Toyota Production System in Action
Many people confuse the Toyota Production System by thinking that it is just for the production floor. That notion is incorrect. In Toyota plants everyone is trained in the TPS. According to Seizo Okamoto, president of Toyota Manufacturing Indiana, Inc., 'At Toyota, we believe that we create real value through production. The most important person is the production team member. But we have decided that other functions have to support production - I mean in administration, accounting, and engineering. Without fully understanding TPS, they can't support effective production; they just create conflict.' (Lindsay Chappell, 2005) So TPS can and should extend beyond the shop floor. But what about non-production facilities?
A good example of a service industry employing the TPS would be hospitals. The Allegheny General Hospital has trained their employees to let no problem go unsolved. By examining the way that intravenous lines are inserted they were able to reduce infections by 90% in just 90 days after instituting new procedures resulting in savings of $500,000. (Wysocki Jr., 2004) In analyzing the infections it was found that femoral intravenous lines had the highest rates of infection. The directive was made to use this site for intravenous lines only if there was no other alternative. The application of Root-Cause-Analysis is obvious. The monetary impact is quantifiable but the human factor is priceless.
Well known window and door maker Pella Corp. adopted the TPS many years ago. They recently "loaned" some of their employees to a local hospital. In a billing example a mapping process was done and it was found that billing insurers could be reduced from 14 to 11 days just by changing the process by which follow up calls were made to discharged patients. Everything can be mapped and questioned. How much inventory really needs to be in the pharmacy? (Wysocki Jr., 2004) The idea is to find the smoothest workflow. Mapping processes and ferreting out waste can reduce inventories, reduce waiting time, and prepare operating rooms faster with fewer errors. The customer (the patient) must always be the focus.
Order custom essay Toyota Production System in Action with free plagiarism report
At a meal therapy program in Montana health care workers were frustrated because they only had 20 out of 45 minutes time to spend with patients administering care. Not only was this a human interest concern but the time lost in setting up for the next patient was non-billable time. By systematically studying the way time was used it was possible to reduce wasted time so that quality time could be dedicated to the patient.
The current state was mapped, root causes of problems identified and countermeasures enacted. In this example it was found that some steps of setting up were duplicated by technicians, therapists and other workers. It was also determined that "kits" could be pre-arranged to reduce some of the set-up time. The analysis was done on an "A3" report. (William Inman, 2006) An A3 report is a paper on which a full report is documented. On this one piece of paper must be the problem, the current situation, the root cause, alternative suggestions, recommended solution and cost benefit analysis. Why A3? This is the biggest size that can fit in a fax machine (11x17 inches). (Jeffrey Liker, 2004)
The service industry is actually looking to the manufacturing sector to gain insight into how the TPS can work for them. Hospitals have even used unlikely sources such as Ariens, a well known producer of lawnmowers and snow blowers, to model after. (Marybeth Matzek, 2006) An important difference in operating philosophy is how Toyota treats suppliers. A common practice of American based companies is to push cost cutting mandates to their suppliers.
At Toyota a collaborative approach is taken which they believe brings more value to the final customer than harassing the supplier just for cost savings. At Toyota it is believed that working with the supplier on methods to reduce defects and to find mutually beneficial strategies will ultimately strengthen both parties. To build this collaboration Toyota has even formed an on-site supplier park at its Texas facility capable of housing 21 various suppliers. (John Teresko, 2006)
Toyota Production System Summary
So why does the TPS system work for Toyota but not for everyone? The simplest explanation is that the TPS or similar system of continual improvement cannot be confused with the individual tools utilized and perhaps most important is that the culture of the entire company must make a permanent change. Lean or the TPS is easy to understand but it takes commitment starting with management. A master plan should be developed outlining training and the cultural change within the organization. Company goals have to be aligned with individual and team goals. A plan needs to be in place to address the fears of downsizing. (George Alukal, 2006) "Kaizen consciousness" must be on the mindset of all employees. (Making Things: The Essence and Evolution of the Toyota Production System, n.d.)
In a global economy some industries in America have reengineered themselves with specific players emerging stronger than ever before. There are examples found in the steel industry. Other industries have not managed to do so and have vanished from the manufacturing landscape of the United States. The textile industry is gone. The auto industry is currently being put to the test. (John Teresko, 2006) It seems that Toyota with their Toyota Production System will be one of the strong survivors. But true to the Toyota way "The biggest problem is thinking you are okay". (Making Things: The Essence and Evolution of the Toyota Production System, n.d.)
What a Hybrid Is Any vehicle that combines two or more sources of power that can directly or indirectly provide propulsion is a hybrid. (How Hybrid Cars Work, n.d.) In today's automobile society, the most typical hybrid in use is a gasoline-electric combination. A gas-powered vehicle has a fuel tank, which supplies gasoline to the engine, which turns the transmission that turns the wheels. An electric car, on the other hand, has a set of batteries that provide electricity to an electric motor that turns the transmission, which turn the wheels. The concept behind the hybrid is a compromise; it attempts to increase mileage and reduce emissions in a standard gasoline combustion engine, and make the battery of an electric car more practical while maintaining low emissions.
In most recent years there have been just two forms of gas-electric hybrids available: Parallel and Series. A parallel hybrid provides power to both the gas engine and electric motor with the capability of utilizing both sources simultaneously to turn the transmission. In a series hybrid, the gas engine turns a generator, which charges the batteries or powers the electric motor that drives the transmission. Thus, the gas engine never directly powers the vehicle. The main reason why hybrids are capable of high mileage per gallon averages is because of its partial use of an electric motor. (How Hybrid Cars Work, n.d.)
Cite this Page
Toyota Production System in Action. (2018, Sep 24). Retrieved from https://phdessay.com/toyota-production-system-in-action/
Run a free check or have your essay done for you
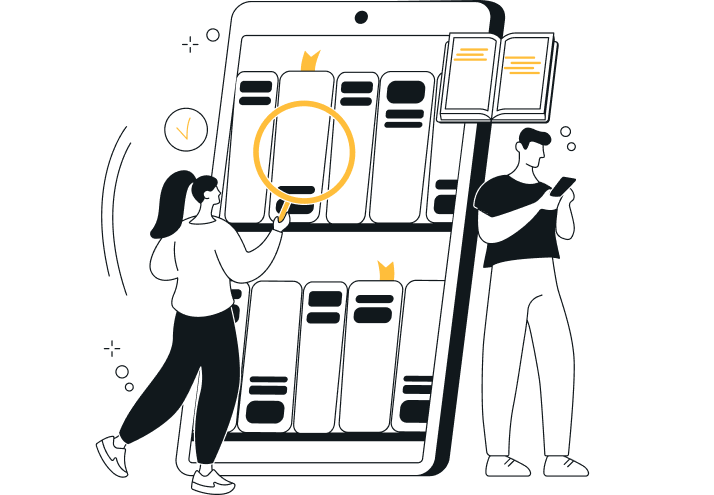