LOM Process Review
Background and History
Rapid prototyping, also known as RP technology, witnessed rapid development in the early 1980s, and received growing attention in the following decade. Professor Hideo Kodama from Japan was the first person to develop a rapid prototyping method, and Charles Hull[2] from California invented the stereolithography method (known as SLA). The two scientists were acknowledged as the pioneers in this field, whereas in 1997, a report on rapid prototyping in Europe and Japan claimed that the idea of Solid Freedom Fabrication (SFF) was not actually new. It pointed out that the ancient Egyptian civilizations had recorded similar manufacturing concepts, such as the construction of pyramids, which was technically creating a three-dimensional object in layer fashion, just as the main idea of SFF. Following that, two techniques were considered as the foundation of rapid prototyping, namely photosculpture and the creation of maps in topography. Initially labor intensive, these processes later evolved to more modern techniques, and rapid prototyping at the same time has evolved into a field with wide application.
Some widely-used and commercialized techniques include 3D Printing (3DP), Fused Deposition Modeling (FDM), Stereolithography (SLA), Selective Laser Sintering (SLS), etc. One of the relatively recent rapid prototyping technique is Laminated Object Manufacturing (LOM), emerging in the 1990s. The prototyping system was developed by Helisys Inc. of Torrance, California, featuring forming a plurality of laminations into a stack to create three-dimensional objects. Principle The diagram below is the initial version of the LOM system created by Helisys. The system includes an X-Y plotter device fixed above the working platform, which is movable vertically. The plotter device has a forming tool to form a layer from a material sheet positioned on the working platform. All layers are bonded to each other by the heat sensitive adhesives. A bonding tool translates across the platform to apply a lamination force and heat to the layers. Both of the plotter and bonding tools translate along the rails on a common reference frame, which includes two rigid beams on a base frame. A sensor between the reference frame and bonding tool would sense the force applied to the laminations and then accordingly adjust the height of the platform. Another infrared sensor senses the layer temperature to give feedbacks to controlling devices, adjusting the speed of the bonding tool. The laser system includes a laser, mirrors and lens
Order custom essay LOM Process Review with free plagiarism report
Figure 1. LOM system designed by Helisys Inc. Figure 2 shows a simplified diagram of LOM apparatus, and the general working process is as follows [5]: 1. The material sheet adheres to the substrate and a heated roller 2. The laser traces out the contour of the prototype of each layer 3. Laser cross hatches the remaining area and facilitates waste removal 4. The platform moves down with the completed layer, a fresh material sheet is rolled into position 5. Platform adjusts to a new position to receive the next layer, the process is repeated Figure 2. Simplified LOM apparatus The excess material supports the overhangs or other weak parts during fabrication, and the cross-hatching facilitates the removal of waste material. The finished part is a wood-like texture which is composed of paper layers. Post-processing may include sealing or anti-oxidization treatment, due to the material’s (paper) tendency to absorb moisture and expand. Also note that there can be smoke emission during the printing process, also localized fire appears.
Therefore, a chimney system is required for ventilation. However, material selection of LOM is not limited to paper. The process has later been improved by developers to manufacture with stronger materials, such as plastic and metal, even sheets of powder metal (bond with adhesive) which produces “green” parts as a result. Heat treatment then follows to finally build the parts [6]. Major vendors/players The principal US commercial provider of LOM, also the developer of the technique, is Helisys Inc., which ceased operation in 2000. Then a successor organization Cubic Technologies continued to sell their products and the services are still available up to now. Toyada Machine Works in Japan also produces LOM systems under the license from Helisys. Several other companies providing innovated LOM technologies include Kira Corporation in Japan, which provides Paper Lamination Technology (PLT). It uses a knife for layer cutting rather than a laser and utilizes xerographic technology to bond layers. A similar technique is used at Mcor Technologies in Ireland but at a lower cost. Solido Ltd. of Israel (formerly Solidmension) bonds plastic layers with a solvent to form objects and is small enough to fit on a desk. Some vendors also hybrid CNC technology with LOM, cutting thick layer edges to avoid stair stepping, and at the same time accelerating the process and increasing material versatility.
Stratoconception in France is a Thick Layer Lamination technique developed by CIRTES, where the material layers are machined from metals and bonded mechanically together, allowing wider material selection and lowering the stair stepping effect. The similar offering can be found at Custom Motion Inc. and Zimmermann of Germany. Solidica provides a laminated fabrication approach based on CNC cutting of aluminum strip material, where the strips are ultrasonically bonded [7]. Applications Unlike most of the other commercialized RP techniques, LOM is relatively limited in terms of applications. It is primarily used for creating conceptual prototypes and scaled models, which can be tested for design or shape. It also has applications in making patterns for traditional manufacturing use, such as metal casting, sand casting or investment casting. Applications of LOM are closely related to material selection at the same time. The technology is relatively versatile, almost any material can be bonded – but the most commonly used material is still paper. Metal sheets are more unusual mainly due to the difficulty in the cutting stage.
In terms of plastic products, LOM has satisfactory performance and is widely used. Its low cost and fast speed make it stand out among many other techniques, though the final product lacks precision and is far from end-used parts. MCor of Ireland has proposed a new-type LOM, renamed as Selective Deposition Lamination (SDL) which features adding colors in the print. Paper sheets are color printed, glued and then cut with a blade. Such innovation adds to the competence of LOM and widens its application in multicolor objects production [8]. Ceramic components can also be printed via LOM. Advanced ceramic structural components have been made from Ce-ZrO2 and Al2O3/ Ce-ZrO2, exhibiting high strength and good microstructure after heat treatment. Additionally, alumina, silicon nitride, Al2O3/ Ce-ZrO2 components with typical densities have been reported to be successfully produced by LOM, which can function as turbine blades or biomedical filters. These applications also indicate LOM is better suited to produce small order size prototypes. In terms of the biomedical use, further research has been conducted to apply LOM to produce mimetic bone biostructures from alumina, zirconia and phosphate-based bioceramics.
Data of bone microstructures and certain human tissues are acquired by Computer Tomography (CT) scanning and then generating geometric models to be exported to the LOM machines. A potential application is producing custom bioceramic implants directly according to the patient’s own body data [9]. Figure 3 shows some 3D printed parts by LOM technique. Figure 3. Parts printed by LOM Advantages and Disadvantages Like most of the rapid prototyping processes, LOM has various advantages and some unique characteristics, while drawbacks and limitations also exist and require further improvement and in-depth research. The major advantages of LOM include:
- Low cost, given the fact that raw material is readily available and cheap.
- Large parts available, since the process involves no chemical reaction and not the whole part area needs to be processed.
- Fast speed, where only the contour of the part is cut off, compared with other RP methods working on the entire layer.
- No support structure is needed, the cross-hatching area functions as support and facilitates material removal later.
- Potential for increasing processing speed.
Disadvantages also remain to be addressed through further study. Main problems may include:
- Weak bonding between layers.
- Poor-quality surface finish.
- Inability to print hollow structures and some complicated geometries.
- Low printing accuracy especially in z direction, unable to create functional prototypes.
- Models have to be sealed to prevent moisture.
Research/Improvement issues Considering the limitations of LOM, researches have been focusing on improving printing accuracy and seeking for methods to produce hollow parts. Y.Y.Chiu et.al proposed a new Bridge-LOM process and algorithm, which can build bridge structures to connect 2D layer contours with the outer frames. It adopts a “free-cut-press then adhesive spraying” method, the flow chart and illustration of apparatus are shown below in Figure 4 and 5. Figure 4. Flow chart of Bridge LOM Figure 5. Illustration of the LOM equipment The algorithm took into consideration two major problems – support and position. The support in this bridge-LOM method emphasizes using bridges to provide all required support, rather than the traditional LOM where all the remaining area are cross-hatched and function as supporting structures. Position issue can be eliminated by maintaining the process in X-Y position only, so all the bonding treatment and position holding can be well controlled. Such improvement features reducing post-processing time by building less but accurate support structures, and realizing fabrication of hollow or thin-wall parts with the bridging [11].
MCor Technologies improved LOM by proposing an innovated method named Selective Deposition Lamination (SDL), which differs LOM in that it replaces laser with a tungsten carbide blade and applies water-based adhesive only in necessary regions. No infiltration is required for post processing. However, Iris (with color capability) by Mcor costs $65,000 while some FDM machines producing similar parts may cost less than $1,000. Regarding metal parts printing, M.Prechtl et.al investigated LOM with metal foil and highlighted the realization of sheet metal processing. Figure 6 shows the entire procedure. In order to enhance the stability of the foil stack, diffusion welding or high temperature brazing are performed to join the layers, producing parts without pores or inclusions. Additionally, the layer fixing, generation and final joining steps are vital during the whole process. A short pulse solid-state laser is used for the first two steps, and the last step is performed in a furnace via a thermally activated process under high temperature.
Figure 6. Procedure of the metal foil LOM (N = number of layers)
References
Kodama H. Automatic method for fabricating a three-dimensional plastic model with photohardening polymer. Rev Sci Instrum. 1981;1770–73.
Hull C. Apparatus for production of three-dimensional objects by stereolithography. US Patent #4575330 A. 1984.
Lengua C.A.G. (2017) History of Rapid Prototyping. In: Farooqi K. (eds) Rapid Prototyping in Cardiac Disease. Springer, Cham Patent
”Laminated object manufacturing” https://en.wikipedia.org/wiki/Laminated_object_manufacturing
'Rapid Prototyping: LOM.' http://www.efunda.com/processes/rapid_prototyping/lom.cfm (accessed June 8, 2012).
'Laminated Object Manufacturing.' April 10, https://web.archive.org/web/20100102182152/http://home.att.net/~castleisland/lom.htm (accessed April 19, 2008).
“LOM (Laminated Object Manufacturing): 3D Printing with Layers of Paper” https://www.sculpteo.com/en/glossary/lom-definition/
“Rapid Prototyping – Laminated Object Modelling and Computer Aided Manufacturing of Laminated Engineering Materials” Sep 13, 2002 https://www.azom.com/article.aspx?ArticleID=1650#_Laminated_Object_Manufacture
“Laminated Object Manufacturing (LOM)” Nov 15, 2017 https://3d-expo.ru/en/article/izgotovlenie-obektov-metodom-laminirovaniya-lom-78841
Y.Y. Chiu, Y.S. Liao, C.C. Hou, Automatic fabrication for bridged laminated object manufacturing (LOM) process, Journal of Materials Processing Technology, Volume 140, Issues 1–3, 2003, Pages 179-184
“Paper 3D Printing – It’s Not Your Daddy’s LOM” Oct 24, 2012 https://www.mcortechnologies.com/paper-3d-printing-its-not-your-daddys-lom-blog__trashed/
M. Prechtl et al., 'Rapid Tooling by Laminated Object Manufacturing of Metal Foil', Advanced Materials Research, Vols. 6-8, pp. 303-312, 2005
“What is Laminated Object Manufacturing?” October 9, 2013 https://www.livescience.com/40310-laminated-object-manufacturing.html
Cite this Page
LOM Process Review. (2023, Feb 13). Retrieved from https://phdessay.com/lom-process-review/
Run a free check or have your essay done for you
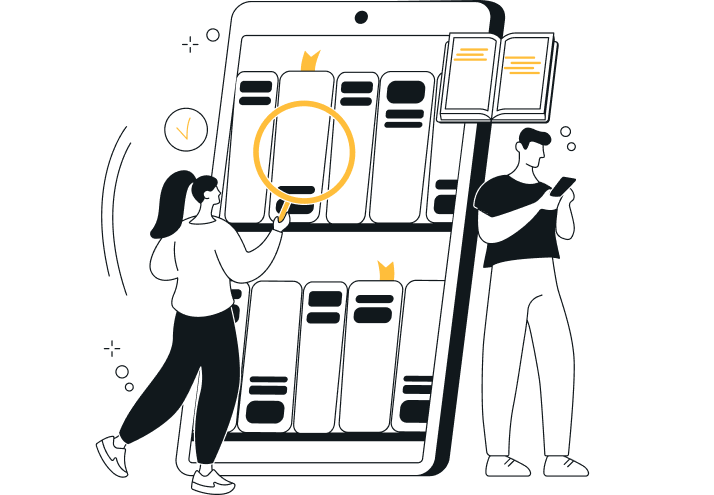