A Case Study of the Glass Bangle Industry
The glass manufacturing industry in Ferozabad, Uttar Pradesh, produces bangles, utensils, bulbs, decorative articles etc. The glass industry has been classified as hazardous and the employment of child labour (children below age 14 years) in it is prohibited. However, available research and literature indicated that child labour was concentrated mainly in the production of glass bangles. At the time of the present study over 50,000 children were generally believed to be engaged in the hazardous glass bangle industry of Ferozabad.
The process of manufacture of glass bangles is broken down into six separate stages and each stage is done by a separate specialized enterprise. At the first stage, the spring bangles are produced at a glass factory and it involves work at the furnace and handling, coloring, and shaping the molten glass into a spring form or rings. The subsequent processes like straightening, linking up the edges of the glass spirals, joining the edges, hardening them, cutting designs into them and coloring the bangles are done in separate stages by small informal sector enterprises using different tools like kerosene lamps, abrasive wheel, mud oven, and chemical colors for each of the processes.Unlike glass factories, these small informal sector enterprises are not registered and difficult to observe as they are often located inside households and in small alleys. Moreover, the Child Labour (Prohibition and Regulation) Act of 1986 does not cover the informal sector.
Order custom essay A Case Study of the Glass Bangle Industry with free plagiarism report
OBJECTIVES AND METHODOLOGY
The study aimed to document the extent of child labour, types of activities
in which children are engaged, employment conditions , and the cost implications of eliminating child labour. Data collection involved an enterprise survey. As the production process for glass bangles involves a number of different and distinct stages, enterprises were chosen from individual stages of production to ensure a representative selection. In all 268 enterprises with 4100 workers and approximately 1000 child labourers were covered.
Anticipating that the information furnished by the employers on child labour and the number of children employed may be misleading or grossly understated, field investigators were trained to distinguish children from adults through observation. As this was still difficult to do for children in the 12-16 age group, investigators were allowed to record their observation in either of the three categories ‘definitely adult’, ‘definitely child’, or ‘probably child’. The category of ‘probably child’ was used when an investigator could not decide if a worker was a child.
KEY FINDINGS
The total number of child labourers employed in the glass bangle industry was estimated on the basis of the number of children employed in different stages of production. Of the approximately 60,000 workers in the glass bangle industry, 9,40011,000 are children constituting about 16 to 19 percent of the workforce in this industry. Employment of children was confined mostly to unskilled jobs like carrying and sorting in the glass factories. Within the stages of production where several different activities are performed, children do the least skilled of these activities (see table). In other words, children do not have unique or irreplaceable skills and are therefore not necessary for the glass bangles industry.
The daily productivity per worker is between 12 to 32 tora (312 or 13 double dozen) bangles per day for different production stages. Children are commonly said by employers to work slower and take longer hours to achieve the same output as their adult counterparts. Each enterprise is paid on a piece rate basis. The wage payment system has a very strict control of the output.
Teams of workers must achieve a prescribed minimum level of output in order to be given the agreed daily payment, and it often takes more than eight hours to achieve this minimum acceptable output. Since children are said to work slower than adults, they generally need to work longer hours than Working conditions & Health hazards adults in order to achieve the same output and therefore As ‘carriers’: the same daily income. carrying molten glass from the furnace to the Working spaces are small and cramped. Burns and respiratory problems are common occupational health hazards (see box). Several young males and adults were observed without the thumb or forefinger. Tuberculosis is a very common health problem in Ferozabad.
Payments to child labourers are estimated to account for only about 15 percent of the total labour cost and so about 4 to 7 percent of the cost of producing a glass bangle. shaper or loom maker, constant exposure to the heat, sound and pollution. Straightening: work in closed rooms, no cross ventilation and are continuously exposed to smoke emitted from dozens of kerosene lamps. Joining and cutting: long hours of sitting in one posture, risk of cramps; continuous exposure to smoke from the kerosene lamps.
Colouring: high toxic effect of chemical-based colours, handled with bare hands; colours stick to the fingers and palms and are difficult to remove. The increase in the cost of production of one dozen bangles (as most consumers buy bangles by the Hardening: dozen) as a result of elimination of child labour was working around a small furnace and hot trays; calculated in three different ways based on three burns are common. different assumptions.
If a sufficient number of adult workers from the large labour reserve in India are available and willing to work at the present, market determined wage rate , there would be no cost effect, as adults would replace children at the same piece rate payment. Assumptions 2 and 3 presuppose that adult workers would need to be paid a higher wage (10 and 20 percent, respectively) in order to attract the additional adult workers required to replace the child workers. In that case, production costs go up by only about 2-3 paise a dozen for plain bangles and 6-12 paise for coloured and detailed cut bangles.
In percentage terms, this would mean only a 0, 2 and 4 percent increase in the cost of glass bangles in all three scenarios. Even at the retail level (which we assume has a 200 percent mark-up compared to wholesale), the cost of a dozen glass bangles would go up by only 10-20 paise for plain bangles and 12-27 paise for coloured and detailed cut bangles. There is no economic justification to employ child labour in the glass bangle industry, as children do not occupy a necessary role in the glass bangle production, nor do they have the skills that could not replaced by adults, and elimination of child labour would increase the cost of production only marginally.
RECOMMENDATIONS
Improve production technology and work environment of the glass bangle industry. In the shortrun, the health of those children who continue to work would improve. In the long run, the demand for child labour should decrease as the increased capital investments made would create a need for more skilled and responsible adult workers. The number of adult labourers interested in doing this work should increase along with improvement in working conditions and increased wages resulting from the need for greater skills and responsibility. Thus it will have a favourable impact on the goal of eliminating child labour.
Related Questions
on A Case Study of the Glass Bangle Industry
Cite this Page
A Case Study of the Glass Bangle Industry. (2016, Jul 16). Retrieved from https://phdessay.com/a-case-study-of-the-glass-bangle-industry/
Run a free check or have your essay done for you
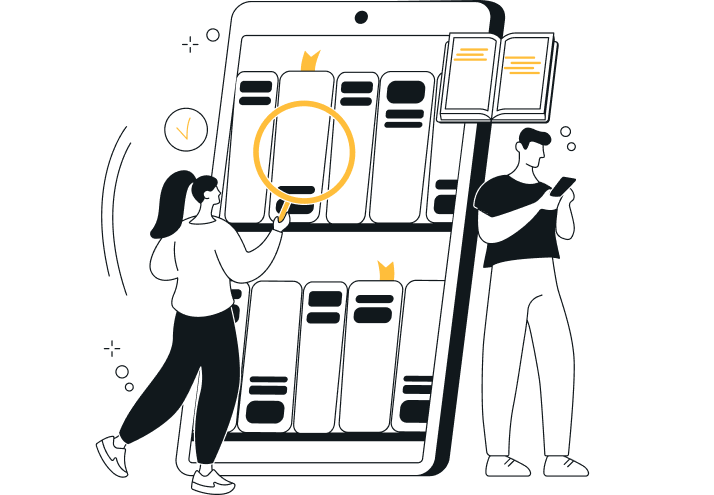