Replacement of Kiln Shell
Everything must be properly placed so that the next step, shell removal, goes aimlessly. Once the kiln shells lengths, weights, cribbing and crane requirements are determined, the shell layout can begin. The ultimate goal is to cut the shell, at the proper location, perpendicular to the centerline of the kiln.
Best ways to do this is to
- Perform a series of stop cuts in the kiln as it is rotating,
- Paying special attention to keep the thrust tree against the thrust roller and also against the same set of tree retainers. Once the cuts determining the overall length are complete,
- A relief cut must be laid out.
Order custom essay Replacement of Kiln Shell with free plagiarism report
This is usually 10-inn wide section on one end ND, once removed, will provide some extra room for removing the shell. Finally, the kiln must be parked and the drive locked out, the support cribbing raised into position, the relief section cut out by hand and the kiln pushed apart by 1-1. In to allow extra room to get the new shell back in. Shell removal with stop cuts in, the cribbing up and the relief section removed, it is time to rig the shell pieces for removal.
Typically, a spreader beam is used to provide more leeway and control while removing a section. Under the spreader beam, braided cables can be shackled together through the clearance holes that eve been cut in the kiln and reinforced. It is critical that the shell thickness is analyzed to make sure that the cables and reinforcing will not tear the shell. The shell is then cut free Of the rest Of the kiln with the use Of torches. This process will be repeated until all of the shell sections have been removed. The final step is to grind the exposed ends of the shell.
Since the new joints were cut with a torch, the cutting slay and imperfections need to be ground smooth to provide a good surface to weld to. The installation of the new kiln shell typically occurs in the opposite order of he removal. The shell sections are hoisted ensuring that they are hanging perfectly on the kiln slope - once in location this will provide an even joint to fit. Consideration should also be given to installing the longitudinal seams in adjacent shell sections opposite each other.
The kiln shell is held in place by temporary joint hardware and cribbing as required. The joint hardware typically consists of angles and radial adjustment blocks, welded to the shell and threaded through rods and nuts that fit through the angles to adjust and support the shell. Radial shell mismatch is extremely important when fitting he shell using the radial adjustment blocks that were installed in the shell. When new shell fits to new shell, the inside diameter is typically the same, thus there should be less than a 1/inn mismatch. However, it is not uncommon that the inside of the old shell is corroded.
When this is the case, it is important to ensure the mismatch is very even around the joint and does not vary by more than 1/inn, even if the total mismatch is 1/in. With the joints aligned, the through rods are used to pull the shell sections together. Tie bars should be installed to lock in the joint alignment attained with the mint hardware and to take up the torsion's forces exerted on the joint during rotation. At this point all equipment and material is removed from the inside of the kiln. Run-out stands, fixed location roughly inn uphill and downhill of each joint are set up.
The kiln is rotated and a set of stations, 1-12, laid out on the shell. At each of these stations two readings are taken, one at the uphill run-out stand and one at the downhill. The resulting numbers are then taken and laid out on a polar graph. When looking at the magnitude of the run-out on a polar graph, opposite readings will show any corresponding moves. Several of these indications in the same quadrant will warrant a corrective adjustment of the joint. With run-out readings showing no corrective adjustment, the shell and joints are ready for the next step, welding. Weld Eng The shell is typically welded on the outside first. The shell joints are ground so that the mill scale is removed several inches uphill and downhill of the actual joints bevel. A root pass in the base of the bevels is welded in by hand with the welder taking care to properly preheat the shell. The remaining outside bevel is welded using the submerged arc welding (SAW) process. SAW is the preferred welding method for the majority of the bevel because of its consistent, superior quality of weld and its very high deposition rate.
Cite this Page
Replacement of Kiln Shell. (2018, Apr 13). Retrieved from https://phdessay.com/replacement-of-kiln-shell/
Run a free check or have your essay done for you
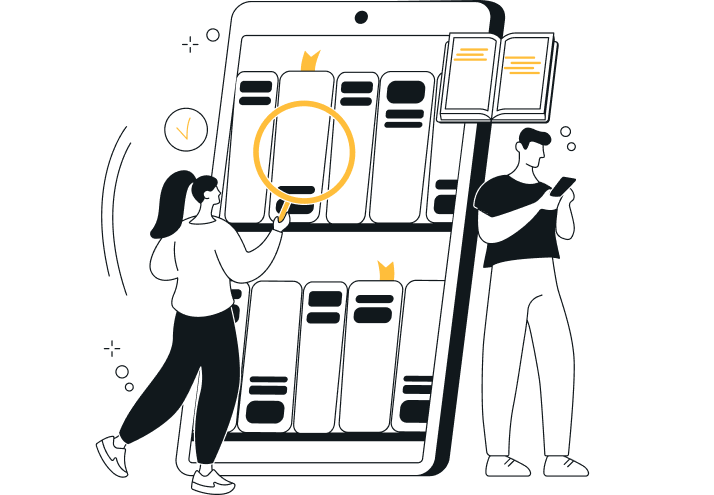