Sustainable Development in Kazakhstan
The Institute of Metallurgy and Ore Benefaction, Almost, Republic of Astrakhan 2 Abstract The Republic of Astrakhan is continuing to develop its extensive petroleum reserves in the Tenting region of the northeastern part of the Caspian Sea. Large quantities of by-product sulfur are being produced as a result of the removal of hydrogen sulfide from the oil and gas produced in the region. Lack of local markets and economic considerations limit the traditional outlets for byproduct sulfur and the buildup of excess sulfur is a becoming a potential economic and environmental liability.
Thus, ewe applications for re-use of by-product sulfur that will benefit regional economies including construction, paving and waste treatment are being developed. One promising application involves the cleanup and treatment of mercury at a Astrakhan chemical plant. During 19 years of operation at the Palomar Skimpier color-alkali production facility, over 900 tons of mercury was lost to the soil surrounding and beneath the buildings.
The Institute of Metallurgy and Ore Benefaction (Almost) is leading a team to develop and demonstrate a vacuum- assisted thermal process to extract the mercury from the soil and concentrate it as ere, elemental mercury, which will then be treated using the Sulfur Polymer Stabilization/Solidification (SPAS) process. The use of locally produced sulfur will recycle a allowable industrial by-product to treat hazardous waste and render it safe for return to the environment, thereby helping to solve two problems at once.
Order custom essay Sustainable Development in Kazakhstan with free plagiarism report
SPAS chemically stabilizes mercury to mercuric sulfide, which has a low vapor pressure and low solubility, and then physically encapsulates the material in a durable, monolithic solid sulfur polymer matrix. Thus, mercury is placed in a solid form very much like stable cinnabar, the form in which it is found in nature. Previous research and development has shown that the process can successfully encapsulate up to 33 wet% mercury in the solid form, while still meeting very strict regulatory standards for allocable mercury (0. 025 MGM/l in the Toxicity Characteristic Leaching Procedure).
The research and development to deploy Astrakhan recycled sulfur for secondary applications described in this paper is being conducted with support from the International Science and Technology Center (CIST) and the U. S. Department of Energy Annihilates Tort Prolongation Prevention ( Introduction Since the breakup of the former Soviet Union, Astrakhan, like the other newly independent states (EN'S), has taken steps to rebuild its economy from the ground up. Unlike other small INS however, Astrakhan is fortunate to possess huge potential petroleum reserves in the Tenting region adjacent to the Caspian Sea.
Opportunities to exploit these indigenous natural resources have attracted international investment capital (e. G. , Covenanter, Complexion, Nine-Agape) enabling rapid construction and deployment of productive oil and gas wells. For example, Covenanter and the National Astrakhan company "Gunnysacks" formed partnership known as Tenderloins TCO), which is currently producing 13 million metric tons (284,000 able/d) of oil per year and expects to reach 23 million metric tons per year by 2006. Figure 1 . Map of Astrakhan and the surrounding region Kananga Salaam's Agrarian Estate Kananga Figure 2.
North Caspian Sea (left) and Kananga region (right) where Agape-CO will conduct petroleum exploration Agape-CO has signed an agreement with the Astrakhan government for development rights in the Kananga oil fields and expects initial production of 22 million metric tons per year in 2008, increasing to as much as 60 million metric tons re year. The location of Kananga and Tenting oil fields in Astrakhan can be seen in Figures 1 and 2. Astrakhan oil and gas is rich in hydrogen sulfide (HAS), which is removed as elemental sulfur during the production process.
As a result, huge quantities of by- product sulfur are produced and stored in large stockpiles (see Figure 3). Astrakhan based oil & gas companies currently recover 2,000 to 3,000 metric tons per day of elemental sulfur from their product streams (approximately 500 tons of elemental sulfur is recovered for every 100,000 barrels of extracted trolled in Astrakhan) [1]. In 2000, total world production of elemental sulfur was 57. 4 million tons, including 1. 4 million tons from Astrakhan [2]. The current sulfur stockpile exceeds 8 million tons at Tenderloins and is large enough to be seen from the Space Shuttle.
The Astrakhan Ministry of Environment, Figure 3. Sulfur storage at the Tenderloins concerned about the chronic build up of these facility "mountains of sulfur" will impose fines for continued storage. Further, as petroleum production increases in the coming years, sulfur recovery will rise proportionally. Agape-CO expects recovery of sulfur will rise to 5,770 metric tons/day at the Kananga Field and Tenderloins is planning an additional 2,400 ton/day facility to manage sulfur from the recovery of sour natural gas at the Tenting field [2].
Anticipating potential problems associated with this expected buildup of by-product sulfur, Engaging, the operating partner in Agape-CO, commissioned Battle Memorial Institute to conduct a study to assess potential applications for excess sulfur [1]. Battle identified a number of traditional markets for recycled sulfur in Europe and the U. S. Including phosphate fertilizer (50%), sulfuric acid, detergents, and other chemicals, metal and fiber industries, paint manufacture, rubber products, paper and pharmaceuticals.
Lack of local markets and the cost associated with transportation of the sulfur to distant markets make these options less attractive in Astrakhan. The study focused therefore, on applications that would have commercial benefit to the local economy, e. G. , use of sulfur based asphalt and concrete for paving, construction, and waste treatment. Sulfur can De uses to supplement petroleum-Dates bitumen in asphalt paving applications. As much as 50% by weight of the asphalt binder in asphalt concrete can be replaced with elemental sulfur.
This would allow Astrakhan, Russia, and other former Soviet Union countries to easily extend the output of their Figure 4. Sulfur modified concrete roadway demonstration at Tenting asphalt refineries and aid region-wide efforts to upgrade the highway infrastructure. Furthermore, the use of sulfur in asphalt concrete does not require any special additives and normal asphalt road paving equipment can continue to be utilized as the temperature of the asphalt binder is normally kept above the melting point of lawful.
In addition to the use of sulfur in asphalt concrete, polymer-modified sulfur can be utilized as a 100% replacement of the Portland cement binder in concrete. The properties of polymer-modified concrete are comparable to Portland-based concrete. Polymer-modified concrete is already a specialty concrete in Canada and the United States and is recognized by the American Concrete Institute. In 2002, K Interconnect (SKI), JSP, coordinated a large-scale demonstration project at Tenting to install a mom stretch of roadway using a standard asphalt plant and 2000 tons of a sulfur concrete mixture (Figure 4).
More recently, a sulfur extended asphalt demonstration was completed by the company Reconsider in Tartar, the oil capital of Astrakhan. These demonstration projects have helped open the door to new opportunities for secondary endues of sulfur within Astrakhan and surrounding countries and identified areas for further engineering research and development. For example, large-scale production of sulfur polymer in Astrakhan will require specialized equipment to precisely control mixture parameters. For optimal performance and safety, traditional asphalt paving equipment will need to be modified for reduction of odorous emissions.
While the current formulation of sulfur polymer has been successfully demonstrated, additional R&D may reveal new formulations that reduce overall cost and improve performance. Sulfur Polymer Elemental sulfur is a thermoplastic material that can be melted at ICC, mixed with aggregate and then cooled to form a solid product. The U. S. Bureau of Mines determined that it could be reacted with the addition of a small quantity of organic modifiers to form a sulfur polymer cement (SSP) that has added strength and durability compared with elemental sulfur [5]. When combined with aggregate, SSP an be used in place of conventional, hydraulic (e. . , Portland) cement concrete for construction applications. These include poured concrete footings, floors, walls, tanks, etc. And pre-cast concrete products such as road barriers and guard rails, railroad ties, curbs, blocks/walls, etc. ) Additional potential applications include fabrication of synthetic aggregate to form roadbed underpayment and for use in forming artificial retest at ten 011 recovery sites In ten Caspian sea. In tense applications, ten sulfur polymer is heated above the melt temperature, mixed with sand or stone aggregate, ND then cooled to form concrete.
SSP concrete has high compressive strength and is resistant to attack in harsh chemical environments so it is ideal for use in chemical production facilities. Unlike conventional hydraulic cement, SSP concretes do not require water for mixing and curing and thus are suitable for use in arid environments. Potential opportunities to use SSP for construction, paving, and chemical/industrial applications are beginning to emerge to help offset the need for low-cost building materials and infrastructure upgrades in Astrakhan's post-Soviet economy.
Further implementation of construction applications for recycled sulfur in Astrakhan is one of the objectives of the current project. Development of the capacity to produce viable secondary end-use products from the by-product sulfur will reduce the negative economic liability associated with safe storage and/or disposal of the sulfur reserves, and generate a potential positive income as the applications for SSP are exploited. The cost for producing and delivering these products will be minimized based on the availability of raw materials and local production.
Sulfur Polymer Stabilization/Solidification Under support from the U. S. Department of Energy (DOE), Brookhaven National Laboratory (BUN) has pioneered the use of SSP for environmental restoration and waste management applications including treatment of a wide range of hazardous, radioactive, and mixed wastes [610]. SSP can be used to simply physically encapsulate the waste (SSP miscalculations) and has been demonstrated for treating radioactive and mixed waste contaminated ash, soil, sludge, and evaporator concentrates. In a previous effort sponsored by the U. S. Environmental Protection
Agency, BUN established feasibility of using Astrakhan sulfur for the production of sulfur polymer cement (SSP) and its use for the encapsulation of waste [8]. Sulfur Polymer Stabilization/Solidification (SPAS) is a related process that chemically stabilizes and physically encapsulates the waste. The latter process was more recently developed to specifically treat elemental mercury and mercury contaminated soil, sludge and debris. The resulting final waste form product is durable under long-term disposal conditions and successfully immobilizers contaminants from the environment.
SPAS is a two-stage process. In the first stage, mercury and/or mercury-contaminated materials are reacted with the SSP and other reagents to form mercuric sulfide, which has a low vapor pressure and low solubility. The stabilized mercury product is a dispersible powder that is then heated with SSP to form a inhomogeneous molten mixture. When cooled, the product is physically encapsulated in a solid brick-like material. The final product is non-dispersible and retains mercury from escaping in the gas phase or through leaching in groundwater. Previous Figure 5.
Pilot-scale SPAS Process equipment installed at BUN research and placement has shown that the process can successfully encapsulate up to 33 wet% mercury in the solid form, while still meeting very strict regulatory standards for allocable mercury (0. 025 MGM/l in the Toxicity Characteristic Leaching Procedure)[10]. A pilot-scale SPAS process system is shown in Figure 5. Mercury Problems at Palomar The Palomar Chemical Plant in eastern Astrakhan was constructed by the Soviet Union beginning in the mid-asses The large (10 square mile) complex employed 6500, including 500 engineers.
Among other chemicals, chlorine and caustic soda ere routinely produced by electrolysis of a salt solution in a mercury cathode cell. Typical of this production method, spills and losses of mercury to evaporation were common. One report estimates that the total quantity of mercury lost was in the neighborhood of 3000 tons [11]. Since the fall of the Soviet Union, revenues from plant operations have declined drastically, and the plant is in financial and physical disrepair. For example, large spills of toxic mercury used for the production of chlorine and alkali have gone without remediation due to lack of funds.
Remediation of mercury-contaminated soil t Palomar, in collaboration with a related project supported by the International Science and Technology Center (CIST) is one of the objectives of this proposed work. A vacuum-assisted thermal retort system will be used to remove and condense mercury from the soil beneath and around the plant (see companion paper at the AREAS conference). The residual elemental mercury that is collected will then be treated using SPAS. Under support from CIST and DOE IPP for this newly funded project, a pilot-plant will be constructed at Palomar to produce SSP from Astrakhan sulfur.
The resulting SSP ill be used to conduct various demonstration projects including the production of SSP-based concrete products and the treatment of residual mercury that has been removed from the soil beneath and around the Palomar Chemical Plant. Summary and Conclusions Although faced with many of the difficult problems shared by other former Soviet countries, Astrakhan is fortunate to possess large reserves of petroleum that are just now being exploited. However, Khaki oil and gas is typically high in HAS that must be removed prior to sale on the open market.
The by-product sulfur currently as Eliminate commercial pathways Tort recycling Ana re-use Ana Is accumulating at a rapid rate. Over 8 million tons are already being stored and with new oil reserves scheduled to come on line within the next several years, this quantity will continue to grow rapidly. If left unresolved, the potential environmental and economic liabilities associated with the stored sulfur will pose an increasing risk for the international oil & gas oil companies operating in Astrakhan.
However, with creative solutions such as described in this paper, a plan for sustainable development that balances the reduction of by-products with appropriate cost-abating recycling options can be realized. Acknowledgements The authors would like to thank Mr.. James Noble (US DOE), Mr.. Andrew Hood, and Ms. Laura Schmidt-Williams (US Department of State) for their support of this project and Dry. Arturo Kankakee (Palomar Chemical Plant) for his assistance in providing logistical assistance.
Cite this Page
Sustainable Development in Kazakhstan. (2018, Aug 19). Retrieved from https://phdessay.com/sustainable-development-in-kazakhstan/
Run a free check or have your essay done for you
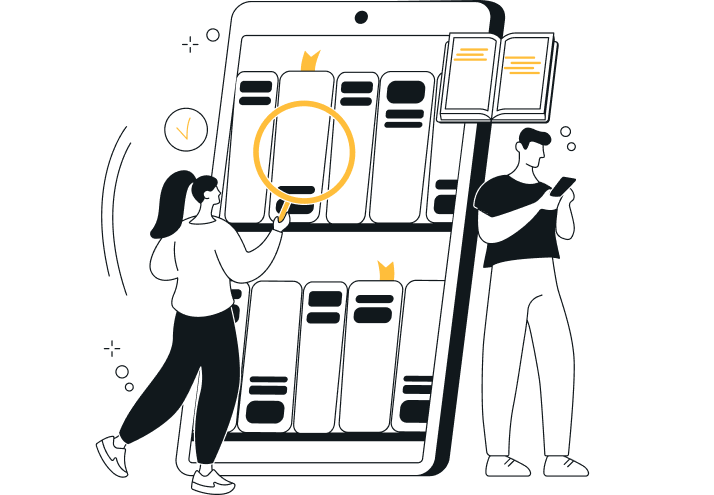