Process Safety And Loss Prevention Plant Engineering Essay
The system in figure 1 schematic of a nomadic incineration unit. The equipment is arranged as a skid-mounted bundle, recess and out pipes have been disconnected from the unit.for the care purpose unit can be skidding out to open infinite and accessing needed constituents straight, or subsequently taking constituents from the unit in order to derive the entree. All supply and waste connexion are from the unit. Because of cramped conditions. Figure 2 shows the forepart and side positions of the unit are 2.5m tallness, 5m deep, 2m broad.
Components:
- Heat money changer ( EX )
- Rotary kiln ( RK )
- Scrubbing unit ( SC )
- Temperature accountant ( TC )
- Fan motor ( FM )
- Screw feeder ( SW )
- Screw motor ( SM )
- Feed hopper ( FH )
Order custom essay Process Safety And Loss Prevention Plant Engineering Essay with free plagiarism report
The kiln, heat money changer, and scrubber are each secured to the border by 6 bolts and there are 4 connexions to each of the motors. The whole unit can be slid out to let care utilizing raising cogwheel and this requires 20 proceedings to hale out and 40 proceedings to return. The clip takes to take nuts and bolts 2 proceedings and the clip takes to replace 5 proceedings. MTTR ( Average Time To Repair ) is besides known as Mean Corrective Tim - MCT or TC is the colored norm of the fixed times for the system.
Calculation of MTTR when the unit is slid out for fix:
Here failure constituents are removed from unit and it will be repaired and replaced to unit.
Components:
- Heat money changer ( EX )
- Rotary kiln ( RK )
- Scrubing unit ( SC )
- Temperature accountant ( TC )
- Fan motor ( FM )
- Screw feeder ( SW )
- Screw motor ( SM )
- Feed hopper ( FH )
- Formula for MTTR:
- TE†c = [ a?‘ni=1 ( I»i.Tc ( I ) ) ] / a?‘ni=1 ( I»i )
Where:
- TE†c ( I ) is the disciplinary clip for the i'th unit.
- I»i is the failure rate of the i'th unit.
- N is the figure of unit. [ 2 ]
- Failure informations ( I» ) :
- Heat exchanger failure rate ( I» ) = 40 ( failure per 10^6hours ) or 40A-10^-6hours [ 3 ]
- Rotary kiln ( I» ) basic constituents of a rotary kiln are the shell, the furnace lining liner, support tires, rollers, driven cogwheel and internal heat money changer. So rotary kiln failure rate we may gauge amount of all constituents which are utilizing to do rotary kiln.
- Under technology premise rotary kiln failure rate ( I» ) = 30 ( failures per 106hours ) or 30A-10-6 hours
- Under technology premise Scrubbing unit failure rate ( I» ) = 45 ( failures per 106hours ) or 45A-10-6hours
- Under technology premise fan failure rate ( I» ) = 57 ( failures per 106 hours ) or 57A-10-6
- Corrective clip for constituents ( Tc ) :
- ( Tc ) = Tdet + Tloc + Tpla + Tsel + ( Tpre / Tlog ) + ( [ Trem + Trep ] /Trip ) + Tver + Tstu
- Tdet = observing mistake
- Tlo = placement failure
- Tala = be aftering the work
- Ts = select the failed point
- Tpre = shutdown & A ; readying
- Tlog = logistics clip
- Trem = remotion of failed point
- Trep = replacing of failed point
- Trip = repair-in-place
- Tver = verify the repaired point
- Tstu = re-start [ 4 ]
- Corrective clip for heat money changer ( Tc )
The heat money changer has four connexions in the unit and heat money changer framed by 6 bolts and nuts so clip to take that constituent ( heat money changer ). Entire nuts and bolts for the heat money changer in the unit = 6. Time is taken to take bolts and nuts at each connexion = 2 proceedings. So clip taking to take heat exchanger = 6A-2 = 12 proceedings. Time taking to replace bolts and nuts at each connexion = 5 proceedings. Time taking to replace heat money changer = 6A-5 = 30 proceedings. And we have to unplug the connexions here we have an entire 4 connexions. Time taking to unplug the pipeline the unit line from the whole unit.
Components:
- Heat money changer ( EX )
- Rotary kiln ( RK )
- Scrubing unit ( SC )
- Temperature accountant ( TC )
- Fan motor ( FM )
- Screw feeder ( SW )
- Screw motor ( SM )
- Feed hopper ( FH )
- The formula for MTTR:
- TE†c = [ a?‘ni=1 ( I»i.Tc ( I ) ) ] / a?‘ni=1 ( I»i )
- Where:
- TE†c ( I ) is the disciplinary clip for the i'th unit.
- I» i is the failure rate of the i'th unit.
- N is the figure of unit. [ 5 ]
Failure informations ( I» ) :
Heat exchanger failure rate ( I» ) = 40 ( failure per 10^6hours ) or 40A-10^-6hours [ 6 ]
Rotary kiln ( I» ) basic constituents of a rotary kiln are the shell, the furnace lining liner, support tires, rollers, driven cogwheel, and internal heat money changer. So rotary kiln failure rate we may gauge the amount of all constituents which are utilizing to do rotary kiln. Under technology premise rotary kiln failure rate ( I» ) = 30 ( failures per 106hours ) or 30A-10-6 hours. Under technology premise Scrubbing unit failure rate ( I» ) = 45 ( failures per 106hours ) or 45A-10-6hours. Under technology premise fan failure rate ( I» ) = 57 ( failures per 106 hours ) or 57A-10-6
Corrective clip for constituents ( Tc ) :
( Tc ) = Tdet + Tloc + Tpla + Tsel + ( Tpre / Tlog ) + ( [ Trem + Trep ] /Trip ) + Tver + Tstu
- Tdet = observing mistake
- Tlo = placement failure
- Tpla = be aftering the work
- Ts = select the failed point
- Tpre = shutdown & A ; readying
- Tlog = logistics clip
- Trem = remotion of failed point
- Trep = replacing of failed point
- Trip = repair-in-place
- Tver = verify the repaired point
- Tstu = re-start [ 7 ]
here we don't necessitate to take constituents from unit for fix
Corrective clip for heat money changer ( Tc ) :
Instrumentality which has system is utile to find the mistakes.so instrumentality in this system temperature accountant ( TC ): Here TC maps to modulate the temperature of the liquid come ining the heat money changer that is, it pre-controls the liquid come ining the heat money changer. As shown in the figure, the temperature accountant modulates the temperature of the liquid released from the heat money changer and before being cooled by the fan which is control by the fan motor. So temperature accountant is utile to observing the mistake which may happen in the heat money changer. Based on the given figure it can be likely to assume that the degree index may be used for the rotary kiln. a flat index is placed at the top of the rotary kiln. This is used is indicate the maximal degree of the mixture that can be accommodated in a rotary kiln. So this may be indicated the mistakes if anything occurs. A flow rate valve is placed in the scrubber unit, so as to command the flow rate alkalic solution into the scouring unit. This flow rate valve allows merely the coveted sum of the solution into the scouring unit. Once the coveted degree is reached the valve will automatically close off the flow of liquid into the unit. And we have some detector dismay at the fan and fan motor and screw motor why because if these have any jobs will give the signals so we can easily find the mistakes.
Question description:
The procedure works to respond to liquid A and liquid B to bring forth merchandise C. liquid A passing into storage A utilizing liquid accountant. From storage it will pump to reactor. Liquid B goes throughing storage B utilizing liquid accountant from storage B to pumping to the reactor. From the reactor, merchandise C coming out. Acid gas from reactor pumping to scouring unit. In the scouring unit, acid gas is cleaned utilizing an alkali solution that is going through into the scouring unit. Scrubing unit leaves impersonal waste watercourse. Liquids are ever available at the recesses to the procedure. There are at least two scouring units working right for the procedure. Stand-by pumps switch over automatically. Pipework failures can be ignored. [ 1 ]
Available information:
- Alarm failure
- Liquid control
- LAL fails
- Liquid control
- Low degree
- High degree
- Agitator failure
- Coking job
- Motor failure
- Shaft break
- High degree
- Low degree
- Excess flow of liquid Angstrom
- Excess flow of liquid B
- Reactor
- Pump failure
- 2 ( a ( two ) )
- Fault tree analysis here liquid waste watercourse composing outside bounds is the top event
- Low degree
- High degree
- Internal mal maps failure
- Connection fails between scrubbers
- Improper cleansing temperature
- Improper alkaline solution pumping to the scrubber unit
- Scrubber unit failure
- Improper flow reactor to the scrubber
- High degree
- Low degree
- Low degree
- High degree
- 2a ) computation of dependability of parts of the system
- Here parts of the system:
- Storages
- Reactor
- Agitator
- Pumps
- Scrubing unit
- Dependability of reactor:
- Here reactor failure can affect the fomenter failure. First one is shaft break and 2nd one is motor failure
- The failure rate of shaft break = 0.1/year
- The failure rate of the motor = 0.3/year
- Scrubber unit has a weilbull failure characteristic with I· = 600 yearss, I? = 60days, and I? = 1.8 [ 1 ]
- Failure rate of pump ( I» ) = 13A-10-6hours [ 2 ]
- Dependability of shaft break:
- Equation for failure rate:
- Z ( T ) = I?/I·I? ( t-I? ) I?-1
- Here I? = form factor
- I· = characteristic life
- I? = location parametric quantity
- T = lasting a clip
- Equation for the dependability:
- R ( T ) = e- ( ( t-I? ) /I· ) ^6 [ 3 ]
- Failure rate of shaft break = 0.1/year
- So utilizing this we are happening T
- Z ( T ) = I?/I·I? ( t-I? ) I?-1
- 0.1/year = ( 1.8/ ( 600 ) 1.8 ) A- ( t-60 ) 1.8-1
- Here one twelvemonth = 365 yearss
- 0.1/365 = ( 1.8/ ( 600 ) 1.8 ) A- ( t-60 ) 1.8-1
- T = 90.11 yearss
- Equation for the dependability:
- R ( T ) = e- ( ( t-I? ) /I· ) ^6
- = 0.995
- So dependability for shaft break = 0.995
- Dependability of motor:
- Equation for failure rate:
- Z ( T ) = I?/I·I? ( t-I? ) I?-1
- Here I? = form factor
- I· = characteristic life
- I? = location parametric quantity
- T = lasting a clip
- Equation for the dependability:
- R ( T ) = e- ( ( t-I? ) /I· ) ^6
- Failure rate of the motor = 0.3/year
- So utilizing this we are happening T
- Z ( T ) = I?/I·I? ( t-I? ) I?-1
- 0.3/year = ( 1.8/ ( 600 ) 1.8 ) A- ( t-60 ) 1.8-1
- Here one twelvemonth = 365 yearss
- 0.3/365 = ( 1.8/ ( 600 ) 1.8 ) A- ( t-60 ) 1.8-1
- T = 177.29 yearss
- Equation for the dependability:
- R ( T ) = e- ( ( t-I? ) /I· ) ^6
- = 0.948
- So dependability for motor = 0.948
- Dependability for scouring unit:
- Equation for failure rate:
- Z ( T ) = I?/I·I? ( t-I? ) I?-1
- Here I? = form factor
- I· = characteristic life
- I? = location parametric quantity
- T = lasting a clip
- Equation for the dependability:
- R ( T ) = e- ( ( t-I? ) /I· ) ^I?
- Here we have the T = 133.6 yearss
- Z ( T ) = I?/I·I? ( t-I? ) I?-1
- Z ( T ) = ( 1.8/ ( 600 ) 1.8 ) A- ( 133.6-60 ) 1.8-1
- Z ( T ) = 0.2/year
- Equation for the dependability:
- R ( T ) = e- ( ( t-I? ) /I· ) ^I?
- = 0.996
- So dependability for scouring unit R ( T ) = 0.996
- Dependability of pump:
- Failure rate of pump ( I» ) = 13A-10-6hours
- Dependability of pump R ( T ) = e-I»t
- Surviving clip t = 70 yearss
- One twenty-four hours = 24 hours
- Surviving clip T = 1680 hours
- Dependability of pump R ( T ) = e-I»t
- = vitamin E ( -13A-10^-6A-1680 )
- Dependability of pump R ( T ) = 0.978
Mentions:
- Plant dependability and maintainability, assignment inquiry paper, faculty ( CPE6250 ) held on November 30 to December 3, 2009.
- Frank P. Lees, 1996, Loss bar in the procedure industries, 2nd edition, volume 3.
- Cris Whetton, ility technology. Failure information analysis. [ Lecture press release ] .from works dependability and maintainability, faculty ( CPE6250 ) held on November 30 to December 3, 2009.
Here parts of the system:
- Storages
- Reactor
- Agitator
- Pumps
- Scrubbing unit
Dependability of reactor:
- Here reactor failure can affect the fomenter failure. First one is shaft break and 2nd one is motor failure
- The failure rate of shaft break = 0.1/year
- The failure rate of the motor = 0.3/year
- Scrubber unit has a Weibull failure characteristic with I· = 600 years, I? = 60days, and I? = 1.8 [ 1 ]
- Failure rate of pump ( I» ) = 13A-10-6hours
- Failure rate of fan ( I» ) = 57A-10-6hours [ 2 ]
Dependability of shaft break:
Equation for failure rate:
- Z ( T ) = I?/I·I? ( t-I? ) I?-1
- Here I? = form factor
- I· = characteristic life
- I? = location parametric quantity
- T = lasting a clip
Equation for the dependability:
- R ( T ) = e- ( ( t-I? ) /I· ) ^6 [ 3 ]
- Failure rate of shaft break = 0.1/year
- So utilizing this we are happening T
- Z ( T ) = I?/I·I? ( t-I? ) I?-1
- 0.1/year = ( 1.8/ ( 600 ) 1.8 ) A- ( t-60 ) 1.8-1
- Here one twelvemonth = 365 yearss
- 0.1/365 = ( 1.8/ ( 600 ) 1.8 ) A- ( t-60 ) 1.8-1
- T = 90.11 yearss
Equation for the dependability:
- R ( T ) = e- ( ( t-I? ) /I· ) ^6 = 0.995
- So dependability for shaft break = 0.995
Dependability of motor:
Equation for failure rate:
- Z ( T ) = I?/I·I? ( t-I? ) I?-1
- Here I? = form factor
- I· = characteristic life
- I? = location parametric quantity
- T = lasting a clip
Equation for the dependability:
- R ( T ) = e- ( ( t-I? ) /I· ) ^6
- Failure rate of the motor = 0.3/year
- So utilizing this we are happening T
- Z ( T ) = I?/I·I? ( t-I? ) I?-1
- 0.3/year = ( 1.8/ ( 600 ) 1.8 ) A- ( t-60 ) 1.8-1
- Here one twelvemonth = 365 yearss
- 0.3/365 = ( 1.8/ ( 600 ) 1.8 ) A- ( t-60 ) 1.8-1
- T = 177.29 yearss
Equation for the dependability:
- R ( T ) = e- ( ( t-I? ) /I· ) ^6 = 0.948
- So dependability for motor = 0.948
Dependability for scouring unit:
Equation for failure rate:
- Z ( T ) = I?/I·I? ( t-I? ) I?-1
- Here I? = form factor
- I· = characteristic life
- I? = location parametric quantity
- T = lasting a clip
Equation for the dependability:
- R ( T ) = e- ( ( t-I? ) /I· ) ^I?
- Here we have the T = 133.6 yearss
- Z ( T ) = I?/I·I? ( t-I? ) I?-1
- Z ( T ) = ( 1.8/ ( 600 ) 1.8 ) A- ( 133.6-60 ) 1.8-1
- Z ( T ) = 0.2/year
- Equation for the dependability:
- R ( T ) = e- ( ( t-I? ) /I· ) ^I? = 0.996
- So dependability for scouring unit R ( T ) = 0.996
Dependability of pump:
- Failure rate of pump ( I» ) = 13A-10-6hours
- Dependability of pump R ( T ) = e-I»t
- Surviving clip t = 70 yearss
- One twenty-four hours = 24 hours
- Surviving clip T = 1680 hours
- Dependability of pump R ( T ) = e-I»t = vitamin E ( -13A-10^-6A-1680 )
- Dependability of pump R ( T ) = 0.978
- Dependability of the complete system over twelvemonth R ( T ) = norm of system parts dependability
- = ( 0.995+0.948+0.996+0.978 ) /4 = 0.979
- Therefore dependability of the complete system over twelvemonth = 0.979
Mentions:
- Plant dependability and maintainability, assignment inquiry paper, faculty ( CPE6250 ) held on November 30 to December 3 2009.
- Frank P. Lees, 1996, Loss bar in the procedure industries, 2nd edition, volume 3.
- Cris Whetton, ility technology. Failure information analysis.
To accomplish mark dependability of 0.90 over one twelvemonth:
The reliability mark is a nothing failure mark. This is an of import mark implied for those low acting workss, such works do non accomplish certain ends designed by applied scientists. So we have to put an appropriate mark to accomplish works design. the dependability of the system must be improved to accomplish the mark. to accomplish the dependability mark or to better dependability three basic ways must be employed.
By component specification:
For the dependability of a constituent, it must be adequately specified for its full length of service. Extra dependability can be provided by runing the constituents at lower emphasis so their operating emphasizes. By making so early failures of the constituents can be reduced. in a procedure industry, it is really hard for better dependability merely by the specification. This is attributed to the deficit of necessary information sing the effect of the emphasis on the constituents. Components of high quality can non be used ever for economic grounds. Normally the parametric quantities required to better dependability frequently contradict procedure demands.
Some of the dependability betterments include:
Use of disciplinary maintenance- it is defined as the care which is required to mend and convey merchandise after the fix is carried out. it is carried out in constituents who are failures don't impact of the overall working of the procedure system significantly. This activity chiefly involves fix, Restoration or replacing of constituents. Design improvement-the design of any high-quality procedure works is based on the design of parametric quantities and proficient specifications. the reactor design must be improved for high rates of efficiency. Temperature, force per unit area, and other external considerations must be included in the design of reactor and storage armored combat vehicles. Quality control-Quality control assures conformity to specifications. quality control checks whether measurings of the constituents like reactors, storage armored combat vehicle, scrub units as in this instance conform to the demands.
Preventive care:
Is defined as care carried out to forestall failure or warring out of constituents in the procedure works. This is carried out by supplying systematic review, sensing, and a bar of inchoate failure. The preventive care attempts are aimed at continuing the utile life of the equipment and avoiding premature equipment failures, minimizing any impact on operational demands. In add-on to the everyday facets of cleansing, adjusting, lubricating, and proving. it is carried out merely on those points where a failure would hold expensive or unacceptable effects e.g. reactors, storage armored combat vehicles, scouring units. Many of these points are besides capable of a statutory demand for review and preventative care.
Cite this Page
Process Safety And Loss Prevention Plant Engineering Essay. (2018, Aug 18). Retrieved from https://phdessay.com/process-safety-and-loss-prevention-plant-engineering-essay/
Run a free check or have your essay done for you
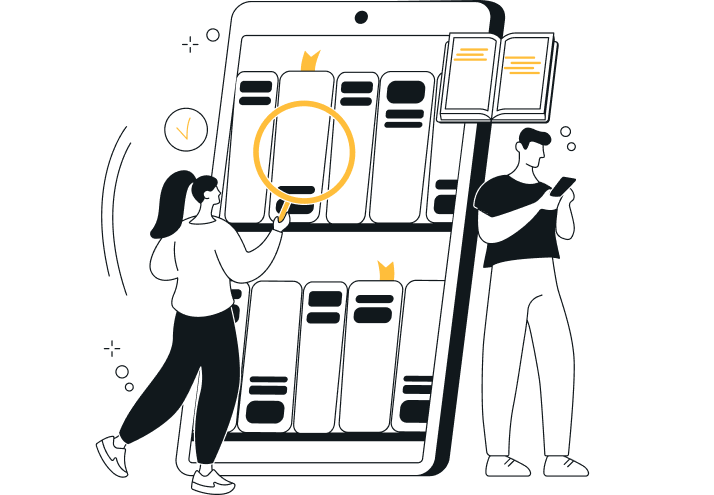