Hank Kolb Case
The following are the problems that Kolb’s production line has to address:
- Personnel - the operator of the filling equipment is not suitable for the job because of lack of knowledge and proper training 2
- The filling equipment – the machine is not particularly designed for filling the Greasex cans. It was originally made for other purpose.
- Maintenance – there is no definite schedule of preventive maintenance for the filling equipment.
- Purchasing – agents from purchasing have not yet finalized on a supplier that has non-defective nozzle to fit on the nozzle heads
- Product design and packaging – the contoured shape of the can is perceived to be catchy by the designers because of its easier to be gripped feature. But Kolb sees the shape as problem for filling
- The manufacturing manager – despite the favorable production quota from Simmons, have some issues for cost improvements and reduced delivery times that Kolb has to re-consider before filling in Simmons for promotion
- The marketing – the introduction of Greasex was rushed to market even if the product is still a bit off-spec
Order custom essay Hank Kolb Case with free plagiarism report
Suggestions
Using the Six-Sigma Analysis, Kolb should solve the major problems of his production line using the DMAIC as recommended below:
Define
- Identify customers and their priorities.
- Identify a project suitable for Six-Sigma efforts based on business objectives as well as customer needs and feedback.
- Identify the CTQs (critical-to-quality characteristics) that the customer considers to have the most impact on quality. Kolb should have in mind already the safety of the products to customers, not just target unit sales.
Being the new Director of Quality Assurance, he must look closely to the process and implement improvement to which the steps are causing trouble or maybe eliminate or change what is causing the trouble. It is also important that he has an active list of customer feedbacks that he would refer to every time he tries to improve his processes.
Measure
- Determine the measure the process and how it is performing.
- Identify the key internal process that influence the CTQs and measure the defects currently generated relative to those processes.
Kolb can use the three tools: Run Charts, Pareto Charts and Checksheets to measure the process and defects that are found (usually in in type and number of customer complaints). After seeing the influencing factors and types of defects, he will be able to decide whether replace or improve these influencing factors.
Analyze
- Determine the most likely causes of defects.
- Understand why defects are generated by identifying the key variables that are not likely to create process variation.
Kolb can make use of the Fishbone Chart to analyze the causes of the problems in his line of work. The first cause of defect in his production line is the filling equipment because the machine is not originally designed for its current process. Kolb has to decide whether to continue using it or to replace it with equipment specialized for a specific activity which is filling the bottles. The personnel is also one reason for defects because of insufficient knowledge in his line of job. The purchasing department also caused defects because they acquired defective nozzles on a supplier just to keep up with the orders.
Improve
- Identify means to remove the causes of defects. Confirm the key variables and quantify their defects on the CTQs.
- Identify the maximum acceptance ranges of the key variables and a system for measuring deviations of the variables.
Control
- Determine how to maintain the improvements.
- Put tools in place to ensure that the key variables remain within the maximum acceptance ranges under the modified process.
Kolb will have a difficult time to improve the processes in the production line but quality of the product should not be taken for granted. Once the improvements are implemented, he should still have a regular schedule of maintenance of at least once a month to ensure all equipments and processes are checked.
Cite this Page
Hank Kolb Case. (2018, Feb 21). Retrieved from https://phdessay.com/hank-kolb-case/
Run a free check or have your essay done for you
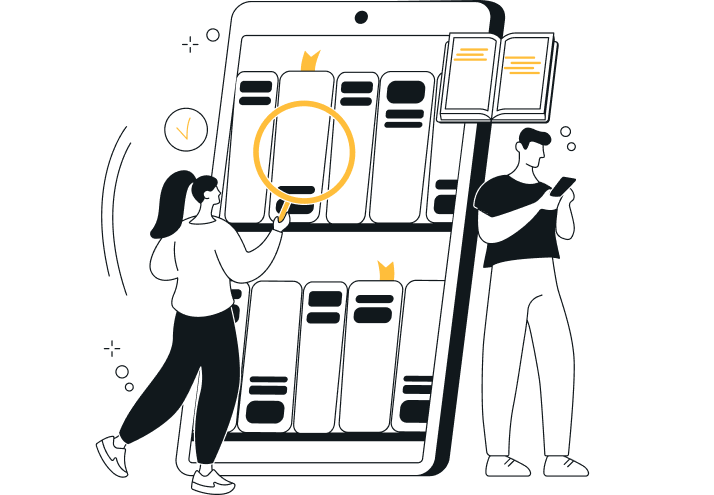