Smed, Continuous Improvement Activity for Crank Changeove
I would like to thank the Human resources managers who gave me an opportunity to undertake such a project in world renowned company as General Motors. I would also like to thank all the operators who passed on all the knowledge that they could in two months to help me understand all the processes. They also helped me in various situations where it seemed that my project would come to a standstill, giving me exactly what I needed to go on. Next I would like to thank the each and every single person in the crank line who helped me and guided me in every step.
They provided me with the resources and made suggestions that helped me improve and build a base for my ideas. I would also like to thank my fellow project trainee who had much more experience than me. He helped me to take off on my own path to completing the project with his valuable suggestion and ideas. Above all I would like to thank him for being a very good friend at the hour of need. I cannot fail to mention the undying support of Mr Kisan Kapse, Mr Prashant Kurde and Mr Bharat Sawant who helped me in every stage of the project. They were of great help in difficult times.
I am deeply in debt to them whose stimulating suggestions and encouragement helped me in times. Last but not the least I would like to thank my project guide Mr Vinayak Angane who looked closely throughout the project, correcting and offering suggestions for improvement. He took time off his busy schedule to explore me with alternate approaches to my problem and with ideas that could never have occurred to me on my own.
Order custom essay Smed, Continuous Improvement Activity for Crank Changeove with free plagiarism report
Introduction
The General Motors powertrain in Pune machines cam carrier, cylinder Head, cylinder block and crankshaft. GMI powertrain in Pune is a level IV flex plant.
This power train plant is the one and only Level IV Flex plant in India. A level IV flex plant means that the plant can machine different types of the same component in the same machine. This is done by changing the die holding the component and also changing the program mentioning where to machine. My project revolves around the SMED of crankshaft. Some different parts constitute of the Cylinder block, Cylinder head & the Crankshaft. The crankshaft is the part of an engine which translates reciprocatinglinearpiston motion into rotation.
Basically the crankshaft powers the engine. Crankshafts can be monolithic (made in a single piece) or assembled from several pieces. Monolithic crankshafts are most common, but some smaller and larger engines use assembled crankshafts. The different types of crank made in GM Powertrain Talegeon plant are 1. 0 xSDE, 1. 2 BDOHC, 1. 3 xSDE and 1. 4 BDOHC. SMED (Single Minute Exchange of Die) is a method for rapidly and efficiently converting a process from running the current product to running the next product. SMED is also often referred to a Quick Changeover.
The SMED method can, and often is, used in starting up a process and rapidly getting it to running condition with minimum waste of time.
Setup Change/ Changeover
Setup change/ Changeover is preparation, execution of activities in work station which includes hardware changes, sometimes software changes e. g. : locator centres, chuck jaws, steady program calling etc. to produce good to good parts. Change over time is defined as the time difference of the last product produced and the next new product produced with the right quality and at the right speed. The production capacity of a plant is determined by the changeover time.
Unless the changeover time is reduced to the bottleneck the production can’t meet the target Production sites with long setup times are characterised by
- Low flexibility of the component
- Large batch sizes
- High levels of stock
If we decrease the setup change time then we could use the extra capacity either to increase productivity or to decrease the batch sizes. There are many benefits likereduction in lead time and therefore increased, improved and faster delivery, higher productivity and therefore satisfying customer needs faster, Reduction in working capital, less disturbances etc.
Single Minuite Exchange Of Die (Smed)
The process of changing die is called Single Minute Die Exchange (SMED). Single-Minute Exchange of Die (SMED) is one of the many lean production methods for reducing waste in a manufacturing process. It provides a rapid and efficient way of converting a manufacturing process from running the current product to running the next product. This rapid changeover is the key to reducing production lot sizes and thereby improving flow. The phrase "single minute" does not mean that all changeovers and start-ups should take only one minute, but that they should take less than 10 minutes.
In short it should be a single digit number. The different features of SMED are:
- It is a systematic approach that decreases disturbances and problems
- The main factor that can lead to its success are team work & creativity
- SMED methods are used for exchange of dies, but it can also be used for cleaning and for maintenance purposes.
Importance Of Reducing Changeover Time
Reducing changeover time is like adding capacity, increasing profitability and can help most manufacturers gain a competitive edge.
Image a pit crew changing the tires on a race car. Team members pride themselves on reducing changeover by even tenths of a second because it means that their driver is on the road faster and in a better position to win. The same philosophy applies to manufacturing – the quicker you are producing the next scheduled product, the more competitive you are. Reducing changeover times is a fundamental requirement of any company to take lead over the other in production and maintaining top position.
By understanding the principles and practices of the SMED system organisations will be able to cut changeovers by over 50% with very little expenditure, and to single minutes with the modification of tooling and fastening systems. Single Minute Exchange of Dies can be applied to any changeover operation and aims to reduce the overall downtime for a complete changeover to less than nine minutes. An understanding of the operational benefits to be gained from the fast exchange of tooling. The interaction of a multi-disciplined workforce constructively looking to eliminate waste from the changeover process.
How unstable setups can adversely affect subsequent operations and how standard operating procedure can eliminate these concerns. A team approach in understanding the methodology used in applying SMED through theoretical explanation and practical involvement in actual changeovers.
SMED Implementation
To successfully implement SMED in a system is a difficult task. Therefore to successfully guarantee the implementation of the process, the following steps should be followed closely.
- Start by choosing the right equipment to start with. . This is normally a bottle-neck with long set-up times
- Work cross-functional. Operators, Technicians, Engineers and Managers should worktogether
- Visualize the present situation and agree on a common goal
- To succeed you will need a clean and well organized work-place. A 5S implementation is recommended. This process will be explained in detail as we move ahead.
- Keenly observe the operations and processes. Analyze the present situation video-technique. The different moments are classified as being external or internal and waste or not waste. All known disturbances are listed as well.
- The purpose is to secure that all external set-ups are performed when the machine is running. Use checklists, function controls and improved transports. For example collect necessary tools and consumables before the next operation starts up or sharp the tools before activity starts. S
- Measures are carried out to reduce all types of waste.
- This includes: Elimination of all need for adjustments. Exchange of bolts for quick-fasteners.Standardized parts, tools, dimensions Need for quality control
- Each changeover should be so planned that it is better and faster than the previous one.
Each changeover should be analysed and properly documented which includes suggestion that could make it faster THE 5S SYSTEM “5S” is a method to create a safer, cleaner, and better-organized workplace. The five S in the process stand for: SET IN ORDER
The principle here is to keep things in their proper places. One guide to proper placement is to keep frequently-used items handy, and store other things where they can be found.
In reference to a workplace, it means: At present the tools required for the changeover process are stored in red tool carts and the carts are kept in a specific location for easy access. The tool carts are rolled to the machine where changeover is taking place at the required time.
Sort
Every tool which is used for a changeover process must be tagged and identified properly. All the operators involved in the changeover must be aware of the location and purpose of the tool.
Shiny Clean
This is the exception – the only one-time activity in the 5S method. This stage has two goals: Determine and gain agreement on the desired level of cleanliness * Learn how to make new routines so this will become standardized STANDARDIZED CLEANUP In this phase consider the sources of dirt: air-borne dust; sawdust or other dry powder from cutting operations; splatter from wet processes; or simple trash because there is no proper container. A practical target is to have all workers take five minutes every day to tidy up after themselves – including the time to complete and sign the checklists. Supervisors should monitor compliance with the clean-up. The checklists make this both important and achievable.
Sustain
This phase is perhaps the most important concept that includes instilled discipline, self-discipline, common cultural values, and self-motivated practice to improve. This step requires continued management support and communication. It brings out the leadership qualities of the employees and also improves their human values too. All these activities should be followed up on a regular basis with full commitment and hard work from all operators as well as managers for SMED to be a success.
Cite this Page
Smed, Continuous Improvement Activity for Crank Changeove. (2016, Dec 01). Retrieved from https://phdessay.com/smed-single-minute-exchange-of-die-continuous-improvement-activity-for-crank-changeover-process/
Run a free check or have your essay done for you
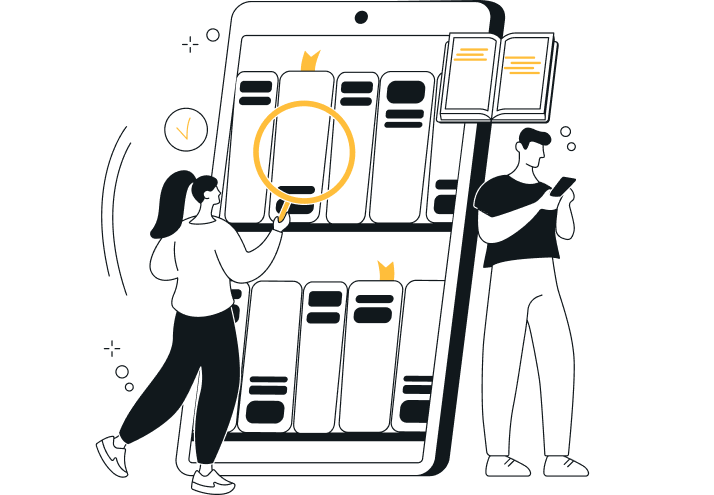