Tools for Problem Solving and Process Improvement in Quality Ice Cream Company
During the problem solving process, Quality Ice Cream Company will need to have a structured approach to determining a solution. There are seven tools that Quality can use to improve their processes during production of the ice cream. These tools are: flow charts, run charts, process-control charts, check sheets, Parent diagrams, cause-and-effect diagrams, and scatter diagrams (Shower, p. 182). Each of these will help the identification of the variation that is happening and will also aid in the analysis, documentation ND organization of the information.
This will help with process improvement. "They are simple but powerful tools that can be of significant value throughout the problem-solving and continuous-improvement processes (Shower, p. 183). " The first place for Quality to start is with a flow chart. The flow chart can show the relationship between the activities and tasks for each process, and give a better idea of how the rejections are happening. Next, a scatter diagram can be run from the data collected.
This will show the link between he run time and viscosity of the ice cream. This type of tool can also determine how long the ice cream should be mixed to avoid soapiness and stiffness. From the ten days of data collected, it seems as though the run time is too short resulting in a too soupy mixture (Shower, p. 201-202). After a more suitable run time is determined Quality can then look into the other problems causing the rejects. Aside from the soapiness causing most of the rejects, there are other problems.
Order custom essay Tools for Problem Solving and Process Improvement in Quality Ice Cream Company with free plagiarism report
Cite this Page
Tools for Problem Solving and Process Improvement in Quality Ice Cream Company. (2018, Apr 04). Retrieved from https://phdessay.com/sour-grapes/
Run a free check or have your essay done for you
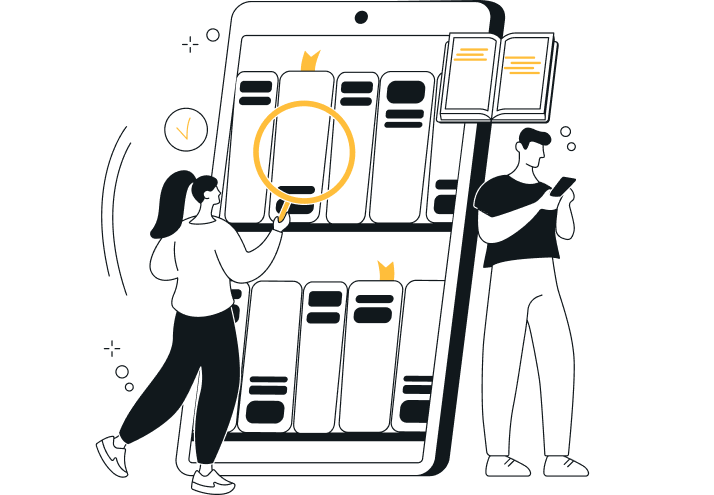