Macro-Scale Modeling
In order to analyse the response of large structures with complex architecture, macro-scale modeling approaches is preferable to save computational time when running a simulation. In general, relying on classical laminate plate theory, macro-scale modelling approach are accessible in most commercial finite element codes like Abaqus and LS-DYNA.
To model a structure with anisotropic properties using macro-scale approach, several material parameters in different directions are needed such as stiffness, Poisson's ratios, strengths and damage parameters. Determination of all of these parameters are either from a number of experimental tests or the results obtained from a meso-scale homogenization. Prediction of the effective properties of the material using analytical methods have been reviewed by Younes.
There are several disadvantages of the macro-scale modeling approach which limit its application. Basically, fiber architecture such as the undulation and intercrossing of fiber tows in the model is neglected in this approach. Hence, detailed stress and strain solution among the constituents and localized damage or failure cannot be provided. Regardless of the drawbacks, macro-scale approach can provide efficient global response for the simulation of composites with different fiber architecture.
Order custom essay Macro-Scale Modeling with free plagiarism report
This is particularly evident when the analysed structure is relatively large. Macro-scale material parameters such as elastic and failure properties are very important in order to provide an accurate solution. Obtaining those parameter is tedious and costly since good experimental support is needed. Consequently, composite structure with less material parameters like transversely isotropic unidirectional composite laminate is favourable for macro-scale modelling.
Y. Shi et al have employed the macro-scale approach to predict the impact damage of composite laminates in the form of intra- and inter-laminar cracking under low velocity impact. Essential features of the model such as stress-based criteria for damage initiation, fracture mechanics techniques for damage evolution and Soutis shear stress–strain semi-empirical formula to capture nonlinear shear behaviour of the composite have been applied.
A good agreement between numerical results and experimentally obtained curves of impact force and absorbed energy versus time have been achieved. Besides, the proposed damage evolution model also able to capture various damage mechanisms that occur after the impact.
Macro-scale FE analysis of carbon fiber reinforced composite plate have been conducted by A. Riccio et. al to predict the damage onset and evolution under low velocity impact. Both inter-lamina (delaminations) and intra-lamina failure mechanisms were predicted using the cohesive elements and Hashin's failure criteria respectively. Moreover, to improve the accuracy of the result, a global–local technique was applied to refine the mesh in the impact zone. Comparisons between numerical and experimental results under different impact energies in terms of global impact parameters, maximum impact force, maximum impact displacement are found to be in fair agreement.
D. Feng et. al examined the structural response and the failure mechanisms of the composite laminates subjected to low-velocity impact using the macro-scale technique in combination with the constitutive models for intralaminar and interlaminar damage modes. The results of numerical simulations were compared with experimental data obtained by drop-weight impact testing and stereoscopic X-radiography. Both the structural impact response and the major damage mechanisms over the range of impact energies provided by the numerical FE model shown a reasonable good agreement with drop-weight impact testing data.
H. Ullah et. a conducted the experimental characterisation and numerical simulations on the deformation behaviour and damage in woven CFRP composite laminates under quasi-static bending. Two-dimensional macro-scale models are developed and numerical results showed that damage initiation and evolution processes in woven laminates are in agreement with experimental data.
Yumin wan et. al studied the mechanical properties and failure mechanism of three-dimensional (3D) braided composites subjected to compressive quasi-static and high strain rate loadings. Both meso- and macro-scale model integrated with strain rate sensitive elasto-plastic constitutive relationship and ductile and shear failure criterion were developed.
Experimental data was used to verify the results obtained from both models and the results are promising. A macro-scale model of woven composite has also been developed by Xiao et. al using LS-DYNA to simulate the onset and evolution of damage. Remarkably, failure mechanisms under different type of loadings including tensile, compression and shear can be predicted with this model
In summary, even though the macroscale modeling approach is incapable to predict the behavior of the reinforcement, matrix or fiber-matrix interface, with its homogenization feature, it can act as an effective first level overall solution in the modeling framework especially for impact simulation of a large scale structure.
Prediction of detail local failure is only applicable for micro- and meso-scale model approach. Besides, higher scale model can exploit the effective material properties obtained from both methods. To be brief, a comprehensive evaluation of material failure responses can be achieved through combination of micro-meso-macro scale approaches
Cite this Page
Macro-Scale Modeling. (2019, Mar 25). Retrieved from https://phdessay.com/macro-scale-modeling/
Run a free check or have your essay done for you
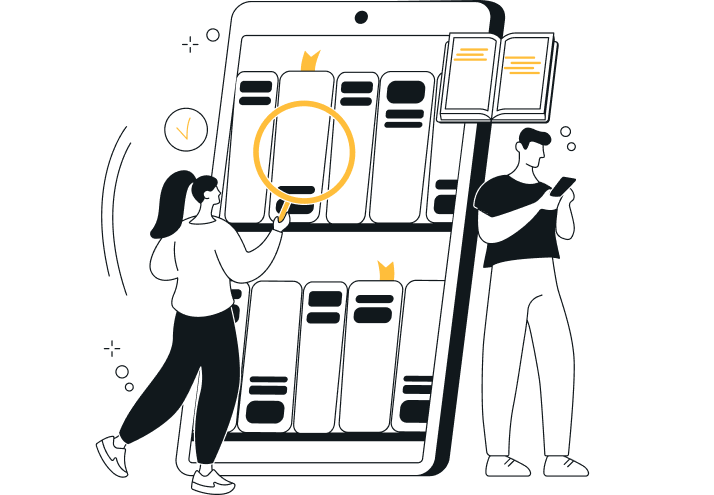