Process variations
For a Q of 113 units the total cots TC = Co D/Qopt + Ch Qopt/2 + PD; where PD is the price * the demand. This will be equal to [(40*400/113) + (598. 5 * 113/2) + (240* 400)] = $129,646. 09. This would be the total ordering and holding cost since according to the discount offered by Kony, any number of units below 1000 would be charged at $ 240. On the other hand, if we were to adopt the Qopt of 170 units; the TC = [(90*400/170) + (598. 5 * 170/2) + (250* 400)] = $151,084. 26. Thus the adoption of the second strategy would have the impact of increasing the total ordering and holding costs (Terspine, 1993).
This further confirms that fact that Kony offers a better supply deal for Steve if he is to undertake proper inventory management (Hamblin et al. 1973). Portfolio Exercise 1: Delta Plastics, Inc. The situation at Delta Plastics Inc clearly highlights the concept of process controls. This implies that the director will have to undertake a sound analysis of the prevailing situation if he is to make a rational decision process controls based on the figures presented (SkyMark Corporation, 2009). This company produces products based on two models; the standard material and the supper plastic.
To make such an informed judgment as to whether the process is fairing well or not, the manager needs to understand and apply the concept of control charts; a statistical technique for monitoring and making improvements in the quality of a given production ( SQCOnline. com, 2007). The concept of control charts is based on the idea that no matter the design of a production process, certain types of variations in measures of output are still bound to occur ( SQCOnline. com, 2007). The rationale is that a process is said to be in control when the causes in the quality process are as a result of random causes only.
Order custom essay Process variations with free plagiarism report
However, where process variations also include special causes apart from the random causes, such a situation is deemed out of control. Basically, a control chart is a representation of process measurements plotted against time. The plotted points are usually compared to the control limits in which case any point exceeding the control limits is considered an alarm (SkyMark Corporation, 2009). There are several assumptions which usually surround the use of control charts. The first assumption is that the mean used in measuring the process performance indicator is normally distributed ( SQCOnline. com, 2007).
The second assumption is than the measurements do not depend on one another. To construct a three sigma control chart, the first requirement is to establish the parameter needed to be monitored which in this case is the number of defects per week of production. Next, it is important to create the baseline of the plot depending on target value of the parameter under control. The next task is to categorize the process measurements in terms of samples or groups by time period (SkyMark Corporation, 2009). The points which are to be plotted will be some functions of the process measurements within each subgroup, determining the target value.
What follows is a determination of the upper and lower control limits (UCL, LCL) (SQCOnline. com, 2007). Eventually, having determined the control limits, the points are plotted as function of time. What needs to be noted here is that a point exceeding the control limits is an indication that the process is out of control thus calling for the need to take an action (SkyMark Corporation, 2009). The figures in the data presented in the case of Delta Plastics Inc represent the total number of each type of defect per week.
For instance in week I, the total number of uneven edges defect is 10 while that of week II is 7. From the presented data (see table in the appendix), we can determine the mean number of defects per week from both models. For the standard model the total number of defects is 193 while the number of weeks is four. Our mean number of defects = [Total number of defects/ number of days] going by the theory of control charts (SQCOnline. com, 2007). This gives [193/20] = 9. 65 per day. The same could be represented in weeks thus, [193/4] = 48. 25.
Cite this Page
Process variations. (2018, Sep 13). Retrieved from https://phdessay.com/process-variations/
Run a free check or have your essay done for you
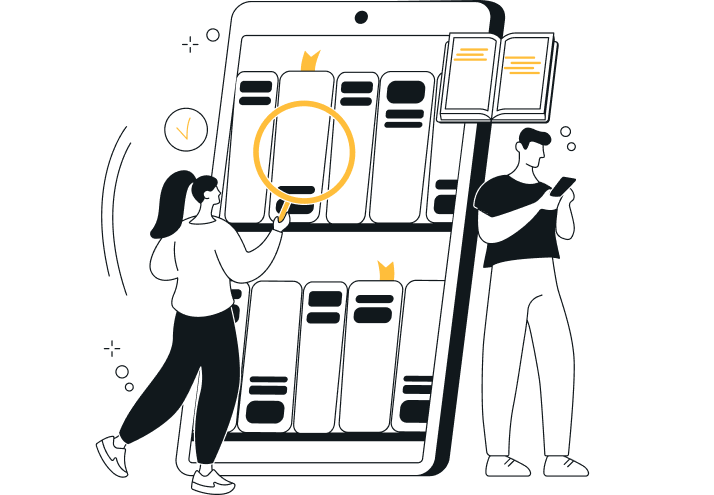