Simulation model for Mercedes-Benz production facility in Alabama
Abstract
Mercedes-Benz United States International (MBUSI) built a manufacturing facility for the production of the new M-Class “All Activity Vehicle” (AAV). This plant consists of three large sequential shops: the Body Shop, the Paint Shop, and the Assembly Shop. When the plant reaches full production, 270 vehicles will be produced each day by two shifts. A finished vehicle is intended to leave the end of the assembly line every 3.6 minutes.
- The main objective of this study is to simulate the design and operational policies of the AAV assembly facility and to verify that the daily throughput requirements can be met. The simulation study also answered the following questions:
- What is the maximum throughput (capacity) of the facility?
· What is the daily distribution of throughput?
· Does the current design produce the required throughput of 270 cars per day?
· How do the buffers behave in terms of quantity fluctuations?
· What are the possible bottlenecks to the desired throughput?
Order custom essay Simulation model for Mercedes-Benz production facility in Alabama with free plagiarism report
This paper provides a description of the integrated simulation model to analyze the capability of the production facilities at MBUSI. This paper includes the inputs used for the development of each of the three individual models: the Body Shop, the Paint Shop, and the Assembly Shop. Additionally, it includes descriptions of the model features and the assumptions that were made.
Introduction
Prior to starting operations of its new assembly plant in Vance, Alabama, Mercedes-Benz United States International (MBUSI) approached the University of Alabama for simulation assistance. Separate efforts to model the operations had not produced an acceptable result.
The MBUSI facility is comprised primarily of three distinct functional “shops”: the Body Shop, the Paint Shop, and the Assembly Shop. The vehicle body is welded together in the Body Shop. It then goes through the Paint Shop for treatment and painting. Finally, the engine, transmission, and all other parts are installed in the Assembly Shop.
This facility, MBUSI’s first in the United States, is scheduled to produce 65,000 AAVs annually when fully operational. This is a relatively small output in comparison to typical automobile assembly plants. When the plant reaches full production, two nine-hour shifts will produce 270 vehicles per day, or in other words, a finished vehicle will be leaving the end of assembly every 3.6 minutes. The option content will vary widely from car to car; there will be many choices available in engines, transmissions, and interior appointments. Hence, the plant will operate a
“mixed model” assembly line. MBUSI hired external engineering firms to design each of the three shops. Two of the firms developed Automod simulations of their respective shops. Durr Engineering developed a simulation of the Paint Shop. Mitsubishi- Chiyoda did the same for the Assembly Shop.
These simulations were developed independently of each other in order to validate the local throughput capacity of each shop. For example, Durr Engineering developed the Paint Shop simulation without direct concern of starvation from the Body Shop or blockage from the Assembly Shop. MBUSI wanted to verify that the overall facility will be able to produce the targeted 65,000 units per year.
While the facility has been divided into three functional areas, the functions are very interdependent. The throughput of one affects the throughput of the others. For example, a problem in the Paint Shop could starve the Assembly Shop and block the Paint Shop. Therefore, it is important for Mercedes-Benz to understand the Park, Matson and Miller interdependencies between the shops. Since the factory layout is an entirely new design, Mercedes-Benz management thought it was important to investigate th design of the plant and its operational policies, and to validate it using simulation. This was considered important considering the effect stochastic disturbances and vehicle flow dynamics might have on the system performance. If problems were revealed in the design, they could be dealt with prior to implementation of the system.
The main objective of this study was to develop a detailed simulation model of the AAV assembly plant to verify that the daily throughput requirements could be met by the current design of the AAV assembly facility.
Additional objectives of this study were to address the concerns of the management. The simulation study answered the following questions:
· What is the maximum throughput (capacity) of the
facility?
· What is the daily distribution of throughput?
· Does the current design produce the required throughput of 270 cars per day?
Additional questions also addressed by the analysis were:
- How do the buffers behave in terms of quantity fluctuations?
- What are the possible bottlenecks to the desired throughput?
This paper provides a description of the work that has been done for this research. This paper includes the inputs used for the development of each of the three individual models: the Body Shop, the Paint Shop, and the Assembly Shop. Additionally, it includes descriptions of the model features and the assumptions that were made. Actual data used in the analysis will not be presented due to proprietary concern.
Model concepts
A modular approach was taken. Three individual models, each representing one of the functional shops (the Body, Paint, and Assembly Shops) were developed to study the capacity of each shop in isolation, without concern of starvation or blocking from the other two shops (Roher and Strong 1997). After the models were validated individually, they were integrated in order to study the performance of the entire system.
As part of the Paint Shop, the Selectivity Bank was modeled. Since a body’s option/accessory list will affect the level of work in the Assembly Shop required for assembly, it is important to provide the Assembly Shop with a stream of bodies that is optimally sequenced for a balanced workload. The bodies are optimally sequenced before they enter the Body Shop. However, there are several events that can occur in the Body Shop and Paint Shop that disrupt the original sequence of bodies. The Selectivity Bank, a 24-position buffer between the Paint Shop and Assembly Shop, is used to reshuffle the order of the bodies back to an optimal sequence before they enter the Assembly Shop.
The schematic presented in Figure 1 represents the construction of the integrated model. The Body, Paint, and Assembly Shops were modeled using the SIMAN (Pegden 1994) simulation language. But, due to the relative complexity of the algorithms involved in operating the Selectivity Bank, the Selectivity Bank was modeled separately in the C ++ language and is accessed by the Paint Shop model via files and event statements. As the schematic shows, the integrated model receives input from an ASCII text file containing information on the model mix. The model mix was developed from data provided by MBUSI. The data defined indicated the accessories and the percentage of the vehicles that will carry the given accessory. The model mix was developed under the assumption that high-end cars will have many options, and that low-end cars will have fewer options.
Model development
Once all data had been collected, the individual Body, Paint, Selectivity Bank, and Assembly Shop models were developed. Each of the models is explained below in details.
Body shop model
The Body Shop has a total of 35 stations. The skid system of the Body Shop was included in the simulation model. There is a marriage station, at which a body is placed on a particular skid and remains attached to this skid until it gets to a divorce station whereupon the two separate. The current design consists of 35 skids, whereas the skid system or skid cycle contains 45 stations, with 38 stations where a body can be stationed. The number of skids serves as a natural constraint on the in-process inventory of the Body Shop, with 35 being the maximum number of bodies in the cycle.
The cycle time, which is defined as the total amount of time it takes for a body to enter the station, receive work, and leave the station, is different from 178 to 209 seconds depending on the type of bodywork completed at the station. The mean cycles between failures (MCBF) and mean time to repair (MTTR) for the Body Shop are different from station to station. No repair time takes more than 23 minutes, and the minimum repair time is modeled as two minutes. The mean cycles between failures (MCBF) were converted into mean time between failures (MTBF) by multiplying the cycle counts by the station cycle time to make analysis easier with SIMAN.
The belt conveyor of the Body Shop is modeled as a no-gap conveyor. No-gap implies that there are no empty positions on the conveyor. This means that the conveyor will stop if there is no body waiting to be transferred at the station just after the divorce station. The stations on the conveyor are manual stations. Each station is designed to complete its work within the takt time of 215 seconds. The conveyor also has a certain operational downtime associated with it. The downtime can be due to mechanical failure of the conveyor, or due to a mechanical failure at the stations. Any failure stops the conveyor.
Paint shop model
The Paint Shop has 101 stations in total. The cycle times are quite different from 6 to 300 seconds. The mean time to repair (MTTR) is modeled as five minutes, with no repair taking more than 23 minutes, or less than two minutes. Several features unique to the Paint Shop are modeled. During times of scheduled failures or breaks, bodies empty into designated strip out areas. For the purpose of the simulation model, three distinct pre-strip out areas and strip out areas are defined. The system is modeled such that a body may not enter any pre-strip out area unless there is enough space in the strip out area to hold at least 70% of the bodies in the pre-strip out area. Second, parallel lines are modeled such that under normal operating conditions bodies are sent to the two stations alternately. If one line fails, bodies are sent to the line that is operating. Third, major repairs and spot repairs on a body are modeled. A total of 11.3 % of all bodies are sent to the major repair area and a total of 12.6 % of all bodies are sent to the spot repair area. A body may not receive more than two major repairs or more than 4 spot repairs.
Not all Paint Shop conveyors are modeled using the SIMAN Conveyors element. Some of them are modeled as queues and resources. This is performed to more accurately model special features, such as no-gap conveyors.
The conveyors that were modeled as resources simply follow the operating schedule by means of the SIMAN Schedules element and the machine breakdown by means of the SIMAN Failure element. For the conveyors that were modeled with the Conveyor element, a small submodel is written to start or stop the conveyors at the appropriate times to model the operating schedule and the machine breakdown.
Selectivity bank
The Selectivity Bank was developed as a C++ program. It is an external program that is accessed via files and event statements. The purpose of the Selectivity Bank, a 24- position buffer between the Paint Shop and the Assembly Shop, is to restore the sequence of cars coming out of the Paint Shop and going into the Assembly Shop. The various options available on the AAV take different amounts of time to install. It is therefore important to balance the sequence of vehicles in a way that provides the smoothest assembly process over time.
The Selectivity Bank is laid out in a series of six rows. Each row has four positions. This is illustrated in Figure 2. The numbers in the cells represent the sequence numbers of bodies. Positions without a body are marked as “empty.” As bodies enter the Selectivity Bank from the left, they are directed to the row with the fewest bodies. In this case, a car would be placed on row 6, since it has the fewest number of bodies.
There are rule sets that control the Selectivity Bank. Rule sets contain the criteria for selecting the next car to leave for the Assembly Shop. The rules are currently divided into three separate rule sets. The oldest car in the Park, Matson and Miller Selectivity Bank will be chosen as the first candidate for leaving for the Assembly Shop. It will have to pass all three rule sets in order to be removed from the Selectivity Bank. If it fails any of the rule sets, then the next oldest car will be selected for evaluation and the process continues until a car passes all three rule sets. If no car passes, then the oldest car is sent to the Assembly Shop.
Assembly shop model
The Assembly Shop consists of seven conveyor lines: Trim 1 Line, Trim 2 Line, Final Line, Chassis Line, Door Line, Engine Line, and Axle Line. Of the seven, the first four conveyors are modeled as non-accumulating conveyor systems, but the last three are modeled as resources (Savory and Mackular 1997). Buffers between the Trim 1 conveyor, the Trim 2 conveyor, the Final conveyor, and the Chassis conveyor lines define in-process storage. The cycle times used for each station on the conveyors and the lifter station is 3.6 minutes (216 seconds). All idle stations including buffers are assumed to cycle in 15.7 seconds. The assembly lines are assumed to incur mechanical breakdowns on a random basis. Initially, the mean time between failures (MTBF) and the mean time to repair (MTTR) were calculated using uptime percentages and repair times provided by the Chiyoda engineering subcontractor. But the MTBF and MTTR were revised to represent a more realistic situation after discussion with the MBUSI engineers. A truncated exponential distribution was assumed for both parameters (Jayaraman and Agarwal 1996). It was assumed that repair times would take 5 minutes on the average, and will never exceed 23 minutes or be less than 2 minutes.
Two types of input data are defined for the simulation models, operational data and process data (Thomson 1995). Operational data includes all data relevant to the general operations of the system, such as the layout schematics of the shops and the operational logic of the shops. Process data are the specific data used to drive the shops, such as the time between failures, the time to complete a repair, the daily operating schedule, the repair percentage, and the conveyor speeds and types. MBUSI engineers provided the operational data and the process data were primarily obtained from the company’s Standard Method & Procedures (SM&P) sheets.
After the models were developed, they were verified with the SIMAN trace reports in details. The SIMAN trace reports can be a very useful tool for model verification because it details the movement of entities (vehicles) from block to block and the processing of each entity at each block. Once the models have been verified with the SIMAN trace reports, each of them was again verified and validated through a series of meetings with MBUSI engineers and the project contact person. After deciding that the four individual models were correct, they were combined to form an integrated model of the MBUSI assembly plant.
Analysis
The integrated simulation model of the assembly plant has been run with the vehicle data generated from the SM&P Sheets as mentioned. Each run of the simulation model used a warm-up period of five days followed by 20 replications of one day each. Each day is 24 hours in length, contains two shifts, and operates according to the production schedule provided by MBUSI. This schedule includes the time required for all work and breaks. A run length of 20 days was chosen because it accurately portrays the behavior of the system. Comparisons were made between run lengths of 20 days and 100 days, and the differences in output were statistically insignificant.
Using the completed integrated model, statistics regarding the total number of cars in each of the three shops at any given time were collected. These statistics were generated using counters: a counter for a particular shop was incremented when a car entered the shop and the same counter was decreased when a car left the shop. The main objective of this study was to verify that the daily throughput requirements could be met by the current design of the AAV assembly facility. Additional objectives were to address the other management issues, such as the maximum throughput (capacity) of the facility, the daily distribution of throughput, the buffers’ behavior in terms of quantity fluctuations, and the possible bottlenecks to the desired throughput. Each of the objectives is taken into consideration during the process of simulation analysis. The results of simulation analysis are summarized below in terms of each objective.
Throughput: The issue of whether or not the current design can produce the required throughput of 270 cars per day was addressed by studying confidence intervals representing the throughput values for each of the three shops. The display for each statistic provides both the minimum and maximum values recorded for the statistic.
It also provides the 95% confidence intervals with the average value clearly marked. The confidence interval indicates the range of values in which one can be 95% confident that the actual value will fall. Table 1 provides the average throughputs with their 95% confidence intervals for the Body, Paint, and Assembly Shop. Simulation and Analysis of The Mercedes-Benz All Activity Vehicle (AAV) Production Facility
Inspection of the confidence intervals for the Assembly Shop daily throughput value indicates that the average throughput for the facility is 257 cars per day. Ninety–five percent of the time, the daily throughput value falls between 254 and 260 cars per day. These results indicate that the current design does not produce the required throughput of 270 cars per day.
Maximum Throughput Capacity: The maximum throughput capacity, also known as the theoretical maximum capacity, of the facility was determined by running the model without the effects of unscheduled downtime for a warm-up period of five days followed by 20 replications of one day each. A maximum throughput capacity of 289 cars per day was observed.
Buffer Fluctuations: Statistics regarding the fluctuation of the buffers of the Body Shop, the Paint Shop, and the Assembly Shop were collected. Specifically, in the Assembly Shop, the Trim 1 buffer remains full the majority of the time while the Chassis buffer remains empty almost 40% of the time, which indicates that a lack of chassises is a problem in the Assembly Shop. Each body must be paired with a chassis before final line processing can begin. If the chassis buffer is empty a large percentage of the time, then bodies are delayed until a chassis becomes
available.
Bottlenecks: After running the Body, Paint, and Assembly Shop models separately and comparing the individual model results to the integrated model results, it becomes evident that the Assembly Shop is the bottleneck to the desired throughput. This is best indicated by the fact that the Selectivity Bank remains full a large majority of the time, causing cars to back up onto the end of the Paint Shop. This implies that the Paint Shop is processing bodies faster than the Assembly Shop.
In an attempt to improve the Assembly Shop throughput, an experiment was run where the Chassis Line operated on a different schedule. For this particular experiment, the Chassis Line lifter was run longer at the end of each shift so that the Chassis buffer could fill and therefore begin each shift at its maximum capacity.
The results of this experiment do not show any improvement in terms of the average throughput, which indicates that the Chassis Line alone is not the only impediment to the system. Other throughput improvement scenarios need to be run and evaluated. These throughput improvements will focus on the speeds of the Trim 1, Trim 2, Chassis, and Final lines.
Conclusion
The purpose of the study was to develop a detailed simulation model of the AAV assembly plant to determine whether it can reach the targeted output of 270 cars per day. The models of the Body Shop, Paint Shop, Selectivity Bank, and Assembly Shop were developed and analyzed based on a five-day warm-up period followed by twenty one-day replications. Statistics are collected from each replication and tested statistically for their significance. Examination of the results reveals that the current plant design cannot consistently yield 270 cars per day. The fact that the Selectivity Bank remains full most of the time indicates that the Assembly Shop is the current bottleneck to the system.
It is recommended that work on the detailed Assembly Shop model continue. Once this work is complete, the model will provide a more accurate evaluation of the performance of the production facility as a whole. The model can then be used to study issues such as how to increase the daily throughput goal of the plant to a number other than 270 cars per day.
The completed integrated model, including the more detailed version of the Assembly Shop, may be used by MBUSI to explore several different issues. For instance, ways to increase daily throughput of the plant beyond the current goal of 270 cars per day may be studied. For a given desired throughput, the model can be used to determine the required cycle times and conveyor speeds. Completion of this task will provide MBUSI an accurate indication of how well the facility will perform under higher throughput demands.
Author biographies young
- PARK is a Professor of Industrial Engineering at the Kwandong University in Koria. Dr.Park has his Ph.D. in Management Science from the Park, Matson and Miller University of Alabama, an MBA from the University of Arkasas, and a BA in Business Administration from the Kangweon National University. Dr. Park’s research interests are in the areas of system simulation, management information system, and statistics. Dr. Park is currently a visiting scholar at the Alabama Productivity Center, University of Alabama. JACK E. MATSON has over ten years of industrial experience as a manager with the Bell System in MIS and strategic planning and four years as the owner of a small business. Since 1991, has been a faculty member in the Industrial Engineering Department at the University of Alabama where he has taught the management-related courses in the Industrial Engineering curriculum, including engineering management, engineering economics, statistics, quantitative methods, simulation, and project and systems design.
The companies that he has consulted with include Mercedes-Benz, ACIPCO, Alabama Power Company, Goodyear Tire, NASA, Delphi Saginaw Steering Systems, as well as smaller industries such as Gulf States Steel, Royal Cup Coffee, Speedring, and American Olean. Dr. Matson received the Ph.D. in Management Science from The University of Alabama and the M.S. in Industrial Engineering from Mississippi State University. DAVID M. MILLER is currently a Professor of Management Science at the University of Alabama as well as Director of the Alabama Productivity Center. His professional honors include being appointed as the Reese Phifer Faculty Fellow in Manufacturing Management, selection as a Fellow in the World Academy of Productivity Sciences, appointment as a 1992 Malcolm Baldrige National Quality Award examiner as well as being listed in the International Who’s Who in Quality and the Who’s Who in Technology. Dr. Miller holds a Ph.D. in Industrial Engineering and Operations Research from the Georgia Institute of Technology. He also holds a masters in Industrial Engineering from Georgia Tech, along with a BS degree in Industrial Engineering from the University of Alabama. He has published over 45 professional articles in journals such as the Harvard Business Review and Management Science, as well as a text book on Industrial Engineering. In his capacity as Director of the Alabama Productivity Center, Dr. Miller oversees a $750,000 annual operation involving 15-18 industrial projects and 30 graduate students. Since starting the Center in 1986, he has directed over 200 projects in industries ranging from steel fabrication to apparel.
Cite this Page
Simulation model for Mercedes-Benz production facility in Alabama. (2018, Mar 28). Retrieved from https://phdessay.com/simulation-and-analysis-of-the-mercedes-benz-all-activity-vehicle-aav-production-facility/
Run a free check or have your essay done for you
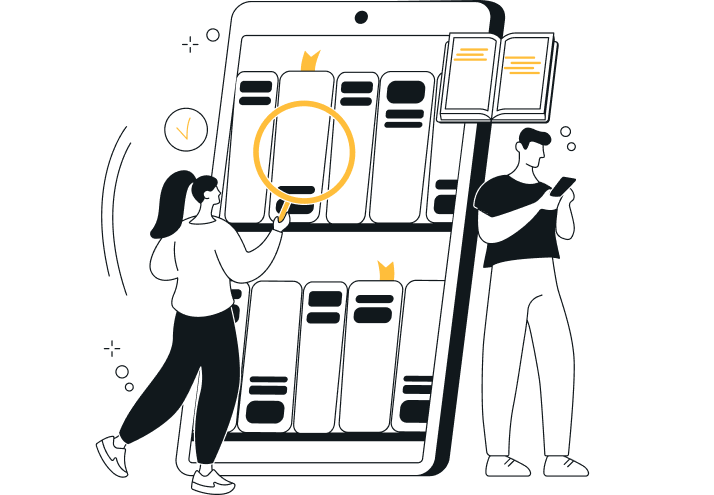