Comparison between lean and mass production
To efficiently describe and understand lean production, it is important to draw contrast and comparison with mass production and craft production. Craft production employs the services of skilled human recourses and simple tools which are flexible to produce what has been requested by the customer on an item-by-item basis. The outcome of this process is that the customers obtain exactly what was ordered but at a high cost. On the other hand, mass production employs the services of specialized professionals in the design of products manufactured by unskilled workers who nurtures the expensive machines which are single purposed.
These machines generate high volumes of standard products. Because there is disruption in the production process which is costly, the production process requires buffers such as additional supplies and workers to ensure efficiency in the production process. Additionally, the extra costs required to change to the new product calls for maintaining of standard product designs for along duration. This results in low costs in consumer prices at the expense of product variety. Furthermore, the workers involvement in the production process is boring.
By contrast, lean production employs the services of multi-skilled professionals at every level of the production process within the organization and utilizes automated machines which are highly flexible and therefore capable of producing huge volumes and varieties of products. The word lean is derived from the use of half of the human resources in the production process, half the available production space, half the number of tools investment and finally half the hours of engineering available to produce a new product in exactly half of the total time required.
Order custom essay Comparison between lean and mass production with free plagiarism report
The most outstanding difference between lean and mass production is the setting of goals by the mass producers. Achieving better performance would therefore cost a lot and consequently exceed the capacity of the available human resources. On the other hand, lean producers are more concerned with perfection and thereby achieving continuous benefits. Additionally, in lean production, responsibilities are pushed down the ladder in the organization to individual levels.
Lean production requires individuals to poses variety of professional skills which should be employed in a creative way in a team environment. This is not the case with the conventional view of career channeling in which case the individuals develop enormous technical skills and knowledge is a narrow specialized discipline. The contradiction however is that the better one becomes at teamwork, the limited is the knowledge about a specialized area. The foundation of lean production is dated back to 1908 when Henry Ford created a T model.
This model achieved two objectives which were that the car was user friendly and was designed for manufacturing. The principle behind mass production was contrary to the common belief of assembly line production but rather the parts interchangeability and simplicity of being attacked to one another (Noyes, 1997). Challenges to lean production The successful implementation of lean production requires a shift in mindset. The use of lean production requires a shift from the production of huge quantities to small quantities.
Instead of maintaining large inventories as demand buffers, organizations adopting lean production principles maintain low product levels in the production process. These processes must be reliably and efficiently managed in order to eliminate defects. The movement of materials and product parts as well as people must be maintained at an optimal level. This will help in the elimination of time wastage inherent in waiting for equipments, materials and people.
The implementation of lean production involves several changes in the organizational structure. These structural changes are necessary because of the shift of principle from functional areas to product families. The workforce is shifted from the functional categories into cells which are responsible for the overall production. The workforce must therefore acquire knowledge and skills necessary to perform multi-skilled duties. Furthermore, the multi-skilled workforce within a cell should operate as a team which is capable of self directing.
These workers should constantly strive to achieve perfection by focusing on the process improvement. Implementing these changes is difficult. Transforming the operation into teams requires restructuring of the organization which at times triggers resistance and fear. The requirement of multi-skilled workforce necessary for efficient implementation of lean production is vulnerable to resistance from workers. Proponents of this production strategy argue that these changes are necessary to achieved enhanced and participatory work environments.
However, several research studies have shown that these changes present challenges to organizations. The identified areas of difficulties include organizational changes in work teams, multi-skilled professionals, constant improvements and changes of roles in the resulting work teams which are self directed (Humphreys et al. , 1999). Working as a team is the underlying principle behind lean production strategy. It is therefore important to consider the impacts of the changes in the working environment and the relationships in these teams.
Teamwork has been found to be a necessary requirement in order to successfully implement the principle of lean production and to improve the quality and flow of just-in-time delivery strategy (McLachlin, 1997). This importance has been reinforced further by a case study conducted by Banker et al. (1996). The quality, labor effectiveness and production of the workforce were compared before and after the divisions into various teams. The three performance measures were found to be higher in most organized teams as compared with teams which had frequent conflicts which had poor display of performance.
Social interactions within the teams also play a significant role in the performance of the team. The perception of members presents a significant challenge during the formation of these teams since it involves integration of members who traditionally worked in separate departments. This integration is a possible cause of conflict as observed by Humphreys et al. (1999). This case study described the relationship between an operator and engineer who initially belonged to different departments of the organization.
These people were grouped in the same team; however their collaboration was sabotaged by their view of each other. The engineer viewed questions asked by the operator as threats to his seniority while the operator perceived the engineer responses as insulting (Humphreys et al. , 1999). The findings of this study is coherent with another study conducted by Yauch and Steuedel (2002) which concluded that rigid boundaries prevalent among groups within an organization impedes the migration to lean manufacturing.
These organizational factors are impediments to efforts aimed at continuous improvements. These organizational factors include absence of mutual respect, boundary rigidity, and under organizing among others. Under organization affects the process of migration to lean production as well as causing time wastages. The absence of mutual respect implies that workers do not initiate improvements because the culture of the organization punishes mistakes. Boundary rigidity makes information flow and continuous improvement difficult (Yauch & Steuedel, 2002).
Cite this Page
Comparison between lean and mass production. (2018, Jan 10). Retrieved from https://phdessay.com/comparison-between-lean-and-mass-production/
Run a free check or have your essay done for you
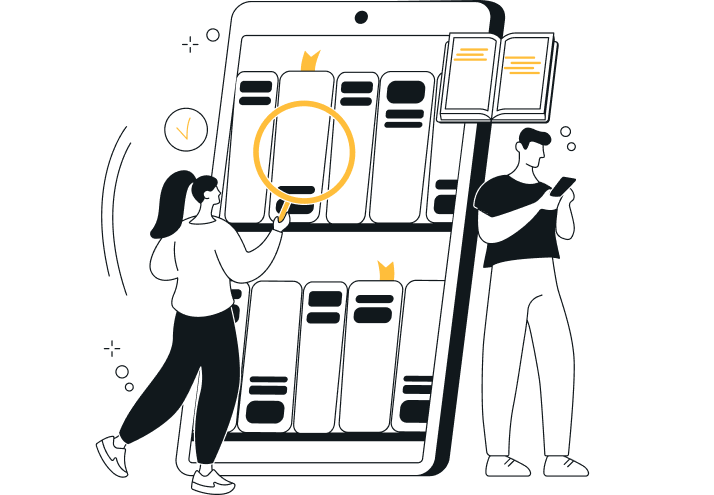