The Use of the Concept of Supply Chain Management in the Business Environment
The concept of supply chain management is widely employed in the business environment. In recent years, the interlinking between supply chain and quality management has gained significant attention. Through this relationship, it is possible to identify quality management issues within the supply chain environments, both internal and external. Today, the business environment faces the challenge of competition. Companies are required to constantly improve the quality of the end product in order to overcome the market dynamics. Therefore, supply chain managers are increasingly embracing quality management.
Quality Concepts and Theories for Supply Chain Management
A supply chain is the core of business activities because it facilitates the flow of materials and information from upstream to downstream members of the supply chain. Supply chain activities facilitate the processes involved in the planning, production, and delivery of products and services. This implies that supply chains are the lifeblood by which business survive and thrive. Quality management, on the other hand, focuses on the flow of elements in the supply chain: processes, materials, information, and funds. According to Foster (2016), the flow of these elements ought to be efficient and effective to guarantee quality.
Order custom essay The Use of the Concept of Supply Chain Management in the Business Environment with free plagiarism report
A range of quality concepts is implemented in supply chain management. Different quality dimensions are used to define the quality of the supply chain. Among the dimensions of quality associated with, products, include performance, conformance, features, durability, reliability, serviceability, aesthetics, and perceived quality. With regard to services, dimensions of quality include tangibles, service reliability, assurance, empathy, and responsiveness (Foster, 2016). These dimensions are instrumental in enhancing the quality of all supply chain processes, thus enabling a company to derive benefits such as improved process efficiency, cost reductions, as well as enhanced resource management.
Additionally, various quality improvement theories are associated with supply chain management. Although there is no unified theory explaining the concept of quality improvement in relation to supply chain, different approached to quality improvement have been established. The major contributors of the quality improvement movement include Deming, Juran, Ishikawa, Feigenbaum, Crosby and Taguchi. Deming employed a transformational approach to quality improvement by emphasizing on the management practice. He emphasized that continuous quality improvement occurs through efficient management practices and systems. In this regard, he identified 14 points of management that can help improve quality of products and services (Foster, 2016).
Juran employed a strategic approach to quality improvement, through which he indicated that quality problems arise from ineffective and insufficient planning. According to Juran, companies can increase the quality of processes by reviewing the strategic plan. Juran's approach emphasizes on the need to set goals and devise them through effective plans because this enhances quality (Foster, 2016). Juran Trilogy indicates that there are three basic processes for quality improvement: planning, control, and improvement. Ishikawa indicated that it is essential to involve employees in quality improvement programs and insisted on the importance of training. He identified the seven tools (B7) of quality that are shown to democratize statistics. Crosby, on the other hand, emphasized that quality improvement entails having products and services that have zero defects. He argued that human resources have a significant impact on the quality; hence, companies should engage workers in quality improvement. This implies that worker input is fundamental to the successful implementation of a quality improvement program.
Among the different quality dimensions are process-driven and customer-driven quality aspects. Process driven quality dimensions focus on the design specifications of different business processes. Heravizadeh, Mendling, and Rosemann (n.d.) identifies four major processes in operations management. They include process flow, process cost, process quality, and process flexibility. This indicates that process quality plays a significant role in the efficiency of the supply chain. Process quality focuses on how a process can be used to enhance the quality of products. The major dimensions aligned with process-driven quality include reliability, accuracy, and conformance to product specification. These elements are crucial in ensuring that internal processes enable a company to create a positive external perception towards quality in terms of goods and services.
Quality based dimensions are based on the functions of an organization, which operates under different functions: human resource, marketing engineering, and finance among others. Each organizational function has its own processes; therefore, quality dimensions depend on the function (Heravizadeh et al., n.d.). For instance, the marketing function may perceive process- driven quality as conformance to design specifications. The human resource function, on the other hand, may perceive, process-driven quality as effective resource utilization.
Process-driven quality reflects in different business environments and is used by different companies to gain a competitive advantage. For example, today a company like the Caterpillar, which offers products to farmers, enhances quality through its processes. During harvest season, the company's supply chain department ensures that farm equipment is delivered earlier than scheduled in a bid to enhance product or service quality.
Customer-driven quality focuses on the needs of customers. Some of the quality dimensions that are customer driven include aesthetics and product features. The goal of customer-driven quality is to enable a company to overcome competitors. For example, a company like New York's Chemical Bank focused on customer-based quality. The organization launched a user survey to establish the needs and preferences of the customers. The findings indicated that customers needed rapid response to inquiries regarding their account status. In this regard, the bank installed a computerized system to ensure customer's calls are received immediately. Consequently, the bank was ranked fourth in the industry as far as quality is concerned. This example indicates that a company can improve quality by focusing on customer needs and preferences.
The Impact Quality Theories on Manufacturing and Service Industries Quality improvement theories play a critical role in ensuring efficiency and effectiveness of operations, thus enhancing the quality of products and services. Manufacturing and service industries can employ quality theories to enhance the quality of products and services. Various assumptions provided by quality improvement theories are applicable in the business environment, thus can help manufacturing and service industries to improve the quality of their offerings by increasing the efficiency of processes across the supply chain. For instance, Joseph Juran indicated that quality could be controlled by looking into avoidable and unavoidable costs (Foster, 2016). For instance, manufacturing industries may minimize avoidable costs by minimizing wastes such as defects and inventory.
For instance, companies may improve product quality by preventing failures that lead to complaints, repair, and rework. Unavoidable costs on the other hand, should be prevented to enhance product qualities. For example, manufacturing industries should conduct quality control activities such as sampling and inspection to improve product quality. In this regard, manufacturing industries can employ Juran's approach to quality improvement by reducing failure costs. Based on Feigenbaum's approach, manufacturing companies should engage in improving quality by focusing on total quality control. This means that high-quality products can be achieved if all organizational functions operate in as a team.
Service industries can as well employ assumptions of Crosby's theory, which emphasizes on the importance of involving workers in quality improvement. This theory indicates that companies should ensure that employees are aware of the importance of quality improvement. For instance, service industries could deliver zero-defect services by capitalizing on employee development programs. The human resources function is one of the major contributors to quality in the service industry. Therefore, service-oriented companies could definitely gather insight from this theory.
Evidently, quality management is an important component of supply chain management. The integration of these two concepts is associated with different benefits, among them efficiency, effectiveness and a competitive advantage. Therefore, managers and other organizational leaders should implement quality concepts in their supply chain in order to deliver the desired results. Nevertheless, it is important to understand that perception towards quality differs based on a variety of dimensions inherent to products and services. In this regard, companies should define perceived quality based on the dimensions that relate to both customers and processes.
Cite this Page
The Use of the Concept of Supply Chain Management in the Business Environment. (2022, Nov 21). Retrieved from https://phdessay.com/the-use-of-the-concept-of-supply-chain-management-in-the-business-environment/
Run a free check or have your essay done for you
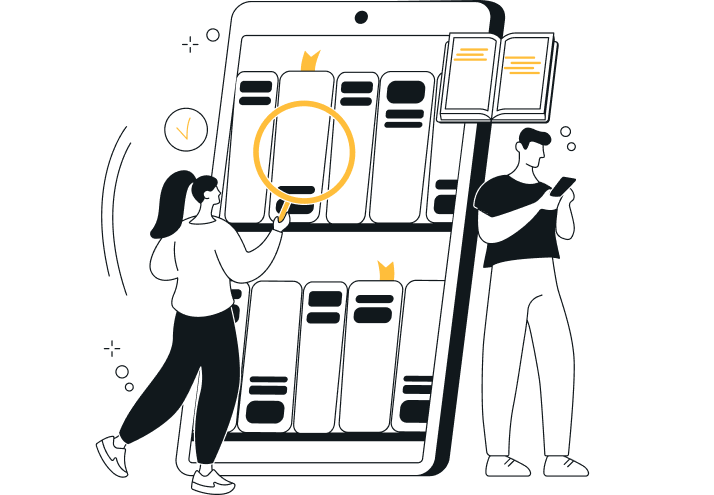