Toyota Motor Manufacturing Usa – Seat Problem
1. As Doug Friesen, what would you do to address the seat problem? Where would you focus your attention and solution efforts? Why? The two major causes of seat defects originate with KFS, relating to material flaws and missing parts. The seat bolster issue is a distant third. As KFS is the responsible party the situation needs to be addressed at their site. Using the traditional TMC first principle of ‘let’s go see it’ and then converge on the Five Why’s, Doug should visit KFS and inspect the manufacturing and QC process.
By focusing on uncovering issues at the source of the seats, it is likely there will be fewer problems at the TMM plant. The focus on QC at KFS could potentially eliminate 113 of the 138 problems reported between 14-30 April, 1992. In the short term, address the immediate issue of the backlog by reconciling orders with KFS to ensure the backlog is cleared. This would require little resource and be a quick win. 2. What options exist? What would you recommend? Why?
Simplifying the seats could reduce the problem since product proliferation appears to added complexity to KFS manufacturing process, though it’s unlikely that the designers will take this feedback as welcome given similar issues are not faced at the Japanese plant. Redesigning the seat or replacing easily broken parts could reduce breakage and installation issues, while training the staff to be more careful with installation, or the KFS staff with assembly, may also be an option.
Order custom essay Toyota Motor Manufacturing Usa – Seat Problem with free plagiarism report
Replacing the supplier would be a high-risk option that would only be explored if the issues at KFS were so irreversible that TMM had no other choice. While all of these options may potentially address part of the issue, improving the QC process and then working backwards from there into the assembly and manufacture at KFS will ultimately have the greatest single impact on production efficiency. 3. Where, if at all, does the current routine for handling defective seats deviate from the principles of the Toyota Production System?
One of the major underlying principles of TPS was building in quality on the line. The reporting of defects at the seat assembly point did not appear to be consistent and was only uncovered by interviewing team leaders on the factory floor. In addition, cars were reported as defective yet continued down the assembly line until completion, where they were taken off-line to wait for a replacement seat. Nowhere else on the line were cars removed due to defect: team leaders or production managers were responsible for resolving issues while still in the assembly line.
The reasons for doing so appeared rational, since the car could be finished with a defective seat, seats needed to be ordered from KFS and stopping the line for such a lengthy period would have decreased productivity. One flaw in the process was that there were flaws that could be rectified in the Code 1 clinic. These flaws could have been dealt with while on the assembly line and thus reduced the burden in the clinic, while raising awareness of common defects and their source earlier in the process.
The clinic did not appear to have the same reporting responsibilities as the assembly line since management were not aware of the main causes of the defects. 4. What is the real problem facing Doug Friesen? Process and feedback management problems at TMM and quality control management issues at KFS were the underlying reasons for the seat problems. Moreover, the ‘jidoka’ process had been bypassed in the seat installation process, exposing a potential weakness in the production line.
Doug should implement an in-line attempt at fixing seat problems prior to the referral to the Code 1 Clinic. Regular feedback from the clinic as well as the assembly line would improve information transparency and identify the source of defects for management at the earliest point in the process. Finally, the same processes should be adopted at KFS and QC strengthened considerably to avoid the delivery of defective seats as much as possible. Since this is a critical path to seat delivery, no seats should pass to TMM without a thorough QC test at KFS.
Cite this Page
Toyota Motor Manufacturing Usa – Seat Problem. (2018, Feb 02). Retrieved from https://phdessay.com/toyota-motor-manufacturing-usa-seat-problem/
Run a free check or have your essay done for you
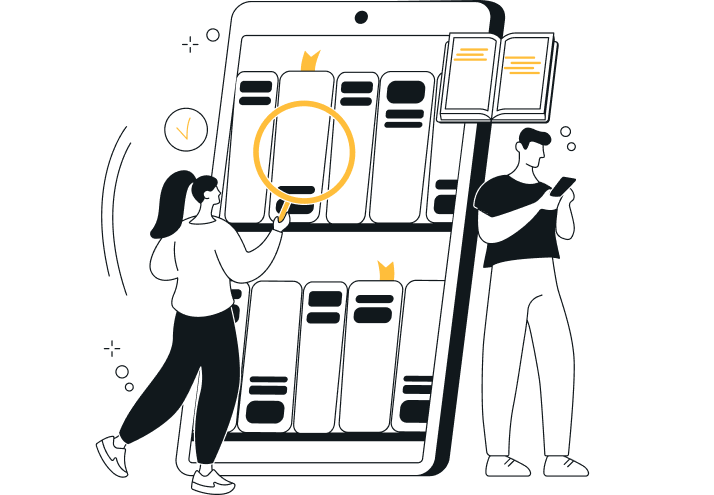