Selection, Hardware and Software Requirements of a PLC
Understand the selection, hardware and software requirements of a PLC There are 3 types of PLC, unitary, modular and rack-mounted. A unitary PLC Is a stand alone unity, it has no room for expansion and works on Its own. They are useful for automating activities such as stress testing. For example the stress testing of a hoist, Instead of paying someone to manually control the hoists up and down movement leaving time In between each motion a PLC could be used Instead. It could be set up to perform a number of cycles of movement of the holst by the use of Ilmlt switches t the top and bottom of Its movement to detect when to change direction.
The time to walt between movements can be set so that the motor doesn't get strained. Other safety features could be added, for example, a set of sensors could be installed around the hoist to stop it's movement if some one comes too close to it. It would also be easier to set the parameters of the test and change them easily for testing a different hoist or piece of equipment. It would have to keep its functionality to a small scale as it can't be upgraded at all. A large variety of inputs and outputs could be sed as most PLCs support analogue and digital.
This would mean you could have temperature sensors in use on the analogue and through-beam sensors on digital. It is likely that this type of PLC would be mounted somewhere near the object it is controlling, most likely to a nearby wall. A modular PLC allows for other modules to be connected to it increasing its functionality such as position sensing, stepper and servo motion control and packaging and press controls. Where it may have only had the ability to handle a certain amount of functions adding more increases this. The two or more connect ogether and act as if they still Just one.
Order custom essay Selection, Hardware and Software Requirements of a PLC with free plagiarism report
This would be useful for a company that uses a greater amount automation than the above company, perhaps for a conveyor belt system that is wanted to be upgraded in the future and with modularity more modules could be added to allow for the extension of the conveyor belt and the new Inputs and outputs that are required. For example a bottling company may only just fill bottles but not label them, they could extend the conveyor to allow for them to print and attach labels to the bottles as well which would require a lot more sensors o detect the location of the bottle and outputs for controlling the labelling machine.
Individual parts of the PLC can also be swapped out such as the power supplies and CPU, Central Processing unit, handles the programming and Interpreted the Inputs/ outputs. A rack-mounted PLC is very similar to a modular PLC with the ablllty to upgrade and change different parts of it but they are on standard cards that slot into standard more can be fit into a cabinet due to their design to fit closely with similar units. They are most likely to be used on large assembly lines with a wide range of equipment in use simultaneously.
They can be upgraded to allow the line to run better with more memory and faster CPU to better work with the large amount of things happening. The racks with the PLCs in are likely to be kept either in the factory control room or their own individual room specifically for them. Cost is the most important aspect to selecting the right PLC and the lowest cost PLC is the unitary because it is as it is. It can't be modified in anyway they can get expensive though as the specifications increase.
Next up is the modular PLC which can be quite large to allow it to be upgraded with more memory, faster CPU and greater power upply. The most expensive are the rack mounted PLCs. They are much smaller than the modular PLCs but still retain the ability to be upgraded allowing you to have more powerful PLCs in smaller space. A robotic arm inside a cell would need to perform the same task continuously and because of this a PLC could be used.
Using a series of limit switches to control when the arm moves there wouldn't be a problem because it would be able to stop before hitting any obstructions that may be in the way. For example a series of optical sensors would be able to detect when the item to be manufactured as entered the ell and is in the correct position for the arm which would allow the arm to pick it up and perform what it had been programmed to do. Be it to spray paint on it or to add something onto it, because those motions do not need to be dynamic a single program would be enough to manage it.
The software requirements could be quite large depending on the complexity of the task and the robotic arm If there are a lot of joints on the arm that are controlled by motors then the program will need to control each one independently and add to the fact the movements required then it is quite complex set of instructions the arm requires because of this it will need a large amount of memory and a fast CPU to execute the commands quickly as it is likely that the manufacturing cell is required to get through a lot of items a day.
This would most likely rule out the use of a unitary PLC because the cost would be too great for one with the required specifications. It is also likely that a large amount of robotic arms would be in use so a rack mounted system would be more space efficient, they do cost more than modular PLCs but keeping all the PLCs in cabinets near each other n a neat and organised manner can make it easier for any maintenance required on them. They would need to be near enough to a computer to program them and update software when necessary.
The computer could be in a completely different room as a ethernet cable is used to load the new software into them but having one nearby would make it easier for any quick alterations to the software needed in the likely that the operator would use a proprietary piece of software to program the PLC with, if they were from Siemens they would be programmed in Ladder Logic. A PLC would be very useful for this type of activity because it is repetitive, the same item would be having the same thing done to it.
A PLC controlled arm doesn't need breaks, if set up properly, so it could take the place of a human and thus save money. A problem though is that the item that comes into the cell could have a defect on it that wouldn't be noticed by the sensors in use so whatever the arm does may be done to something that needs to be scrapped. That is something a human worker would have noticed and would have thus saved money by not doing anything to it.
The main benefit of having a PLC control it is that the Job is done autonomously and would be more cost effective than employing a human to do it but you lose out on the fact the human can see what they are doing and ensure that the item entering the cell is correct and make sure he does his Job completely before sending it out, if it was spraying they would be able to check the coat is even and well done by eye where you would not get that from a PLC.
Stricter control further down the line would eliminate this though. Immediate costs would be expensive with a PLC solution, the obotic arms that are going to be controlled need to be bought, the PLCs need to be bought, mounted and wired, someone needs to write the software for them and then maintain their operation. That position would likely be a higher paid position than someone working on the assembly line.
Those that do work on the assembly line do not have as high start up costs but the costs are continuous plus allowance for tools and equipment needed such as PPE. Which leads on to the potential cost each has. If a robotic arm breaks it could potentially lead to the whole line being stopped while it s repaired, both of which will cost time and money.
If a worker was to not be wearing the required PPE or Just sustain an injury it could mean that the line has to stop although he would be quickly replaced to keep the line running. There is also a possibility that the person that was injured might file claims against the company that could lead to a large loss of money. The expansion of what the PLC controlled could be very costly as it would require new equipment and wiring which could mean that parts of production need to be shut down for it to be laid.
Cite this Page
Selection, Hardware and Software Requirements of a PLC. (2018, Jul 31). Retrieved from https://phdessay.com/selection-hardware-and-software-requirements-of-a-plc/
Run a free check or have your essay done for you
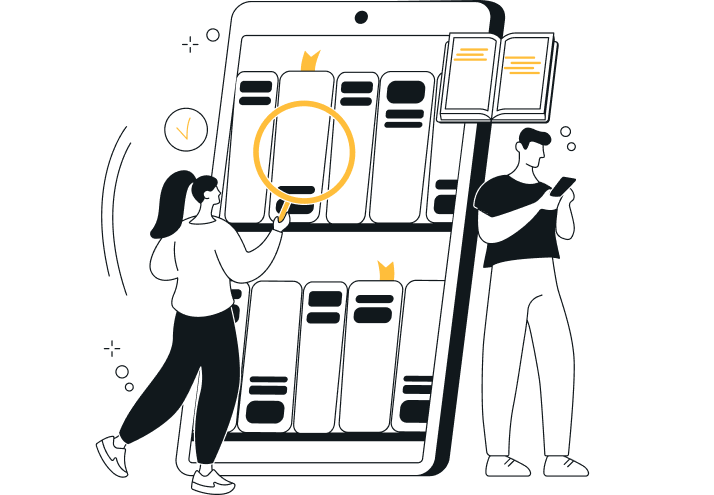