The Importance Of Wind Turbines Engineering Essay
- History of air current turbines
- Modern twenty-four hours wind turbines
- Example of a typical HAWT
- Tip velocity ratio can be defined as the ratio of blade tip velocity to weave velocity
- Lift, Drag, and Pitching Moment
- Betz bound
- Blade Element Momentum theory
- Power and Thrust Coefficient
- Blade Elements
- Tip losings
With world-wide energy demands invariably on the rise, the demand for sustainable green energy beginnings is going of all time more of import. Global population growing and emerging developing states paired with an exhaustible supply and changeless addition in monetary value of the universe 's fossil fuels is doing an increased involvement into alternate energy beginnings. Based on current ingestion of the universes fossil fuels an appraisal of the length of clip staying before each modesty runs out, taken from ; World Fossil Fuel Reserves and Projected Depletion, Colorado River Commission of Nevada, March 2002, can be seen in table 1.
Even though these appraisals do n't take into history the find of new fuel militias and the outgrowth of new more efficient dodo fuel energy engineerings they still give a image of why investing and research into sustainable engineerings is going of all time more extended and popular. Figures show that in 2011 the planetary air current power market grew by 20 % with a world-wide investing transcending 50 billion.
Wind power engineering is quickly going one of the most popular alternate energy beginnings for several grounds:
Order custom essay The Importance Of Wind Turbines Engineering Essay with free plagiarism report
- It is environmentally friendly and will greatly cut down C dioxide emanations
- Contrary to popular belief, wind turbines are going more and more efficient at change overing energy and hence more cost effectual
- Wind power unlike fossil fuels is an unlimited beginning of energy and is readily available all around the universe.
- Low running costs one time wind turbines have been set up and a comparatively little required work force compared with conventional energy engineerings.
- Much safer than dodo fuel combustion and atomic power works
History of air current turbines
Worlds have been tackling the power of the air current for 1000s of old ages. The earliest hint can be dated as far back as 4000BC where the ancient Chinese began utilizing the air current to power canvass attached to their ships. Other than sailing, the air current has influenced much technological promotion. It has played an of import function in agribusiness, where windmills have been used to crunch grains and irrigate Fields.
It wasn't until the last 150 old ages that wind power has been used to change over kinetic energy into electricity. The first of all time automatically operated air current turbine in the universe was built in 1888 by Charles Brush. It consisted of 144 blades and was able to bring forth 12 KW of power used to bear down batteries. But it wasn't until ww1 and ww2 where air current turbines were used commercially as a beginning of energy, peculiarly in Denmark as it was cut off from oil supplies from the remainder of Europe.
After this period research and involvement in air current engineering was non sustained due to the belief that it was non cost effectual. Although there was small planetary involvement in air current engineering at this clip some research was still carried out by independent developers, most notably the design of the 200KW Gedser air current turbine in Denmark. This was a pioneering design consisting of three flying blades and flying tip interruptions and is mostly considered be the trademark of all modern twenty-four hours wind turbines.
It wasn't until the 1972 oil crisis that wind power began to come into fruition with Denmark and the USA taking the manner in invention.
Modern twenty-four hours wind turbines
Modern twenty-four hours wind turbines differ greatly from Charles Brush 's 144 blade turbine both in aesthetics and public presentation, but the rule behind bring forthing electricity is the same. Aerodynamic lift forces caused by the air current blowing past the blades cause them to revolve a shaft and in bend power a generator which converts this mechanical power into electricity.
The air current turbines can be split into two classes:
- HAWT; horizontal axis air current turbines, these are turbines which axis of rotary motion are horizontal, and VAWTS; perpendicular axis air current turbines, these are turbines which axis of rotary motion are perpendicular.
- There are advantages for utilizing either for case the VAWT in nonwind way orientated and does non necessitate to confront the way of the air current whilst HAWTS do, but HAWT's are much more economical and practical than VAWT 's and besides produce more power. HAWT's are by far the most common constellation of air current turbine and therefore for the intent of this thesis merely HAWT will be discussed.
Example of a typical HAWT
When planning a HAWT there are several factors that have to be taken into history:
The HAWT design can be split into four different subsystems:
- Turbine rotor subsystem
- Power-train subsystem
- Nacelle subsystem
- Tower subsystem
The design of the rotor subsystem if frequently considered the most of import, as it straight affects the cost, efficiency and public presentation of the air current turbine. When planning a rotor subsystems there are several facets which must be examined:
From flying tip to root, the form of the rotor blade does non stay changeless. The tip of the blade is much narrower than the root. This is because of demand for the root to structurally back up the remainder of the rotor blade. Besides the farther off from the root the greater the additive velocity, purchase and the greater the part toward the blades rotation. Power force ten velocity This means that points nearer the shaft have less of an consequence on rotary motion, and hence holding a thicker less aerodynamically efficient blade subdivision at this point will non hold every bit serious effects as it would at the tip.
Unlike a typical aeroplane flying blade a air current turbine blade has a just sum of turn. Besides unlike an aeroplane wing, turbine blades undergo rotational motion doing this demand for greater turn. Turn of a turbine blade is when the tip is non parallel to the root. As mentioned before the tips of the blade have a greater additive velocity than closer towards the root, but the air current velocity along the full blade remains changeless. Due to the comparative velocity non staying changeless along the blade, holding the same angle of onslaught throughout would intend different points along the blade meeting the air current at sub-optimal angles of onslaught with hapless lift to drag coefficients. Therefore to do the angle of onslaught relation to the way of wind the same throughout the full blade, a turn angle must be implemented.
Modern twenty-four hours HAWT most normally have merely two or three blades, although they would still work with a smaller or larger figure of blades, but these constellations are uncommon. It is mostly considered that three blade turbines are the most effectual with the best combination of balance, efficiency, and aesthetics.
Blade pitch is the angle between the blade chord line and the plane of rotary motion. Pitch mechanisms allows for a manner to command the starting torsion, peak power, and halting torsion of the turbine. Most big air current turbines have a pitch mechanism integrated into the design, but due to their cost some smaller turbines have fixed pitch. Some wind turbines may besides hold tip interruptions. These halt the rotor rotary motion by turning the tip of the blades to right angles with the way of gesture, doing an addition in retarding force.
Choosing the right stuff for the design is of import, depending on the rotors size and design a stuff with equal strength, stiffness, weight and cost must be found.
Early on air current turbine rotor blade designs consisted of wooden complexs and lightweight metals. Most wind turbines today use either fiberglass or plastic complexs for building due to their low costs, strength and weariness features.
Consists of a series of mechanical and electrical constituents, to change over mechanical power caused from the rotor to electrical power. It includes ; low velocity and high-velocity thrust shafts, a gearbox, an electrical generator and a rotor brake every bit good as subsidiary equipment. This is done by reassigning mechanical energy from the low velocity thrust shaft attached to the rotor, to a high-velocity thrust shaft to power a generator.
The nacelle is the lodging to all of the power train subsystems every bit good as the gaping systems. It must protect these systems from all conditions every bit good as act a primary burden way from the shaft to the tower.
The ability for a turbine to gape is of import. A turbine turned at 90 deg; to the air, current will bring forth no lift and hence no rotary motion, whilst if it is at 0 deg ; to the air current it will bring forth the maximal sum of lift and maximal rotary motion. Yawing is of import in acquiring maximal power out of a air current turbine and even gaping a twosome of grades to confront the air current will profit.
Modern air current turbines have a yawing mechanism to let, non merely for the turbine to confront the air current but when in non in operation to confront 90 deg ; to the air current to halt rotary motion.
The tower raises the nacelle and the rotor off the land. The tallness of the tower is dependent on geographical location and the trade of between increasing the tower tallness to make more powerful air currents and cost. The tower must be structurally really strong and stiff both to back up the nacelle and rotor, every bit good as withstand quivers caused by the rotor. Towers are normally made from steel or reinforced concrete.
The velocity in which the blades rotate is an of import factor to see. If the blades rotate excessively easy so most of the air current will go through between them undisturbed with really small energy extracted. If excessively fast, so the blades will be whirling through disruptive air caused by the other blades, every bit good as doing the turbine to be put under increased emphasis which could take to mechanical failure. Wind turbine blades are hence designed to revolve with an optimal tip velocity ratio to pull out the maximal energy possible from the air current.
Tip velocity ratio can be defined as the ratio of blade tip velocity to weave velocity
The tip velocity ratio is straight affected by the figure of blades of a turbine, the fewer the figure of blades the faster the rotary motion velocity will necessitate to be to pull out maximal power. For three bladed air current turbines the tip velocity ratio is by and large in the scope of 6-8 with 7 being the most common value ITECHOPEN.com pg Betz one pg 29 Generally interior decorators will take to maintain the tip velocity ratio every bit high as possible to increase the velocity in which the shaft connected to the generator spins, but higher tip velocity ratios besides have several disadvantages:
- Increased tip losings ensuing in decreased efficiency
- Increased noise
- Increased quiver
- Erosion caused by dust atoms
- Efficient airfoil design is hence particularly of import to let for higher optimal ratios to be met whilst restricting these negative effects.
Lift, Drag, and Pitching Moment
The lift, retarding force, and pitching minute are all moving on an air current turbine rotor blade. And figure shows the orientation of these. Lift is the force moving perpendicular to the oncoming airflow and is required to get the better of gravitation.
The retarding force acts perpendicular to the life force and hence parallel to the oncoming airflow. The retarding force is a combination of the syrupy forces between the air and the airfoil, and the force per unit area differences over the airfoil ensuing in whirls.
As mentioned by Hansen, 2008 pg 8 the lift to drag ratio should be maximised to acquire a more efficient airfoil. The coefficients of lift and retarding force can be defined as:
- Where is the air denseness and is the length of the airfoil chord. These coefficients are maps of Reynolds figure, Mach figure and angle of the onslaught.
- To full depict the forces it is necessary to cognize the pitching minute about a point of the airfoil. As stated by Hansen 2008, pg 8 This is located at a distance of length along the chord line from the taking border. It is defined as:
Betz bound
The Betz bound was foremost introduced by German applied scientist Albert Betz in 1919 and is the maximal theoretical power that can be extracted from an air current watercourse. Harmonizing to Intechopen.com pg 26 for maximal energy extraction the downstream speed should be equal to the upstream speed, therefore the optimal value for the power coefficient will go:
This value is about and is known as the Betz bound. Using this standard a value for air current turbine efficiency can be defined as the ratio of power coefficient to Betz bound:
Hansen 2008 pg 40 shows how the maximal efficiency is affected by the tip velocity ratio. For low tip velocity ratios, the efficiency will be decreased for illustration, a tip velocity ratio of 1 will give a maximal efficiency of about 70 %, whilst a tip velocity ratio of 10 will give a maximal efficiency of about 98 %. This shows that air current turbines' higher tip speed ratios can pull out more energy and therefore a higher tip velocity ratio is a coveted feature.
Blade Element Momentum theory
Blade component impulse theory is a combination of two air current turbine analysis methods. The 1st method is to execute impulse balance equations on a revolving annulate watercourse tubing that passes through the turbine. The 2nd is to analyze the forces generated by the lift and retarding force coefficients along the blade by dividing it into subdivisions.
- Assuming an air current turbine as being in a control volume disc actuator theoretical account as seen in the figure.
- This is a really basic theoretical account that assumes no aftermath rotary motion.
- Stations 1, 2, 3, and 4 are at places upriver of the turbine, merely before the turbine, merely after the turbine and downstream of the turbine, severally.
- Between Stations 2 and 3 energy is extracted from the air current ensuing in a force per unit area alteration. The mass flow rate of the control volume must stay changeless harmonizing to the continuity equation:
Besides if we assume continuity of speed through the turbine so and because the flow is frictionless so we can use Bernoulli's equation between 1and 2, every bit good as 3 and 4 giving up:
Uniting these equations gives:
- As force is equal to coerce clip's country so the push generated by the turbine can be calculated as:
- The axial initiation factor is a factor of variation of the cross-sectional country of the turbine blade which varies as a map of flow speed.
It can be defined as:
Therefore:
- If this is substituted into the trust equation it yields:
- Using this equation the power end product of the turbine can so be found by specifying it as thrust times speed. Therefore:
Power and Thrust Coefficient
The power generated by the kinetic energy of the air current fluxing at a air current turbine can be defined as:
The public presentation parametric quantities of a air current turbine can be characterised by the power and thrust coefficients. Where the coefficient of power is the ratio of power generated by the air current turbine to power available given by:
Similarly the thrust coefficient can be defined as:
Harmonizing to the Betz limit the coefficient of power can ne'er transcend a value of. These public presentation parametric quantities can be related to the axial initiation factor by uniting with the power and thrust equations severally giving:
Blade component theory involves dividing a blade up into N figure of subdivisions. The fluid flow will be different across each component as they will hold different rotational velocities, chord length, and turn angle. Therefore numerical integrating along the blade p is required to find the overall public presentation.
The comparative air current speed is the vector amount of the horizontal air current speed at the blade, and the speed caused by blade rotary motion. The rotary motion constituent is the vector amount of the blade speed and the rotational flow due to aftermath rotary motion is. To give a more accurate estimation of the airfoil public presentation a norm of the recess and issue is used where is the mean rotational flow due to wake rotary motion.
Blade Elements
From this equation the influence of retarding force can be clearly be seen. An addition in retarding force will diminish the torsion hence the power end product of the turbine. This is why when selecting or planning an airfoil for turbine usage, one of the key aims is to maintain the coefficient of retarding force every bit low as possible while keeping a high coefficient of lift.
These equations can be expressed in footings of initiation factors by replacing equations and simplified by utilizing the solidness factor. The solidness factor can be defined as the ratio of blade country to country of the disc given by the equation ;
The equations can so be written as: These two equations specify the push and torsion moving on an annulate subdivision of the blades severally.
Tip losings
Due to the difference in force per unit area on the top and underside of the airfoil, air flows from the high force per unit area side to the low force per unit area side around the blade tip, cut downing the lift of the blade. To account for this loss of lift and hence power, a rectification factor is implemented. A method of gauging the tip losings was obtained by L. Prandtl and the equation for the rectification factor is: Where is in radians. Equations.
Equations for blade component impulse theory which are used in blade design and optimisation can now be defined by uniting the impulse theory equations for axial push and torsion, with blade component forces equations. These are:
- The entire power of each ring can be calculated utilizing equation
- The entire power from the rotor can be calculated utilizing the equation
- Where is the hub radius? The power coefficient of the rotor can now be calculated utilizing the equation
- Where is the blade tip radius? Using the annulate subdivision torsion equation this power coefficient can be written as
Cite this Page
The Importance Of Wind Turbines Engineering Essay. (2018, Sep 17). Retrieved from https://phdessay.com/the-importance-of-wind-turbines-engineering-essay/
Run a free check or have your essay done for you
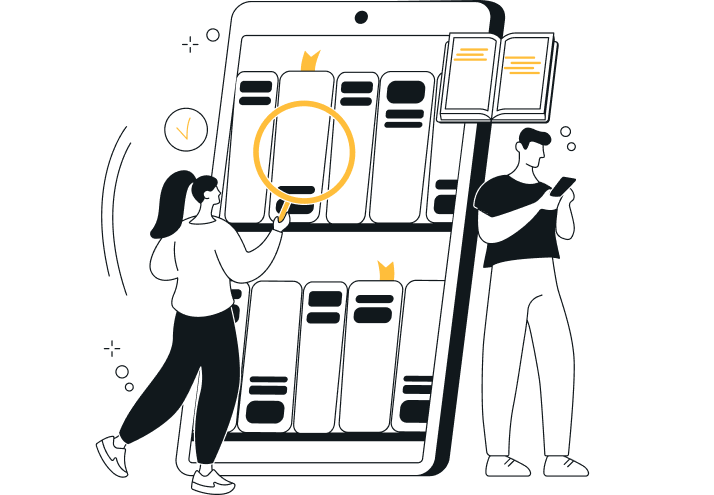