Heat Transfer Lab Report
UNSTEADY STATE HEAT TRANSFER
Heat transfer processes are prominent in engineering due to several applications in industry and environment. Heat transfer is central to the performance of propulsion systems, design of conventional space and water heating systems, cooling of electronic equipment, and many manufacturing processes (Campos 3). Unsteady state conduction is the class of heat transfer in which the temperature of the conducting medium varies with time and position.
This occurs frequently in industrial processes, especially food preservation and sterilization, where the temperature of the food or of the heating or cooling medium constantly changes (Farid2). The work reported here involves the investigation of unsteady state heat transfer in two cylindrical rods and the conformity of experimental results to different methods of theoretical analysis. Aluminum and Plexiglas cylinders were used. Thermocouples were placed at different radial and axial positions, and the cylinders, which were in thermal equilibrium with an ice bath, were placed in a warm water bath at 370C.
Order custom essay Heat Transfer Lab Report with free plagiarism report
Temperature profiles were obtained using a data acquisition system on a computer. Theory The applicable form of the heat transfer equation for conduction in solids is given by (Welty1): If the thermal conductivity is constant and the conducting medium contains no heat sources, Equation 1 reduces to Fourier’s second law of heat conduction (Welty1).
Equation 2 can be written in cylindrical coordinates as (3) Assuming that no heat transfer occurs in the axial position, and temperature varies with radial position and time only, (4) Equation 3 therefore becomes (Welty1) (5) Nomenclature for all equations is shown in the appendices.
For a cylindrical rod immersed in a higher temperature fluid, heat transfer occurs by convection from the body of fluid to the surface of the rod, and by conduction from the rod’s surface to its center. If conduction through the rod occurs much faster than convection from the fluid, convection is the rate-limiting heat transfer mechanism, and the temperature within the solid will vary with time only. This condition, in which the external resistance is large relative to the overall resistance, is the primary characteristic of a “lumped” system.
The Biot number, (Bi = hV/kA), is a ratio of the internal (conductive) resistance to heat transfer, to the external (convective) resistance to heat transfer. A general rule of thumb is that a body can be assumed to be lumped if Bi < 0. 1 (Welty1). For lumped bodies, the temperature variation with time is described by Equation 6 (Welty1) For cases in which the internal and external resistances are significant, Equation 5 must be solved numerically or graphically to determine the temperature variation with position and time.
Graphical solutions (Heisler charts) are shown in Welty1 for different shapes and geometries. To use the Heisler charts, three dimensionless ratios must be known, and a fourth will be read on the appropriate axis. These dimensionless ratios are: Y, unaccomplished temperature change=T? -TT? -T0 (7) X, relative time=? tx12 (8) n, relative position=xx1 (9) m, relative resistance=khx1 (10)
DISCUSSION
Before the data was analyzed, the thermocouples were calibrated and the voltage readings were converted to temperature. To achieve this, the final value from each thermocouple was set to be equal to the warm water bath temperature (370C), and the initial reading was set equal to the ice water bath temperature. Thus, for each thermocouple an equation was obtained using the two points to convert voltage readings to temperature. An example of the calibration for one of the thermocouples is shown in Appendix
II. LUMPED ANALYSIS
To determine if a lumped-parameter analysis could be applied, the Biot numbers for the systems were calculated (shown in Table 1). Table 1: Biot numbers for the aluminum and Plexiglas cylinders. | Bi| Aluminum| 0. 07| Plexiglas| 81| Since the Bi value of the aluminum system is less than 0. 1, convection from the water to the surface of the cylinder is the rate limiting heat transfer mechanism. Thus, a lumped-parameter analysis can be safely applied. The Plexiglas system, on the other hand, has a Bi >> 0. 1, and the rate limiting mechanism is conduction in the cylinder.
The temperature-time plot gotten by applying a lumped-parameter analysis (Equation 6) to the Aluminum cylinder was compared to the plot obtained from the thermocouple located closest to center of the cylinder. This thermocouple is chosen for comparison because it is located farthest from the heating source and will have a temperature history that differs most from an ideal lumped system. With this thermocouple, we should therefore obtain the maximum error associated with applying a lumped-parameter analysis to the system.
Figure 1: Temperature history plot for the aluminum cylinder. The thermocouple is located 0. 25 in away from the center. A lumped parameter analysis is also shown in Figure 2 for the Plexiglas cylinder to illustrate the error encountered by applying Equation 6 to “un-lumped” systems. Figure 2: Temperature history plot for the Plexiglas cylinder.
COMPARING TEMPERATURE HISTORY AT DIFFERENT RADIAL POSITIONS
Based on their Biot numbers, it was expected that the temperature history plots at different radii for the aluminum cylinder should follow a similar path, while those for the Plexiglas cylinder shouldn’t. Figure 3: Experimental temperature for the aluminum cylinder history at various radial positions. Figure 4: Experimental temperature for the Plexiglas cylinder history at various radial positions. Figures 3 shows that the temperature curves are all the same at different radii in the aluminum cylinder.
This is attributed to the fact discussed earlier that the aluminum cylinder behaves as a lumped system, that is, there is negligible resistance to internal heat transfer (conduction). Figure 4, on the other hand, shows differences in the temperature history plots at different radii in the Plexiglas cylinder, confirming that conduction through the cylinder is the rate limiting heat transfer mechanism.
GRAPHICAL SOLUTION –HEISLER CHARTS
For systems that cannot be accurately modeled by lumped-parameter solutions, such as the Plexiglas cylinder, we must resort to other analytic methods.
Graphical solutions in Heisler charts (Welty1) were used to estimate the temperature history at three thermocouples. These plots are compared with the experimental plots in Figures 5 – 7. Figure 5: Experimental and graphical-solution temperature history plot. The thermocouple is located at a radius of 1. 25 in away from the center. Figure 6: Experimental and graphical-solution temperature history plot. The thermocouple is located at a radius of 0. 50 in away from the center. Figure 7: Experimental and graphical-solution temperature history plot. The thermocouple is located at the centerline of the cylinder.
The percent differences show that predicting the temperature history using Heisler charts produces much error. This method was open to mistakes for the following reasons: 1. Curves on the charts are drawn for integer values of relative time, position and resistance. Therefore, reading and approximation errors result when decimals to be read are not shown on the axes. 2.
Some areas of the Heisler charts are so crowded with lines that reading a value with accuracy is nearly impossible. 3. When producing the charts, Heisler did calculations for some set of numbers and then linearly connected the points on a logarithmic-linear modified scale. Dimensionless ratios obtained from the charts are thus slightly different from their real values (Dilsiz4).
NUMERICAL ANALYSIS – MATLAB
Equation 5 was solved numerically using MATLAB. The code used is provided in Appendix IV. The solutions were extracted to Excel and plotted (Figures 8 and 9).
The temperature plots at different radii for the aluminum cylinder are superimposed and therefore indistinguishable. This further demonstrates the fact that the temperatures at all points in the aluminum system were identical. Figure 9, on the other hand, shows that the Plexiglas had varying temperatures at different points. Figure 8: Numerical Solution from for the aluminum cylinder. Results were found using MATLAB and plotted in Excel. Figure 9: Numerical Solution from for the Plexiglas cylinder. Results were found using MATLAB and plotted in Excel. The results obtained from the numerical analysis were compared with experimental data.
Table 4 shows the average percent differences between their values. The percent differences for the Plexiglas cylinder are significantly lower than those obtained when using the Heisler charts (see Table 3). This suggests that the numerical analysis using a partial differential equation solver is a more reliable method of analyzing the data for the Plexiglas cylinder. Table 4: Average percent differences between experimental results and the numerical analysis solution. Radius (in)| Average % difference| | Aluminum| Plexiglas| 0| -| 7. 54| 0. 25| 3. 68| 5. 81| 0. 5| -| 5. 75| . 75| 2. 99| -| 1| 3. 35| 6. 34| 1. 25| 2. 27| 4. 92| | | | Average| 3. 0725| 6. 072|
CONCLUSION
The rate limiting heat transfer mechanism for the aluminum and Plexiglas cylinders were convection and conduction, respectively. It was found that the temperature history for the aluminum cylinder conformed to a lumped-parameter analysis while that for the Plexiglas cylinder didn’t. This was expected based on the Biot numbers calculated for the two systems. Temperature profiles obtained from Heisler charts produced much error, and deviated significantly from experimental data.
For the Plexiglas cylinder, the numerical analysis using MATLAB, although tedious, provided the least error when compared to experimental results. The temperature histories at different radial positions were compared: the temperature-time curves for the aluminum cylinder overlapped, that is, the temperatures were the same at different radial positions. On the other hand, there were significant differences in the temperature-time curves for the Plexiglas cylinder. This is attributed to the fact that the aluminum rod was lumped, while the Plexiglas wasn’t.
SOURCES OF ERROR
It was assumed that no heat was transferred through the ends of the cylinders. This may have induced some error in the analysis. If there was indeed significant heat transferred through the ends, two thermocouples placed at the same radius will report slightly different temperatures, with the one closer to the edge being heated faster. As discussed earlier, error is introduced when reading the Heisler charts. These errors were considered minor, and were not substantial enough to affect the major conclusions drawn from the analysis.
SAFETY CONSIDERATIONS
The proximity of water baths to electrical equipment presented an electrical hazard.
It was important to make sure not to spill water when transferring the cylindrical rods between baths. We also made sure to move any movable electrical equipment as far as possible from the immediate area. The baths used weren’t hot enough to cause scalds upon contact with the skin. Safety glasses and closed-toed shoes were worn throughout the duration of the experiment.
REFERENCES
1. Welty, James R. , Charles E. Wicks, Robert Wilson, and Gregory L. Rorrer. Fundamentals of Momentum, Heat, and Mass Transfer. New York: Wiley, 2001. Print.
2. Farid, Mohammed M. Sterilization of Food in Retort Pouches. New York, NY: Springer, 2006. Print.
3. Campos, Marco, Estaner Claro Romao, and Luiz Moura. "Analysis of Unsteady State Heat Transfer in the Hollow Cylinder Using the Finite Volume Method with a Half Control Volume. " Applied Mathematical Sciences 6. 39 (2011): 1925-931. Print.
4. Dilsiz, Resul, and Onur Y. Devres. "Graphical Solution of the Transient Heat Transfer Problem. " AIP Conference Proceedings 1048. 855 (2008).
Cite this Page
Heat Transfer Lab Report. (2017, Feb 03). Retrieved from https://phdessay.com/heat-transfer-lab-report/
Run a free check or have your essay done for you
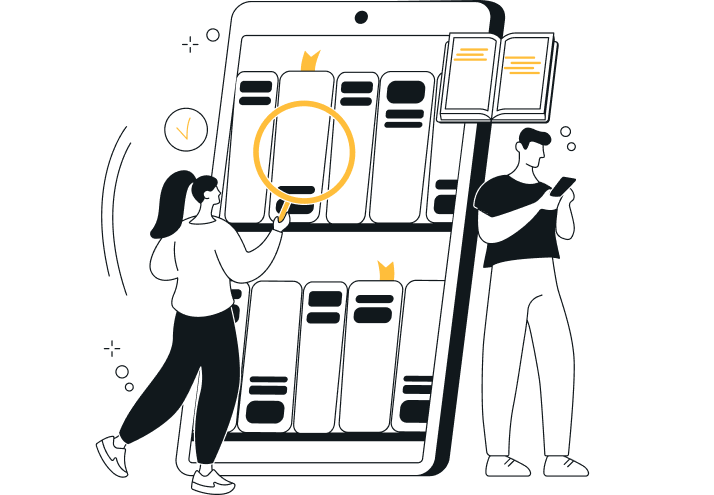