Stress Analysis Of A Imple Suspension System Of Car
The stress analysis of a imple suspension system of car is done in this report which not only provides the reader with the stress calculations but also gives an insight of how proper stress analysis of real life problem can be done by using simple engineering formulas and techniques. Only one member of complete assembly is analyzed in ANSYS and the results were really promising. Acknowledgement:- We are thankful to Dr. Khalid Rehman for teaching us so well that we were able to do the stress analysis of a real life problem.
Without his teachings nothing in this report could be done. We are thankful for his time and help which he always gave during time of any confusion or problem. 1 . Introduction... 2 2. Problem 33. CAD Model Statement ” 34. Manual Solution 7 4. 1. Force Analysis 7 4. 2. Stress Analysis ? 10 4. 3. Failure Analysis 11 4. 4. Deformation Analysis ..... 12 5. ANSYS Analysts 13 5. 1. Messing . 13 5. 2. Procedure 15 5. 3. Results 21 6. Conclusion 25 1.
Introduction:- The deciding step that passes any particular design is its stress analysis which gives the designer an insight that particular design would work or not, whether or not the esign is feasible for fabrication or further improvements are required. Stress analysis of any design not only includes the basic force and stress calculation in members but also the failure, deformation analysis of the complete assembly. Stress analysis can be done manually or by using any CAD tool like ANSYS etc.
Order custom essay Stress Analysis Of A Imple Suspension System Of Car with free plagiarism report
The results obtained from both solutions should match each other but there is always variation in the results. The variations can be due to ideal approximations in the manual calculations or any other assumed data. The report includes the stress analysis of a imple suspension system of a car; various assumptions are being made which are mentioned in respective sections of the report. The solution was done both manually and by using ANSYS and the results were really promising. The report includes force and stress analysis, failure analysis and deformation calculations.
The report not only provides the reader with the stress calculations but also gives an insight of how proper stress analysis of real life problem can be done by using simple engineering formulas and techniques. Stress analysis of a simple suspension system of car. 3. CAD model:- The first step of any design is to make its CAD model which in our case is done by using CREO VI . 0. The Cad models are shown as follows: (Fig 3. 1 complete assembly) (Fig 3. 2 complete assembly) The above fgures show the cad model of whole assembly. The individual member models are also shown below: (Fig 3. 4 Hub) (Fig 3. 5 Connecting arm) (Fig 3. 6 spring) (Fig 3. Suspension arm) 5. ANSYS 5. 1. Messing: The details are provided according to ANSYS 13. 0 Mechanical APDL. Mesh size: smart size 1 5. 1. 2. Element type: PLANE182 2-D 4-Node Structural Solid 5. 1. 3. Element Description PLANE182 is used for 2-D modeling of solid structures. The element can be used as either a plane element (plane stress, plane strain or generalized plane strain) or an axisymmetric element. It is defined by four nodes having two degrees of freedom at each node: translations in the nodal x and y directions. The element has plasticity, hyperelasticity, stress stiffening, large deflection, and large strain capabilities.
It also has mixed formulation capability for simulating deformations of nearly incompressible elastoplastic materials, and fully incompressible hyperelastic materials. The geometry and node locations for this element are shown in Figure 182. 1. The element input data includes four nodes and the orthotropic material properties. The default element coordinate system is along global directions. Element loads are described in Node and Element Loads. Pressures may be input as surface loads on the element faces as shown by the circled numbers on Figure 182. 1. Positive pressures act into the element. 5. 1. 4.
For triangular elements where the or enhanced strain formulations are pecified, degenerated shape functions and a conventional integration scheme are used. 5. 2. Procedure:- Filter GUI for analysis of structural members (Fig 5. 2. 1) Select element type plane quad 4 nodes 182 (Fig 5. 2. 2) Select Linear, Elastic and Isotropic material type (Fig 5. 2. 3) Input youngs modulus of elasticity and Poisson's ratio to define material in Ansys (Fig 5. 2. 4) Mesh the area using the finest mesh for accurate results (smart size 1) (Fig 5. 2. 5) Apply Pressure on line and Restrict DOF for some nodes at the center to compensate
Cite this Page
Stress Analysis Of A Imple Suspension System Of Car. (2018, Jul 30). Retrieved from https://phdessay.com/stress-analysis-of-a-imple-suspension-system-of-car/
Run a free check or have your essay done for you
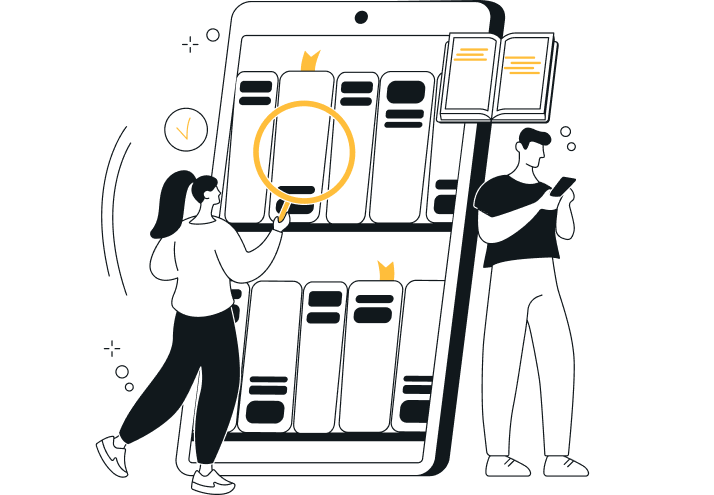