Usage of ABC System
A. ) Critically discuss the way (ABC) operates, referring to pools, drivers and activity hierarchy. Definition Activity based costing (ABC) is a cost accounting approach concerned with matching costs with activities (called cost drivers) that cause those costs. It is more sophisticated kind of absorption- costing and replaces labour based costing system. ABC states that (1) products consume activities, (2) it is the activities (and not the products), that consume resources, (3) activities are the costs drivers, and (4) that activities are not necessarily based on the volume of production.
Instead of allocating costs to cost centres ( such as manufacturing, marketing, finance), ABC allocates direct and indirect costs to activities such as processing an order, attending to a customer complaint, or setting up a machine. A subset of activity based management (ABM), it enables management to better understand (A) how and where the firm makes a profit, (B) indicates where money is being spent and (C) which areas have the greatest potential for cost reduction.
The motivation to choose the ABC system is because it is too difficult to assign some cost like, indirect cost, management salaries and office staff salaries through Absorption costing. And this method (ABC) has found its niche in the manufacturing sector. It can be applied to derive realistic costs in a complex business environment. It can be applied to all overhead costs, not just production overhead and also it can be used just as easily in service costing as in product costing.
Order custom essay Usage of ABC System with free plagiarism report
Although it is apparent that ABC alleviates considerably many of the worst effects if the arbitrary product line cost allocations inherent in many conventional systems, it does not eliminate the mall. Cost pool: some measure of cost apportionment may still be required at the stage of cost pooling. Overheads common to more than one cost pool (especially in the absence of specific resource metering) could include rent rates, insurance, building deprecation, power, heat, and light. They may require to be attached to cost pools although no definition means of doing this is available.
Indeed the proliferation of cost pools under an ABC system could increase the amount of such apportionment which is necessary. Cost drivers: once pooled an appropriate cost driver must be used to attach cost to individual products. It is doubtful whether even a very detailed segmentation of cost into a large number of cost pools will ever achieve a perfect homogeneity within each pool. Thus the ability of a single cost driver to fully explain the cost behaviour of a cost pool is questionable.
In order to have a usable cost driver a cost must be caused by an activity that is measurable in quantitative terms and which in turn can be related through this measure to production output. Not all costs will be readily susceptible to this process. For example, it will be difficult to identify meaningful cost drivers for corporate as opposed to based advertising, top managerial activity relating to the business as a whole and other general costs such as external audit, finance costs and goodwill amortisation.
It is doubtful that ABC system can completely avoid the problem of cost commonality at the stage of applying cost driver rates to achieve product line costs. This will occur where the chosen cost driver relates t more than one product. For example where a maintenance hour is spent in repairing a facility used by several products or a purchases order contains items used on many different products. The cost of that hour or invoice is not specific to one product but will have to be spread over all products affected on the basis of the cost driver weightings given to each of the relevant products.
The selection of cost driver is not automatically provided mangers with an easy-to-step cost control ‘handle’. (ABC book, p. 109). Also this ABC system is not good for making decision because this is not true cost this is based on average cost. Disadvantages ABC will be of limited benefit if the overhead costs are primarily volume related or if the overhead is a small proportion of the overall cost. The choice of both activities and cost drivers might be inappropriate. It is impossible to allocate all overhead costs to specific activities.
And it can be more complex to explain to the shareholders of the costing excise. Although the benefits obtained from ABC might not justify the costs. ABC operating way ABC has two stage to produce the first one is the Cost pool and the second one is the Cost drivers which are linked to the activity hierarchy. And the activity hierarchy is based on five different activity, such a Unit-level activities, Batch-level activities, Product-level activities and Facility activities. Cost pool A cost pool is an activity that consumes resources and for which overhead costs are identified and allocated.
Cost pools are the grouping expenses, which is a locatable of accounts serving to express the cost of goods and service, within a business or manufacturing organization. The Principe behind the pool is the direct and indirect cost to be correlated with specific cost drivers, so to find out, the total of expense associated with the production of a product. Cost driver A cost driver is the units of an activity cost an activity cost driver is something that drivers the cost of a particular activity. A factory can run such machine as an activity.
The activity cost driver with the execution of the two machines are connected, could be machine hours, what is the cost of Labour, maintenance and energy consumption drive the machinery activity. An activity can have more than one cost driver attached to it. For example, a production activity may have the following associated cost drivers a machine, machine operates, floor space occupied, power consumed, and the quantity of waste and or rejected output. The ABC activity hierarchy has five levels: Level one: Unit basis- costs are primarily dependent on the volume of production.
This category will therefore include costs such as machine power. Level two: Batch basis- costs primarily dependent on the number of batches. This category will include the costs of set-up and batch monitoring. Level three: Process level- costs are primarily dependent on the existence of process. This category will include such costs as quantity control and supervision. Level four: Product level- costs are primarily dependent on the existence of the product group or line. This is management and parts administration.
Level five: Facility level- costs are primarily dependent on the existence of a production facility or plan. Costs as rent, rates and general management. Example of Cost pools and Cost drivers Direct labor hors Supervising cost pool Number of parts Painting cost pool Number of test Inspection and testing cost pool Number of parts Assembling cost pool Machine hours Machine cost pool Number of set ups Setting up Machines cost pool Number of purchases orders Ordering and Receiving Material cost pool Classify in Activity Based Costing method to cost driver is very necessary for unit costs and total costs.
We know that. Costing on the concept that products consume activities and activities consume resources based Pools of activity, we find cost drivers. Assume a company wants to produce several products. At this time, what with companies to calculate the unit cost? Only by the raw material and labour costs and production overheads to absorb direct labour hours or machine hours is not good way. There will be many activities in which we are spending money, such a number of purchases order, number of setups, machine hours, number of parts, number of test and direct labour hours.
B. ) What kinds of firms/products would you advise to use ABC? It would be advisable for big or/large companies with multiple products to use ABC, because for these companies it makes a lot of logic with multiple products or services who are distress from inaccurate costing information and need to know which products are really winners and which are losers. For these companies the effort required to successfully implement ABC is worth the time and resources.
ABC can identify high overhead costs per unit and find ways to reduce the costs, avoid decreases in head counts due to inaccurate allocation of costs, and measure profitability with higher accuracy than traditional costing that uses direct-labor hours as the only cost driver. ABC is most useful when you have lots of overhead and a bunch of different products. In any environment that doesn't have a lot of overhead; ABC isn't worth the work and won't deliver insights. Also, ABC doesn't make sense in any business that sells a single product or that provides a single service, hich is usually the case in a small firm. The reasons for implementing ABC is many Companies they will have better Management, good budgeting, performance measurement, calculating costs more accurately, ensuring product/customer profitability, evaluating and justifying investments in new technologies, improving product quality via better product and process design, increasing competitiveness or coping with more competition Similarly, when assessing the costs of products and services, ABC can illustrate the costs of them and help in establishing the profitability of the individual products and services.
This can be particularly useful in modern economies where companies are increasingly trying to differentiate and personalise both products and services and tailor them to individual needs and requirements ABC can be used on wide ranges of products, and also in modern manufacturing. This system is also good for a lot of non-factoring-floor activities such as product design, quality control, production planning and customer services. Here are some examples of ABC users in the UK: British Aerospace (defence) Hewlett Packard (electronics) IBM (electronics) Black and Decker (tools) Royal Bank of Scotland (banking)
Cummins Engines (engineering) Guinness (drinks) DHL (couriers) Norwich union (insurance) Lucas industries (engineering) Nissan Yamato (cars) Seven Trent Water (water) C. ) Evaluate the extra commercial value of using ABC in comparison with standard absorption costing. ABC has been developed to solve the problems that traditional costing methods create in these modern environments. The Activity based costing (ABC) assigns manufacturing overhead costs to products in a more reasonable manner than the traditional approach of basically allocating costs on the basis of machine hours.
Activity based costing first assigns costs to the activities that are the real cause of the overhead. It then assigns the cost of those activities only to the products that are actually demanding the activities The Traditional accounting focuses on what it cost to do something, for example, to cut a screw thread; activity based costing also records the cost of not doing, such as the cost of waiting for needed for part. ABC records the costs that traditional cost accounting does not do. Any unit cost, no matter how it is derived, can be misinterpreted. There is temptation to adopt a simplistic approach.
This would say for example, that if it cost 10000 to produce ten units, it will cost 10000 to produce 100units. As we know, this in incorrect in the short term, owing to the existence of short-term fixed cost. The ABC approach does not eliminate this problem anymore than the traditional approach. The alternative to presenting full absorption costing information in a traditional costing system has been to prodive the user with a marginal costing statement which distinguishes clearly between the variable cost of production and the fixed cost of production.
This carries an implication for the decision-maker that if the variable cost of production is 100 for 20 units, the additional cost of producing a further 50 units will be 50x5=250 The traditional method of costing relied on the arbitrary addition of a proportion of overhead costs on to direct costs to attain a total product costs. The traditional approach to cost allocation relies on three basic steps. Advantages of ABC ABC provides a more accurate cost per unit. As a result, pricing, sales, strategy, performance management and decision making should be improved.
ABC also provides much better insight into what drives overhead costs. And it recognises that overhead costs are not all related to production and sales volume. In many businesses, overhead costs are a significant proportion of total costs, and management needs to understand the drivers of overhead costs in order to manage the business properly. Overhead costs can be controlled by the managing cost drivers. D. )Research and briefly trace the main developments in ABC theory from 1988 to date
Activity based costing (ABC) is a cost allocation model pioneered by Harvard Cooper and Kaplan (1988) in the field of the management account. Studies have investigated the structure of ABC models that emerge from the process (e. g. Noreen & Sanderson, ABC has been successfully applied manufacturing and service industries (Helmi & Hindi, 1996; Kroll 1996; Reimann & Kaplan 1990) for improving tactical and strategic decision making and for enhancing corporate cost control and customer profitability (Bradway & Ross 2000; Mabberly 1998). In 1999 Peter F.
Drucker explained in the book Management Challenges of the 21st Century, that traditional accounting focuses on what it cost to do something, for example, to cut a screw thread; activity based costing also records the cost of not doing, such as the cost of waiting for needed for part. ABC records the costs that traditional cost accounting does not do. Granof Platt & Vaysmann (2000) discuss ABC implementation in the public sector, by using the example of a university department. They have demonstrate the validity of ABC method application in accordance with university process
Cite this Page
Usage of ABC System. (2017, Mar 29). Retrieved from https://phdessay.com/usage-of-abc-system/
Run a free check or have your essay done for you
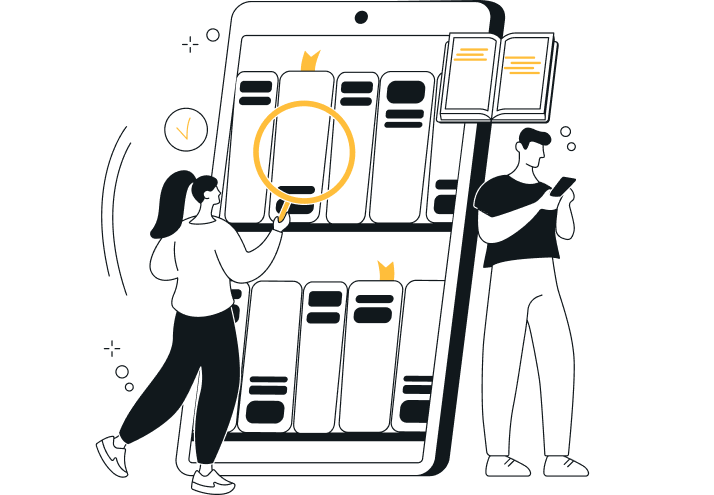