer, supplier and retailer with each other and cooperates effectively in order to reduce the lead time of the production. Generally, many manufacturers, suppliers and retailers are struggling to use information technology for adopting quick response strategy and to streamline their supply chain. At present, some textile enterprises use quick Garment Sector response system to be the leaders and to have a competitive advantage over their competitors.The textile and garment industry in Pakistan should have to adopt effective supply chain management systems in order to face the challenges of global Competitiveness. They have to be quick in their responses and even quicker to meet the increasing demands / trends of the customers.
They have to streamline their supply chain to timely process the production orders of their customers. They have to think of the lead time to export, for example which is 5 days in Denmark and 25 days in Sri Lanka as compared to 33 days in Pakistan (refer to page 11). They have to work on reducing the lead time along with their takeholders including the government. They have to benchmark other countries in order to be competitive in this arena. 9. Inventory Management Systems Missing of the raw material is also the major cause of high cost. It is observed that in many factories there is no proper system for controlling the inventory.
Due to which raw materials are lost about 5% in every month particularly small items such as label, snap, zipper, etc. Moreover many errors and omission were observed in the records for stock, which is undesirable (a crime) in any industry.Efforts are required to be put on revamping and adopting an effective and efficient inventory management system based on the new tools and techniques prevalent especially in the garment sector. This can also be rectified by hiring of consultants on inventory management systems. Suggested techniques to improve are to implement Enterprise Resource Planning (ERP) and Material Resource Planning (MRP) programs. 10. Inefficient Storage Storage is an integral part of any industry.
It is the place where we place / store items for certain period of time and use on when and where necessary basis.The inventory on the other hand is the list / register of those items. Mostly in the Pakistani garment factories, the people do not have the knowhow of how to store the items. They do not have the proper concept of inventory management; instead they are just maintaining registers. Inventory levels are not defined and sometimes they have to wait for the item to be purchased from the market. Similarly, the placing of items is also not proper, and if one has to find a certain item, he / she has to spend time in searching for that particular item.Also, in many companies we find things that probably should not be in the store or not required / needed (for example old fabric, old accessories & machines, raw material, finished goods, etc.
), thus incurring extra cost. It is required to improve the storage designs keeping in mind the first in first out (FIFO) rule, space utilization, identification & traceability, ease of search & access and handling of items. It is also required to put due emphasis on stores, which is a neglected department in almost every factory. It is also important to dispose off the items that are not necessary in order to effectively utilize the money.Some of the factories are also facing the problem of insufficient space for storage, which may be addressed by hiring extra storage space (where needed). 11. Shortage of Raw Material This problem is linked with the material handling system or the inventory management system.
This is also the result of poor supply chain management system. Addressing these issues would solve the problem of shortage of raw material. 12. Fabric Utilization Many garment businesses misunderstand that labour cost is the most important item to control cost and do not concentrate to control cost of raw material in Particular fabric.This kind of thinking can lead them to high cost, therefore, the Management should have to implement fabric utilization project by using computer program, hire consultant, training employee, and establish fabric utilization. 13. Quality Management Mostly top management has concerns on quality; and the emphasis is on quality control staff of customers and strong inspection control of the production lines and the finished goods.
But this is not the end; today the concept of quality is more challenging and demanding. It requires a lot more effort than in the past days.It requires implementing different standards such as WRAP, ISO 9000, ISO 14000, SA 8000, OHSAS, etc. in order to be competitive in the global market. It also requires the modern concepts of TQM and Kaizen Management in order to improve continuously apart from observing the standards. Adoption of an Integrated Management System is necessary in this context. It needs strong management commitment and dedication of the staff to achieve quality; quality workforce, quality skills, quality environment, quality team management, quality leadership, quality documentation, quality control, etc.
All this can be achieved through training of existing personnel, Master Trainers/consultants, strong and focused planning and a visionary & committed Leadership. INNOVATION DRIVEN ASPECTS 14. Technology Development Technology development is another aspect of competitive advantage among the Companies. Most of the companies in the dyeing & garment sector do not support technology development and their process designs are weak or less productive than their competitors in the global market.Some of the large companies have invested a lot of money to recruit experienced people and consultants to develop their process designs, including the usage of computer software and high tech machines like Garment Gerber Technology (GGT) and computerize hanger system in garment sector, automatic chemical dozing & computerize sampling in dyeing. The result is that they are surviving in the global markets. Our garment industry, at large should focus on their R&D capabilities and activities in order to develop their technology and to be competitive.
15. Brand ManagementMost of the companies have not created their own brand which present the Companies face to the market. So a consideration as a business strategy for future is to start creating a permanent own brand and to try selling the products with it to the existing buyers at a so-called advertisement price which means no commercial price just to develop it. CONCLUSION We have tried to highlight some of the direst needs in this research. Factories have an immense potential to increase productivity and efficiently use resources applied to basic techniques. Industrial engineering, production engineering, systems and controls and ther modern management concepts are of the highest priority as basic things like having the right attitude and suitable climate can improve the productivity up to 20- 25%. Training and professional development to implement such programs are needed.
Compared to international standards we have a low training budget and few training programs, which are not based on scientific training principles. Staffing levels are generally too high, which results from poor practices as well as insufficient training. Often factories have no separate training budgets and no defined training program.It is easy to assume that employees will learn necessary skills while doing their jobs over time. These poor training methods are detrimental to productivity. Training is the single most effective strategy as well as the lowest cost strategy to increase productivity and quality. It deals with professional development, weaknesses in production controls, industrial engineering and organization of work.
To achieve maximum flexibility, productivity, and quality, training of production personnel, particularly middle management and supervisors is essential and programs and production controls should specifically cater to this need.Professional development systems should focus on training personnel who have many years of practical experience have very little theoretical background. This can help reduce manufacturing costs and help introduce new procedures for production, quality control, planning, and information systems. This shows that investments in people, systems and equipment have large returns and so has significant implications for top management.The demand for different types of skills for example operational, technical, and managerial skills in the industry will continue to grow, as will demand for workers with practical skills. A workforce that is skilled in technical and management arenas will be the best one. If the long term requirements for education, training, and development are met efficiently they will surely yield enormous benefits.
REFERENCES: The Global Textile and Garments Industry by Infodev Publications Garments and made ups report by SMEDA Pride. org. pk Prgmea. org. pk
Cite this Page
Garments Industry Pakistan Cometitiveness. (2019, Feb 22). Retrieved from https://phdessay.com/garments-industry-pakistan-cometitiveness/
Run a free check or have your essay done for you
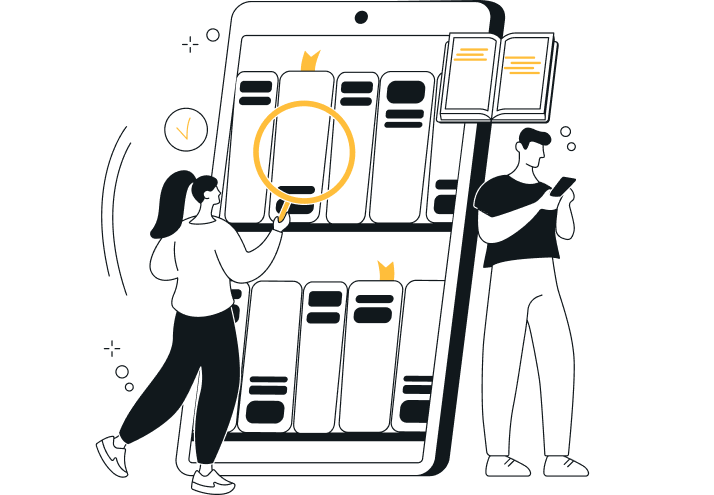